When looking at the performance of a vehicle, weight is one of the most important factors in the equation. Heavier vehicles take more energy to accelerate and are harder to stop. They’re also more difficult to control through the corners. Overall, anything that makes a vehicle heavier typically comes with a load of drawbacks to both performance and efficiency. You want your racecar as light as possible.
However, now and then, automakers have found reason to intentionally add large weights to vehicles. We’ll look at a couple of key examples, and discuss why this strange design decision can sometimes be just what the engineers ordered.
Vibration
Anyone who has taken a course on vibrations in university will know that adding mass typically changes things for the better as far as vibrations go. More mass reduces the natural frequency of a system. In a vehicle, if the natural frequency of a chassis or subsystem drops lower than that of excitations from things like the road, drivetrain vibrations, or the engine, vibrations felt throughout the vehicle can be reduced precipitously.
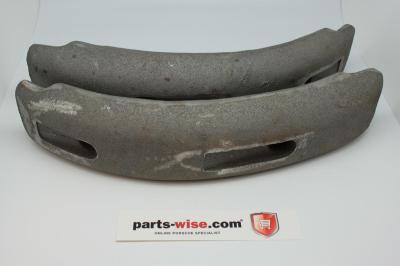
A common example is the Porsche 912E, which substituted a smooth-running six-cylinder engine for a clattery Volkswagen four-cylinder engine. When designing the vehicle to accept this engine, Porsche engineers decided to add a hefty 12-pound weight underneath the transmission cross member. The weight is listed as a “vibration damper,” and likely changes the natural frequency of the rear subframe enough such that it is below that of the vibrations generated by the engine. Adding twelve pounds of dead weight to a cheap, low-performance “sports” car has little noticeable negative effect, but can make a difference in the feeling of refinement, if less vibration is transmitted from the engine to the cabin.
Porsche aren’t the only ones to have pulled such a trick. Toyota used a bolt-on weight on certain Hilux models to reduce drivetrain vibrations, mounted to the transfer case of used to tamp down on excessive vibration. Weighing around six pounds, it was just enough to make a meaningful difference. Meanwhile, the added weight would hardly be noticed on a vehicle with a kerb weight in excess of 3480 lbs.
Volkswagen included a similar item, approximately 25 pounds, in the rear of mid-90s Golf Cabrio models. The “rear added mass” was apparently included to cut down on vibrations.
This technique is still used to this day, though often in a less obvious manner. Engineers work hard to reduce noise, vibration, and harshness in new models, known in the industry as “NVH.” Tacking on a big lump of metal a la the 912E is a quick way to deal with a vibration problem in an existing model. However, if you’re designing a car from the ground up, you can be tidier about your work. Frames and cross members can be designed with thicker cross sections, or extra material can be added to things like engine mounts or brackets to more subtly alter the picture. However, if a vehicle is nearing production and there’s no time to change the molds for other parts, sometimes a little bolt-on weight gets tacked on to tamp down on those nasty little vibrations.
Automakers sometimes go even further, however. Dodge has mounted active mass dampers that shake weights out of phase with the vibrations created by the engine in their RAM trucks. The shaking from these weights destructively interferes with the shaking of the engine, and when tuned properly, can cut down heavily on vibrations throughout the chassis of the vehicle.
Mass dampers have been used in motorsports too, with the Renault Formula 1 team pioneering the technology in 2005 before it was outlawed by the sport’s governing body. In this case, the damper consisted of a 19-pound disc that could move in a vertical plane, held in place by springs, with its movement damped by oil. The disc would help absorb energy from the car hitting bumps in much the same way as tuned mass dampers help reduce oscillations felt in skyscrapers, and was considered a significant competitive advantage for the team until it was banned from competition.
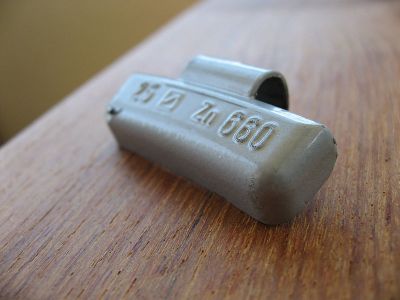
Of course, we can’t forget that one of the most common times weight is added to a vehicle is during a wheel balance. Tires and wheels aren’t always of perfectly homogenous construction, and can have heavy spots. Rotate them up to speed, and you’ll get all kinds of horrible shakes and vibrations throughout the car. However, with the aid of a balancing machine, a few weights can be stuck on to balance all that out.
Balance
Sometimes though, large weights are added to a vehicle to aid in balance and grip. A great example is the 1957 Willys FC-150 truck, which mounts a hefty 265 pound weight over the rear wheels. In this case, the truck as designed has the engine and passenger cab way up front on the chassis, meaning all the weight is very forward-biased. This has the rather negative effect of making the vehicle want to lift the rear wheels under hard braking, and just generally makes the vehicle unbalanced an difficult to control. The solution was obvious: chuck a big weight on the rear to keep those wheels on the ground.
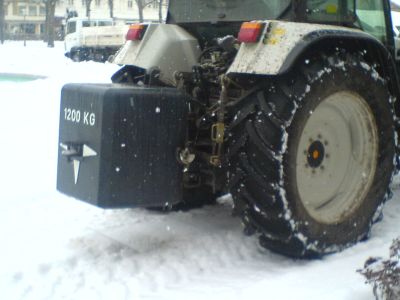
It’s a very simple solution, of course. Back in the 1950s, petty concerns like fuel economy and efficiency simply weren’t front of mind. Thus, it was easy to slap a weight on and be done with it. These days, trucks are designed with a little more finesse and are usually plenty heavy all around, so such obvious measures aren’t needed. Regardless, it’s still important for a vehicle’s weight distribution to be appropriate, whether loaded or not, to maintain good handling.
In fact, when it comes to pickup trucks, a common solution to add traction in the winter is to simply add a dummy load in the bed. A few hundred pounds of sand or pavers can help reduce fishtailing or spinning up the rear wheels in the snow. It comes at a cost to fuel economy, but if it keeps the truck out of a snowdrift, you’re saving plenty in towing fees to make up for it.
Similar measures are often used on tractors to help them pull implements and not lose grip in mushy terrain. These may be applied to frames on the front or rear of the tractor, or even directly on the wheels themselves, helping to increase the force pressing the tires into the ground for more traction. These can weigh in the thousands of pounds at the high end.
It’s Not All Bad
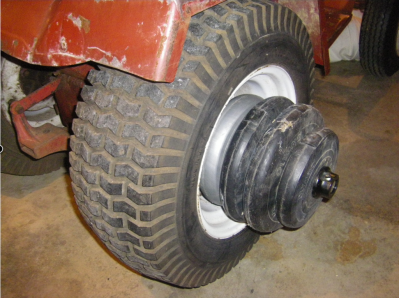
As it turns out, more weight is not always a bad thing. If a little extra weight helps cut down on annoying vibrations, or solves some tricky handling issues, it’s usually worth the trade-off.
If you’re competing in motorsport, and need the ultimate in performance, cutting out every last bit of weight makes sense. However, for daily use on the road and elsewhere, often a little extra goes a long way to solving some garden-variety engineering problems!
Another example is in landspeed cars. Weight negatively affects acceleration in all directions…but not top speed. So weights are often added to landspeed cars for the same reasons they’re added to tractors, for traction and balance. Wings could also be used to affect traction and balance, but these would add drag which would decrease top speed, the most important performance metric of the landspeed car. Weights inside the car don’t have that problem :-)
I recall talking to a team at Bonneville with an Opel GT they had massaged a big block v8 into. They had the car ballasted to a relatively portly 4500 lbs for that very reason: traction.
Oh I remembered one more interesting example from motorsports: F1 has a minimum vehicle weight rule to basically keep the wealthy teams from having a huge advantage through costly weight reduction. But these teams take advantage in another way: they still spend huge money to make the cars as light as they can, well below the minimum weight, and then bring the car up to the minimum weight by layering lead sheets onto the area around the bottom of the driver’s seat, the lowest point inside the car. This gives their cars a lower center of gravity than the smaller-budgeted teams at the same weight.
In NASCAR, similar cheats were filling the fire extinguisher or driver’s helmet with lead,for the official weigh-in, and swapping them out before the race.
Except the F1 thing isn’t a “cheat”, since the car has the weights during the whole race.
But yes, if a team were to remove the weights, then yes it would be cheating. (and likely caught since the cars are inspected after each race, and yes that is a logistical nightmare for the teams as they need to get to the next track on schedule.)
it has been a cheat eons ago, some teams had water tanks for “brake cooling”, in reality it was just to increase the weight until the water was dumped on the first lap, one team went even further adding water with lead shot to the tanks after the race
One NASCAR racer [Dale Earnhardt Sr.?] used clay “pills” in his suspension to meet the minimum road clearance. Those would crush usually on the first curve.
The best thing about F1 is how the entire thing is dedicated to not having to deal with the rules wherever possible or making them entirely irrelevant :)
Are they too good for tungsten?
Surely Osmium would be even more ideal?
Well, the rich teams used depleted uranium until it got banned.
they never miss a chance to spend money, until was banned some teams used helium instead of air for the wheelguns, because it could make them spin faster…
I think NASCAR still uses very high pressure nitrogen for their impact wrenches.
I have a feeling they do use tungsten to be honest, but that is better than what they used to use before it was banned, depleted uranium believe it or not.
They use a tungsten/nickel alloy called Densamet for some ballast. It looks like stories of depleted uranium ballast are apocryphal from what I can find though.
Now there’s a good use for California’s Proposition 65. Get the lead out of Formula 1. ;)
Even better was the tuned mass damper in the nose of whichever car it was, that was found out & banned.
Of course, there are also the obvious counterweights on crankshafts and (usually) on camshafts.
And harmonic balancer added to (some) crankshafts.
And the additional balance shaft often seen on 4-cylinder engines (is that still a thing? seemed like a hack to me).
In the winter we’d just leave a half ton of green wood in the back of the truck when we mounted the plow.
Balance shafts have been used for many decades on lots of engines, and are still very much a thing. I haven’t dug that deeply into a 4cyl auto engine recently, but Dodge pickups definitely aren’t the first application. Can confirm they’re used on single and twin cylinder powersports engines from several manufacturers, as well.
Balance shafts seems to only be used on high revving four cylinders.
Otherwise it’s usually 1,2 or unequal number of cylinder in-lines, and some V6
My single cylinder motorcycles has a balance shaft. Does use some of the limited power, but makes for a much more pleasant ride. Some motorcycles also use handle bar end weights to damp vibration, they make a huge difference in rider comfort, with not having numb hands after a long ride.
Balance shafts are used on high reving 4 cylinder engines as well as larger ones such as Chryslers 2.4L engines. Some people have removed them deciding they dont care about vibration so they remove them. That’s generally a bad idea as the vibration is transmitted down the power train. It’s like having a hammer beat hit your transmission 3000 times per minute when driving. Eventually,something’s going to break. For some applications like racing use it might be appropriate though.
But the balance shaft can’t be considered “a hack”. 4 stroke engines with 4 cylinders are inherently unbalanced. It’s just a fact of internal combustion engines.
I wondered what the purpose of the damper was on the rear axle of my CR-V!
My old 88 Cheyenne drove so much better with 4 or 5 sandbags in the back.
And forget going out in the snow without them!
That thing was a brick in the front, a feather in the rear.
Also, a bit of weight might make cornering more difficult but on a straight but bumpy road driving fast it helps you keep moving in a straight line. A long drive on back-road highways and driving around a circular racetrack are very different things. A bit of weight to allow you to go faster on the straight-a-ways might be more than worth the sacrifice of having to slow down a bit more coming into the curves.
A car I used to drive handled much better fully loaded than empty, and then I realized the rear shocks were not doing much, even if they would pass the inspection (which only tests asymmetry, not for proper damping).
I clearly had that same feeling on bumpy roads, and then it drove like a feather with 4 new shocks, even unloaded.
My tiny front-wheel-drive Polo used to drive just fine in the snow and ice, because all the weight was right over the driven wheels.
On a Saab 90 the engine was in “backwards” sitting mostly ahead of the front axle. It’s difficult to say whether that was a good or a bad thing – it went very well in snow but it tended to sink into it. 60/40 weight distribution, I always had sand bags in the rear, for the ballast and for the sand/grit.
Some cars manufacturers (Ford) used taped-on wheel weights on to brakes calipers and discs back-plates to avoid noisy vibrations as an after-sales fix.
Rigidity can also make difference in these cases. My car’s design has been copied/pasted with minor improvements from the early 80s to 2010. When they introduced a new diesel engine, it would cause the body to vibrate at specific frequencies, so the manufacturer fitted some steel beams to shift those resonances. In later iterations of that design, knowing this engine was so rumbly, the stamped some ribs in the sheet metal bodywork to get the same result than the beams but for cheaper with no added mass.
There are also mass-oil dampers on some cars’ engine/transmission mounts. Oil is contained into a rubber chamber to damp the vibrations better than rubber itself. However, the rubber cracks over time, eventually losing all the fluid leaving you with plenty of vibrations. This way you can genuinely brag about the powertrain having so much torque it can sheer its mounts.
Mass is also added to driveshafts, especially on FWD cars where they have unequal lengths. It’s done either with a rubber/steel ring added on one side, or using hollow shafts of different diameters on each side. The idea is that both sides should have a similar inertia momentum, to avoid torque-steer.
Would your car happen to be of this lineage? https://en.wikipedia.org/wiki/Daewoo_LeMans Originally an Opel, sold off to Daewoo, imported from Korea as a “Pontiac” LeMans and eventually ending up being produced in Uzbekistan with engines much more powerful than it had in the hands of Opel or Daewoo. The car got various changes to the nose and tail but the doors look like they’re all interchangeable. I wonder what a “Pontiac” version would be like with an Uz-Daewoo 85HP engine transplant?
It’s more like the platform idea, where they design a compact car, squish it to make it a city-car, copy-paste/rescale the front layout and rear suspension into a minivan or a full-size SW. The body has evolved a lot due to design trends and crash regulations, but looking underneath makes you understand the trick where things didn’t change much in 30 years of production.
Parts are still interchangeable, mostly drivetrain, suspension and interior.
Tractor tires often have the capability of being filled with water for added weight.
And calcium chloride
The most likely place to see ‘tuned mass absorbers’ on modern cars is the exhaust. They’re frequently used to change the anti-nodes of the the exhaust so they do not line up with the hangers that attach it to the body.
My father loves to tell the story of how he and my mother went skiing, missed the last lift and ended up in a valley next to where their hotel was. They took a hitchhike with someone in a Citroen 2CV, but it started snowing and the (very light) car lost traction. So the driver asked my dad to put on his bonnet and glasses and sit on the front hood — and my mother to sit next to him in the front seat — and in this fashion they managed to drive uphill, and be the only car to do that that evening.
I was taking a double decker bus back from Cambridge and it started snowing rather heavily.
The gritters hadn’t been out and the driver, albeit going slowly, was having trouble with the front wheels
sliding down the camber of the road into the gutter.
So I encouraged the other passengers all to move up to the front of the bus, some of us standing in front of the line you must stand behind. He regained traction and was able to get us home. Result!
I’ve done that multiple times, sitting in the trunk of a BMW to make it up a snowy hill and sitting on the hood of a light FWD offroad. Stupid teenagers doing stupid things.
Note that driving an FWD car backwards makes it a RWD, that can sometimes help.
The story is VW Bug acts like a powered sled in the snow, tall skinny wheels in front work like steering paddles and the weight is centered at the rear wherls for traction XD
I can’t really think of a case where driving a FWD car backwards would help with anything.
Going up a steep hill is when it works, because of the weight transfer to the downhill end of the vehicle
I remember the days of adding tubs of sand in the back of my 2WD truck back when. Really helped getting to work in the winter as it was steep ‘up hill’ to get there with stop lights on the grade…. Dreaded those commutes. In ’97 bought a 4WD pickup which solved those issues. Like to get a new truck, but at the inflated current prices, I can buy a LOT of gas. So will just ‘maintain’ my o’ Dodge Ram. Way cheaper that way… And as a bonus, it doesn’t have all the silly electronic do-dads they insist on adding on the new ones either…. a plus.
It’s all good until you have to get out of your truck and fill your shoes with mud and snow when it’s time to lock the front wheels, I’ll take a modern 4wd with a nice convenient lever in the passenger compartment.
Don’t have to put in the hubs with the Dodge. I just have a floor lever to pull into the different positions. You must be thinking of the Fords at the time.
You must be thinking of a narrow range of trucks because locking hubs are not universal to old 4WDs… Land Rover have had a lever in the cab since ~1948, although aftermarket free-wheeling hubs (supposedly for fuel economy) were available.
My boss actually swapped his auto hubs to manual in his 01 excursion.
No vacuum issues to worry about and he like to also use his low range for control to back heavy trailers up hills
I am assuming it was RWD. I remember a particularly bad winter and following a Merc which was sliding all over the place while my FWD Diesel had no issues with the majority of the weight over the wheels. BMW’s are also terrible in the snow for the same reason
I’m remembering my friend who got his 4WD pickup truck stuck in a perfectly flat restaurant parking lot with no snow, just some freezing rain that infiltrated the wheel locks so he couldn’t turn them. His truck was empty and the rear wheels spun as if they were resting on Teflon. We found a guy with a Honda civic who helped us push the truck into the salted street where it could get some traction.
Reminds me of people who either throw all-seasons or offroad/mud tyres on their luxobarge 4×4 SUV and expect it to be dominating winter roads.
Cue them ending in a ditch or crashed into a utility pole or parked car, while a clapped out early 90’s corolla with sandbags and a shovel in the back and 4 guys in it drives around with no problem.
Though from personal experience, you can still FEEL the snow scraping at the undercoating.
When I used to work in Vail, my employer’s FWD Cadillac sedans were just as good in the snow as the 4WD Suburbans. The Cadillacs had very expensive Finnish snow tyres and very good (for the early 2000s) traction control. The only place the Cadillacs couldn’t go was the rougb dirt roads.
Jeri Ellsworth gave a talk where she describes adding a fake weights to her racing car to throw off people who were snooping on her car.
Snowmoblies for nordic ski grooming are special case machines. Based on snow conditions and what grooming equipment was being pulled, we often added mass to our Skandic to maintain steering. Not uncommon to attach weight lifting bars (in a vertical orientation) to the nose so you could change mass distribution by simply dropping on additional weights.
I have experience from multiple vehicle and aviation vibration projects. When vehicles running over IEDs became a big issue in the mid-east conflicts, the military added mass for protection (think thick heavy metal sheets) to their humvees. This really threw off the suspension and handling. With bigger transport equipment, you also have the additional issue of tuning the suspension for empty vs full load conditions. In a convoy, the slowest vehicle sets the pace. If you can’t steer you slow down which isn’t what you want in a war zone. I worked on magneto-rheological fluid damper systems that allowed you to quickly change damper characteristics so the suspension would automatically be tune for road conditions and load. Same technology as the sport car (corvette magneride, many others). Fast enough that you could detect hitting a bump and change the damping while the wheel was moving up. Tested by deliberately hitting 6″ and 8″ half rounds/pipes and driving some nasty off road test courses. The metric for success was speed driving the course.
Another project I worked on was essentially adjustable wheel weights for propellor aircraft. Typically, prop balancing is done on the ground which isn’t ideal. The system I worked on measured vibration and adjusted two rings with weights that were spinning with the prop shaft. The system could “step” each ring to move CW or CCW and reduce the vibration. Lots of other details (multiple props) but basically the system was two wheel weights with accelerometers so you could automatically measure and tune while the plane was flying. The amount of mass required was miniscule relative to any other mass based vibration strategy.
The easy solution to vibration is mass. In aviation the last thing you want to do is add mass. Especially helicopters which have limited lift capabilities at high/mountainous altitudes. Active vibration technologies exist that spin adjustable unbalanced shafts to create equal and opposite vibration to cancel the problem frequency.
I agree with the article that mass is critical aspect in vehicle handling and vibration. If you want to reduce mass(and you do!) while keeping the same or improved performance you need to understand some science and engineering. With some engineering knowledge, it’s quite feasible to electronically change the damping ratio, actively move small balance weights, or even create equal and opposite force to control vibration without adding mass.
Awesome comment thank you. This is why I read the comments on hackaday
Cadillac and Benz both add weights to their doors so the car will ‘feel more solid’. No other reason, besides stupidity.
It was funny on the Alante. Pininfarina would spend tons of effort removing weight from the body, when it got to the USA (via 747 freighter, but that’s another stupidity), GM would bolt on weights.
I once added basically an asphalt layer to the inside of my car doors mostly for audio purposes (remnant ice and water shield for roofing is the poor man’s dynamat), and it definitely did make the doors feel more solid when closing them.
A couple of months ago, I was walking my dog. As we walked past a house, the owner was getting into his 1970s era Ford Ranchero. The sound of the door slamming shut was something I hadn’t heard in a long time.
Here’s a tip: buy a Miata and enjoy the ideal 50-50 weight distribution.
If you’re under 5’6″. Any taller, you’ll have to enjoy it sitting at the curb ;)
Depends on your torso/leg ratio.
But you can also take out the seat and pour yourself a ‘bead seat’ (search or scroll a little and its there) http://www.dpcars.net/dp4/da.htm
Its a foam in a bag, with micro beads filler, conforms to you, let it set, and wrap it in gaffer tape.
Some classes of auto racing add weight to cars that win a race. The more races a car wins, the more weight gets added. It’s like the people who came up with the rules read “Harrison Bergeron” and thought it was a great concept. Please never elect or appoint any of those people to any government office.
20+ years ago I heard a tale of a guy who wanted to add a lot of weight to the bed of his pickup, but didn’t want to take up a lot of space with sand, gravel, bricks, etc. So he bought a 1/2″ thick, 4×8 foot sheet of steel and had it set into the bed. Wasn’t bolted down. It worked great until he hit a road too slick, slid off at speed and the steel plate didn’t stop with the truck. It sliced through the front of the bed, the back of the cab, and the driver.
Yes, I submitted that one to Mythbusters but they didn’t test it.
a silly reason is in places where adding heavy steel plates to bring the weight up above a limit that makes the vehicle classify differently so there is less tax or less strict emission requirements ..
Jaguar batteries in my XJR’s and XJ-S are in the boot – opposite side from the driver. That’s not adding weight that wouldn’t be on the chassis anyway, but distributing it in an intelligent fashion.
That reminds me, I really need to install the mounts for the rear weights on my lawn tractor so it can do a better job plowing. It worked last year but I imagine it will slip less with the weights in addition to the tire chains.
https://dodgeforum.com/forum/3rd-gen-ram-tech/346102-rear-damper-bar-2.html
I’ve seen this on my friends Dodge Ram
Seems to be a 34lb iron bar hiding by the back bumper.
Back in the day, when I drove a 1984 fox body mustang (a notoriously front heavy car) at terrifying speeds down dirt roads, I had a 4′ x 3″ (1219mm x 76mm) bar or stainless steel in the luggage compartment. The bar of steel was gifted to me by a friend who worked at a machine shop, and it weighed roughly 95lb (73kg). Because of my early habit of never cleaning my car, I became accustom to the extra weight far behind the rear axle and I can say that I noticed a difference immediately after removing it from the car (after some months of it being there). It was fun to recall this story, and as a person who has studied engineering I can say it is good to play with the normal force if you want to change the handling characteristics of a vehicle. Sometimes the static margin is more important than the mass if you value handling over acceleration as a measure of performance.
I guess I am being pedantic here, but your pounds to kilos conversion is suspect.