Here we are in the future, thinking we’re so fancy and cutting edge with mega-scale 3D printers that can extrude complete, ready-to-occupy buildings, only to find out that some clever inventor came up with essentially the same idea back in the 1930s.
The inventor in question, one [William E. Urschel] of Valparaiso, Indiana, really seemed to be onto something with his “Machine for Building Walls,” as his 1941 patent describes the idea. The first video below gives a good overview of the contraption, which consists of an “extruder” mounted on the end of a counterweighted boom, the length of which determines the radius of the circular structure produced. The boom swivels on a central mast, and is cranked up manually for each course extruded. The business end has a small hopper for what appears to be an exceptionally dry concrete or mortar mix. The hopper has a bunch of cam-driven spades that drive down into the material to push it out of the hopper; the mix is constrained between two rotating disks that trowel the sides smooth and drive the extruder forward.
The device has a ravenous appetite for material, as witnessed by the hustle the workers show keeping the machine fed. Window and door openings are handled with a little manual work, and the openings are topped with lintels to support the concrete. Clever tools are used to cut pockets for roof rafters, and the finished structure, complete with faux crenellations and a coat of stucco, looks pretty decent.
But [Mr. Urschel] wasn’t one to rest on his laurels, for as the second video shows, by the late 1940s he had made some improvements to the machine. The extruder design had been streamlined, and the number of potentially dangerous pulleys and belts had been reduced. He also added the ability to angle the boom relative to the mast, letting new courses corbel in over lower courses. The beehive-shaped structure that resulted was pretty charming, even if it needed manual finishing for the very top. Equally charming are the antics of helpers [Larry], [Curly], and [Moe]. It was also good to see that the original building was still standing a decade or more later, although the buildings no longer appear to be standing, at least judging by a quick look at Valparaiso, Indiana on Google Maps.
Granted, [Mr. Urschel]’s design was pretty limited, and we’ve far surpassed his vision by 3D-printing all kinds of structures, from complete castles to wind turbine towers. But there’s no denying that he got there before we did, and it took some pretty clever hacking to do it.
Thanks to tipline stalwart [Keith Olson] for the heads-up on this one.
Those walls look a lot nicer than the 3D printed walls that I have seen elsewhere. It would be a big improvement on the modern machines to have a spinning disk like he had to smooth out the edges.
I have seen some video of concrete extruders with what are basically trowels on the sides to blend in the layers so it does not look like a building skinned by the Michelin man.
just like conventional construction I imagine the outside could be later clad in something more appealing … for example just on top of my nasty construction C grade plywood is a wrap and a brick face
Have a second arm that trails the first and carries devices to stamp a texture on the fresh concrete. If you used modern technology you could probably carve something ornate instead of stamping.
It works fine for straight or slight curves, but as soon as you do a 90 degree corner it would dig into the wall.
Would have to be more like a couple of thin blades pointing down, then a lot of material would fall down on the floor and on layers below.
A more recent way to solve that is just to have a follower wheel the smooshes the layer. It’s surprising just how much that helps with wall evenness.
LOL, same here
With 3D printed walls (also the current tests): What about armoring irons? Aren’t they essential to build a strong wall with concrete?
From what I understood, they are experimenting with carbon fibre strands embedded in the extruded concrete sausage.
Armoring irons, or lintels, are required when there is tensile strenght involved, such as over window/door openings.
Armoring irons are not required in walls in a normal building as it is strong enough to whitstand the compressive strengths involved.
Only for high load parts, such as bridge pilars, etc, this are used to use less concrete while keeping it’s strenght.
Needing large amounts of concrete has certain challenges in preventing cracks during curing, so using less thick concrete has advantages. (i.e.: Hollow bridge girders, etc…)
You also need to understand there are many “types” of concrete which literaly have strengths that are orders in magnitude apart.
i.e.: Your homemade concrete is nowhere as strong as the concrete used in mordern high-rise buildings.
okay, understood. thanks
After watching both videos, I think building a brick wall would have been much faster ;-)
I was looking at the videos and trying to work out why the structures are not there today.
I was going to say that there was no pre-stressed lintels over the windows. But after looking at the patent (182) they did add strips or rods of iron wire which would have helped. But I still can not help thinking that arches would have been a better long term structural option. Over 80 years I would expect ground settling (there did not appear to be a typical load distributing foundation) and environmental vibrations to cause at least some cracks in the concrete above the windows.
The black and white video on the larger building shows laying a piece of rebar in the channel of the first course above a window opening. I’d want to put rebar in at least two courses over any such openings. The rebar should extend a couple of feet past the sides of the openings.
If you go to 158 South Napoleon Street, Valparaiso, in Google sat view, you will see the remnants of the larger building, changed a bit (chopped a bit on two sides, and raised by a story) still on its original location, next to the tracks. One, at least, has survived. :-)
Oh, good catch! I was looking all over Valparaiso on Google Maps trying to find some remnant of the building, but kept coming up dry. Can’t believe it’s still standing after 80 years:
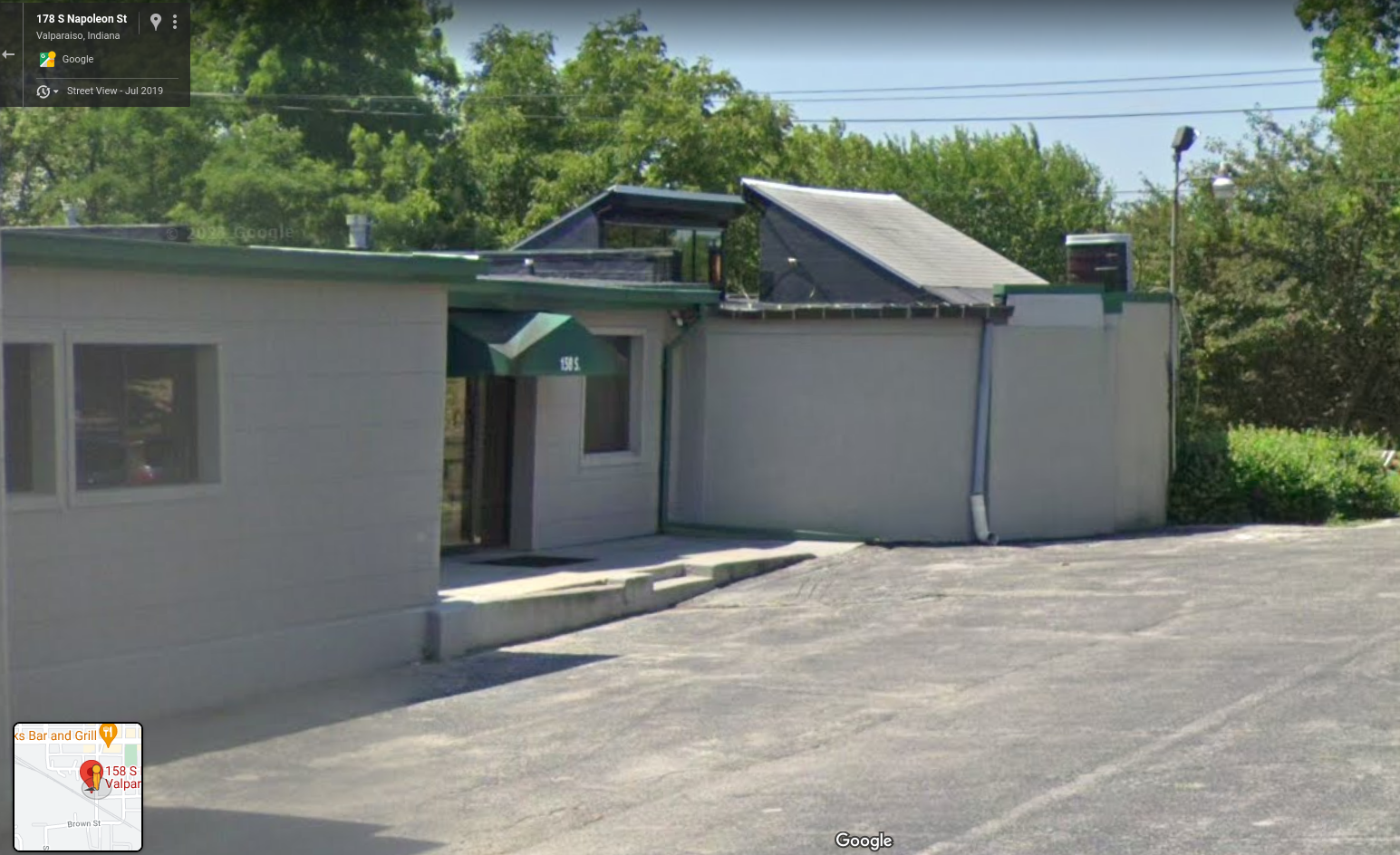
Google Maps
Looking at 158 from above you would never recognise it as the same building.
https://www.google.com/maps/@41.4661597,-87.0637369,99m/data=!3m1!1e3
So, what are those angled panels on the roof? Launch doors?
The Urschel company is still in business. They make food cutting machinery.
The workers are hustling to keep the machine fed so that it looks good for the camera.
The first video explicitly mentions (shows a description) that the machine stops when the material runs out.
The workers could have taken it a bit easier by letting the machine idle for a bit between refills.
I saw a newspaper article about what I think is this a few days ago in a Technology connections video poste 2019 (https://www.youtube.com/watch?v=hpwLDQSadE4 timestamp 10:19).
I thought “oh foam houses, the idea of 3d printed houses is older than I thought it was.” now I saw this article and I think it is possibly the same or related thing. Otherwise curious about this 1940s foam house technology actually was.
Well now you have quite literal lego walls, where you stack insulation brick (PS or PU) with a channel inside, put some rebar in the channel and pour a 10cm layer of concrete inside. Voila you have a perfectly insulated wall (in and out which is perfect) with a rebar concrete core.
It’s fast, but not cheap.
Actuall it costs only 5% more than conventional wood construction couple of years ago and that was mostly shipping low weight high bulk foam blocks. Finding a qualified engineer and contractor is the difficult part
Aussie company based in Perth built and commercialised a one-arm brick laying robot few years ago.
https://www.businessinsider.com.au/video-a-one-armed-australian-robot-can-build-a-house-four-times-quicker-than-a-brickie-2016-7
IIRC, HackaDay had an article about a brick laying robot a number of years ago.
I make you wonder what those individuals could have done with the tool we have available to us!
Absolutely.
I think the bigger building is still there. It’s just been partially incorporated into the main building. Go to 158 South Napoleon Street, Valparaiso, in Google sat view, and you can see the round building. It’s been reshaped and is taller, but it’s in the right location (in relation to the tracks), this address being the original location of the company, so I think it’s the original round building.
Wow, well spotted. I think you can see a remnant of the original parapets:
https://maps.app.goo.gl/GenPzw112xEmcsaa6
That material is probably what we call architectural cast stone or precast limestone today. The “trowels” as you describe them are really better described as rammers functioning like what is used in sand casting to ram the sand around a form. I would bet that you do not see them around anymore because unless it was raining the whole time they were forming the building it probably cured on the crumbly side. When you make precast stone it is usually cured under a wet burlap material or in a cold or hot steam room. here is a video on how it is done today. https://www.youtube.com/watch?v=3GNQQ9lvMso
Scary watching the gentleman work. No hearing or eye protection, and putting his hand just above the mixing blades. An accident waiting to happen.
Uhm… it’s called brick and mortar or straw-brick and mud or… and are several millennium old.
Those are the REAL original 3-D building materials.
Considering the need for housing after WWII you think this thing would have been more popular than it wasn’t. I can imagine Germans would have been happier living in a concrete beehive as compared to rubble.
What would happen if the arm center wasn’t raised up? A dome! I watched day after day as a cluster of domes were “printed” in the mid 60’s in my town with foam “filament” beams 6×4 inches heated to sticky on the surface then pressed into place. An hole for a skylight was left in the center. Then they were sprayed with concrete and mesh. Would have lasted forever and cost little to heat and cool. Sadly the nearby hospital expanded and then left and all is gone, the domes as well. They housed a women’s clinic. Tittie city it got called, painted in a subdued pink.
https://twitter.com/joshlipnik/status/1233438843304660992
Add the ability to move the head in and out radially and turn then this machine could make non-round buildings. Instead of the discs spinning on a horizontal axis, use a pair of vertical cylinders. Minimum corner radius would be determined by the cylinder size.