Wind turbines are a fantastic, cheap, renewable source of energy. However, nothing lasts forever, and over time, the blades of wind turbines fatigue and must be replaced. This then raises the question of what to do with these giant waste blades. Thankfully, a variety of projects are exploring just those possibilities.
A Difficult Recycling Problem
Around 85% of a modern wind turbine is recyclable. The problem is that wind turbine blades currently aren’t. The blades last around 20 to 25 years, and are typically made of fiberglass or carbon fiber. Consisting of high-strength fibers set in a resin matrix, these composite materials are incredibly difficult to recycle, as we’ve discussed previously. Unlike metals or plastics, they can’t just be melted down to be recast as fresh material. Couple this with the fact that wind turbine blades are huge, often spanning up to 300 feet long, and the problem gets harder. They’re difficult and expensive to transport and tough to chop up as well.
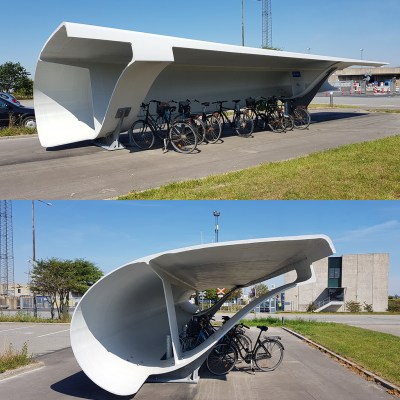
Thus, the Re-Wind project is looking more towards reuse than recycling. Rather then spending energy and time breaking down turbine blades back into reusable raw materials, the project is exploring uses where the blades may be modified and repurposed while remaining largely in their existing form.
A variety of projects have been proposed thus far. Perhaps the simplest is a project by wind turbine manufacturer Siemens Gamesa. The company took a used wind turbine blade, and fashioned it into a sleek and modern looking bike shed in Denmark.
The blade was cut and shaped in order to act as an effective break for the wind and rain, and was able to be quickly installed as a single pre-fabricated piece atop a pair of custom-built metal supports. It’s a quick and easy way to build a shed or shelter, for sure, but unlikely to be a solution that scales well. As the company itself notes, it’s a “small-scale solution,” but one that makes good use of a few scrap blades nonetheless.
The Re-Wind project aims to explore broader uses, with the BladePole concept one of the most interesting. The aim is to reuse wind turbine blades as electrical transmission poles. A paper on the topic shared by Re-Wind highlights the fact that while strength and stiffness are lost in turbine blades due to fatigue loads in their service life, this is only on the order of 10-20% by retirement. In a application such as serving as a utility pole, the dynamic loading would be significantly less, and the overall static loads lower as well. Thus, the blades could potentially serve a useful second life in this application.
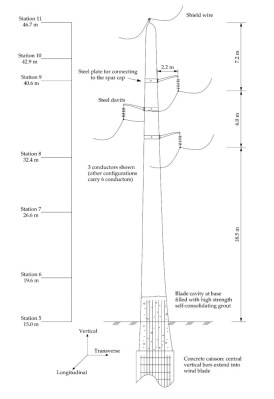
There are some caveats, however. To be effective at scale, and to avoid giving utility engineers massive headaches, ideally blades repurposed in this fashion would all be of the same size, shape and construction. Given the broad variance in wind turbines installed around the globe, this isn’t the case. However, this isn’t an insurmountable obstacle so much as it is an added frustration to the reuse effort. However, if a utility did find itself employing broad numbers of the same turbines, it could then reuse its own waste stream to build out its network in future. It’s potentially a very neat solution.
Other concepts are in development too, such as using the blades in construction applications. The Re-Wind project has explored ideas such as using blade sections as roofing for small houses or as girders to build small bridges under 50m in length. Thus far, these efforts remain largely speculative.
However, for more serious structural applications, several problems are faced. One noted in a paper by Kullberg and Nygren, 2020, is that wind turbine manufacturers hold the finer details of their blade designs as closely guarded secrets. This frustrates efforts to properly engineer new projects using the blades, as it’s difficult to run accurate calculations without a proper knowledge of the materials being used. There’s also the concern of damage and fatigue that a blade may have incurred in service. Cracks or other defects may have built up over time and one used blade may not be as tough as the next. Thus, conservative safety factors would have to be used in designs, or blades would need to be carefully inspected to ensure they were up to reuse in structural applications. The prospect of further degradation of the composite parts already exposed to 20 years of UV and weather is also something that must be accounted for.
An Uncertain Future
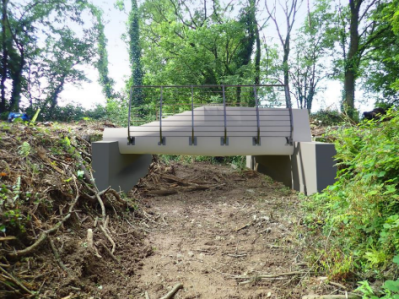
That hasn’t stopped all reuse projects, however, with the Wikado Playground in Rotterdam, Amsterdam famously putting old blades to great use. However, a few children running about is not quite the same loading that a bridge or other structure may see. Thus, wind turbine manufacturers and engineers will likely have to learn to work together if used turbine blades are going to see any real structural use en masse.
It may yet be that the issue of composite recycling is solved and thus reuse efforts will play only a minor role in disposing of wind turbine blades going forward. Efforts like the RecycleBlade from Siemens Gamesa hope to do just that, using new advanced resins to enable easier recovery of raw materials. However, for the time being, research will continue on both recycling and reuse streams until a viable path forward is found. In the meantime, expect to see some creative efforts making good use of these gigantic composite structures!
[Main image: Jhimpir Wind Farm by Muzaffar Bukhari CC-BY-SA 2.0]
Maybe reinforced and sharpened could work as swords for giant robots…
But We need giant robots first, and a very good reason to give them swords.
Sounds like enough reason to me, start building!
We don’t need a good reason, we just need to publicly challenge Musk that it can’t be done…
LOL!
We need a solution now! Not next year.
I wonder if they can be sunk into the ocean for reef building or as a breakwater structure
I wonder if they could be used for SIDING, if not for houses, then for barns, workshops, industrial buildings. Spray a top coat of something rubberized or protective. Use the longest straightest pieces.
Interesting. And great ideas
One obvious problem is that they will catch the wind, making them dangerous in many of these suggested reuse scenarios.
Not necessarily dangerous, but rather that’s just a factor to be considered in the engineering.
Could they be made from aluminum?
Sure, they would be heavier and thus produce less current from the same wind but they would be fully recyclable. Maybe swap out the bearings in the generator and recycle the blades into new blades every two or three decades and they ought to just about last forever. Build more to get the same power out and someday they will pay for the difference. I hope.
I’m not so sure they would be heavier. This is based on my experience with plastic vs. aluminum boats. I don’t know why they chose fiberglas instead; could be the complex shape, could be cost (neglecting recyclability), dunno. But they don’t make airliners that way.
The newest airliners are made from carbon composites.
and some of the newer engines even have composite fan blades
Fiberglass boats are heavy, not because they are fiberglass, but because the manufacturer process.
If they built boats like they do aircraft or turbine blades, there would be a thin layer of glass over a lightweight core.
Fiberglass boats use fiberglass and resin as the core. It is real simple;
1. have a mold
2. Use a chopper gun that fills the mold with resin and short pieces of fiberglass.
3. Use lots of spray to get enough strength out of the short pieces of glass, then some more to make a core, then some more for the inside of the boat.
4. Let dry
5. Let marketing claim “modem technology”.
Boats built this way use a polyester resin, not epoxy. Polyester isn’t a strong as epoxy, so they have to use more resin.
Mass produced fiberglass anything is done this way.
Hand built fiberglass items are built with light weight cores and thin layers of glass in either side.
That depends on the boat you are looking at.
The cheap dingy you can put on a trailer, yes it can be spray formed.
While larger boats tends to use glass fiber cloth as the construction material instead. But this is obviously a more labor intensive task.
This post induced a throwback memory for me. A long time ago our Scout troop wanted to build a bunch of kayaks.
We volunteered building them at our place, under a carport. Cutting sheets of chopped strand fibreglass off large rolls (it was hugely cheaper than the woven cloth glass) and mixing resin from metal drums into plastic ice cream tubs, gelcoating, painting the resin on the glass and rolling with aluminium paint-roller-style rollers was a big part of it.
And with all the other work involved, it took months and months but we made about 14 I recall. Four and a half decades later just the mention of ‘polyester resin’ and I can smell it right now…
Not a bad idea. There is research at the moment to put aluminium and other materials on the leading edge of blades to improve erosion response. However, at the scale on turbines now, aluminium is not stiff enough. Weight would go up hugely and aluminium is more expensive and very energy intensive to produce.
Very cool. This is something I’ve never thought about. The proposed solutions are brilliant and aesthetically pleasing for as long as these sleek, organic shapes are fashionable.
Agreed, great article.
The first two application that come to mind are using them as part of the aggregate filler in cement, and cut into strands they may be able to be used like lower strength rebar in cement. They probably aren’t damaged by salt or UV.
I was actually please to see that they are hollow. I had never thought about it and always assumed they were solid. That right there takes the bulk out of the amount of material I thought was there. Does that count as reduction?
But they already are damaged by UV.
There was an episode of Grand Designs where glass fibres were added to concrete to replace rebar – not lower strength at all.
Using it as filler in concrete and perhaps tarmac sounds like a great idea!
My first thought was to grind them up and use as filler. In construction there is always a need for fill material. I’m curious what it’s compaction rate and break down are.
I love the idea of concrete regolith. It could serve many purposes in concrete, basic fill, fiber, or bar.
Making fill dirt is an economical solution but would upset someone probably.
Nice! Hopefully when we take climate change seriously and go nuclear, they will all find happy homes.
Like the Marianas Trench?
B^)
New drinking game, whenever there’s any article about any renewable energy at all… when you see the comment from someone seriously suggesting nuclear take a drink.
I’m walking to the fridge for a beer right now…
I don’t have the alcohol tolerance for that game.
Nuclear energy is the solution. If you are going to discontinue use of fossil fuels but you don’t want to replace them with nuclear then you are a fool. How else can we satisfy our need for energy? Go on, I’ll wait.
And with renewables how are you going to demand the renewables produce power when it’s needed? Please god, let the sun shine! Make it so!
Seriously, renewables play an important role in generation, but a secondary role until/if a reasonable type battery storage solution can be produced so that when the power is needed it can be provided. Elon’s battery banks are a step towards this. But until then, you need a primary power source that can be controlled. Coal, gas, well any greeny will tell you they’re bad and rightly so. They’ll also give doom stories about nuclear, oh no think of the waste hanging around for years! But the reality is, modern reactors eat waste for breakfast, producing their own, even somewhat reduced waste. That is then tucked away and safely stored.
But as long as folk brush of nuclear as dirty/scary/dangerous/polluting then we’re gonna have Greta breathing down our necks for still using coal & gas.
If you look at all of the true price of nuclear, including safely handling the fuel, safely handling the things contaminated by radiation from the fuel, safely storing the waste for many times the length of recorded human history so far, I don’t see how you can claim with a straight face that nuclear is a cheap form of energy. The US alone produces more than 2000 metric tons of waste per year. Maybe it’s less now, I’m quoting from a 12 year old Scientific America article from 2009. That is a lot of waste in one year and it’ll be dangerous for 250,000 years. It’s not even useful for very long. Reprocessing is not economical and requires expensive reactors that can easily break down and also generates stuff needed for nuclear bombs. Increasing proliferation. Nuclear may have made sense once, but not after you take all of the costs and safety issues into consideration.
Meanwhile a solar panel can produce energy for decades, can be installed and used by common people, and isn’t deadly if anyone is exposed to it. It’s also cheaper than it’s ever been. You can buy panels for 50 cents/w or less. They can be used to lessen your power consumption. If you have batteries they can charge those for use later. I have also heard of people charging their electric cars from them. And it’s great to have some independence from the power grid if it’s down. As long as you have the right setup so you can isolate your system.
https://www.scientificamerican.com/article/nuclear-waste-lethal-trash-or-renewable-energy-source/ (SA article)
https://shop.signaturesolar.us/collections/new-solar-panels (Solar panel pricing)
If nuclear received the same amount of subsidies as wind and solar it would be competitive. In the long term it already is competitive since these plants outlast wind turbines. But politicians only look for things that can be done in one term, so it keeps being pushed back.
“Reprocessing isn’t viable because nuclear proliferation” Lets make sure we all die from global warming so that we can maintain the power dynamic that limited access to nuclear weapons facilitates.
2000 tonnes for the entire US for a whole year doesn’t sound that bad. How much fly ash from coal power stations is produced in a year? That stuff is radioactive too you know.
As an aside, I am always dubious when someone specifically says “metric ton” as if it’s somehow more ominous because it’s metric. A metric ton (correctly called a “tonne” BTW) is 1000kg, very close to the old fashioned ton which is 2240 pounds. Oh wait, now that I look it up, there’s also a weird american ton which is 2000 pounds. Is that what Americans normally use? I don’t want to start another futile metric vs imperial argument, but god what a mess.
Here here
i would be curious to know it those blades could be made into float-able objects like rafts and boats. if they can you could potentially build houseboats or small artificial island with them.
Excellent idea. Using them in air, like repurposing them as power poles, will continue to put large stresses on them. But floating them in water should avoid that problem. I could imagine using them as pontoons for building yet more offshore wind turbine generators.
Maybe housing?
It seems that the turbine blades could be easily used to build A-frame houses similar to metal arch buildings.
The photo of the playground using them spooked me, DAMHIKT fiberglass bits are difficult to remove!
This & also small homes I’m sure are good solutions. I see potentially whole properties & roofing for industrial units too
Here in Germany, you can buy floor components and other construction parts made from turbine blades. It’s a market and it works.
The downside is that – even with todays impossibilities of getting any construction wood in quantities – this stuff is EXPENSIVE like hell. If you have the choice of buying really good, long living, high priced wood flooring or remanufactured turbine blades at the same cost, it’s hard to go for plastic.
The assymetric shape of the blades myght be an obstacle against wider range of subsequent repurposing. To avoid this problem would be nince to biult apx equal quantities of right and left rotating turbines. In this case the mirror shaped pairs of retired blades could be used in much more applications (ie. ships, bridges, buildings, towers, etc.) requiring preferably symmetrical structures.
First off, I like your idea, but you would think that in the 21st century, we have overcome the possibility of wrong parts being shipped to construction sites.
We have yet to solve even more basic problems than that, such as checking train schedules:
https://www.youtube.com/watch?v=W75cvVMFzRo
The truck driver though spent a good second or three to stop, then stod still for another 10 seconds before deciding to get out of there.
If they just hit the gas they would have not been there.
But regardless, yes. If crossing a level crossing with an absurdly long load, then maybe check the train schedule…. Or at least make a phone call to the rail road and ask if any trains will pass and when.
I saw spread them around national parks as coyote dens or just pile them up in Malibu and other posh areas. Anything other than building new ones on every scenic vista in the US! They are a plague on the land.
Could they be ground up and used as a reinforcing medium? Like, added to fiberglass or resin projects or added to a concrete mix?
Bundle them together like reeds, pump them full of rocks and concrete, and use them to build dikes for low lying coastal areas?
The leftovers can be used to build a wall around the paperclip mountain, or even a bridge to the land of the missing socks.
If the carbon fibers is made from plant materiales, It would still be CO2 neutral to burn them on a former coal power plant.
Fiber glass would require more energy to reuse, but if its renewable energy, It should not be a problem to make them into glasswool, triple layer windows or other glassware.
The problem is that splitting glass fiber from epoxy is hard and burning resins emit lots of very noxious gases.
Send him this movie.
https://en.wikipedia.org/wiki/Robot_Jox
Ah, lets just make the blades from laminated wood like they did 100 years ago.
Well there’s the tower being wood.
https://youtu.be/lJsznA1ug1w
A silly idea I have had a few times when it comes to recycling wind turbine blades is to just use them to make a high rise building. Ie, use them as pillars to support the floors and such. If the thing is good enough to handle the forces of the wind bearing at it for two decades, it can likely be used in a more static load without major issue. (though, reinforcements is still a good idea to have.)
Such a high rise could likely get a fairly interesting visual design, unlike the frankly boring boxes that so often gets built these days.
The most major issue of wind turbine blades is though their sweeping curves, makes them rather impractical in most applications.
And to a degree one could ask about the feasibility of reusing the blades by renovating them for future use in wind turbine applications. After all, most damage is likely superficial from dust beating at the surface and UV. The inner structure might be fine for further use. Best case, a wind farm might not need to scrap a blade unless it has serious damage and could repair them on site instead of shipping them out somewhere else. (transporting blades on a wind farm is likely less hassle than transporting new ones from a factory.)
Another thing that has poked my interest when it comes to wind turbines is the sound. Wind turbines are rather noisy. But maybe the noise could be lessened if the trailing edge of the blade had a wavy pattern on it, similar to what can be seen on some jet engines where it is used to reduce noise. (Even if it slightly reduces efficiency, the lessened noise solves a lot of issues.)
I had the same thought about using them for small building structure support.
Surely it would be possible for the blade manufacturer to mark out the blade surfaces inside and outside with faint datum lines at say 100mm intervals, in order to help future recyclers position for cuts and fixture holes.
To be fair here, marking out reference lines on a large object requires fairly simple tools and a bit of patience.
A measuring tape goes a long way. Though, a theodolite can help. (a theodolite is a relatively inexpensive piece of measurement equipment. Not for Joe average, but a construction company likely owns one already.)
I believe most of the noise from wind turbines is from the tip speed (induced drag vortex) and from the whole propeller acting like a giant speaker cone to transmit any vibrations.
The main complaints surrounding wind turbines to what I have seen has been low frequency noise. Usually due to fluctuations in the actual noise. Every time a blade comes sweeping down low its sound is a lot more audible compared to when it is 200 meters into the air. (Practically AM modulated noise.)
Introducing a wavy edge on the trailing edge of the blade could help mix the air on each side of the blade and soften the air pressure difference more gradually. It has been tested on the exhausts of air plane engines with relatively good success.
But the tips of the blade could likely also have some modifications done to it. Maybe add a perpendicular winglet to stop a vortex from forming as easily. Something that also has been tested on airplanes where it has reduced noise rather noticeably.
Even if it just cuts the noise in half is a fairly major difference.
This is actually a great idea, it would not be hard to repurpose blades into trusses needed for the structure for e.g. a construction hall.
There was a house built from the wings of a 747, that’s a very similar situation to this. Odd shape, catches the wind.
https://www.archdaily.com/165172/747-wing-house-david-hertz-architects
Someone above mentioned “pile them up in Malibu”
Can they be used to build tripod oil rigs?😛
That’s some outside the box thinking….
Having worked on these I can tell you 20-25 years is extremely optomistic. Even after 8-10 they are usually getting pretty ratty and full of cracks and repairs. Fixing them up into something useful is expensive- that’s why they are trash in the first place.
Disposal of these things is the Wind Industries’ dirty little secret. That and how much bearing grease they spray across the countryside.
That seems much better than the alternative.
Or maybe a blade-less wind generator?
https://youtu.be/nNp21zTeCDc?t=126
ive postulated that the roots of the blades are so cavernous you could use them a housing for the homeless. with the root and the first 10ft of the blade and a kit containing concrete footings, a door/window wall that bolts to the mounting flange, a plywood floor, and a contoured piece to seal the other end (possibly also with a window), a couple tubes of caulk and some bolts. provided the kit is tailored to a particular model of blade, assembly time probibly less than a couple hours.
Cut the base end off and bolt it to a concrete slab using the same holes used to attach it to the generator hub. For the roof, cut the tip end off the blade. It could be short, or long to cover a patio or carport. I have an idea for a simple way to profile cut the top of the base to match the shape and angle of the bottom face of the tip / roof. Same for cutting the open end of the tip / roof to match up with a piece of some other part of the blade to close it off.
Blades with a smaller root diameter could be storage sheds or animal shelters for pets or livestock. Get over 6 feet diameter and that’s emergency shelter or tiny house size. Could also be dotted around in recreational areas as rental cabins or shelters from inclement weather.
The Seimens B75 blade from 2016 was already big enough that the root end turned upright could make a decent sized cabin. https://iacmi.org/wp-content/uploads/2017/02/Jaques-Nader_IACMI-Presentation-FINAL-For-sharing-1.pdf
Now there are bigger ones, large enough at the mounting ring to make a quite nice sized house.
Chicken coops!
It strikes me that these could easily be used as siding for homes. Nearly invincible siding with a much longer life span than any current siding.
The problem there is with the flammability speed. There are many safety standards to follow there.
I think you could make some pretty impressive art sculptures with these. Lay some out like a giant skeleton, viewable by people in passing airplanes.
You could of course build a big wall, though I have no idea for what purpose. Maybe to redirect wind to other turbines?
Make them floatable, build a big boom with them to corral ocean plastic?
Play a giant game of pick-up-sticks?
@Lewin Day said: “Wind turbines are a fantastic, cheap, renewable source of energy. However, nothing lasts forever, and over time, the blades of wind turbines fatigue and must be replaced.”
Material fatigue is not a big problem in blades that are properly designed, constructed, and maintained. The two biggest problems are material breakdown due to UV exposure, and abrasion from rain, especially on the leading edge of the blade. (Rain abrasion is much worse than abrasion from airborne dust [1].) Coatings/paints are good protection from UV exposure and minor abrasion. Leading edge protection requires a hardened covering or periodic application of resilient tapes [2].
Properly designed, constructed and maintained, wind turbine blades should have very very long lifespans. But from the blade “recycling/repurposing” problem, it is clear that too many blades are failing too early. Fix that problem first rather than seeking out ways to recycle and/or repurpose blades that fail early.
* References:
1. Leading Edge Erosion: A BIG Problem For Wind Turbine Operators, January 17, 2021 (look at the shocking pictures in this paper)
https://weatherguardwind.com/leading-edge-erosion/
2. 3M™ Wind Blade Protection Tape 1.0, 3M ID B00042164
https://www.3m.com/3M/en_US/p/d/b00042164/
could´t they be used as fence on the side of the road to protect from animals?
or dump them between the middle where the now use steel barriers.
The strength of composites comes from the reinforcement (fibers), not the matrix (resin). The job of the matrix is to hold the reinforcements in place. Assuming that you have the optimal amount of reinforcement, the challenge is have enough resin to wet it all out, but no more.
With woven cloth, the amount of reinforcement can be carefully controlled, and layers can be organized to align the reinforcement to be stiff in one direction whilst compliant in another. With chopped strand mat, the alignment is random. With sprayed matting, so is the quantity.
The method used to compact chopped mat and minimize resin quantity is far from perfect. It is typically rolled with a hand roller, so the pressure used is inconsistent. Also, the binder holding the strands dissolves in the resin, and the strands start moving around – there’s only so much rolling it will take before it starts collecting on the roller and pulling up.
Most composites today are woven. Many production composites are made with “prepreg”, where the woven cloth is already impregnated with the optimal amount of resin. The layers are pressed together by air pressure and then autoclaved to cure the matrix. Other methods using raw cloth also use air pressure to minimize the resin, and sometimes vacuum to infuse it in the first place. Prepreg has the advantage that you don’t have to bleed off excess resin. It can also be handled much easier, including being cleanly cut into shapes required to form 3D shapes.
The weight of rolled composites is significantly higher than composites produced with pressure.
Paint is a pretty cheap and effective UV inhibitor.
BTW Rotterdam is a city in the Netherlands of which Amsterdam is the capitol city. Not sure what the author means with “with the Wikado Playground in Rotterdam, Amsterdam”.
https://inhabitat.com/wikado-playground-is-built-from-recycled-wind-turbine-blades-in-the-netherlands/
Wouldn’t be surprised if Rotterdam was a town in the US with a district called Amsterdam ^^
Teacher: “Jonny use Rotterdam in a sentence. ”
Jonny: “My sister took my candy bar, I hope it’ll Rotterdam teeth!”
Lets revisit the nuclear option for a moment, because it’s important. NREL studied the problem extensively and found that renewables could provide approximately 80% of our energy needs, in the US. So that leaves 20% to make up. Guess how much Nuclear we have? Approximately 20%, problem solved. Obviously we don’t want to rely on nuclear fission for ever, but some day we will have nuclear fusion, a much cleaner power source, a step in the right direction. Also advances in power storage will reduce the 20% number further. We will get there, now we just have to start using less energy as a society, I don’t have an answer for that problem.
Yep. And storage will become less of an issue as “smarter” machines (houses, vehicles, dishwashers, whatever) cooperate with production to schedule usage simultaneously. Surge demand storage capacity in EVs parked nearby will also increase with their numbers.
Use the odd, assymmetric shapes structurally in threes or sixes instead of trying to make everything square.
Oriented Strand Board is possibly the worst construction material in widespread use today. It’s only popular because it’s (until recently) extremely cheap. Use (longer) pieces of blades instead of waste wood. Or maybe even make standard size “plywood”. At least it could be highly moisture-resistant. Then finding a use for the initial sawdust would remain. Onsite sawdust, well, that’s likely a serious challenge.
Maybe not with existing designs, but perhaps just wrapping blades with another layer every decade would prolong their life.
I want a fence around the house I am buying. Why can’t I use the material from these wind turbine blades?
1. If they are large enough and hollow then they could be turned into tiny houses or put on a trailer for a tiny towable tiny house.
2. Whenever a person buys an EV they have to pay to have the portion of the blade that would produce the electricity they use for their vehicle transported to their property and stored for whatever use they want, the cost, of course would also have to include the cutting up of that portion of the blade.
Maybe they could be reused as wing sails for boats (after some repairs)? Alternatively, maybe they could be used as foundation pilings?
Why not buildings. Roofs, walls, drainage ditch pipes, roadside- landscape retaining walls
Stop cutting down trees cut this stuff into the same size as wood products no more termites eating our homes
Use as car park Sun/ hail protection in tropical areas. ie: Cairns
I’ve been researching the environmental impact of wind turbine blades once they reach the end of their life, and I’m curious if anyone has experience or ideas on how we can repurpose or recycle old turbine blades. I’ve heard that traditional recycling methods are difficult due to the materials used (like fiberglass and epoxy), but are there any innovative solutions for reusing or repurposing these blades?
Has anyone come across creative uses for old blades, either for art projects, construction, or other sustainable uses? Or, are there newer technologies or companies finding ways to break them down more efficiently? Would love to hear any suggestions or examples of successful repurposing!