[joekutz] made an impulse purchase of a CNC machine. It was a 3040 CNC that looked reasonably complete and had an attractive price, what could possibly go wrong? As it happens, [joekutz] really didn’t know what he was in for. Sometimes the price is good, but you pay in other ways. But where some would see defeat, [joekutz] sees an opportunity to document the restoration.
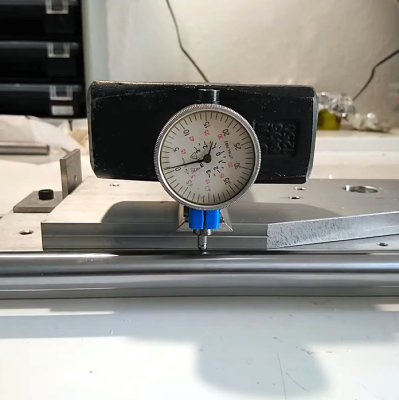
The 3040 are relatively cheap and simple CNC machines that have been available from a variety of overseas retailers for years. They have 30 cm by 40 cm beds (hence the name) and while there are many variations, they all work about the same. [joekutz] expected that getting his up and running and converted to open source would be a fun weekend project, but it ended up taking far longer than that. In fact, it turns out that the machine was damaged in surprising and unexpected ways.
[joekutz] has a series of videos demonstrating the process of diagnosing and repairing the various things wrong with this device. In the first video, he dismantles the machine and discusses the next steps. In the second video, he takes some time to repair some dial indicators that will be critical for measuring the various things wrong with the CNC parts. Video number three delves into finding out the horrible things wrong with the machine, and the fourth is where repairs begin, including bending shafts and sanding blocks back into service.
Those videos are embedded below, and while the machine isn’t quite restored yet, progress is promising. We’ve seen easy and effective upgrades for such CNC machines before, but if you happen to be in more of a repair and restore situation, give [joekutz]’s work a look because it might just save you some time and frustration.
I had one of those, designed a usb grbl to parallel converter for it and the upgrade to a 6040. Same design just bigger
3020, 3040 and 6040 CNC mills are the same design. And there are many brands made in one OEM factory…
GRBL is nice, I had it with 3018 mill, which was made of aluminum extrusions. The only issue was PC side software, bCNC. It convinced me that one should never use Python for anything serious or advanced. Just compare it with Mach3, which is much more advanced but can run on 25 years old hardware.
You should probably ask for a refund on bCNC if you don’t like it. Personally I think it’s great, and an excellent match for grbl.
Mach3 on the other hand is an entirely different beast. Either you are being disingenuous, comparing it with grbl, or you don’t know what you are talking about. The reason it runs on 25 year old hardware is because it needs the antiquated obsolete LPT port to work. And you have to pay for it.
By all means compare like with like, but don’t try to compare two things that are quite different.
No! they are definitely not all the same design. Every Chinese chopshop throws together some parts to bake their own variant. And though the cheapest variants often resemble each other, there are also a bunch of quite different and better designs.
And often you sort of get what you pay for. For example there are anodized blue variants, which cost around EUR1200 and these have much better square linear rails, although they are still a clear compromise on quality to keep the price down. For example they use only one bearing block for each rails, and even among these blue versions I see differences in the way they are built on the photographs.
Fully Agreed! Mine is definitely on the low end of that spectrum: Too thin round shafts (deflection measurements in video no. 4 :) ) instead of linear square rails, nylon nuts instead of ball screws, under-designed metal frame. And a spindle of unknown power.
One would think after this much work, you’d just go splurge the extra money on a better CNC.
But one good thing about these videos – besides the excellent repair knowledge – is now I don’t have to buy a 3040 to know they’re crap.
Sometimes “splurge” is not an option. Also, what you consider to be “crap” may very well be someone else’s chance-of-a-lifetime splurge.
Most people are just using the machine wrong, it’s just an engraver and they are using it to CUT different kinds of materials.
I know the sellers call it engraver, I guess to reduce expectations of buyers. The construction is indeed not made to cut let’s say aluminium (I will try later, regardless), but cutting wood, plastic and FR4 etc. will work fine.
As someone else said there are lots of manufacturers. I have a 11 year old one and its brilliant. Some have basic leadscrews like this one, mine has ballscrews etc. I have a few different cnc machines and my 3020 is very reliable.
I have 3020 with USB controller board. I managed to burn out the 300W spindle motor. Then I replaced all the wiring with thicker one with shielding. I have to repair wiring again, because my kids, Ada and Tavi, managed to break it…
One of the mods I did was a probe connector for my (failed) attempts to autolevel for PCB cutting. I gave up on that pretty early and now I order my boards from China. Still, metal engraving would be fun…
“I managed to burn out the 300W spindle motor. ” – I actually saw comments like that a lot reading around. I am not trusting my motor very far. It is less than 300W (may be 150?) and I wonder anyway how well it performs. You can find out in (uuh..) a year in video 20ish :)
For around EUR125 you can buy a BLDC spindle motor with controller. And as with the CNC machines themselves, there are variants here too. With the ER11 variants, the collet often is one piece with the motor shaft, and thus relatively stiff. With the ER16 variants, the motor shaft is quite thin, and an ER16 collet holder is clamped on the motorshaft. Because of the thin section of the motorshaft and the coupling this is not optimal, but bearings that would fit over the ER16 collet holder would be quite big, and big high speed bearings are expensive, which would reflect in the price of these motors.
I have not used (nor hold in my hands) such a motor (yet) but my best guess is it would be a nice (and not over the top) upgrade for a CNC engraver like this. Especially when your brushed DC motor dies or is worn out, I would put on a BLDC and not replace it with another brushed motor.
The 3040 and its smaller sibling, the 3018, are built to a price point, a very cheap price point. I like to call it Shelfware. The typical buyer is looking to learn about CNC. There are two very common results of this. A) the buyer runs into all sorts of problems, gets zero support from the seller, becomes frustrated/disillusioned and it winds up unused. B) the buyer learns enough to realize they need a better/bigger machine, upgrades and the 3040 winds up unused. In either case, the machine winds up on a shelf, unused. As a learning experience a key part of what gets learned is how to deal with a CNC router that has a lot of flex and a tiny working footprint.
The upgrade path is a complete waste of money. Better to sell it and buy a better machine.
For learning CNC, I recommend people find a local makerspace that has a CNC machine and get some hands on time.
My 3020 has a sturdy metal frame. 3018 and smaller machines use aluminum extrusions, like 3D printers. These are not rigit enough to be both fast and accurate. It’s a trade-off. Mills made of extrusions and 3D printed parts work well at low feedrates. Machines like 3020, 3040 and 6040 with frames made of metal plates, work well at moderate speeds, especially with bigger spindles. But if you want industry-standard performance, you need industry-standard machine.
I got a 3018, which I managed to set up fairly easily. The GRBL firmware was fine, and the CD presumably containing a cracked Corel draw or similar went straight into the bin, to be replaced by CNCjs, initially running on my laptop and then on a pi.
It quickly paid for itself, for the job I’d bought it for (engraving names in wooden USB sticks)
I then had a play at upgrading it – was quick and easy to add limit switches and a fan to remove dust. truing it to a higher degree was more fun… the parts were all true enough except for the bed which had a bit of a curve – not a major issue as I fitted a waste board which was flat – but it lacked any screws to make fine adjustments, so I had to rig something up.
The bits which come with it were utter junk though, could barely cut balsa. I got a used carbide bit from a friend who works for a precision engineering firm, and accidentally cut through a steel hold-down bolt with a misplaced rapid move. Eek.
All in all, very capable. Yes, there’s better machines available, but only at significantly more cost. And I believe a lot of them still need work.
Skeptical.
Did you check the bolt with a magnet?
Carbide + rapid typically results in broken carbide.
I think you had an aluminum fastener, maybe ‘pot metal’. Even then, it’s impressive the carbide didn’t shatter.
Yup, was a steel bolt – something like an M8. Wasn’t a very deep pass but took a clean cut through the head of the bolt.
Don’t forget that the rapid speed on a 3018 is well below the working speed on the mill the carbide bit was made for. Also I suspect the bit when new cost more than my entire 3018 CNC… I got it because it was used and so probably not within tolerance.
Good carbide is pretty tough stuff, you obviously can and will break it eventually with abuse but good carbide tooling will take so much more than you expect without breaking if you only used poopy cheap carbide before.
You could put in the largest face mill it can take then use the mill to skim the bed flat.
I did consider this, but was advised that lapping it would give a better result?
The largest face mill a machine like this can take would be about 5mm.
And after you’ve leveleled the (anodized aluminium! ( or add wasteboard) and you put any work piece on top of it, then it would sag again under the weight of whatever you put on top of it.
These cheap versions are just atrocious in stiffness. If you need a machine for more then cutting though light materials or need accuracy then these cheap machines just don’t cut it anymore, and you’re much better of spending your money on better hardware.
I see what you did there.
I ordered a 1310 pro mini CNC and it was a joke. Linear rails are nice but the thing was so gritty and out of true. It’s really sad because the form factor is so nice! Now I’m getting ready to make one using sendcutsend.
Yeah, save your money for an industry standard CNC machine! Considering most people have the space, the proper voltage supply, constant supply of compressed air, and the means to move such a behemoth from the point of sale into their residence. Oh wait, most people dont, lol
Industry standard CNC machine… Most people would use them wrong as well. The bigger and stronger the machine, the harder they crash! And speaking from experience, having crashed an old Mori Seiki slantbed CNC lathe was an event I never wish to experience ever again. Like a nasty car wreck taking place literally just a couple feet in front of you. The machine more or less self destructed, all 3 jaws were sheared off the hydraulic chuck. The part itself grazed my chin lacerating the skin as it was ejected from the machine. One of the jaws struck me square center of my chest which resulted in a massive contusion which took a good month to heal. A word of advice, never run a CNC with the safety locks overridden! The entire event lasted maybe 3 seconds, and then pure silence. All eyes were on me as I stood there in absolute shock, the pain in my chest hadnt even registered yet! An estimated $70K to repair the machine was more than it was worth. It was sent for scrap. It can happen quite easily if you do not double check everything before pressing that big green button. Something to think about for casual makers who wish they had an bigboy cnc machine.
is there any OSS for semi-intuitive 3d carving? seems all the easy ones are subscription.
Kiri Moto worked pretty good for me a few times – http://grid.space
Wow, thanks for the link. I have been looking for something with easy STL->CNC path for years now.
For 2D stuff, my favourites are KrabzCAM and OpenBuilds CAM. For 3D stuff, I have used FreeCAD and Blender CAM, but neither of those is easy nor intuitive.
Hmm, does Kiri:Moto actually do any kind of 3D carving? For me it somehow just seems to extract the outline from the STL.
How silly of me, I missed the operation menu at the bottom.
It’s nice to see that I’m not alone in buying random shit just because i have poor impulse control
There’s a 4540 sitting in my basket at your favourite Chinese shopping site. One day I will push the button to buy…
What works for me is whenever I feel the urge for an impulse buy, I make a note of what it is (It can be a photograph in a brick & mortar shop or a screenshot on my PC) and this enables me to let it rest for a while. If I still consider it worth buying a few days or a week later, then I go back and do just that, but most often those photographs end up in some dusty corner of my past life.
My business partner and I got a 6040 years ago to do a job involving engraving control panels.
We call it “the problem child” to this day, it has had so many problems and upgrade projects over the years.
It works fine in general now, but it was a long hard path (new controller, new spindle motor, mods to add probing and limit switches, SO MANY additions of shielding to cables and electronics to keep out the EMF elves…)
Can you give us an estimate on the time you spent holding hands and babysitting that thing?
I guess that if you bought something decent at the start, it would have paid back the price difference several times over.
The cheap chinese machines can be an “enabler” to get things done that would not be possible without such a machine, but I guess they are only “cheap” if you do not value your time and see it as a hobby to have something to play with and learn from.
If I would have bought the machine as shop workhorse then my answer would be “too many hours”.
But I bought it without many thoughts as hacking project, so fixing it is my hobby. The journey is the goal, so to speak. And filming and storytelling of course. (Without filming I would probably be done with everything, but that is true for any project on YT :) )
> We call it “the problem child” to this day
@Bryce, we had exactly the same problem (metal control panels for a machine we sell) a couple of years ago. The local CNC shop was charging us a fortune to make control panels out of aluminium. We looked into a home CNC but decided we didn’t have the space to put it or the time to babysit it. We eventually made some mods to our machine so that it could use a control panel made of PCB. PCBs can be cut, routed, printed and have lots of shiny metal accents if you need them. Line art is as easy as dropping a vector graphic into Kicad. Each control panel only costs us a couple of dollars, even in small quantities and a revised panel is a quick order from your favourite fab house.
I hope you found a solution that works for you, but I really feel the need to spread the “PCB control panel” word because it has saved us (low-volume custom electronics) a pile of time and money since 2020.
Lol cheap easy CNC is such an oxymoron. Good luck.
cheap easy cnc … pick 2 lol
Is “easy CNC” even a valid choice? Maybe if that consists only of “send it to a pro”.
I have been mostly happy with my CNC3020 (owned for 10 years now). The one part I’m least happy with is the spindle motor, I’ve been meaning to upgrade that for quite some time.
That said, after finishing a bigger and better custom-built CNC for our hackerspace, the difference in usability is huge. Even just having enough working space for clamping without it getting into way makes a big difference. Also LinuxCNC gives much more immediate controllability vs. grbl/smoothie-style stuff.
I understand I just purchased the Yorahome Silverback 1M X 1M. That’s a1M X 1M cutting area – and I haven’t used one before.
Now for the cliff of a learning curve
Everyone seems to be blaming the manufacturer for producing cheap junk, however, OP bought this unit second hand. We have no idea if the elements that needed repair were supplied that way, or damaged by the previous owner. I suspect the latter, which then led to the sale.
Yea, that info got a bit lost in all the text and comments :)
I have never impulse-ordered a new item online, but that thing was offered on what is like craigslist here literally a 5 minute drive away and for cheap. As described in video 1, I didn’t have much info about it, and the previous owner just mentioned how hard it was to put it together. Now I know, why.
And I don’t regret it. I think at the end I will have capable machine. And the awesome HaD community a dozen or so videos to watch.
It’s all fixable and you’ll learn something in the doing. No machine, even new ones, come to your door truly “working”. There is always something wrong, something that needs adjustment and calibration, or something that is not configured the way you thought it was. It’s practically a physical law of the Universe.