Most of us probably have some vivid memories of high school or college chemistry lab, where the principles of the science were demonstrated, and where we all got at least a little practice in experimental methods. Measuring, diluting, precipitating, titrating, all generally conducted under safe conditions using stuff that wasn’t likely to blow up or burn.
But dropwise additions and reaction volumes measured in milliliters are not the stuff upon which to build a global economy that feeds, clothes, and provides for eight billion people. For chemistry to go beyond the lab, it needs to be scaled up, often to a point that’s hard to conceptualize. Big chemistry and big engineering go hand in hand, delivering processes that transform the simplest, most abundant substances into the things that, for better or worse, make life possible.
To get a better idea of how big chemistry does that, we’re going to take a look at one simple molecule that we’ve probably all used at one time or another: the common artificial flavoring wintergreen. It’s an innocuous ingredient in a wide range of foods and medicines, but the infrastructure required to make it and all its precursors is a snapshot of just how important big chemistry really is.
Natural or Artificial?
My interest in wintergreen came from a recent video that described what happened to a child who accidentally overdosed on wintergreen essential oil; spoiler alert, it wasn’t good. The medical story itself was fascinating, but it got me curious about where wintergreen oil comes from. While wintergreen oil can be harvested from a number of shrubs of the Gaultheria genus and from some species of birch, the primary aromatic substance in wintergreen oil, methyl salicylate, is much more commonly produced synthetically. Artificial wintergreen lacks the additional compounds found in natural wintergreen oil, and therefore some of its complexities, but methyl salicylate still has enough of the familiar aroma and flavor of the real deal to serve as a suitable substitute.

The pleasant aroma of methyl salicylate is a characteristic of the chemical bonds within it, specifically the ester bond. An ester bond is one that connects two species through a carboxyl group; in the case of methyl salicylate, it’s the methyl group (-CH3) that is ester bonded to the salicylic acid. The reaction that accomplishes this is known as a Fischer esterification, and while there’s a lot of complexity involving exactly how electrons are shuffled around, for our purposes all that’s important to know is that mixing salicylic acid together with the alcohol methanol (CH3OH) in the presence of sulfuric acid transfers the methyl group from the alcohol to the salicylic acid.
This sounds simple, and it is — simple enough that there are plenty of examples of making artificial wintergreen oil on YouTube. On an industrial scale, things get a little more complicated, as the reaction needs to be cleaned of impurities, but the interesting part here is where the two main compounds needed for this reaction — methanol and salicylic acid — come from in the first place. As it turns out, like natural oil of wintergreen, both of these substances can be found in nature, but both are now more commonly sourced from the same place that nearly everything else seems to come from — petrochemicals.
Methanol
We’ll take methanol first. Methanol, also known as methyl alcohol or wood alcohol, is a single-carbon alcohol that is produced as a waste product by some anaerobic bacteria. Methanol was traditionally produced by burning wood under reducing (low-oxygen) conditions and condensing the vapor that comes out. Industrially, the process is much different, and relies on syngas, or synthesis gas, as a feedstock.
Syngas is a mixture of mainly carbon monoxide and hydrogen, with a little carbon dioxide and water vapor mixed in. Although most syngas produced is used to make methanol, to the tune of 157 million tonnes globally in 2020, it’s also a feedstock for myriad chemical processes, including the Haber-Bosch method of making ammonia. While syngas can be made using virtually any source of carbon — the gas given off by the aforementioned low-oxygen wood fire is pretty much syngas — and via multiple methods, most syngas today is manufactured by steam reformation of natural gas, or methane, in the presence of a catalyst like nickel or copper:
Steam reformation is a process that requires huge industrial installations to handle the high temperatures and pressures needed — up to 850 °C at 25 to 40 atmospheres. Since so much syngas is devoted to methanol production, the output of the steam reformers is often piped directly into the reactors, which contain beds of zinc oxide catalyst on ceramic supports. The reactor is heated and under pressure, but to a comparatively mild 250 °C at 50 to 100 atmospheres:
The crude reactor output is a mix of methanol, ether, and other products such as ketones, aldehydes, and heavier alcohols. These byproducts are isolated through a combination of distillation and phase separation to leave methanol that’s ready to use.
Salicylic Acid
Despite the fact that nature seems to make salicylic acid in abundance — it’s found naturally in the bark and leaves of some species of willow tree, extracts of which have been used medicinally since antiquity — it turns out to be easier to manufacture than to obtain from nature. And again, the primary feedstock for its synthesis is petrochemicals.
Salicylic acid is most commonly made with the Kolbe-Schmitt reaction, which combines a sodium salt of phenol, called sodium phenolate, with carbon dioxide and sulfuric acid. The reaction is carried out at moderate temperature and pressure (125 °C, 100 atmospheres) and results in the carboxylation of phenol, with salicylic acid being the primary product.
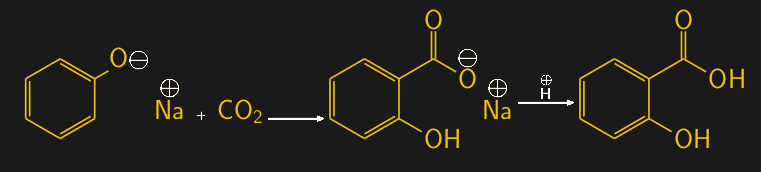
The Kolbe-Schmitt reaction is carried out on huge scales every day, as the salicylic acid it produces is the precursor for one of the most commonly used medicines ever: aspirin, or acetylsalicylic acid. About 40,000 metric tons of aspirin are produced every year.
Phenol
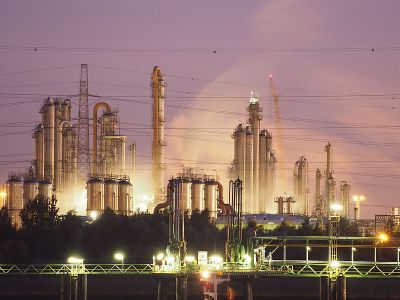
So where does the feedstock for the Kolbe-Schmitt reaction come from? Sodium phenolate is derived from phenol, which is also known as carbolic acid. Phenol is a common organic acid that has all sorts of uses in making everything from plastics, including everyone’s favorite retro plastic Bakelite, to pharmaceuticals. Oral analgesic sprays like Chloraseptic are basically a weak phenol solution mixed with flavoring to mask its characteristically medicinal aroma.
It should come as no surprise by now that phenol is mainly sourced, drumroll please, from petrochemicals. Just a glance at its chemical structure shows that phenol is based on benzene, a six-carbon ring with alternating double bonds. Each of the carbon atoms in benzene has two hydrogens a hydrogen attached to it, giving it plenty of places for other species to attach; in the case of phenol, a hydroxyl (-OH) group is attached to one of the carbons.
While phenol was once extracted from coal tars, today there are more efficient ways to make it. There are several commercial processes, but the cumene process is one of the more common methods for phenol production. It uses benzene and propylene, a three-carbon alkene, which react with oxygen in the presence of a catalyst to create phenol and acetone. The overall reaction is shown below, but that’s a simplified picture of the full reaction, which proceeds through the intermediate isopropyl benzene, or cumene, hence the process name. About 11 million tonnes of phenol were produced in 2020 worldwide.
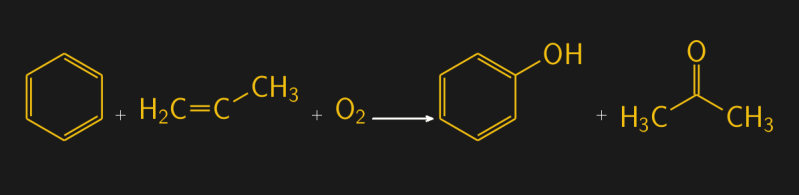
Benzene and Propylene
We’re now almost at the end of the road for artificial wintergreen — remember wintergreen? The last two feedstocks to consider are benzene and propylene, both of which come more or less directly from crude oil processing. Propylene, which is also a feedstock for the manufacture of polypropylene plastics, is made by a process called steam cracking. Steam cracking uses high temperatures and pressures to break saturated hydrocarbons, where every carbon has a full complement of hydrogens, into smaller, unsaturated molecules. For propylene, the starting saturated hydrocarbon is propane, a three-carbon gaseous hydrocarbon.
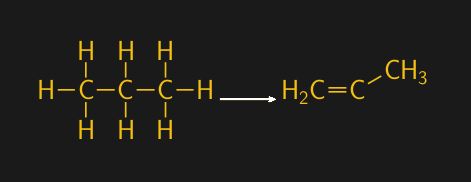
Which finally brings us to benzene. While the six-carbon ring does occur naturally in crude oil, it’s generally in small enough concentrations that other methods are needed to get industrial quantities. Benzene is the “B” in the so-called BTX hydrocarbons, which along with toluene and xylene are made from a mixture of crude-oil-derived hydrocarbons having between six and twelve carbons. The feedstock undergoes a process called catalytic reformation, where it’s mixed with hydrogen gas, often sourced from our old friend syngas, in the presence of a catalyst like platinum. The reaction takes place at high temperature and pressure, 500 °C and up to 50 atmospheres, and converts the long-chain hydrocarbons into ring structures. Distillation and extraction steps separate the BTX products into separate streams, which then go on to produce hundreds of different products.
While none of this is to say that these are all the exact reactions used in the synthesis of artificial wintergreen, or that starting the process with benzene and propylene would be commercially viable — it would be far easier to start with salicylic acid, which is an ingredient used in the synthesis of aspirin, and treat it with some methanol — the string of reactions discussed here trace one common flavoring agent back to its unexpected roots, and points out just how dependent we still are on petrochemicals, even when we’re not burning them.
I feel like I just read the script for a NileRed video, which is meant as a compliment.
Also, kudos for watching ChubbyEmu.
ChubbyEmu rocks!
You missed one thing that lots of persons in sports know: methylsalycylate is used as an effective analgesic for injured muscles (I can’t speak for females, as I’m not one, regardless of the snickering we did as kids regarding access to the girls’ locker room). I can attest to how good this analgesic feels when used effectively. However, I can even more attest to its misuse when applied to someone’s jockstrap or underwear, either intentionally or accidentally — in either case, it just hurts a lot and for a long time. A lot!!!
“Most of us probably have some vivid memories of high school or college chemistry lab”.
Yup, being allowed to play with mercury in our hands as an end of term “special treat”. (UK late ’70s).
Yep. and actually hands on use some metal that vigorously reacted with water. Sodium I think it was. Was soft. By the time our kids were in high school most of the stuff we were allowed to do was off limits … not as fun or instructive anymore :rolleyes: .
Those were the days when we would fill our pencil cases with gas then set them off with splints.
Great article! Also, I feel that I need to appreciate the artist behind the cover illustration. Whoever you are, know that your work has an uncanny ability to make me smile!
Nobody on the editorial staff has piped up so: Looks like another Joe Kim masterpiece.
What Paul said: Joe Kim, our Art Director.
Little known fact: he comes up with most of these without being able to even read the article in question beforehand. I give him the quick gist, sometimes a photo or two when it’s relevant, and he hammers it.
Well this does show that even if everybody drives an electric car we will still need petroleum for a lot of things, it’s not going anywhere. And having read what it takes to make wintergreen I dread to think what it takes to make butterscotch!
Agreed, we aren’t walking away from oil any time soon.
Yes, it’s an awful shame to burn the stuff when there are so many other good uses for it.
It’s interesting how many chemical processes are used to create even quite simple materials. Even aluminum isn’t so simple to extract.
It’s been mentioned before in these pages: it’s not enough to have the elements available in (say) a bunch of batteries you want to recycle: they are still inaccessible and useless until you come up with a cost-effective chemical process to extract the material of interest. A process tuned to extract aluminum from bauxite, or lithium from spodumene (or aluminum from spodumene) is useless for extracting either from a crushed car, or a recycled battery.
The same is true for virtually every material we extract from the earth and process into something useful to us — an extremely specific chemical process is involved.
It makes you wonder how long it will take to establish resource extraction processes for extraterrestrial sources: Moon, Mars, asteroids. How long will ‘the colonies’ be dependent on expensive rare material hauled up from the factories on Mother Earth?
I believe that a lot of recycling innovations are really idealistic pipe dreams. The local recycling company picks up a lot of plastics that can’t be recycled and a lot of glass that costs more to recycle than produce new. The plastic gets sorted and the unrecyclable plastic gets burned and turned into electricity while the glass ends up in the local landfill.
Thanks.Very interesting to me as I want to build a charcoal kiln
to make charcoal to use as a soil amendment.
My research revealed that the amount of condensate per ton of finnished charcoal is alarming!
What I had not considered was tuning the burn for a specific
condensate product,say methanol.
I do know that the pyrolitic condensates from certain fruit woods can be very aromatic.
But for wintergreen what is needed is an old growth pine forest, and little three leaved ground cover plants with little red berries.
Wintergreen oil is good for reconditioning rubber parts. Will bring back some pliability and making it at least useable again. Works good for car and motorcycle intake pieces.
You can produce commercial quantities of salicylic acid with the blue-green algae Anabaena cylindrica.
Excellent article. However, the description of benzene as “each of the carbon atoms … has two hydrogens” is incorrect. A six carbon ring with two hydrogens per carbon would be cyclohexane, (C6H12), while benzene, (C6H6,) has only one hydrogen for each carbon atom.
It would be fun if someone could discribe a green synthesis for biologically important dyes like picogreen or gelgreen.