Modern society has brought us all kinds of wonders, including rapid intercontinental travel, easy information access, and decreased costs for most consumer goods thanks to numerous supply chains. When those supply chains break down as a result of a natural disaster or other emergency, however, the disaster’s effects can be compounded without access to necessary supplies. That’s the focus of Field Ready, a nonprofit that sets up small-scale manufacturing in places without access to supply chains, or whose access has been recently disrupted.
As part of this year’s Hackaday Prize, a each of our four nonprofit partners outline specific needs that became the targets of a design and build challenge. Field Ready was one of those nonprofits, and for the challenge they focused on quality control for their distributed manufacturing system. We took a look at Field Ready back in June to explore some of the unique challenges associated with their work, which included customers potentially not knowing that a product they procured came from Field Ready in the first place, leading to very little feedback on the performance of the products and nowhere to turn when replacements are needed.
The challenge was met by a dream team whose members each received a $6,000 microgrant to work full time on the project. The’ve just made their report on an easier way of tracking all of the products produced, and identifying them even for those not in the organization. As a result, Field Ready has a much improved manufacturing and supply process which allows them to gather more data and get better feedback from users of their equipment. Join us after the break for a closer look at the system and to watch the team’s presentation video.
Put Your Name On It
The basis of the new system started simply enough as a label with the Field Ready name printed on it along with a serial number. This allowed end users to know that the product was made by Field Ready and also provided them with contact information. Selecting an effective labeling method presented its own challenges though, and the team ended up trying out a number of different methods based on the type of product, its size, and its intended use location.
For example, if a product was single-use, the group realized they could simply use the shipping label only as their means of tracking the product. If not, paper labels on the products themselves could be used instead if the product was being used indoors.
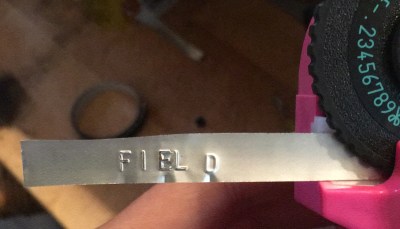
For exposure to the elements, an embossed label or an engraved label might be used, and for very large objects they could also spray paint the label onto the product. Each of these methods would need to be either included in the standard set of equipment that Field Ready would ship to an area in need, or be otherwise easily accessible to the local area, which poses its own set of challenges.
QR Codes Embed Great Detail
With the labeling issue sorted out, the focus could shift to documenting various aspects of the products involved. Making sure documentation gets completed is challenging in any environment, let alone those that Field Ready works in, so they set about trying to make the documentation process engaging, quick, and as easy as possible while relying on as little infrastructure as they could. The solution here was to create an app that allows for rapid creation of QR code labels for any of the products, without relying on internet access for links like QR codes are sometimes used for. The code directly contains all of the information in the product and can be produced and read without network access. If Internet access is available, however, the labels can be easily uploaded or shared using a variety of messaging systems.
The key to the QR code use is the JSON tags that are created for them with a hash value. Each time a QR code is scanned, a record is created about who scanned it and at what time, allowing for a paper trail of each product that the group creates. This is extremely effective at tracking products and their uses, and maintaining a high standard of quality control. The information can be used in a blockchain, which ensures the fidelity of the information gathered. Data produced with the app by scanning the QR codes is also fully integrated with Airtable, which simplifies the process of gathering and maintaining the data. Everything runs on iOS and care was taken to make sure that older Apple phones with smaller screens would be just as capable of running this software as more modern devices. Presumably the iOS limitation was because of the two-month window of delivering a product like this and the team does have some beginnings of an Android port.
Democratize Quality Control
One of the most important notes that Field Ready had after developing this quality control solution for their distributed manufacturing is to not get caught up in all of the techonology. Quality control is about humans and human processes, and keeping that in mind can result in a much more user-friendly experience. They also focus on making an organization that revolves around the humans using the products and those involved in the creation of the products as a foundation for good quality control as well.
While the team has a great start on this quality control system, they hope to develop their prototypes out further to make them more robust to varying use cases. With that in mind, they are going to roll out their solutions slowly, to one region at a time, so that they can more accurately track the deployment and make changes to a smaller set of systems as needed. Of course, the work that they have done isn’t just limited to their organization either. They’ve released the iOS code for the app on GitHub and have released their Android code as well, and have make access to their reports and to their Airtable databases available to those who want them, whether you are a small business needing a way to track small-batch orders or another nonprofit in a disaster-ridden area.
We certainly can’t wait to see some of the ways that this gets put to use and are excited to see Field Ready push this system out to wider and wider audiences too.
Methinks that there are some people do not understand the meaning of quality control and quality assurance.
I do not understand the ‘democratization’ of QC. Earnest query -> please explain.
I do like the idea of cutting up a pop can to make Dymo labels!
Very interesting for use outside of highly regulated industry. I’ve really only researched, used and lead in 21 CFR parts 210 and 211 regulated industry based on SAP, Sharepoint, Trackwise, Beckman LIMS, Peak and I’m forgetting what the calibrations and engineering department used since I’m certain was another app or at least initially… now I’m thinking the calibrations along with qualifications, validations and documents or other changes Change Controls were databased in Trackwise ultimately. Interesting the range of having paper based systems to challenges with implementing more automated equipment transactions with e-notebook systems and going paperless ideally. Neat to see advances with Smartphones versus like a Crackberry from back in the day. I do wonder how Field Ready can be updated to get into that 21 CFR Part 11 compliance maybe for expanded operations capabilities if there is a demand. Awesome project and system! I’ll read into Airtable as I’m not familiar with. Wondering about minimalist ways and means that are reliable, robust, repeatable, etc qualitative/quantitative validation requirements?