Home shop machinists know dust shields are important for keeping swarf out of expensive linear rails and ball screws. [Petteri Aimonen] demonstrates three inexpensive ways to DIY some bellows-style dust covers. Such things can of course be purchased, but they’re priced at a premium and not always available in the size one needs.
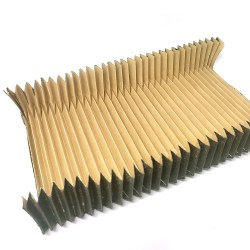
The first method is to fold a suitable flat plastic or paper sheet into a bellows pattern. This method is all about the fold pattern, and thankfully, there’s no need to reinvent the wheel. [Petteri] used a fellow enthusiast’s bellows folding pattern generator which is, believe it or not, itself inspired by a remarkably comprehensive US Patent Number 6,054,194.
The downside to this method is the thickness of the bellows when it is fully collapsed. The corners always contain the most material, because it is there that the material is folded upon itself, and this limits how close to the end of travel the CNC carriage can move with the bellows attached.
The second method is to cut a large number of C-shaped sections from fabric and sew them together to make bellows. This method collapses down well and holds its shape well, but the cutting and sewing it requires can be a barrier.
The final method — and the one [Petteri] found most useful — was to hack some IKEA window blinds. IKEA Schottis pleated blinds are inexpensive, with a slick finish on one side and polyester fabric. The polyester is perfect for gluing. By cutting the material at a 45-degree angle into three sections and gluing them into a U-shape, one can create a serviceable bellows-style cover for a minimum of work.
Any of the explored methods can do the job, but [Petteri] has formulas to determine the maximum extensions and folded thicknesses of each method just in case one would like to see for themselves before choosing. And if a bellows-style cover isn’t your cup of tea, check out this method for turning a plastic strip into a spring-like tube that does the same job.
Here in the netherlands you can buy rolls of a polyethylene and cardboard mixture also used for milk cartons at the hardware shop. Sold as covering for floors during plastering and painting. It is very durable, water resistant and once an bent has been made, stays flexible on that bent. And it can be glued with heat, melting the plastics together. I’ve tried to make a huge camera belows out of it, but it turned out to not being complete light tight. :( Mechanically it is very good though.
For cnc use, where you are actually trying to shield from metal chips- the windowblind thing wont work. They will melt from hot chips.
To make my own custom bellows covers for a Taig mill, that would stand up to hot chips and even coolant, I made them using the first method out of denim fabric from a craft store, used a hot iron to crease them against a sheet metal pattern to keep the pleats very sharp and uniform.
I used marine epoxy and metal tabs to glue the ends of the accordian bellows to those forms at the end, after sealing them with several coats of marine spar varnish. My research led me to believe that compound would stand up to the chemicals in coolant better than anything else for the purpose.
In the end I ended up getting something folded after each coat, I think I did three coats and it stays pretty stiff, but almost a decade later they still work. The Spar varnish soaked into the Denim and gave it a lot more resiliency and it stands up to hot and abrasive metal chips perfectly. I never ended up running flood coolant, but the occasional use of cutting fluids wipes right off them.
I joined the bellows to the machine casting with a bead of Shapelock thermoplastic, into a groove I cut using a Dremel tool into the aluminum way saddle, to both key them in place and seal them from fluid.
The denim has really held up even with tons of fine and medium tool steel chips on top, they look basically new. I highly recommend this method for homebrew covers on manual machines, denim impregnated with marine spar varnish works well from what Ive seen. And because it’s a cloth you can actually iron it to a very sharp pleat. Just do that before you varnish it!
Remember there are also telescopic spring steel leadscrew and ballscrew covers too, for much lower profile protection.
Hot chips melting stuff? Have you tried turning your coolant on?
I agree that the polyester shields wouldn’t be best for installation where the chips fall – it’s not that rare to machine without coolant. I use some rubber coated fabric from old roller blinds for that, it even claims to be anti-flammable.
The polyester shields in my build are far enough upwards from the spindle that hot chips don’t end up there, it’s more about wood dust for those.
You clearly couldn’t be bothered to read past the first sentence. So I’m not sure why you would even read this one but I’ll make this more clear. Perhaps you were being sarcastic.
It was for a desktop mill, not a full size mill in its own enclosure. Have you ever added flood coolant to a desktop mill? Do you understand the logistics of doing that? To do so the mill would have to have an enclosure placed around it with a drain and a sump to pick up the coolant.
My main point was if you are machining metal and not wood, you do not need coolant in all cases with small material removal especially. Even on the job in full size machines there are times where you do not machine with coolant.
Coolant is helpful for cooling chips mainly when they are larger, otherwise the main benefit is tool longevity, where it preserves the integrity of the cutting edges longer by providing aide to the cutting action on the material. Coolant is not a necessity to machine in all materials and types of cuts. It often helps, but there are cases where it isnt used intentionally even.
Metal chips are often sharp and abrasive, and can wear some material covers through with time. In my case, denim has been fairly abrasion resistant against metal chips, easy to form for tight bellows, and with the additional marine spar varnish, should be capable of handling normal coolants if I ever build an enclosure around the thing and add flood coolant.
I have used plastic poster tube bags in the past for simple dust protection. Not as resilient as some of the methods above, but certainly cheap and simple.
Only pain is you need to have access to the end of the shafts/rails to be able to slide them on.
Great article! I went through a similar journey trying to solve dust problems on my Indymill CNC. Initially tried the telescopic covers suggested by the initiator of the Indymilll project, but after months of frustration with poor implementation, I ended up developing my own approach.
The IKEA Schottis hack is clever! Though I found that for precision desktop CNCs like Indymill/Cindymill, you need something that can handle the specific mounting challenges and travel distances. The fabric approach works well but I needed better durability for metal machining.
After extensive testing, I developed a system that combines flexible covers with 3D-printed mounting brackets and conical ring attachment systems. The key was solving the mounting problem – getting secure attachment without interfering with end stops or reducing travel.
The difference is remarkable – not just for cleanliness but for maintaining precision over time. MDF dust in particular is nasty stuff that gets into everything.
For anyone working with Indymill/Cindymill specifically, I documented my whole development process including all the failed attempts and what finally worked. Sometimes the commercial solutions just don’t fit desktop CNC constraints properly.
Thanks for sharing these methods – always good to see different approaches to the same fundamental problem!