YouTuber [MechnicalRedPanda] has recreated a DIY STM hack we covered about ten years ago, updating it to be primarily 3D-printed, using modern electronics, making it much more accessible to many folks. This simple STM setup utilises a piezoelectric actuator constructed by deliberately cutting a piezo speaker into four quadrants. With individual drive wires attached to the four quadrants. [MechPanda] (re)discovered that piezoelectric ceramic materials are not big fans of soldering heat. Still, in the absence of ultrasonic welding equipment, he did manage to get some wires to take to the surface using low-temperature solder paste.
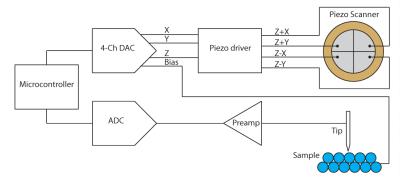
A makeshift probe holder was glued on the rear side of the speaker actuator, which was intended to take a super sharp needle-like piece of tungsten wire. Putting the wire in tension and cutting at a sharp angle makes it possible with many attempts to get some usable points. Usable, in this instance, means sharp down the atomic level. The sample platform, actuator mount and all the connecting parts are 3D-printed with PA-CF. This is necessary to achieve enough mechanical stability with normal room temperature fluctuations. Three precision screws are used to level the two platforms in a typical kinematic mount structure, which looks like the only hard-to-source component. A geared stepper motor attached to the probe platform is set up to allow the probe to be carefully advanced towards the sample surface.
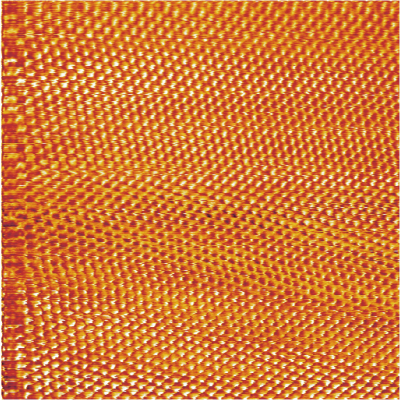
The next issue concerns vibration damping of the whole assembly. This was achieved with a simple hanging sprung platform, damped using an aluminium plate and magnets mounted underneath—a simple and effective eddy-current damper setup. For the electronics, a Teensy 4.1 runs the show, driving the four quadrants via a brace of AD5761 serial DACs and a few summing amplifiers.
Three DACs generate the X, Y and Z signals, which are sent to the quadrants as Z+/-X and Z+/-Y, and the fourth DAC generates a sample bias signal. The tunnelling current picked up by the probe tip is first sent to a preamplifier constructed using a very high gain transconductance (current-to-voltage) amplifier. However, the part used was not identified.
The whole assembly is electrically shielded with metallic tape, including the cable running down the main analog board, which hosts an LTC2326 ADC that can handle the bipolar differential signal being fed to it. The software was programmed using the Arduino stack for ease of use. The reason for the high-speed micro is the need to control the scanning signals based on the measured tunnelling current to form a control loop. We didn’t dig into precisely how that works! As can be seen from the video, he managed to get some quite decent images of the surface of a freshly peeled HOPG (graphite) lab specimen, so the setup works, and the noise sources are under control.
To read along, check out the project GitHub page, but more importantly, the original project by [Dan Berard].
Thanks to [rolmie] for the tip!
Use some Sorbothane pads feet or sheets to calm the machine down more stable up too 90% reduction of Vibration noise.
https://en.wikipedia.org/wiki/Sorbothane
Good tip!
Just 🤩 !
Maybe graphite IS orange but we lack the ability to see it 🤣
The distance between the atoms or the layers is way smaller than visual light wavelengths.
Where we’re going there ain’t no (pulls on sunglasses) “orange”.
Any estimates on the BOM total cost?
Likely ~$500 total. A nice HOPG sample and PtIr wire can be expensive alone. To be clear $500 is very cheap for what the technology is.
You can electrochemically sharpen tungsten wire to an atomically fine point using a low voltage AC source and lye. That’s how we made needles for the STM I used for research.
https://www.ncbi.nlm.nih.gov/pmc/articles/PMC2555190/pdf/bullwho00274-0151.pdf
Tungsten tips do not work well in atmospheric STMs due to oxidation, but you would know that since you work in STM.
My grandmother was born when Orville and Wilbur made their first flight. She also watched men land on the moon. I taught the theory of this groundbreaking, Nobel-prize-winning instrument in my early years of chemistry instruction. Now you can build the d*mn thing at home (“Image atoms at home! Amaze your friends! Loads of laughs!”)
I’m beginning to understand how Grammy felt…
Crazy how much progress has happened in the past 100 years. Wonder what advancements the precise control electron microscopes (transmission mostly) will bring in the next 50!
Cheers
@10:20 “as we learned in kindergarten” lol