As a manufacturer of test equipment and more, Tektronix has long had a need for custom form factors with its CRT displays. They initially went with fully glass CRTs as this was what the booming television industry was also using, but as demand for the glass component of CRTs increased, so did the delays in getting these custom glass components made. This is where Tektronix decided to use its existing expertise with ceramic strips during the pre-PCB era to create ceramic funnels for ceramic CRTs, as described in this 1967 video.
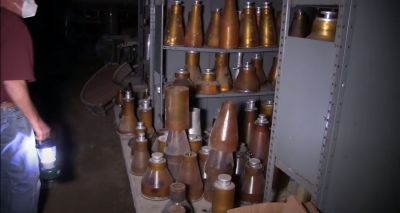
Recently, underneath Building 13 at the Tektronix campus, a ‘catacomb’ full of the molds for these funnels was discovered, covering a wide range of CRT types, including some round ones that were presumably made for military purposes, such as radar installations. These molds consist out of an inner part (the mandrel) made from 7075-T6 aluminium, and an outer cast polyurethane boot. The ceramic (forsterite) powder is then formed under high pressure into the ceramic funnel, which is then fired in a kiln before a full inspection and assembly into a full CRT, including the phosphor-coated glass front section and rear section with the electron guns.
The advantages of ceramic funnels over glass ones are many, including the former being much harder and resilient to impact forces, while offering a lot of strength for thinner, lighter structures, all of which is desirable in (portable) lab equipment. Although LCDs would inevitably take over from CRTs here as well, these ceramic CRTs formed an integral part of Tektronix’s products, with every part of production handled in-house.
I wonder if slip-casting would have been cheaper and more expedient for this?
Given that the parts need to be absolutely gas tight, cold isostatic pressing is probably way superior to slip-casting based on the final porosity, or slip-cast green parts need to be fired a lot longer to achieve the same results.
3D printed ceramics give a good indication how bad it’s going to be, with shrinkages ranging from 5 to 30%. It’s a lot harder to hit anything resembling tolerances with that.
Gee, I’m sure no-one at Tektronix’s vast multi-million dollar specialist CRT casting facility thought of that in the 40+ years it was running.
Slip casting gives poor control of the inner surface, and has a longer cycle time. I suspect the mechanical properties are poorer too, and the material choices. Pressed porcelain was commonplace for lamp holders, ones for high power discharge lamps were quite detailed, so the material technology was available.
Good point. Also fuse holders, insulators, and even chip packages.
In this era of plastics it’s easy to forget that there was a large industry in technical ceramics at that time.
(There still is, but it’s nothing like as big. If you need ceramic nuts and bolts, for example, they list them in the RS catalogue. But you would only use them if nylon wouldn’t do the trick)
Any chance of someone picking these up and doing a run of some of the more commonly in demand CRT’s?
A hacker/restorer can dream…….
I think that the ceramic body would be the easy part. The gun and the screen are where the trouble would be.
For example you could machine the funnel from Macor (or similar machinable ceramic) in the same way that some low-volume X-ray tubes are made.
That’s where we need that hobby friendly lottery winner to finance it.
If Vintage Tek is able to hold onto these parts of the building then the future of these molds will be secure.
They are dedicated to preserving everything Tektronix. If you need manuals, parts, measurements, or insight from the actual designers, they are the source.
Some of these might also make it into RAMS (Recycling and Material Salvage), which is in the same building as VintageTek. RAMS opens to the public on the first and third Thursday of every month.
I’m curious how well these functioned as CRT tubes. Now obviously they worked quite well, but in my minds eye ceramic is a porous substance that I can’t see holding a vacuum. I assume these we’re more like porcelain in terms of ceramics. Honestly I can’t get the image of an orange planters pot material like you get in the lawn and garden section out of my mind when they say ceramics here.
> but in my minds eye ceramic is a porous substance that I can’t see holding a vacuum
It depends on how vitrified it is. Vitiried = “turned into glass”, typically by firing it to a higher temperature.
Normal clay kitchen items are not fully vitrified, which is why they are porous. One of the main reasons it’s done this way is so that the pieces can be self-supporting in the kiln whilst firing.
The outer layer of kitchen items is normally vitrified. This is a thin layer of glaze, ie a clay mix that melts and fuses at a lower temperature than the rest of the clay body. This is a practical tradeoff to obtain the waterproofness and appearance desired without having the entire piece turn into a puddle during firing.
I suspect these vacuum tubes might be fired in their moulds or somehow otherwise supported? Or perhaps the ceramic they’re using can somehow maintain integrity (not turn into a puddle) whilst fired to vitrifying temps?
Alumina ceramic has been used for decades in high power RF and microwave tubes, though…
I just visited their museum in Portland (https://vintagetek.org/). They had one of these on display as well as the mold. It’s interesting because they had to create a way to glue the glass (for the phosphor) to the ceramic. It allowed a more rectangular CRT, but honestly I think just started as a way to reuse the kiln they already owned
As someone who specializes in hard grinding ceramics machining I would be very interested to learn how that’s done. I see a lot of things here that make sense…
I worked a couple summers (80 & 82)on the 611 assembly line ‘flashing’ and soldering connector pins on the ceramic funnels. This brings back lots of memories.
Tektronix’s – Really?