Plastics are unfortunately so cheap useful that they’ve ended up everywhere. They’re filling our landfills, polluting our rivers, and even infiltrating our food chain as microplastics. As much as we think of plastic as recyclable, too, that’s often not the case—while some plastics like PET (polyethylene terephthalate) are easily reused, others just aren’t.
Indeed, the world currently produces an immense amount of polyethylene and polypropylene waste. These materials are used for everything from plastic bags to milk jugs and for microwavable containers—and it’s all really hard to recycle. However, a team at UC Berkeley might have just figured out how to deal with this problem.
Catalytic
Here’s the thing—polyethylene and polypropylene are not readily biodegradable at present. That means that waste tends to pile up. They’re actually quite tough to deal with in a chemical sense, too. It’s because these polymers have strong carbon-carbon bonds that are simply quite difficult to break. That means it’s very hard to turn them back into their component molecules for reforming. In an ideal world, you can sometimes capture a very clean waste stream of a single type of these plastics and melt and reform them, but generally, the quality of material you get out of this practice is poor. It’s why so many waste plastics get munched up and turned into unglamorous things like benches and rubbish bins.
At Berkley, researchers were hoping to achieve a better result, turning these plastics back into precursor chemicals that could then be used to make fresh new material. The subject of a new paper in Science is a new catalytic process that essentially vaporizes these common plastics, breaking them down into their hydrocarbon building blocks. Basically, they’re turning old plastic back into the raw materials needed to make new plastic. This has the potential to be more than a nifty lab trick—the hope is that it could make it easy to deal with a whole host of difficult-to-recycle waste products.
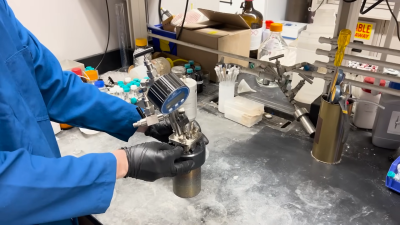
The team employed a pair of solid catalysts, which help push along the desired chemical reactions without being consumed in the process. The first catalyst, which consists of sodium on alumina, tackles the tough job of breaking the strong carbon-carbon bonds in the plastic polymers. These materials consists of long chains of molecules, and this catalyst effectively chops them up. This typically leaves a broken link on one of the polymer chain fragments in the form of a reactive carbon-carbon double bond. The second catalyst, tungsten oxide on silica helps that reactive carbon atom pair up with ethylene gas which is streamed through the reaction chamber, producing propylene molecules as a result. As that carbon atom is stripped away, the process routinely leaves behind another double bond on the broken chain ready to react again, until the whole polymer chain has been converted. Depending on the feed plastic, whether it’s polyethylene, polypropylene, or a mixture, the same reaction process will generate propylene and isobutylene as a result. These gases can then be separated out and used as the starting points for making new plastics.
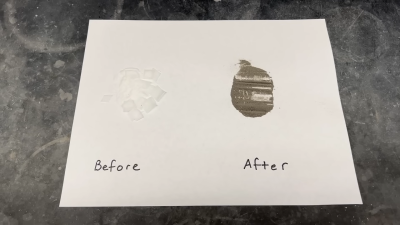
What’s particularly impressive is that this method works on both polyethylene and polypropylene—the two heavy hitters in plastic waste—and even on mixtures of the two. Traditional recycling processes struggle with mixed plastics, often requiring tedious and costly sorting. By efficiently handling blends, this new approach sidesteps one of the major hurdles in plastic recycling.
To achieve this conversion in practice is relatively simple. Chunks of waste plastic are sealed in a high-pressure reaction vessel with the catalyst materials and a feed of ethylene gas, with the combination then heated and stirred. The materials react, and the gas left behind is the useful precursor gases for making fresh plastic.
In lab tests, the catalysts converted a near-equal mix of polyethylene and polypropylene into useful gases with an efficiency of almost 90%. That’s a significant leap forward compared to current methods, which often result in lower-value products or require pure streams of a single type of plastic. The process also showed resilience against common impurities and should be able to work with post-consumer materials—i.e. stuff people have thrown away. Additives and small amounts of other plastics didn’t significantly hamper the efficiency, though larger amounts of PET and PVC did pose a problem. However, since recycling facilities already separate out different types of plastics, this isn’t a deal-breaker.
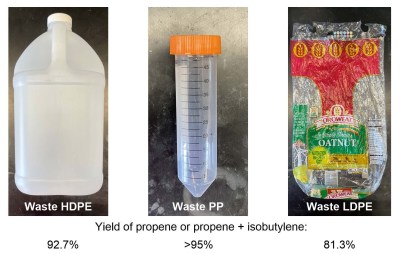
One of the most promising aspects of this development is the practicality of scaling it up. The catalysts used are cheaper and more robust than those in previous methods, which relied on expensive, sensitive metals dissolved in liquids. Solid catalysts are more amenable to industrial processes, particularly continuous flow systems that can handle large volumes of material.
Of course, moving from the lab bench to a full-scale industrial process will require further research and investment. The team needs to demonstrate that the process is economically viable and environmentally friendly on a large scale. But the potential benefits are enormous. It could actually make it worthwhile to recycle a whole lot more single-use plastic items, and reduce our need to replace or eliminate them entirely. Anything that cuts plastic waste streams into the environment is a boon, too. Ultimately, there’s still a ways to go, but it’s promising that solutions for these difficult-to-recycle plastics are finally coming on stream.
Plastic as battery! Since we have plastic explosives.
This isn’t the first time this has been proposed. It remains to be seen if it can scale up economically. I hope it can, but based on the number of past cases I’m not holding my breath.
out of college 20 years ago we were working on gas phase reactions over solid catalysts. I didn’t read article by usually “silica” substrates are zeolites- super micro-porus materials that have crazy high surface areas and, in theory, can function well as catalysts or substrates for holding catalysts. This article’s science, however, begs 1) how hot does it have to be and 2) at what pressure? Our project, and probably this one, had energy balance issues ie the end products needed more energy put in than were recovered. Unless you can create a high value product at the end- complex macrocycles or something.
.
I’m inclined to agree with some other commenters, just burn the stuff and get energy out. From a green point of view, I guess, recycling is a noble goal but not if you need more energy to do it that comes from… probably fossil fuels? anyway.
.
Cool idea in any case, a bit of nostalgia for me.
That’s the devil in the details. Where does the ethylene gas come from?
Why not just burn it for energy?
Additives.
Maybe because that is worse than recycling it?
How?
Recycling takes energy and a feed of ethylene gas using this process, which comes as a byproduct of natural gas production, so whatever materials you save in recycling plastics is lost twice over in running the process.
energy can come from anywhere and ethylene is a basic hydrocarbon. honestly, the more hydrocarbons that go into plastic production instead of being burnt as fuel, the better.
Ethylene can in theory be made by synthesis, but the energy for it comes from fossil fuels and production is so little that for the majority of uses the gas is separated from natural gas anyways. Then, running the recycling process uses more energy and burns more hydrocarbons – by diverting renewable energy away from the grid.
What it means is, you burn more fossil fuels to recycle the plastic than just making new plastic. In a perfect world, you’d make the plastic and the ethylene by synthesis from water and CO2, but we’re not living in it.
Price. Virgin plastic is worth more than the micropennies you’d earn from burning it.
Current recycled plastic is worth its weight in garbage. Annealing it to reshape it into something else breaks the long chains that give it its strength, so it’s only good for heavy bulky stuff like decking and benches.
But reducing it to its initial gases means they can use it to make new plastic equal to the oil based stuff. That’s worth more than its weight in gasoline.
Your economic analysis is shallow.
Ignoring important costs on both sides.
Noteably the cost of recycling the plastic to feedstock and the cost of making feedstock from hydrocarbons.
Do accounting in CO2 if you prefer.
Most common virgin plastic granules have costs similar to gasoline.
There is no goldmine here.
Burn them? In terms of plastics, they’re some of the cleanest fuels around. Basically candle wax. Heat and oxygen have no issue dealing with this “problem”.
Better yet burn them in your engine!
https://solar.lowtechmagazine.com/2023/11/plastic-waste-in-the-fuel-tank/
Burn lean with forced air, add 10% witches to sustain fire through slack power demand periods.
just incinerate it to make heat and power, it is basically oil that has taken a detour. As long as we still use fossil fuel for heat and power it’ll offset other fossil fuels
There appear to be some tests converting coal power plants to burn mixed plastic waste and “biogenic material” like paper or cardboard. Undoubtedly these could eventually be made from post-consumer material. The one I found appears to buy fuel pellets made off-site.
here almost all trash get incinerated for heat
Then is not trash, is fuel.
“Someone’s trash is someoneelse’s treasure”.
More witches!
Sorry, is harvest season.
the longer this carbon stays in plastic and not co2 in the atmosphere, the better for the planet
If we can make plastic from the mess that is crude oil then we can make synthetic oil from the mess that is waste plastic, just add heat from burning the byproducts of the process.
Did you know that if you put plastc, water, and any organic “waste” into a pressure vessel, heat it up above boiling, then flash decompress the mix, the result is randomly broken carbon bonds in the organic waste producing something resembling crude oil?
https://en.wikipedia.org/wiki/Thermal_depolymerization
That article focuses on then burning it which is pretty silly. Why not then put it through a fractional distillation process and recover industrially important materials, quite possibly, even the monomers for the plastic! The process is off patent, though some of the catalyst use may still be patented, but the base process was patented in the 90’s.
Quit searching for perfect solutions. Perfect is the enemy of good.
Because all the heat and energy you use to do that is more than the heat / energy value of the “crude oil” you generate. I worked in the industry – the thermodynamics don’t add up. All those C-H bonds have to come from somewhere. So you’re running a net energy-requiring process and the energy needed to do that comes from. …wait for it… fossil fuels.
In other words what you are saying is take oil, make plastic out of it, then make crude oil out of that. Each of those steps requires energy. It’s a loop that loses every step of the way.
Just burn half the plastic to depolymerize the other half. Sort of like making charcoal.
Definitely burn it rich and cool, nothing bad can possibly come out the stack.
Whatever happened to Plasma Gasification waste treatment? Turned products into a burnable Hydrogen gas mixture and a slag that was easy to deal with. Was supposed to be energy positive by some amount.
Plastics. If you can’t recycle it cheaply is it really worth recycling at all?
Silly question: if plastics are so chemically stable that they don’t break down in land fills, why don’t we just keep burying them? The oil that was used to make them came out of the ground. Putting the plastic back into the ground prevents the carbon from ending up in the atmosphere when the stuff is incinerated. Isn’t putting plastic underground a form of carbon sequestration?
Mostly because what ISN’T in the landfill is breaking down via ultra violet sunlight fraction and leaving wee bits of stable semi toxic (or process modified) plastic fluff everywhere
What plastic isn’t buried and instead exposed to UV gets broken down to smaller and smaller bits, to the point that it begins to biodegrade.
Most plastics do biodegrade – it’s just a matter of the polymer chains being too difficult to break down by organisms. Plastics like PE and PP are hard for bacteria to eat, because their enzymes can only attach at the ends. If you break the strands into smaller bits by UV light, it becomes edible and basically composts away in months instead of decades.
The base plastic isn’t toxic per se. The additives like fire retarding chemicals can be though, you’re right about that.
The main issue with microplastics is when they end up in the sea, because fish and birds eat the small grains of plastic instead of plankton etc. On land, they either get buried in the soil where they’re basically inert and do nothing, or they break down by UV and get eaten up by soil bacteria.
Ethylene is an issue if you are trying to help the environment. It’s production is usually by cracking petrochemicals and it creates lots of CO2 during the process of making it. It’s production is also energy intensive.
Exxon has announced industrial cycling to start at Baytown.
I thought it was dirty to burn?