Anyone who’s ever spent time in a woodworking shop knows how much dust is produced when cutting, sanding, and so on. [Tim] of Pilson Guitars was looking to outfit his shop with centrifugal dust separators to combat the problem, which are supposed to remove over 99% of the sawdust particles right out of the air. Unfortunately, they can cost thousands of dollars. So he decided to try making his own.
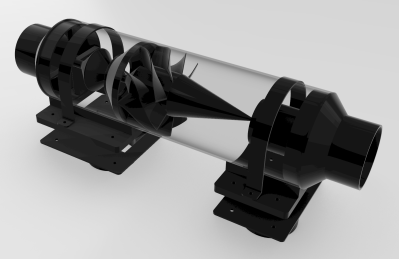
Using a clear PVC tube and 100 hours of printing on his Prusa i3 MK3, his CAD file had come to life, ready to use the power of centrifugal air to leave just enough fine dust in the output port to have a HEPA filter handle the remainder. Unfortunately, initial testing showed that a single dust separator filtered out far less than 90%, and even adding a second unit bumped that up to only 94.2%. Still impressive, but this would clog up a HEPA filter in no time. Thus [Tim] had a second try at it, after a range of helpful comments to the first video.
Changes included a different design for the impeller blades to improve the vortex, as well as attempting to run the system in series. Sadly more issues cropped up, with apparently the air also seeking a way via the collection bins that has [Tim] rethinking more aspects of the design. He has made the design files (STEP and more) available on GitHub for perusal by the community and hopefully some constructive input on how to DIY such dust separation system.
Over the years, we’ve seen many different approaches to the problem of dust collection. We’ve covered other 3D printed solutions if your printer is looking for something to do, but if you’d prefer something a little more low-tech, this traffic cone dust separator is particularly clever.
Thanks to [Keith Olson] for the tip.
I have a vacuum connected to a large bucket with the inlet on the side of the lid and an elbow in the bucket to make the air go swirl. It costs next to nothing and works like a charm with big nails and the finest wood powder.
Taking the vortex action out of the collection bucket makes it unnecessary complex imo.
I was going to say just about the same thing! I work around a 1959 DeWalt 16″ radial arm saw and for dust collection it goes to a Delta dust collector. The fan on it is in tolerable to getting hit by chunks of wood going up the tube. I used a plastic 55 gallon barrel and the lid is configured exactly like you’ve done with yours. Solid chunks that happen to pass through the 3″ collection nozzle as well as the saw dust fall out into the barrel and the Delta unit fills up with a fine powder. It gets emptied once a year to the barrel’s 3 to 5 times a year. Well done Arjan!
Same here, I made one for my cnc and it’s absolutely wonderful. Gravity is that good.
Onieda Air Dust Cobra
It’s nice n all but having read a bit about how many iterations and how long it took to get a cyclonic dust separator working in a small domestic vacuum cleaner* I’d probably have avoided all the pain and recycled the cylnders from a few broken vacuum cleaners from Freecycle or the local municipal tip.
* Apparently it’s not just a matter of scaling them down, some of the dimensions change in non obvious ways
Material choice may also be coming into play as the $4k one is using metal (conductive) tubing and cones / vanes versus the plastic (insulative) tube and cones,etc , electrostatic generation could also be playing a part dropping the filtering percentage by charging the dust particles to repel each other.
While the effort is laudable, it’s a lot of work for something available in a box at retail for $10 (plus the cost of a 5-gallon bucket and a cheap shop vacuum). Put two in line like he did with some good filters in between and you’ve got the same kit for under $50. And like 20 minutes work.
I like wooddust. You can mixed it with hideglue for removable fixed. You can mixed it with woodglue for slow curing fixes. You can fill a area and drop some superglue on it for fast fixed and also mixable with epoxy. It is a really versatile filler. Also i like it to pre soak it in different woodcolor shadings and store them dried in 5 marmelade jars. From light to darker. You can use the wood dust really like pigments and mix the wood tone you need. Next project is to use precolored (i prepare gray colored dust to fit the laminate print) wooddust epoxy on cracken laminate flooring.
That’s a good tip, I must remember that one, thanks.
Here is a example:
https://www.youtube.com/watch?v=QkkV34T2tI8
I don’t like mdf or multiplex dust. Carcinogenic and so on…
I story exactly the dust from laminate cuttings in a jar (exactly more in a small bag), for repair works with wood glue. But laminate is mostly hdf ( it’s denser and more water resistant) and after checking the jigsaw blade (gets dull) after cutting it must be swedish. Swedish laminate (Patent) contains fine quarz sand and also aluminium oxide (like from tile’s). Some woodcraft guys here sand the backside of a pice of laminate put something like autosol chrome polish (i think it is also aluminium oxide) on it and polish there chisel and planes (must be inspirent by american woodworkers).
What’s the deal with it? Why all the hassle to have three containers with dust instead of one?
Most of the dust is largeish. If you can separate the bulky dust, your filter can go much longer.
I have one of those 5 gallon cyclone separators that goes on a 5 gallon bucket. My shop vac has a fine dust bag and a HEPA filter. I am on the same bag for years and my filter hasn’t needed cleaning. I need to empty my 5 gal bucket pretty often.
For me the biggest benefit is not breathing in so much fine dust.
The last one is a HEPA canister filter. The benefit of cyclonic separation is a it drastically improves the lifespan of any filter following it by separating most of the dust and debris in the first container and reduces airflow resistance(compared to other methods). Most people have a cyclonic separator and then a canister filter, so I am not sure why this one has 2 buckets.
I believe this one has two buckets because there’s two holes under the cyclonic separators, one under each end – the inlet stage has two cones immediately after the inlet that fling out the really heavy stuff, and they fall into the first bucket. The second stage uses those vanes to swirl the air, and the finer dust falls down the hole near the outlet into a second drum.
The main issue is that very fine wood dust can remain suspended in the air for a long time and can easily be kicked back up after it settles, so a dust collection system needs to end with a very fine filter to keep workers in the shop safe (inhaling any kind of fine particulate matter is bad for your lungs).
However, dust collection systems also collect huge volumes of much larger wood shavings, bits, and dust in addition to the very fine stuff, so if you dump it all into one container with the fine filter, your filter clogs really fast, or else it has to be enormous (and expensive).
by using cyclonic separation in stages, the chonkier stuff can be dropped out early in the buckets, leaving only the finest fraction to be filtered at the end, prolonging the life of the filter and allowing the other stages to be emptied without stirring up the very fine dust.
I was initially disappointed with my lee valley cyclone lid used with a shop vacuum, but then I added a cardboard thien baffle underneath and was amazed how well it worked. Never looked back.
NOICE!!
I have the Original dust deputy without the “neutral vane” and my shop vac bag catches a large portion of the finer dust but the standard filter still slowly turns pine yellow, I’m going to 3d print an insert to act as a neutral vane and increase velocity of the centrifugal flow, hopefully improving suction, a hepa filter is on the way along with a new bag after that to start fresh , I just disassembled my shop vac and cleaned/lubricated the motor too so I think I’ll have a satisfying improvement by then. To comment relating to this guy’s invention, “more power to ya, because I have as of late a great interest in aerodynamics with 3d prints, and continue to test prototypes because aerodynamics and physics of ultra light dust is complicated”
So many comments ignoring the point of the prototype designs and design goal of having a hepa filter that doesn’t clog easily.
Why not combine origami and filter folding to increase the surface of a diy filter?
Perhaps another train of thought might be to consider other inline vortex generating system and observing that they are SMALL. Two examples come to mind. Dyson vacuums and vortex tube particle separators used on some military helicopters. The later uses a particle separator that uses hundreds of ~1/2″ vortex tubes. The only downfall with those systems is that they require a blower motor to eject the dusty air overboard. Dysons and this system use gravity to move the particles from where they exit the vortexes to the bucket.
https://images.app.goo.gl/NWQeryE7isxbMTsQ6
https://images.app.goo.gl/6h7CvRGoQV3r8KYQ9
https://images.app.goo.gl/4wLv6iH4KDNj7jDHA
100+ hours of wasted energy and plastic printing something that doesn’t work as well as some modified 5gal buckets?
This certainly isn’t written as a “what can we learn from this failure” article.
Why would HaD highlight this?