Even from the very earliest days of the automobile age, cars and trucks have been hybrids of mechanical and electrical design. For every piston sliding up and down in a cylinder, there’s a spark plug that needs to be fired at just the right time to make the engine work, and stepping on the brake pedal had better cause the brake lights to come on at the same time hydraulic pressure pinches the wheel rotors between the brake pads.
Without electrical connections, a useful motor vehicle is a practical impossibility. Even long before electricity started becoming the fuel of choice for vehicles, the wires that connect the computers, sensors, actuators, and indicators needed to run a vehicle’s systems were getting more and more complicated by the year. After the engine and the frame, a car’s wiring and electronics are its third most expensive component, and it’s estimated that by 2030, fully half of the average vehicle’s cost will be locked in its electrical system, up from 30% in 2010.
Making sure all those signals get where they’re going, and doing so in a safe and reliable way is the job of a vehicle’s wire harnesses, the bundles of wires that seemingly occupy every possible area of a modern car. The design and manufacturing of wire harnesses is a complex process that relies on specialized software, a degree of automation, and a surprising amount of people-power.
More Wires Than Ever
The idea for this article came from a conversation I had with Elliot Williams, and an off-hand mention of a chat he had with an engineer who makes software to design car wire harnesses. My first thought was, “There’s software to do that?” which was quickly followed by “Of course there’s software to do that!”. The wiring needed to run a modern vehicle is not something that can be done ad hoc — wire harnesses are highly engineered, both to handle the demands that will be placed on them electrically, and mechanically engineered to not only fit in the space available but to survive the rigors of perhaps several decades of use under challenging environmental conditions.
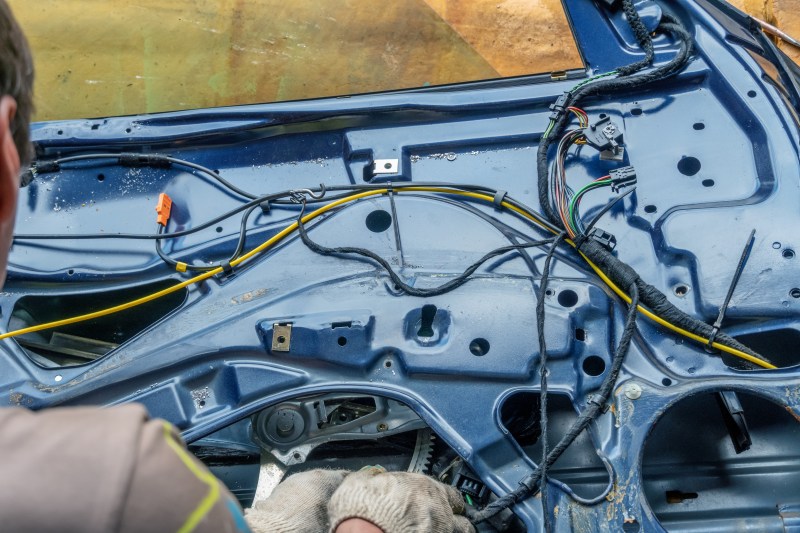
Wire harnesses also have to be manufacturable as separate components. Car and truck manufacturing is increasingly only a final assembly process, where workers add parts made by contract manufacturers to a vehicle’s frame as it rolls down the line. And in fact, wire harnesses are among the very first components added to the nascent vehicle, which is both evidence of their importance to the finished product as well as explaining how difficult it can be to access some of them if they need to be serviced later.
The design of a wire harness starts pretty much the way any complex circuit design starts: with a schematic. In most modern vehicles, pretty much everything talks to one or more of perhaps dozens of electronic control modules, scattered around the vehicle to control everything from ignition timing and fuel injection to HVAC controls and infotainment system settings. Wire harnesses must be designed for each ECM, to provide power and data connections to each sensor and actuator, with consideration given to sizing the wire for the load, providing appropriate ground connections, and making sure the proper connectors are used.
Interdimensional Design
While the initial design process of a wire harness can use more or less standard EDA tools, eventually the two-dimensional schematic representation of the harness has to be translated to the three-dimensional structure of the vehicle. For that job, more specialized EDA and CAD tools are employed. A big player in this world seems to be CATIA by Dassault Systèmes, which has the tools needed to not only create the 2D schematic but to translate it into the 3D space of a vehicle chassis. These tools allow the designer to create bundles of wires, add connectors, define branches off of the main bundle, set the paths over which each bundle will be laid, and look for any contentions between the harness and the rest of the structure of the vehicle. They also allow the designer to specify how the wires are going to be bundled together — tape wrap versus wire loom, for example — and where and how the harness will be attached to the vehicle.
Physical restraint of the harness brings up another important design consideration: slack. Building the correct amount of slack into each bundle and branch of a wire harness is critical. Too much slack is wasteful, both in terms of the copper needed for the extra wire and in terms of decreased fuel efficiency thanks to extra weight. Excess slack can also lead to physical damage to the harness thanks to abrasion on the vehicle body or frame members, or by snagging on road hazards or even being stepped on by passengers. Insufficient slack is a problem, too — wires that don’t have some give may stretch and break as the vehicle frame twists and flexes, and wires that are too tight may make it difficult to undo connectors for repairs. Harness EDA tools are capable of calculating the right amount of slack for a bundle, and of placing hold-downs and restraints in the right place to make sure the wires flex just enough, but not too much.
Once the 3D model of the harness is finalized, the design has to be translated into something that can be manufactured. And since the main manufacturing methods used for wire harnesses all rely on the use of nail boards — more on which below — the painstaking 3D design has to be flattened back into a 2D drawing. CATIA has automated tools for flattening, with the end result being a 2D drawing that details exactly where each wire in a bundle will go, which pin in which connector it will terminate in, and where and what kind of accessories, like retaining clips, grommets, cable ties, or abrasion protection sleeves, will be added. The output from the flattening process represents a complete set of work instructions that can be sent to a contract manufacturer.
Staying in Good Form
With as automated as almost all manufacturing has become, especially for motor vehicles, where production runs in the hundreds of thousands are not uncommon, you’d think that wire harness manufacturing must be completely automated. After all, how could a contract manufacturer be expected to keep up with the volume of harnesses needed by a modern car plant, especially with lean methodologies and just-in-time production? Surely there must be massive CNC machines that use the work instructions to spool out wires and bundle them all together — right?
Wrong. After the design phase, almost all wire harness manufacturing is strictly a hands-on enterprise. As it turns out, human dexterity and eye-hand coordination are really hard to match with robots. Wire harness plants employ thousands of workers to hand-assemble almost every piece of a wire harness. Yes, there are tools to help, but most of them are used to cut, strip, terminate, and coil up wire that will eventually be used by the human workers to build the harness, one wire at a time.
The traditional way of building a wire harness is on a nail board. Also called a form board or harness board, this is essentially a large flat surface to which are attached a variety of fixtures to temporarily hold wires and connectors. The fixtures are laid out to represent the flattened design of the harness, and instructions printed on the board show which wires are to be routed where. Boards are usually worked on vertically, leaning back at a slight angle to keep wires from falling off before they’re secured.
One worker rarely makes an entire wire harness. Instead, a chain of identical nail boards is looped around the factory floor on a powered carousel, slowly and constantly moving from one worker to the next. Each worker adds a specific set of wires to the growing harness before the board moves along to the next worker with a different set of tasks. In addition to placing wires, some workers are responsible for securing bundles with cable ties, adding protective sleeves, or wrapping the parts of the bundle in loom tape.
It’s these fine motor skills that make full automation of wire harness manufacture a difficult proposition. Threading wires through a length of plastic wire loom is a trivial task for most humans, but would be difficult to build a robot to do. It’s worth noting, however, that this is true mainly because there are plenty of people willing to do such work for relatively low wages. Companies like Yazaki, which currently has about 30% of the global market of wire harness production, employ hundreds of thousands of people around the world, particularly in developing areas. Economic forces currently favor the continuation of this model, but as we’ve seen time and again, eventually everyone wants to be able to buy the stuff they’re making for other people, so the supply of workers willing to do this kind of work for low wages is limited. Perhaps then it’ll make sense to invest in full automation up and down the wire harness production chain.
What is it with car wiring schematics? I’ve been reading them for years, but still the format seems crazy.
And, different per manufacturer.
A feature on the history of these (and any conventions employed) would be good.
The Haynes ones are just as bad, I assure you.
The “Project Binky” guys spent a gargantuan amount of time essentially building a fully custom harness for their fully customized Mini, some of which was taking apart a donor harness and re-splicing connectors and re-pathing everything.
About the only universal standard for wiring in cars is ‘black = ground’ and ‘red = battery voltage’, although I could be wrong about both of those.
TVR’s standard was ‘black = everything’. How I laughed as I merrily made my replacement loom…
At least some companies will label individual wires for identification when they use the same color.
In rewiring my old Ford truck, I have the choices of buying pre-made harnesses, building my own with “period correct” and “model correct” wires and connectors, or just doing what I can with reasonably priced alternatives.
(I am choosing the latter option)
Exactly
John Deere always printed a three or 4 digit number on their wires, every 12 to 24 inches.
Made diagnosis and repair easier.
Ahh yes the old fully black loom. Luckily both of my wedges are colour-coded.
@J Cook, brown for battery +, and there are some other conventions in the UK.
I worked in aerospace. All our harnesses were white teflon coated wires…
I worked for a company that used all-pink (with numbers). It stopped the customers thinking that they could fix it without talking to us.
I still use a lot ot pink wiring. Nobody assumes that pink is anything in particular.
I think that I recall reading that a UK (nuclear?) missile had an unmarked all-pink wiring loom and a pre-installed cable-saw at the thickest point. The abandon protocol was to saw throiugh the loom (probably as step 1).
Excellent point, Bad Obsession showed all of it’s fans that there is nothing too complicated to not do slowly & carefully, exception being “let me just do this quickly”…and most of us KNOW what happened next.
More bracketry. And Tea. Time to get the FUNK out!
I would call Brown for Ground in most vehicles I’ve worked on . VW SAAB Chrysler
Funny that – I would say that brown is more often used for +12.
Sorry to say you’re wrong – I once had to intervene with a chap attempting to jump-start a Vauxhall (Opel) because every time he tried to clip the last lead on there were sparks flying – turned out WHITE was negative and BLACK was positive, but the grime on top of the battery was obscuring the markings.
Brown is also common for battery positive, on older British cars (BL/JLR etc.) the wiring standard is brown for unfused live, purple for fused live.
Also worked on a Peugeot where there were only 4-5 wiring colours and the whole loom had ID’s printed along the wires – which rubbed off if you handled the wires.
Why they do it I have no idea, they can buy wires in any damn colour they like.
Brown is ground, at least for MB, and I think many European manufacturers.
I got roped into making some automotive harnesses. That turned into a bit of a cottage industry. Still have the nail boards hanging in the garage.
Hella Gutmann makes really nice consistent and colored wiring diagrams that are layed out exactly the same regardles of car brand. It is available in their “HGS Data” that workshops can subscribe to.
If you have seen a wiring diagram for parking brake on a Volvo you will instantly understand the parking brake diagram for a Chrysler when you see it since they use the same colors and layout regardless of brand.
Throw out the wiring diagrams…
Only half kidding, a lot seem geared to tracing premature open circuit component failure. Get anything other than that and they’re useless. Wire crimped from otherwise minor fender bender, hinge wires fatiguing over time, components having weird failure modes at end of life, and corrosion other issues doing unexpected things, animals chewing on things, either stupid squirrels externally, or little bugger mice getting inside. All and any of that, you will be going round and round in circles for hours, even days, following official wiring diagrams and service procedures. It sounds longer, but it’s quicker to work the car over from one end to the other systematically with a good multimeter. Half the time they leave off the options anyway, and fail to mention where they are routed and tapped concurrent to main harnesses… and don’t isolate them.
I can attest that I have run across so many vehicle wiring diagrams (even official manufacturer documents) that just had to get thrown out. Once I learned the hard lesson that assuming one was correct could lead you to burn out a lot of expensive stuff. Never again, always tracing things now.
Honda actually had a set of ETM electrical troubleshooting manuals for each car. Had wireframe pictures of all ground points and connectors. I firmly believe this is where they got some of their reliability cred. If its fixed and back on the road it’s reliable.
Contrast with Dodge who leaves connections in the fender unsealed and the relay to the fuel pump buried in a $1000 box
I still know all my colors in German because that’s the only way I could find documentation for an old BMW bike.
And I know it’s a manual process because even the factory harnesses I’ve had to rebuild all came wrapped up in miles of gummy decades-old electrical tape! Huge pet peeve of mine. Leaves everything sticky and vaguely blackened, hard to tell what color is what.
I work for a large equipment company as a design engineer. Most of my work is mechanical but sometimes I have to design wire harnesses in the automotive style. It took me months to really learn the style… Even with all of the specs and standards we have. The most difficult part is usually CAN network requirements; splices have to be positioned to meet length requirements between the trunk and branch of the circuit. So sometimes I have had harnesses that have wires running the “wrong” way, and loop back over itself.
I used to work in aerospace design, and talk about frustrating wire harnesses. While all the wires are marked for their full length, in most cases, wires are all the same color regardless of function. (Usually white).
Engineering software meets technical publications department.
Used to work in the field. Amazing machines already automating with high precision. For small harnesses already fully automated. Also interesting for individual configuration in small to micro size batches.
https://www.youtube.com/watch?v=psuForISqQ8
As soon as the harness size increases e.g. towards car or rail coach there is still a lot of manual labor involved but heavily assisted trough smart or interactive assembly tables, directly including testing and more.
In many applications the cable harness is the most expensive part of the build and with growing electrification the trend will probably remain.
Still and always will be amazed by the beautiful, high precision Komax machines.
Cheers
Get rid of all the wires and replace them with thousands of tiny insect sized bots relaying packets of data and electrons around the inside of the car body.
Right. Then nobody’d be able to do business with anybody else. Haven’t you heard that every country accuses nearly every other country of human rights problems?
I’m an American, but I am well aware that people in many European countries look at the US like they look at China.
1. Death penalty.
2. Arbitrary enforcement of the law.
3. Lack of protection for private information.
Let he (or she) who is without sin cast the first stone.
America, for all its flaws, only puts small numbers of people in the concentration camps at guantanamo, China puts hundreds of thousands in the concentration camps in the Xinjiang region. America is not (yet atleast) running a social credit system, though they’re dangerously close with overly digital “money” methods being developed. America has not (yet) entirely forbidden the press to criticize the government, though its gotten most of the mainstream to refuse to question certain narratives. America has not yet condemned whole cities to starvation in an insane attempt to look like they can stop an endemic and thankfully reasonably mild disease. The american security state complex has committed many crimes against humanity, but China is doing much worse still.
… based on the information you have, coming from the Western MSM.
To truly understand, one would need to read Chinese point of view, and then actually travel through the area and openly ask locals.
This “we are holier than thou” attitude is very common. Usually without full picture. After all, you can imagine what information is Chinese government putting out. For their citizens that is the truth. Just like you, they only have limited information.
I think this is a false equality. In US information access is not blocked or censored by the government. I can watch RT or Al Jazera or the BBC, maybe not on TV but I can find them online. Not true in china where everything is filtered.
There is 0 incentive for AP to push a false story about concentration camps in China. If you believe there is some mass conspiracy controlling all “western media”, I have a bridge to sell you.
There’s no conspiracy, just $ interest. War for example is very profitable for the Western MIC. This is why US was at peace in about 5% of it’s existence. No hard feelings, only profit.
It’s hard to find a country so addicted to war. Your own president said that.
Re Chinese censorship you are probably right. But many topics are taboo in the West and have been for some time. In China too- just different topics.
The video is the Yazaki plant in Ukraine.
Their problem seems to be that they do respect human rights (and were hoping to sign up the European Court of Human Rights) and their bigger neighbour wasn’t happy with that.
I think their “bigger neighbor” was unhappy about a lot of things.
B^)
Love your passion. I don’t entirely disagree with any of your comments, but I do (respectfully) think it’s a little oversimplified.
Questions like “What are human rights?” (when honestly in the US we can’t even agree who a ‘human’ is), or when you start throwing in that loaded word ‘deserves’ into conversation are hard, and more so when you want to get 7 billion people to agree to the answer.
And when the United Nations allow countries such as North Korea or Myanmar to sit in leadership roles of the Human Rights Council, even the countries with good human rights records get called out.
I’d say that if my comment was oversimplifying, then simply calling it “Economic forces” was the same, only much much worse. From a “professional” writer too. Just call it what it is: decades of selling out the economy to make things look better right now. Rack up national debt, outsource every single job you can, raise minimum wage again and again and again with no justification except “we want more and we buy from countries that don’t deserve higher wages”, and call boomers “successful” because the house of cards didn’t collapse until they were dead.
I only wonder if they really don’t understand why their name is a curse and an insult to the generations they abused. Cause yeah, having kids pretty much just so they can pay off your debt for you is child abuse.
Imagine having a kid and deciding to leave them, not with money, or advice, but just with the debt you don’t want to pay off yourself. Subfckinghuman.
Yes. Economic forces.
You can’t wave a magic wand and have everyone all across the world suddenly receive the same pay for the same work.
Assuming you could raise the wages of the folks making the wiring looms just by waving a magic wand and making the companies pay higher wages, do you know what would happen?
Chaos.
If you pay a part of the population a drastically higher wage, then those higher paid people become targets for the anger of the other citizens. Prices go up, pricing some folks out of home and food.
It would be great if everyone was paid decently and everyone had decent access to needed goods (food, shelter, etc.) Even better would be if we got all that and decent government as well.
All of us are working on it.
Things are getting better. Slowly.
Keep grinding away at it.
Make things better where you can, and if you can’t then at least try not to make things worse.
“Even long before electricity started becoming the fuel of choice for vehicles,”
I would argue that it isn’t “the fuel of choice”, unless having it shoved down our throats by government is a “choice”.
What do you think governments are?
It is not strictly a fuel at all, the fuel in question is what runs the power station which produces the electricity such cars harge with. The “fuel” for electric cars therefore is often coal. The same would be true for hydrogen cars, with some loss of efficiency, but atleast hydrogen has enough energy density to have a decent driving range an doesn;t take hours to refill the tank. And bring on more nuclear powerplants, fast.
Often?
So %1?
Seems like “often” is your way of misleading people without technically just outright lying. So what is “often”. About one and A HALF percent. Kinda like you’re lying to yourself and everyone here.
Robert is right. And he’s not lying in the least.
The “fuel” for electric cars *is* often coal. In the United States 21.8% of our electricity comes from coal. If you add in oil and gas, the share of electricity generated by fossil fuels is 60.8%
source: US Energy Information Administration https://www.eia.gov/tools/faqs/faq.php?id=427&t=3
Now, it’s true that the laws of thermodynamics strongly favor large turbines over small engine cylinders, so, on net (after extraction, distribution and storage for both options) electricity is much less polluting per mile, but it is still important to remember that electric cars, as experienced now, aren’t *non* polluting, just more mitigating.
That being said, mitigation is a valuable tool in and of itself. Every joule you don’t waste is another Joule you don’t have to create over again.
Excellent example of an ad hominem attack.
The choice is to “use electricity in cars” or “kill the ecosystem”. Electricity is the fuel of choice for the sane.
You dropped your disclaimer:
“This statement brought to you by Fossil fuels supplying a power grid that can barely sustain current loads of your average day.”
Yes, if there is one thing we can say about the fossil fuel industry is that they have been ramming electric cars down our throats for the past 40 years.
Also, you in 1903: “Do you have any idea how big a gasoline supply infrastructure we would need to replace ALL the horses? It’s a fun rich man’s toy, and it has a few niche uses, but that’s all it can be”.
An awful lot of youtube nay-sayers claim that an electric vehicle is no better (often worse) than an ICE vehicle, and that may currently be true.
However, every single one of them fails to acknowledge that as power stations divert away from fossil fuels, the electricity used to power/charge those electric vehicles becomes ‘greener’ over time.
Something an ICE can never do.
“ICE can never do” is also not strictly true, there are plans for making internal combustion engines able to run on hydrogen. Less efficient than fuel cells I have heard, but still more practical than batteries.
Not only that but even the most ardent petrolhead has to admit that electric motors vastly outperform any equivalent ICE motor and are a pretty damn perfect way to power a vehicle – full torque from zero, very fast response, incredibly accurate speed regulation (you can drive it like a stepper), massive engine braking with regen, and very few moving parts with none of this reciprocating nonsense.
Sure they’re not as exciting and they don’t make good noises but for 99% of vehicles no-one cares about that.
Witness both Pike’s Peak and Goodwood records falling to EV’s in recent years.
I’m sure the John Deere DRM’d electric tractors will be a big hit with farmers.
Oh, wait! The USA will only have collective farms by that time.
False Dichotomy. In a true comparison between an ICE and an electric driven vehicle, ICE wins. Hands down. The electricity is very wasteful to produce, transform, transport and store. If you take that into account and provide an ICE vehicle with the equivalent power, every Toyota Corolla will be transformed into a Top Fuel Dragster. It will smack a silly little Tesla until it says uncle.
But hey an electric vehicle allow you to demonstrate your passion for child labor in Africa’s lithium mines and your derision for the environment because of the batteries production process.
Electric vehicles are a 150 year old stupid idea that does not want to die.
At what point does cheap labor become exploitation?
When they fired you to hire it.
When it is me who’s being exploited?
B^)
When you’re actively donating billions in cheap food and medicine to poor overpopulated countries because benefit from their continued astronomically high birth rates that keep the population of desperate people high enough, because otherwise yknow, famine, because they don’t need the education or technology to support themselves, just the cheapest food we can supply and jobs at a factory.
“sorry you can’t support yourself now working in my factory here is some bread and water to feed your kids, have some more so they can all work in my factory, for even less, because overpopulation wi be e en worse.
But don’t worry their grandkids will have all the bread and water they could dream of!”
most labor is exploitative under capitalism
profits = revenue – costs, and all of that revenue (and therefore profit) is generated by the workers’ labor, but the profits are either reinvested into the business (which the workers don’t own and won’t benefit from economically) or the profits are paid out to the business owners, essentially stealing the surplus value generated by the workers
any profits paid to owners instead of workers is exploitative, and the bigger the profits get, the more exploitative it becomes
This isn’t the first time “oversimplification” has been pointed out in the comments today, but IMO it is the most extreme. In a democratic capitalistic society (not one where the capitalist nations trade with communist or fascist nations), competition allows workers to choose amongst many different jobs (even in the same industry), often obviating any perceived exploitation. Let’s say I have a mom and pop grocery store with myself as owner/proprietor and 2 full-time employees that receive an excellent wage: would I be exploiting them if the store lost money this year but they still received their pay? What if I (as proprietor) made the same wage as them, and reinvested profits, would that be exploitative? What about profit-sharing for employees vs. bonuses based on productivity? What if I hire a manager, who receives a higher wage than the 2 employees: would that mean I as the owner would be exploiting all 3 of them if I took a salary? Would the manager be exploiting the 2 workers? I think your terms are too extreme. Not everything is exploitation simply because of a lop-sided power dynamic. Reducing exploitation of workers is a lofty goal, but one that is pursued in every real democracy. (And it’s an achievable one- in the US look at the minimum wage, labor unions, the FMLA, OSHA, etc.). Not that we’ve solved the problem, but at least in a democracy we can attempt to allow equal opportunity. I know where you’re coming from- I’ve read some pretty compelling theories too (like the ones that fueled fascism and genocide, or prompted the French revolution), and I know how appealing it can be to believe that controlling the means of production or restricting profits would bring better opportunity or completely eliminate exploitation, but I dare you to follow your logic through to an actual framework that wouldn’t end up overthrowing the current dynamic just to exchange one group being exploited or oppressed for another.
I worked for a small batch wire harness contractor here in the USA. Wire boards were the way harnesses were built. But adding a 3rd dimension to a harness was possible by adjusting the length of wires making a curve, slightly shorter wires inside the curve and slightly longer wires on the outside, just like 2D layout. Some of the harnesses needed to curve at a specific angle to branch off the main artery to attach within the space available in the final product.
The final step was fabric looming, which is an interesting process in itself. Different colors of tape signaled the loom operator when a branch occurred ot where to terminate the loom on that branch.
I worked for a company that made floor care equipment. Everything from vacuum cleaners, floor buffers, solid surface cleaners up to big ride on scrubbers. Picture a small street sweeper but for warehouses etc. Every harness was built on nail boards. There were a couple of people who stripped then crimped connectors on a special machine then those wires were placed on a cart in indivdual boxes sorted by part no. The cart then went to the nail board where the wires were placed and then loomed. There were only a couple of people who could handle the wire boards because of how tedious the work was. The one guy was with the company for 17 years and loved wiring the boards. The other was a lady who was there for 15 years. She also cut vacuum hoses. 400 FT roll of hose cut in 12 FT lengths. Over and over again. I worked in quality control and one morning got stopped by a line lead who stated that all of that mornings machines were failing because the vacuum motor would not run. It was determined that the stripper crimper people failed to strip the motor wires and then crimped on the connector. In other words the connection was crimped to the outer rubber of the wire. IIRC about 300 looms had to be reworked. Flag terminal cut off, wire stripped, flag terminal crimped back on. 2 connectors x 300 looms = tedious.
I, too, worked for a small outfit and made harnesses for Uncle Sam. I recall the paperwork given to all of us “ managers” quoting misteaks and the labor cost to fix them…then we were told “no problems, the next shift will fix it good”… and all the work was dumpstered and we moved on…doing it all again, but hopefully, correctly.
A long time ago a Boeing worker crossed two wires on one of these harnesses, they were the oil pressure indicators for the two engines. The oil drain plug on one engine was loose and fell out mid flight. The pilot saw the pressure loss, shut down the wrong engine and soon had no engines, plane crashed with loss of life. Be careful with those wires!
Why didn’t testing/quality control/certification catch this error?
“Why didn’t testing find this”
Someone needs to write the test. Sometimes the test writers lack imagination. (I write tests)
Reminds me of the guy that purchased a brand new Eddie Baure Bronco some years back, waited several months for all his custom options and when it finally arrived, he took it home and got sick of listing to the dinger with the key in ign, and door open. He started tearing into the harness looking for the wire that would kill that dinger and it finally got to the point the car wouldn’t start. Called up the dealer for a transporter and when they got it back to the shop, informed him it would be 6 months for the replacement harness, why that is I don’t understand, seems the wires could have been spliced but since I never saw the mess, maybe it was beyond repair. Anyway, the guy asked if it would covered under warranty? NOPE, the bill came to around $10k. I think. Been a while since I heard about it, but no matter, I hope the guy learned his lesson.
I hope the manuf learned their lesson too: NOBODY LIKES DOOR DINGERS
“Local Moron Decides to Cut into a Mass of Wires Rather than Disconnect Bell”
Seriously, that’s pliers and just a relay pull, certainly?
Nowadays it’s part of the entertainment system. The chime and even turn signal “clicking relay” comes through the speakers
My beef isn’t the wires but the connectors.
I’m looking at you, locking connectors that I’ve never seen before and have to figure out by feel while upside-down and backwards with my hands two feet deep between sharp metal brackets.
Seriously, if we can mostly standardize fasteners, which have a much more ‘form-must-follow-function’ thing going, then there’s no reason that every single manufacturer has to use their own different connector. Don’t even get me started about the way that you’ll find twenty different connector styles on one car.
If i were the the dictator of wires my first decree would be that only, say, 4 standard families of connectors would be allowed. That should give you plenty of options. Any engineer who violated that rule would be sentenced to ten years hard labor installing random plugs in a hot, poorly lit repair shop while standing barefoot on a pile of old plastic connector shells while an angry customer berates him about the cost of repair parts.
“I’m looking at you, locking connectors that I’ve never seen before and have to figure out by feel while upside-down and backwards with my hands two feet deep between sharp metal brackets.”
Bravo!
(Especially those 10 years old that have lost flexibility)
@ SteveS I fully connect with you on connectors. I’ve owned G.M. Ford Toyota and finally Chrysler. All the cars had the same kind of connectors. Push the little tab and seperate. The Chrysler is the bain of my existence. Upside down and backwords connector at top of firewall for crankshaft position sensor has a little red tab that moves to the side and then push down super short hurt your finger little tab to disconnect. All the (I own a jeep wrangler) connectors are the same and most it is hard to get to the little red tab. You can tell the ones I took off because there is no more little red tab:)
But since I am related to Murphy, I appreciate it when cables that terminate in the same general area have incompatible connectors!
DAMHIKT!
Keying pins. When using multiple similar connectors keying pins are your $0.02 friend
I won’t argue that!
Fellow Wrangler owner. The confluence of Fiat and Chrysler engineering is a wonder to behold…and not in a good way.
Recently replaced the spark plugs and some of the plug coils on a RAV4. All the rear connectors to the plug coils had the see-saw retainer shatter. HEY! PLASTICS DESIGNERS! LIVE HINGES CAN DIE. Fortunately I had bought a full set of replacement connectors with pigtails; I unpinned all the replacements and then unpinned all the ones on the car, and replaced the connector pins into the new housings.
“Just the wiring inside a door of a typical car today probably exceeds the complexity of an entire car’s wiring from just 30 years ago.”
As an owner of a 30 year car that I work on myself, this statement is incorrect by many magnitudes…
Motorized mirrors, with heating elements, cameras, turn signals, radar: doors with power windows and locks, keypad entry, speakers, curb and door jamb lighting…
Lions, and tigers, and bears! Oh my!
My 1992 Subaru SVX has more wiring harness in the door than my entire 1973 Toyota Land Cruiser (FJ55 model with electric rear window and other bells and whistles). The SVX is only missing cameras, radar and keypad entry, and the rest of the car has plenty of wiring harness complexity. This is an OBD1 vehicle, so no efficiency benefits from the use of a CAN bus.
People tend to forget that 30 years ago was 1992. Even Geos back then came with bells and whistles across the vehicle.
I think that comes from thinking a 30 year old car was built in the 1960s or 70s.
Which many of them may as well have been – takes quite some time depending on just where in the world you are (and if you are wealthy enough for the most premium/import models) for the primitive almost electronics devoid cars to turn into the high tech car phone type stuff that begins to be common in the later 80’s and 90’s.
Certainly not ever 30 year old car is going to be 60’s and 70’s primitive. But I’d bet globally still more than half the production 30 years ago were not far from it, perhaps with added luxury of a cassette player…
30 years? Yeah cars in the 90s had plenty of rats-nest wiring, you’re correct there. Add a few more decades and we could talk. Ah, to work on an engine with magneto ignition again.. Nothing but head and tail lights to worry about.
Hot-tube ignition and acetylene lighting, that’s the way to go.
(1895 Leon-Bollee for example)
The statement that cars have _always_ had some electrics isn’t entirely true, though it is nearly so.
Electric lighting was still pretty unusual at the start of WW1. Lorries for military service often had oil lamps, not even acetylene.
I have a motorcycle with hybrid lighting, the front has one electric and one acetylene lamp, and the rear has a combined lamp with both an acetylene jet and an electric lightbulb. That last item might be unique to the marque.
I worked at a place in the 70’s that made harness for Ford including the “backseat-barbecue” Pinto that ran thru that fire zone. We made at the time the largest harness in the industry for the Lincoln mark 4. This was during that dreaded “seat-belt interlock” era. This was under the dash from the bulkhead connector and plenty of fuses on the fuse block to everything under and behind the dashboard. The middle of it was thicker than your wrist! Of course Fords had more wires just to light the dome light than GM so go figure.
We never had nail-boards but jigs in 3D, Only the testers had flat boards full of flip on plug connections and it stepped thru a stepping relay each circuit and would stop on a dead one. Jiggle that point and on it went, till it passed. Just like pinball machine scoring of the era. Quality took a dive and then they took the jobs to Mexico. I left before we had to strip the plant of everything we maintained. I went from poking wires on the rotary to maintenance of many of the process machines, most operated by women.
Push-Click-Pull
This definitely scratches that “nice to know” itch…
https://youtu.be/pSNe4l3s0gQ
After years of working on industrial and agricultural equipment, I always wondered if it wouldn’t become more economical on more complex machines to just design and run a standardized common harness everywhere in the machine.
Something containing like, a single 1 gauge wire for power, a single 1 gauge wire for ground, and two twisted pairs for a pair of CAN busses.
Then, everything connects to the bus, or a local “gateway” controller instead of long, individual circuits.
Or at least, this may have been feasible in the before times when chips like CAN transceivers were cheap and plentiful.
Good news!
If you own a modern car you will get to replace a rear end/hatch computer soon. Just as you describe. Car vendors say: Parts are profit, lets make more stuff break on a schedule.
Automotive engineers are no longer taught KISS (Keep it simple stupid) rather MISS (Make it shitty smarty).
Aren’t modern cars statistically more reliable? I imagine people just think they’re unreliable because they used to do more work themselves and thought of continual small fixes as normal, wheras they probably get more upset with replacing a computer even if total cost and downtime hasn’t significantly increased.
Same with Linux, where people will say a distro is reliable, even when they really mean “Reliable if you do everything exactly right with a few minor glitches I can solve myself”.
How are you measuring reliable? As that really matters to make any real determination – the same improvements in production methods and so fit and finish of the mechanical parts should lead to similarly if not more robust dumb cars, as long as the owner does the basic maintenance checks they are supposed to.
Which is what the computer on wheels largely makes irrelevant, as it is adapting the way it runs to make up for the lazy owner problems in ways that usually prevent catastrophic engine damage (etc) being possible. But on the other hand it introduces a whole new world of failure points that are pretty mission critical, some of which are really quite awful – as its now a computer on wheels with really lousy security that can only make the whole thing run if all the sensors (that usually don’t have any backups) report back properly.
So in terms of maximum possible lifespan – always going to be easily fixable, can rely on it for decades the computer cars are not I would suggest nearly as reliable as a more traditional car IFF its operated properly, as they have too many extra points of failure for which a compatible substitution is harder to create. But that is a big if, which is where the computer cars could be considered more reliable, as without any real care or comprehension of how to look after it, it will just work between the mandatory MOT check type stuff where the experts can fix all the stuff that should have been done.
No.
Cars were most reliable and durable from the mid 90s to early 00s. The change to 20 weight oil hasn’t helped, skinny racing style rings etc. Much less putting a turbo 4 banger in a truck. (Those are rooted in CAFE standards though, so blame DC lawyers playing Engineer.)
Also the Germans have _perfected_ the warranty timer. Take that GM. Car companies hate cars that go 250k+ miles without making them any money, hate, hate, hate.
Granting 250k miles was never anything except the worst rotten dog eurotaxi Benzs (300D). More a Honda thing.
It is already here in some cars/parts. When I worked for a manufacturer of steering wheel circuits, Steering column stalks (e.g. washer/wiper or turn signal) the 4 wire system you mentioned was frequently used (fewer conductors to wear when flexing). Some things like the steering wheel heater and the air bag igniter did have their own circuits.
That’s a trap. Do that and they will add more complexity. Then you will eventually end up with a car wired bumper-to-bumper with CAT5 and HDMI cables or some horrific thing like that. And a tail light bulb will have a chip with DRM on it like a printer cartridge that phones home and makes sure you are using official replacement tail lights.
Isn’t this already a problem with Buick taillights?
As I recall, there were several models in the last decade that did away with the usual discrete wires for each bulb and just ran power and CAN bus to a modular taillight with an embedded controller.
And then the water got in, and the boards started failing.
But those cars had never been big sellers and GM hadn’t made enough of the Buick-specific lights before retiring the tooling. Their spares inventory was quickly exhausted and there were never enough cars to be worth making new parts again.
So now your 2010 Enclave can be sidelined by failed taillights while you search the planet for a $2000 part made of unobtanium.
When I first heard of this I actually thought “Hmmm… now that’s a plan for some side income when I retire, I’ll set up a little shop to rebuild tailights at $500 a pop”
I’ve watched a DIY channel on youtube: Jafromobile: https://www.youtube.com/user/Jafromobile, where the car owner used donor engine harnesses of dubious reputation and did Further hacking on them to suit his needs. In the end, he caved in and did the one thing he didn’t want to do and that was make a brand new engine harness (from scratch) and rewire the car the right way. He spent a lot of time chasing ghosts related to the donor wire harness. https://youtu.be/MP37hcFOmKU.
I just finished rewrapping my 2018 Honda cb500x harness after I shorted it out. No fun but informative…
On my 2010 PT Cruiser the wiring harness points of failure are corroded ground leads attached to inner fenders under the hood. Many other PT Cruiser owners have failures of the Power Supply Module aka TIPM which will set you back about $700 for a new one if you can’t find just the right one in the junk yard. After 10 years of use the plastic wire looms are falling apart and disintegrating.
Why do modern replacement LED headlights cost thousands of dollars?
Makes you want to go back to sealed beam halogens.
My current project is adding factory new old stock driving/fog lights to my 1995 Ford Thunderbird. You would think it might be cheaper to build every car with all the accessory wiring in place but nope, have to build it from the ground up.
Wiring harnesses getting mroe complex with time? Surely not, in the past every actuator or sensor would need a direct set of multiple wires to it, now surely everything shares a data bus so the entire harness is just data lines, power (maybe at mroe than one voltage) and ground. Not saying necessarily simple, but surely simpler than having to have many specific sets of wires solely for use between many different point to point runs? The complexity is offloaded in to the software on microcontrollers connected to the bus to ensure a faulty device can’t crash the comms for everything.
Even if every electronic part of the car needed just one wire doing power and data at the same time with the ground being the car itself it would still be getting more complex as there are now so very many more electronic parts!
Early days you have a few lights, later you add in more lights for different climate conditions and indicators, then there is the door locks, windows, sunroof, the ever increasing speaker count required to make the ever more complex and capable infotainment systems actually worth the effort. And that isn’t counting the extra wiring in the engines and dashboard themselves as time has gone on and almost all engine control is entirely electric rather than mechanical/physical linkages.
ISO standard says BRN is “hot”, BLU is “0V” GRN/YEL is Protective Earth. I find that sensors made in EU countries usually use BRN for +DC, BLU for 0V and something else for “signal”.
Sure, but modern cars have a cacophony of electrical systems. There are power wires, there are signal wires (CAN), there are high speed diff pairs (GVIF and Cameras), coax cables for GPS and 4G antennae, there is Ehternet or FlexFay and to complete the mix throw a few fiber optic wires for MOST.
How much of that could be replaced with just a single CAN+Power cable, and appropriate use of repeaters?
Cables, connectors, and switches are such a common source of problems. It’s easier to make the (Reliable and cheap) electronics more complicated than add a bunch of unique cables with nonstandard connectors that someone is going to have to buy on eBay from a scrapyard to fix anything.
Wanna bring all the manufacturing home and avoid having to use euphemized slave labor in other countries? Get ready to start a war with a few of them. I wish we never shipped it out as well.
Can’t wait for SPE/PoDL (single pair ethernet with powerr) to replace all this legacy junk.
Cept it wont cuz wire gauge wont transmit enough current for many parts. Data lines maybe, but most of your wiring ends up running dc motors and power hungry lamps, solinoids, etc.
50w is enough for sensors and much else. Power windows, wipers, main lights maybe need their own power, but if you switch them at the device with a ethernet-controlled and powered relays, you can just run a ‘high power bus’ to devices that need it. Currently such devices are often switched centrally, with power wires routed out to each device individually.
50w is enough for sensors, and much else. The rest can be switched with ethernet-controlled and powered relays from a ‘power bus’. Much simpler wiring than providing centrally-switched power to each device individually.
Making every sensor a CAN node would be relatively expensive. Maybe only pennies per sensor, but with that many sensors and millions of cars, it’s a lot of money.
Also, there is a limit to how much data you can fit on one bus. Current production vehicles from my employer are maxing out 5 CAN buses (three of which are running CAN FD) and that is with a topology where many sensors send analogue voltages or PWM to a local node for processing.
But that’s the point, SPE will replace CAN.
I have cut and rebuilt and in many cases made new wire harnesses for rally/racing cars.
You can sva lots of weight by only connecting what is needed, and not using thicker cable then necessary.
As i was scooled on airplanes, I prefer sewing the harnesses with tread instead of using zipties/tape or even plastic tubing.
Of course I use plastic tubing to protect the cables where needed, but not more
Reading a car magazine about 12 years ago I came across a story of a Mercedes with a problem. Brand new car, customer drove it off the lot and 1 week later the stereo stopped working. After a large number of stealership visits later including replacing the stereo (5,400 $USD) replacing several wire harnesses (over 11,000 $USD) and a bunch of other parts and pieces Mercedes gave the guy a new car. The stealership tried to repair the car to no avail. Mercedes called the car back to Germany to determine the problem. The engineers went over the car and finally found the problem. A wiring harness that goes to a computer in the trunk of the car for the subwoofer. You see the wiring harness has a fiber optic link to the computer in the trunk and a screw in the driveshaft tunnel had poked the fiber optic and made it intermittent. Cost of the car new at stealership 110,000 $USD. Cost of repair including shipping and engineer time, etc. 131,000 $USD. At what point does making more complex systems become not worth the cost? And cars have only become more complex think “drive by wire” “throttle by wire” “accident avoidance system” “traction control” etc etc etc.
Awww, MB and the dealership made up for the losses with the next 2 cars they built and sold!
B^)
First rule of wiring looms is don’t expect the colour to mean anything sensible. That’s the safest approach. I took out the carpet in my VW passat to dry out the wiring for the CCM module (controls windows, doors, sunroof and locking etc) after a water leak from the engine bay seal had failed. I documented some of the looms for myself to fix corroded wires but found a real oddity. One big black wire turned out to be the Window washer wipe tube from the engine bay compartment going to the rear window wash incorporated in the loom. How’ that for wiring colours? Black is certainly not always ground and in a VW you may get a real surprise!
Why manual? Have built and programmed a machine to automate that for a company in Europe.
Wow, that product sure does simplify the look, complexity of the electronics.