Buying a desk is all well and good, but [WoodCraftly] found that the options they found online were too pricey for what was being offered. Buying the table frame from scratch was much cheaper, and just required crafting a top to match. That provided the opportunity to create this beautiful herringbone-finish desk created with some simple woodworking techniques.
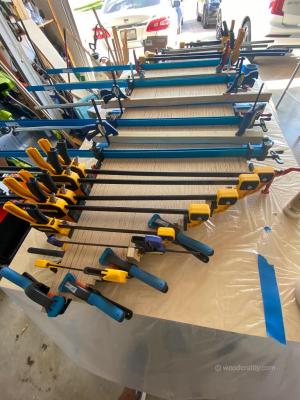
The build starts with a motorized corner desk frame that can be bought from amazon for just $550. To create the chevron-finish top, [WoodCraftly] grabbed some plywood sheets, and cut them into a series of 1-inch strips. These were then flipped 90-degrees onto their side, and glued together to create a panel that showed off the individual layers of the plywood. This panel was then cut into 3-inch wide strips at a 45-degree angle, and these strips were then placed back to back and once again glued up to create the attractive herringbone design.
From there, it was a simple matter of gluing up panels into the L-shape required for the desk, adding mounting holes, and rounding off the corners for a nice finish. The desk was also given a thick coat of epoxy on the bottom which soaked into the wood and helped give the desk some strength, and a top coat that was sanded back to a natural-look finish.
Overall, the final desk is just the product of some smart cutting and gluing steps combined to create a fun pattern in the end. It’s always fun to build your own furniture because you can express your own style in your creations. Video after the break.
https://www.youtube.com/watch?v=K8beIaBkeiM&feature=emb_title
I’ve made wood plane handles out of stacked and glued 6mm plywood and they look fantastic but the wood itself isn’t very durable and wears/dents pretty easily. As such, if you’re going to do this I’d definitely recommend using oak plywood as your starting material, not cheaper construction plywood. But it sure does look fantastic, and his choice of birch plywood is probably a good one. That’s definitely tougher than what I used.
Could you post a photo of one of the plane handles?
I have a soft spot (in my head?) for old tools.
If you use maple ply, it holds up a little better then a few gunstocks are made from maple plywood
*more than
My kingdom for an edit button
I support your view! We want an edit button!!!
Please
“…just the product of some smart cutting and gluing steps combined to create a fun pattern in the end”.
It may be “just” to some but if I attempted something like this it would be a gluey mess!
Jill Taylor:
Don’t you think you should go to the emergency room?
Tim Taylor:
I was just there. They said I wasn’t a priority.
Jill Taylor:
Why, because there was a guy with a whole table stuck to his head?
(Home Improvements)
I’m always curious to know how the epoxy coating holds up in the long run. I suspect yellowing over time.
Looks cool.
Crazy amount of work, rather wasteful with all the lost kerf and 45 deg off cuts.
I question the strength of it being loading across the end grain in this orientation. Soaking in the epoxy will help with that a bit.
Probably fine for a desk.
Seems like backing it with a sheet of plywood might have been a safer bet, even 1/4in glued would prevent splitting I would think. But the effect is nice-looking.
Spyder makes extra thin blades to reduce kerf loss. I am not sure who makes them but I have seen blades even thinner than the Spyder used by guys who make canoes out of 1/2 to 1 inch thick hardwood strips, steam bent and glued. I agree that anything like this is a lot of work but the results are beautiful. I have made small tables out of hardwood block cutoffs that would have been scrap. I glued 1/8th steel sheet to the back of them because I was not sure about how the different expansion rates of the woods I used.. I probably would not have went to the trouble if I was going to keep them, but they were going to a marketing company for the CEO’s waiting room.
He should’ve carried through with the theme and made the desktop chevron shaped!
B^)
I counted 21 clamps on that glue up.
It probably could have used twice as many clamps, the angle of the forces of the blue clamps would leave probably a six inch deep section of strips in between the clamps without compression
“Buying the table frame from scratch was much cheaper”. Cheaper only if you don’t account for your labor. This project not only takes a big deal of time. It takes a lot of tools to do too.
Also, can the desk hold heavy stuff? By laying the plywood on the side and glue them back, it defeated the strengthening purpose of plywood. I doubt it could match the toughness of plain plywood used horizontally.
If you enjoy woodwork (in this case), then the value of your labour when doing woodwork is positive, ie spending time making this table is worth more to the maker than going to a store to buy a table.
I had attempted a desktop constructed like this but I ended up not liking the finished result and scrapped it (I tried using some stain and polyeurathane and the result looked grungy). I found when gluing up the panel that structurally it wasn’t as strong as I had expected. Cut into strips and rotated so that the strips are vertical means that the strength depends on the bonding between plywood layers, which in my experience wasn’t strong enough to hold together just manipulating the panel around. I opted for gluing a 1/8 in piece of plywood to the bottom to shore up the strength.
For anyone thinking about the strength of the desk for this application a youtuber named michael alm tested his patterned plywood for strength. The video is only testing the flex of the piece under a jack but its still interesting enough. The long story short is yes, plywood on its own is incredible durable but for most decorative applications you dont need something to undergo that much force.
Every method has its use case and application and some methods are deeply impractical, complicated and lack the strength of the original material but are done purely for aesthetic. I know as engineers we hate aesthetics over function but if everyone was like us, drywall anchors wouldnt be as popular as they are.
i had the same reservations about delamination / warping / strength as everyone else. my kneejerk reaction is to say this is probably a bad project — something that is garbage within weeks of making the youtube video. but more productively, i know what would be a great post! a photo of this desk in situ after a year of use!
in fact, i think retrospective would be a great regular feature at hackaday. i know i’ve got a lot of projects under my belt that i have thrown away uncompleted or — worse — completed and unused. but i’ve also got a few that last years. i guess i’m actually kind of sad that (for example) my 3d printed pla turns brittle and broken after 1-7 years depending on use. but otoh, getting 7 years of use out of some dumb hack is amazing.
i think such a feature might also simply serve to have a corner of hackaday that isn’t all …well, pointless, disposable, not actually useful (let alone durable). i, for one, do not enjoy seeing all the different kinds of plastic boxes people put around their raspberry pi, pronounced “cyberdeck”. show me one that’s left the house, been used, had the hinges and screen replaced from interactions with gravity and children. show me the one that’s being thrown out after 5 years of faithful service, as you are designing 2.0.
I’d be careful applying a personal concept of value when evaluating others projects. Those cyber decks were made for the joy of experimentation, learning, self extension and to show to a community which enjoys their creation.
Why should 5 years of service be a goal? Why must version 2 only start once the first is worn out? What’s the fun or value of that lock-in?
Heirloom tools are great, but creativity doesn’t need justification. It’s valuable all on its own.
i’m not questioning the value of the project to the creator! and, in fact, in this case i can clearly see the value to the creator: they’re building a brand, presumably monetizing it somehow. there’s nothing wrong with that.
i’m questioning the value of the project to the audience. there are many audiences out there. i’m suggesting that there is at least one audience (me) who would get a lot more out of projects that have withstood (or withfallen!) actual usage.
i didn’t say that hackaday should get rid of the clickbait projects with ridiculous engineering choices and no obvious use case. i said it would be awesome if they had one regular feature that was explicitly not those projects.
I’ve used what could be called cyberdecks by your definition for ages, and other than a touchscreen failure that renders the one put into a HDD caddy kinda hard to use they are all still fine now, and most of them do get used at least weekly. Heck that caddyPi and its decent sound card still get used to play music in the kitchen – ssh in for control as I’ve not bothered looking into the failed screen – turns out its so much easier to select music/video from a ‘real’ computer so the touch interface was barely used. And got a Pi stuffed inside a Bose speaker that let out the magic smoke, it is either my first or second pi, one of the ones before the memory bump on the revision 1 model B with a wolfson audio card and a rather simple DC-DC converter knocked up on stripboard, since its been built that thing has been my workshop ‘radio’ and gone all over the place. Admittedly the loose pouch battery I’ve been using with it (when roaming) is just hanging around loose plugged into the xt-60 (from memory) connector in the back, so it isn’t what you would call great engineering, but it still works and lets you use those rather knacked/puffy RC battery pouches for something…
Also needing replacement parts after coming to harm in the real world isn’t a sign of flawed shoddy workmanship, as that can and will happen to the grand of premium electronics too, and equally not everyone is careless/unfortunate enough to break something despite decades of use, so having required repairs there is also kinda pointless metric, especially if your initial object was built like a tank – the fully rugged laptops like a Toughbook for instance, those things are really really hard to even cause bad cosmetic damage to and can take a drop onto concrete while running no problem…
I also have printed parts that have now been in use at least 8 odd years and are as good now as there were fresh off the printer – pick the right plastics for the environment its going to serve in and it will last… That is kinda the selling point and major problem to plastics. Also the reason almost all my prints are ABS (durable and good for almost any environment you might care to put it in and easy to solvent bond parts together or to other existing objects as ABS is do damn common)
In the case of this desk if they used any of the really decent glues for woods it should be fine. Most of the good woodglues are vastly stronger than the woods themselves, and even the most basic white glue isn’t bad from Matthias Wandel’s testing. So this desk is probably very very much stronger than it needs to be, looks like the legs might well add some real stiffening, and ultimately the way it will fail if you ever manage to break it can just be glued back together again, its going to key into itself well…
Hear hear!