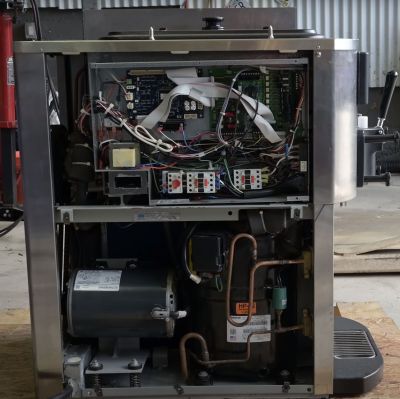
Raising a likely somewhat contentious topic, iFixit and Public Knowledge have challenged the manufacturer behind McDonald’s ice cream machines to make them easy to diagnose and repair. This is a subject that’s probably familiar to anyone who is vaguely familiar with US news and the importance of ice cream at McDonald’s locations to the point that a live tracker was set up so that furtive customers can catch a glimpse at said tracker before finding themselves staring in dismay at an ‘Out of Order’ sign on one of these Taylor ice cream machines.
The story is more complex than just a machine being “broken”, however. The maintenance contracts are lucrative, the instruction manual is long, and the error codes are cryptic. When you add to that the complexity of cleaning and maintaining the machines, it’s tempting to just claim the machine is out of order. These Taylor machines (the C602 and the C709 from the iFixit video) are a bit more complex than your usual ice cream maker in that they also have a pasteurization element that’s supposed to keep already poured mix safe to use the next day.
During the heating cycle and other functions errors can occur that will trigger error messages on the screen, as detailed in the C602 manual. These manuals are apparently available to the employees at McDonald’s establishments, but according to iFixit and those in the business, many error messages still necessitate a (very expensive) call to a service technician. It should be noted that the Taylor Company has been repeatedly bought by and sold off to other companies since 1967, with the Middleby Corporation being the parent company since 2018.
Perhaps the more puzzling aspect of this whole saga is why it is that consumer-oriented organizations are essentially fighting McDonald’s battles for them, as here only McD customers are deprived of a treat, rather than being the ones who are paying the thousands of dollars in service costs. Where these machines are somewhat interesting is on the used market, which is when hacking them becomes somewhat interesting, and that’s where the DMCA exception that iFixit and Public Knowledge are asking the US Copyright Office for makes sense, as hacking an ice cream maker you own should be your right. Just don’t hack the one at your local McD’s without explicit written permission.
OK Peeps. This site monitors in near-real-time which McDonald’s ice cream machines are broken and where they are located:
https://mcbroken.com/
It has a map. Sample pop-up says:
4492 Weston Rd
Davie
Checked 321 minutes ago
Machine Broken
These days to me it looks like there are a lot less broken machines than there used to be, at least in my area. I dunno why.
Then there is this:
Ice Cream Machine Hackers Sue McDonald’s for $900 Million. Kytch alleges that the Golden Arches crushed its business—and left soft serve customers out in the cold.
https://www.wired.com/story/kytch-ice-cream-machine-hackers-sue-mcdonalds-900-million/
Yeah I know – Wired. Sigh…
Don’t like Wired? Try Hackaday! :)
I added the link to our previous coverage into the article.
https://hackaday.com/2021/08/23/freezing-out-ice-cream-machine-competition/
$900M hacker lawsuit and no following it here on Hackaday? Hmmm.
The Taylor McFlurry machines are crappy ON PURPOSE. Taylor’s repair people make good money off this, 25% of their revenue, as a parasite sucking extra cash out of McDonalds.
That McDonalds flipped allegiance and later sided with Taylor shows there’s some kickbacks at the top happening as well. The FTC seems to have done nothing. It’s the mafia against IoT lol.
The machines commonly bungled their overnight sterilization cycle necessitating a service callout. A safety concern, think of all the McDonald’s customers poisoned by McFlurry. RIP.
Taylor uses antique electronics tech, they are an old dinosaur company. Their user interface is hilarious. Not about electronics at all, and obviously not about quality at all, just pure profit.
They’ll lose that lawsuit with any sane justice.
I read some things about this icecream / McDondalds thing a few years ago, but most wat on youtube / entertainment level as there are a few thousands of km of salty water between me and there, and I tend to believe this.
Also, I find it a bit worrying you have to mention that they have to go find a sane judge to get some righteousness done. How many sane judges are there still left in that part of the world?
“How many sane judges are there still left in that part of the world.”
It is really difficult to determine.
(Sigh!)
Eh I don’t know about all this. This seems like something the internet made up or added heavy hyperbole. Does Taylor make all the other perpetually-broken frozen treat machines at all the other restaurants on earth? Not to mention certain other factors..
Kytch is mentioned a number of times in the video.
Want more badness in soft serve ice cream machines? It was common for the switches for stirring the mix and enabling the freezing system to be on completely separate circuits, with nothing but the human flipping the switches to prevent the disaster of freezing the ice cream solid *then* turning on the stirrer.
Why? Why would any company manufacture and sell such a disaster in waiting? It’s a dead simple wiring arrangement between the two switches to allow for stirring with or without freezing yet impossible to turn on freezing without forcing stirring to be on regardless of the stir switch position.
An example of that design fail in action was on the 1st season of TLC’s “Town Haul”. During clearing out of the ice cream shop before its makeover, the host of the show for some reason decided to take on the job of emptying the ice cream freezer – without asking how it worked. She flipped on the freeze switch then futzed around for a while, not able to get it to dispense. IIRC she went off to attend to something else then came back and flipped on the stir switch. That did major damage to the machine so TLC was on the hook to replace it. It cost the company an additional $3,000 to buy a good used machine.
No obvious switches on that machine, but it’s got a magnetic clutch on the stirrer why would that be a problem?
Ah I see, a different machine? Well of course there’s poor design in lots of places. But the key point there, to me, is why is a dumb-ass working with industrial machinery that doesn’t know how to use it? Sure there’s some simple things that can prevent disaster, but similarly you shouldn’t faff with stuff you don’t know how to use. The world is full of people who just don’t think before acting – do we have to mitigate a million dumb people? Why do we pander to the lowest common denominator?
Sometimes there are conventions that people become familiar with. If a manufacturer of cars started putting the accelerator in the middle and the brake on the right in some of their cars, when the inevitable accidents happen would it be justifiable to blame the users and call them dumb?
Min wage employees, that’s why. The alternative is high-skilled workers and more expensive milkshakes.
Cleaning is “high-skilled”? Your abodes must be a wonder to see then.
Why is a machine being designed to be needlessly easy to fuck up a lesser sin than a minimum wage fast food employee at the end of their second shift forgetting a step?
Humans make mistakes. It doesn’t matter how smart they are. Tools should be designed, where practical, to minimize the possibility, and minimize consequences if they occur.
Also, your fundamental attribution bias is showing.
meh it’s a tricky one. IF you price your product so that service costs are an ongoing revenue stream, it’s not fair that someone hacks it and destroys your revenue stream after the fact. I sold you an icecream maker for half the normal cost, so that when it does break I am the only one who can repair it and that means that I’ll eventually get back my investment. The real problem here is that McD’s will have enforced the use of that machine, and the franchisees are relying on McD’s to specify machines that are good. So here the issue is that McDs picked a bad option and it’s forced on francisees, none of that has anything to do with Taylor who are just making machines and selling repair services. I’m always torn on the RTR – as a customer who repairs things, I want it, though I’d accept it voids my warranties etc. As an engineer designing things, if you faff with hardware I’ve put time and effort into designing – that’s fine, you’re on your own though, and I’m not going to give away my schematics so you can do it more easily – they took time, cash and knowledge to create.
“IF you price your product so that service costs are an ongoing revenue stream, it’s not fair that someone hacks it and destroys your revenue stream after the fact”
I see this as totally fair.
What I see as unfair, is that a big company can throw in millions to “sell” products at under cost price, and in that way always outbid smaller companies who likely have a better product, but can not afford to make products for several years before having a chance to make some profit. There are (or there were at least) laws against these dumping practices, but these laws don’t work very well for the last 20 years or so.
The biggest problem with this practice, is that the mechanism of competitiveness to make a decent quality product for a reasonable price is out the window.
I think the world would be a better place if such things were bluntly forbidden. Split the products and the service contracts into two separate entities, so both need to be competitive independent of each other.
The problem is that the purchaser considered only the initial price not the costs over time. If the purchasers did this the mechanism of competitiveness would result in a better product.
Indeed, this only happens because of incompetent purchasers at McD headquarters. There’s no nefarious kickbacks like people think.
They sent at a request for “Give us a contract for the machine with the lowest purchase price if we force all restaurants to buy it”.
Instead they should have asked for “Give us a contract for a machine including fixed monthly service costs with 95% daily reliability and 5 year warranty on the condition that all restaurants buy it.”
The soft serve machine at my local McDonalds has been broken on several of my visits to get my hot fudge sundae. I was PISSED !
Jim
I use to manage a McDonald’s. I know why these ice cream and shake machines keep failing.
It’s not to line Taylor foods pockets with service call payments. Honestly it’s a pain in the rear to get Taylor to show up. McDonald’s corporate selected these machines for the staff to upkeep and keep repairmen out. However they will send out someone to teach the store on how to upkeep it.
When you get down to it, it’s managements fault. They don’t keep the parts in stock for the monthly cleaning. They don’t keep on the crew to keep the machine properly filled with mix. They delegate the cleaning from one manager to another. The machine gets over filled and the machine requires six or eight hours of the “heat mode” cycle if I remember correctly.
The system goes into heat mode every 16 hours and if the system has too much mix or not enough mix then the machine has to be torn down and cleaned. When the machine is in heat mode they just tell the customers it’s down, broken or out of order. The timer for heat mode can’t be set manually and only does it automatically when the system comes back online when the system is cleaned.
replacement parts take a week or two to come in so if you’re not on top of it you’re gonna get complaints.
Most stores are ran by skeleton crews and most owner/operators don’t want some one working on the machine during the peek rush times.
Other fast food chains use the same machine but they tear it down every night.
Tearing it down every night is the normal order of business for food processing equipment. It sounds like most of the trouble is due to trying to avoid that, with less than total success.
You didn’t pay attention, McDonalds is open 24/7. So they sale ice cream the whole time except for when it’s in heat mode.
So they actually need TWO machines as a form of redundancy to be able to sell “icecream” 24/7, like they do with all their other equipment.
To the point of only helping McDonalds… I think the vast majority of McDonalds stores are franchise, so another person/company owns and runs them. For most franchisee arrangements, they would pay the company (in this case McDonalds) for the right to be a McDonalds. The franchisee is required to use the equipment/processes/foods as defined in the franchisee agreement. It is not the case that in most cases, you are helping the franchisee of McDonalds, when McDonalds themselves seems to be letting their subscribers down? Just a thought.
The relevance of ifixit is in the first sentence:
“iFixit and Public Knowledge have challenged the manufacturer behind McDonald’s ice cream machines to make them easy to diagnose and repair”
there was an article, I though on HaD, about somebody basically jailbreaking one of these machines or getting around the DRM. I’m grasping to remember details but when the machine breaks, you need to have a licensed technician ($$$) or something fix it- you can’t just pop the cover and fix whatever broke because half the time nothing is broken, its an electronics/software issue that was tripped. Like, it is a software thing with PIN numbers or other electronic lockouts. Sounds similar to the whole John Deere thing (well covered on HaD too; thx for that).
Anyway, the guy jailbreaking these got cease and desist from McDo and let all the franchise owners that if they jailbreak their machines, they will have their franchise license yanked. So yeah, I agree with someone above that behavior smacks of payola or corruption at McDo headquarters, likely kick-backs from the machine mfgr or something and should be looked into.
I’m certainly mis-remembering a lot of this but I think that is the long and short of it.
I remember something along that line too, but I don’t know whether it was the same or a different thing. I think it was about a gadget that send a text message if the thing stopped during a “cleaning cycle” during the night (or otherwise unattended) and it translated numbered error messages to something a human can understand.
https://hackaday.com/2021/08/23/freezing-out-ice-cream-machine-competition/ ?
Do you want the average macdombles employee sticking their colorful extended nails into the guts of one of these machines and messing up the sterilization cycle? Do you really want them to try and fix something like that
Missing the point. There are a couple local ice cream places here where… exactly that. Behind a big glass window you see all the pimply teenagers manning the big industrial ice cream maker all by themselves. By themselves!! It can’t be that hard honestly and with like a day of training yeah. I fully expect a teenager of even modest intelligence to be able to do it. Even on an sanitization-intensive piece of equipment.
In 20 years I have NEVER seen a broken ice cream machine in Japan. I highly doubt this is a hardware problem as much as it’s a “staff too lazy to upkeep correctly”.
Or the boss won’t let an employee take time from serving customers to do maintenance, too cheap to pay overtime for someone to stay after shift, or too incompetent to keep track of what needs to be done when beyond the every day routine.
It’s wild how the response is always “the workers are too lazy.”
“Boss” is part of “staff” much like “stockholder” is part of citizen. It’s not like evolution gave us “boss” and …everyone else.
I suspect the reason they’re so intense about taking them offline has to do with avoiding headlines like these:
https://www.npr.org/2023/08/22/1195207118/listeria-frugals-milkshakes-tacoma-three-dead
… however I also suspect it’s more about ass covering than safety strictly speaking. I often get the sense that if we lived in a less litigious society fewer things would be locked down due to liability concerns.
I found the article. It was in Wired. Basically the machines are DRM secured and have secret menus and stuff.
https://www.wired.com/story/they-hacked-mcdonalds-ice-cream-makers-started-cold-war/
Also. An ice cream machine needs to be a big auger on a motor with a chill jacket- at least that is what it is at every indy ice cream parlor I’ve ever been to. There doesn’t need to be some crazy microcontrollers and stuff. There are numerous examples like the slurpee machines at 7/11, heck even the ones at gas stations that don’t constantly have issues. The machines are either poorly engineered (generous interpretation) in that they weren’t designed for routine, industry-standard daily tear down/clean/sanitize cycle (every grocery store cleans the meat department top to bottom every night, and so does every restaurant and starbucks and … on and on) or (likely) intentionally made to have secret menus, DRM, and payola for authorized repairs- same story for the BS John Deere parts that have no right to be unrepairable.
https://www.wired.com/story/they-hacked-mcdonalds-ice-cream-makers-started-cold-war/
McDonalds soft serve != Ice cream.
Think about it:
The machine heats itself up to pasteurizing temp once a day and hence never needs to be taken apart and cleaned. _Never_. Until someone screws up and they have to clean it, petty tyrant throws tantrum etc. Average BurgerWorld worker (Beavis or Butthead)…have someone responsible check their work and enter a code.
Just barfed in my mouth a little.
I see no reason to even patronize a McDonalds.
No, they DO need to be cleaned. In fact, if they don’t get taken down for a cleaning cycle (in which all of the user serviceable parts are removed, scrubbed down, lubed back up, and put back together – preferably with new o rings) once every two weeks – the machine will hard lock UNTIL it’s taken down. The whole process takes about three hours to do right; less time if one person scubs the machine while someone else washes the parts, or if you half ass it. Then when it’s back up it takes about an hour for the mix to thicken up enough yo be served. And during all of that time, anyone trying to order a shake or ice dream will probably be told, “Da machine broke.” Meanwhile the manager trying to clean it is probably thinking, “Go… it’s not freaking broken!”
I was a manager at a McDonald’s for eighteen years, and had to clean one of those accursed machines every two weeks. Like clockwork. Like – I was required to plan my vacations around when the machine would have to come down. I had to come in on Christmas (when the store was closed) to clean it. And I could never train anyone else because the owner didn’t want to pay two people to not be serving customers.
Fun Fact – Senator Joe Biden voted to pass the Bill to DISALLOW self-repair in the 1990s.
A simple check at the Library of Congress web site validates my assertion.
Industry Lobbyists greased his palms with a ton of CASH in exchange for his vote.
It was Business as Usual for Joe Biden.
And this will remain the case until people start realizing they can vote for someone other than the crap the two main parties constantly push on us.
Until then, it’s business as usual, with voters dutifully marching to the polls to vote for Bad vs Worse (which one is which depends where on the political spectrum you fall on).
Nope.
The whole election thing and the years long path to it is so utterly broken there not a chance that some decent person gets elected. so you’ve got a choice between a clown and and old fart and that’s about it.
A very interesting youtube video covering this item here: https://www.youtube.com/watch?v=SrDEtSlqJC4
Don’t other companies make ice cream machines? Lots of clever folks on here, maybe design a new one?
McDonalds corporate won’t be done until all the franchisees tell them to f-off and open their own burger joints producing a superior product. Which won’t be hard.
The Franchisees are just a bunch of narrow thinkers currently trapped.
These ‘ice cream’ machines are just one piece of financial sodomy perpetrated by McDonalds’ suits. There is much more.
How much do you think they pay for an order of _terrible_ frozen onion rings? Do you realize how cheap, easy and profitable good rings are.
Fun fact – McDonald’s also has a proprietary soda system that’s just as archaic, if not more so, than the ice cream machines. They’re maintained by techs from Coca-Cola. And while other fast food places (like BK and Wendy’s) have shifted to the Coke Freestyle machines, McDonald’s has refused. Why? Because they want their own machines that only they have. Coke even designed a special version of the Freestyle machine solely for use by McDonald’s (because it’s a more modern design that’s easier for the techs AND the store staff to use and maintain). But corporate said no, because it’s still basically the same machine as what those “inferior” chains use.
What the law says about the legality of repairing these machines without going through the manufacturer doesn’t matter if McDonalds puts terms in the franchise agreement that makes it a violation of said agreement to get the equipment fixed without going through the manufacturer.