Some of the neatest products are made from the byproducts of other industries. Take petroleum jelly, for example. Its inventor, Robert Chesebrough, a chemist from New York, came upon his idea while visiting the oil fields of Titusville, Pennsylvania in 1859. It took him ten years to perfect his formula, but the product has been a household staple ever since. Chesebrough so believed in Vaseline that he ingested a spoonful of it every day, and attributed his 96-year longevity to doing so.
Well, some byproducts can simply be beautiful, or at least interesting. On that note, welcome to a new series called Boss Byproducts. We recently ran an article about a laser-engraved painting technique that is similar to the production of Fordite. I had never heard of Fordite, but as soon as I found out what it was, I had to have some. So, here we go!
Break Me Off a Piece of That Detroit Slag
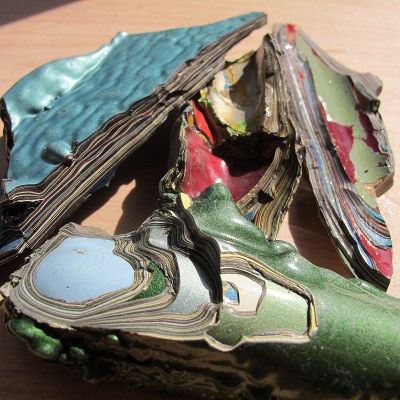
Fordite is man-made agate that came from the automotive industry. But even though it’s called Fordite, Detroit Agate, and other names, it is not classified as a gemstone, although some call it a mineral.
In the early days, cars were hand spray-painted in the factory, and then sent into huge ovens to cure. The over-spray built up on the racks and skids that the frames were painted on, and it eventually became thick enough that it had to be chipped away.
Legend has it that some workers saw beautiful psychedelic agate in the built-up layers and decided that it simply had to be recycled. They found that the stuff polished up with relative ease, and started making jewelry out of it. Fordite got popular enough that rock hounds would show up to the factories to help chip away the paint.
Different Models of Fordite
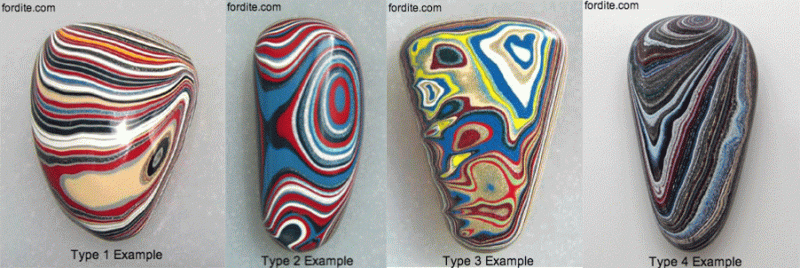
The material is classified in several groups depending on how the paint layers settled, and the resulting color banding:
Type 1 has separated colors, with regular bands of grey primer between the color layers. The rest are color-on-color, with Type 2 focusing on opaques and metallics. These have limited colors.
Type 3 might be the most visually interesting. These are drippy and/or striped and sometimes contain lace and orbital patterns. Type 4 is back to opaques and metallics, but these have bleeding color layers and sometimes pitting from air bubbles.
Layers of History
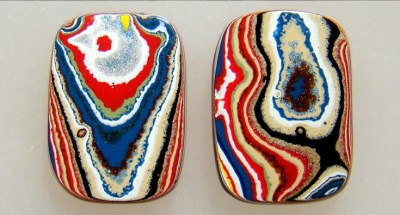
According to an article in the spring 2016 edition of GIA’s Gems and Gemology, it takes around 997 layers of paint to build up a 1-inch-thick slab of the stuff.
And, despite commonly being called Fordite, the material was salvaged from other plants as well, including the Corvette plant in Bowling Green, Kentucky, and there’s Lincoln-Mercury paint from Canada.
As you might imagine, paint from the early days of the automobile came in muted shades, but paint from the 60s and 70s is bright and colorful. Beginning in the 1980s, though, manufacturers stopped hand-spraying cars and started using an electrostatic method that binds the paint to the metal with little or no over-spray.
But there is plenty of Fordite to be had out there in all forms — raw material, polished cabochons, and finished jewelry pieces. Of course, many of those hardened enamel paints contain lead, so proceed with caution.
Many decades ago I visited a cabinetmaker’s workshop. In it was a spray booth with a bench with about 2cm of built up paint I used my pocketknife to carve out a beautiful piece.
Being Detroiters, my wife loves fordite. Our wedding rings are simple tungsten rings with fordite inlays.
pff. i think modern fordite is only made of black, black, black, grey, white, black, grey grey, black and white.
booring!
but on a side note, i used to be a camera mana and the film studios had a similar thing with the floors in the limbo studio: white, grey, blue and green were the colors, with the occasional red or yelow.
What in the world is a “camera mana”, or a “limbo studio”?
A camera mana is a camera man with an extra “a” at the end of the second word, and a limbo studio is a room where the sharp corners between the walls and the floor are rounded off so there is a smooth transition between them. mostly used with green screen techniques.
Awesome, thanks for answering! I never realized the types of techniques necessary to ensure good green screen work. :)
the most important is even lighting of the background an enough distance between the subject and the green background. if you don’t need feet in the shot, things get a lot easier and you can almost completely use separate light for the background (evenly lit) and foreground (dramatic possibilities)
but we digress…
They put cars in ovens? Sure about that?
Carocaust denier!
Yes, I’m sure of it. These were long, tunnel-like curing ovens where painted bodies went through on a conveyor.
Every spray shop has an oven that they wheel the car into, yes – sans interior and plastic trim usually but remember how hot cars get parked in the sun and all that stuff survives OK there.
Remember we’re talking about new cars here. I’m having trouble wrapping my head around the process.
build a car
paint the car
bake the car
install seats and stuff?
poke argue 0
poke ask 1
Poke salad Annie?
B^)
Seriously, the paint and bake occurs before plastics, wiring, and cloth gets put on/in.
Before that the “raw metal” car bodies dare often dipped in a pool of primer with the body with a positive or negative potential potential and the “pool” at an opposite potential, electrically bonding the primer to the metal.
s/dare/are
Went to the cadillac ranch this spring. Cadillacs buried nose into the ground, a wagon selling cans of spray paint to anyone who wanted to spray the vehicles.
Those vehicles had a inch or more of paint sprayed all over them. If you’re in Amarillo Texas some time and want Fordite, just go to the cadillac ranch and break off a few pieces.
(Free and open to the public.)
https://www.visitamarillo.com/listing/cadillac-ranch/625/
So in 1925 you could have any color of Fordite you want just so it was black…
I gave those to my wife in order to show her, that she’s perfect like afordite.