There are those among us who might bristle at something from the early 1980s qualifying for “Retrotechtacular” coverage, but it’s been more than 40 years since the California Department of Transportation’s truck-mounted attenuators crash testing efforts, so we guess it is what it is.
If you’re worried that you have no idea what a “truck-mounted attenuator” might be, relax — you’ve probably seen these devices attached to the backs of trucks in highway work zones. They generally look like large boxes attached to frames at the rear of the truck which are intended to soften the blow should a car somehow not see the giant orange truck covered with flashing lights and drive into the rear of it at highway speeds. Truck-mounted attenuators are common today, but back in 1982 when this film was produced, the idea was still novel enough to justify crash-testing potential designs.
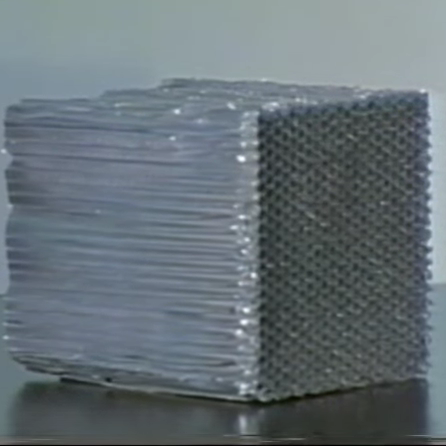
And, boy, did Caltrans crash test! By our count, 18 cars of various makes and models were harmed in the making of this film, along with one very abused dump truck. The tests start with a couple of control crashes into the truck sans attenuator, just to get the lay of the land. The results are predictably horrific, especially for cars from the 1970s. Along for the ride was the delightfully named “Willie Makeit,” a crash test dummy who may or may not be distantly related to the somewhat more famous “Buster.”
It appears that rather than buying commercial units, Caltrans was testing its own designs for attenuators, all of which were based on honeycomb aluminum called Hexcell. They state that the aluminum in this material is only “7/10,000-ths of an inch” thick — just for scale, that’s about the thickness of standard aluminum foil from the kitchen, and not even the heavy-duty stuff.
Even so, the attenuators performed admirably. They tried a couple of designs, with the best being an arrangement of increasingly larger blocks of Hexcell, to sort of ease the incoming car into the main attenuation block. They spared no expense, either, testing every design against both large cars and smaller models. They must have gotten a good deal on 1972 Matadors for the large car category; incidentally, did anyone ever tell the geniuses at AMC’s marketing department that “Killer” isn’t a great name for a car?
Although Caltrans obviously put a lot of effort and taxpayer money into these crash tests, the whole thing has a very DIY feel to it. No fancy test crash lab was used, just a big open stretch of asphalt and a wire-guided mechanism to launch the cars. Their method for measuring the velocity of impact for unrestrained objects on the interior of the car was quite homebrew too; a clear plastic container that turns on a light when a sliding weight makes it to the front of the tube. All the successful tests kept the impact velocity below 27 mph (43 km/h), which would be about the same speed you’d be going after diving off a three-story building. Ouch!
Hats off to the folks at Caltrans for doing these tests and pushing back a little on the more brutal aspects of the laws of physics. Speaking from experience, motor vehicle accidents are generally much more survivable than they were back in the 1980s, and we’ve got good engineering like this to thank for a lot of the progress.
Thanks to [JohnU] for the tip.
Well, hey, that foil stuff was used as shock absorbers for the manned lunar landings, so it’s got a good pedigree.
Around here, a lot of the state and county trucks have these, especially those rigged for painting lines and such.
There are a lot of people out there driving cars who somehow manage to stay on the road when nothing unusual is going on, but as soon as they look over at something off the side of the road, they just drive right into it. My wife works in neurology, and most of her patients have head injuries from traffic accidents, and a lot of those are people who had mild crashes and then were hit standing outside their cars parked off the side of the road post-crash, because there are a lot of people who drive where they look. (Don’t stand beside or particularly in front of your car if you get in a wreck: get well away from the car, well off the side of the road.)
Same concept was taught to us for my motorcycle endorsement class.
“Always point your face towards where you want to go.” followed by “Always be scanning ahead for future obstacles.”
Pointing your face is apparently an effective way of making sure you keep going forward despite scanning back and forth across the street and shoulders for potential hazards.
Seems to work too from experience. It’s REALLY easy to just start easing towards where you’re looking but pointing your face seems to negate it.
I was taught that too. My instructor called it “target fixation”. You look at the pothole, think “I must avoid that” and then ride straight into it. Always look at where you want to go, not at what you want to avoid.
Closely related to the novice motorcyclist trying to steer directly instead of countersteering at speed
Good advice to be sure. I literally almost got killed on the freeway today from some idiots rubbernecking at something incident on the OPPOSITE DAMN SIDE of the freeway.
I swear a good 20% of highway accidents are people looking at a bigger accident that’s already happened.
Also the advice about standing away from the car is crucial and so often ignored – trucks wander onto the shoulder often, you need to be a good distance away and “upstream” of your car (ideally leave it with the wheels turned to point to the shoulder too). It amazes me how few people are capable of actually assessing the risks of that situation.
It’s a problem to have an uncommon but cool car.
People will stare at it, trying to figure out WTF it is. Then drive right into it.
Not a huge issue for my land yacht (they were eventually banned from Demolition derby, why they’re so damn rare.). But my kid brother made his bug powered Fiat 600 racetrack only because some idiot was going to kill him.
No wonder parts are hard to find for AMC Matadors!
B^)
I owned a ’74 Matador and I can’t think of a car more worthy to be crushed. GM engine block, Ford carburetor, Chrysler starter and an absolute nightmare to work on. 4500 pounds and I probably pushed that POS close to a half mile overall.
Anybody else surprised that the Ford Pinto didn’t explode into a huge fireball?
B^)
Some do-gooder foiled their best efforts? ;)
Hexcel is a company that makes aluminum honeycomb core, there are others. Traffix Devices still makes this style of truck mounted attenuator, the Scorpion. The first few years of my career as an engineer were spent at a composites company that made 12″ thick crash attenuator modules and other products out of aluminum honeycomb.
The keys to good HC attenuator design are figuring out how the initial collision energy is translated into core crushing, and how to quickly vent the air from the cells when the core begins to collapse. If these aren’t handled effectively, the car will bounce off the attenuator rather than be decelerated.
Precrushing the leading face of the core is the common solution shown, however some designs perforate the foils of a monolithic core block perpendicular to the line of action to encourage localized cell failure. When the perforation axis is biased properly, this has the added benefit of eliminating the ‘bucking’ artifact of a module-based design.
Maybe I could obtain some hex cells to glue to the corners of my daughter’s car?
B^)
You’re happier not seeing her impression bent over the trunk by her BF.
Also a good reminder that if you are blazing new trails, whatever quality you can muster is an improvement over the current state of things (i.e., nonexistent). As the author mentions, good engineering like this got us to the safety improvements we have today. If the Caltrans scientists had waited for better instrumentation instead of going with what they had available, the science wouldn’t have gotten as far as it has.
It’s so annoying when the camera view changes 3 times during a recording of a crash.
What’s orange and sleeps six?
A CalTrans Van.
Why are CalTrans uniform shirts pockets sewn on upside down?
So they can prop, themselves upright with a shovel handle while sleeping.
These attenuators are not to protect drivers. It’s so the union slobs aren’t woken up when there’s a wreck.