Who can’t resist snapping up a piece of really expensive laboratory testing gear for next to nothing when browsing eBay or similar? Maybe it’s giving you mournful eyes when browsing through a yard sale. Often such gear is sold for cheap because it’s defective, but with a bit of attention, can be brought back to life. This is how [Roberto Barrios] ended up with a Rohde & Schwarz FSIQ 7 signal analyzer lounging around his place for a few months until he got it fixed.
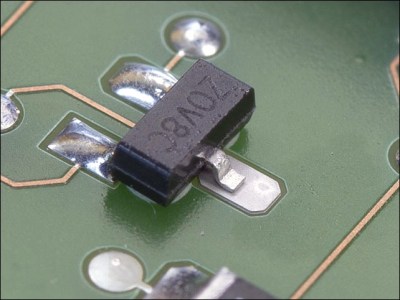
Part of the fix was replacing a busted RF converter module (A160 IF-Filter) with a used-but-working replacement, but this left the device with odd calibration failures. In the process of tracing down the cause, [Roberto] took many high-resolution images of both sides of the PCBs in order to reverse-engineer the circuit. To complicate matters, the calibration results indicated that the unit’s filters were fine on boot-up, but would deviate after a few minutes.
After extending the filter module to work outside the enclosure and experimental use of a hot air gun, ultimately the cause was tracked down to an unsoldered pad. Considering the extremely simple cause of the failure, it would seem that R&S QA had an off-day when that replacement module was produced. If there’s a lesson to be learned here it is probably that a simple visual inspection is sometimes all that is needed to fix a hardware issue.
What are your expensive gear repair stories? What did you learn that could save others hours of their time?
This is not at all foolproof, but when I was working in electronics manufacturing, we found we could often hold a board up so a bright light reflected off it, and spot unsoldered pads because they’re flat and reflect well. Soldered pads have rounded solder on them so you don’t get the same tiny bright flash. This works better on ENIG finishes than HASL like the board shown, but sometimes can save you a lot of time.
That’s a great and caveman-level alternative to automated optical inspection! Sometimes KISS is best.
https://hackaday.com/2021/02/11/aoi-by-diy/
HaD you are cruel. The header photo is of the top side of the board, but the fault is on the other side!
R&S make it pretty difficult for anyone to repair their gear. Service manuals and calibration programs are very difficult to obtain “officially.” Due to several issues with this, and several products not performing to expectations or specifications, I refuse to use them in any of my future Automated Test Equipment Bench projects ($500K+ per bench).
There’s one piece of equipment we designed in for which we needed a specific feature that was advertised in the data sheet and manual as a pricey add-on (which is just a configuration bit enabled in software to activate). Turns out they only built a framework for that function, never completed it, and had no intention to fix the problem. We had to add other hardware software just to work around it. We already had $7 million in benches already built and almost ready to deliver to customers; this threw us 5 months off schedule.
That reminds me of an R+S enhancement I paid handsomely for on a CMU300 (I think Mobile Originated Call) and as it turned out it didn’t interoperate with another feature I already had, and it was the combination of the two that I needed to perform the test.
R+S were very unsympathetic and didn’t offer a refund. Very irritating indeed.
Hey Matt, I am responsible for Signal & Spectrum Analyzer Product Management based in our Munich headquarters since 2019. Thank you for posting your experiences here, of course I am sorry this is your view of R&S. I am not specifically aware of this case (or even if it relates to my group) and it may be quite some time before my tenure, but I would appreciate if you would be willing to fill me in and discuss on a call?
I watched all of the signal paths repair videos, from those it comes out, as far as I could see that R&S is the least repairable.
Certainly stops me from buying any R&S used
I’ve had that exact same problem, an unsoldered pad on a SOT23, just lately. On two parts right next to each other. That was just on an LED driver though (a finnish one IIRC), so nothing fancy or expensive. The faulty pads were’nt even covered in neither ENIG nor HAL, so they were even easier to spot.
That thing worked flawlessly for about three years and then suddenly stopped working. I didn’t mean to seriously repair it at first, but gave it a curious look, because a replacement part was weeks away. Et voila – simple fix!
I had a clock in my car that stopped working, the car at the time was 20+ years old.
On opening up the clock someone had forgotten to solder one wire, it was just wrapped around the terminal. Gradual tarnishing over decades did the rest. Fixing that was a simple 5 seconds soldering with the Weller, but removing and replacing the clock as well as disassembling and reassembling added up to a few hours.