Ink stamps can be fun to make and use, and 3D printers are uniquely positioned to create quality stamps of all kinds with just a little care. As with most things, the devil is in the details and the best results will require some extra work. Luckily, [Prusa] has a blog post that goes through how to 3D print the best stamps and includes concrete recommendations and tips to get the most out of the process.
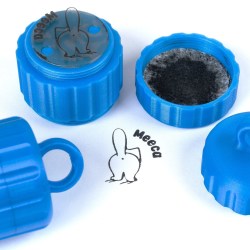
What makes a good 3D-printed stamp? It should be easy to use, transfer an image cleanly, and retain ink reasonably well. To hit these bases, printing the stamp face out of a flexible material is probably the most important, but a flat and smooth stamp surface is equally crucial. Satin-finish build plates will give a weathered look to the stamp, but textured build plates in general are no good.
As for the design, turning an image into a 3D object can be a bit challenging for novices, but there are tools that make that much easier now than it used to be. Some slicers allow importing .svg
files (scalable vector graphics) with which to emboss or deboss objects, and online tools as well as free software like Inkscape will let folks covert images into .svg
format.
Flexible filaments tend to be stringy so they should be dried before use, especially if the stamp design has a lot of separate elements that invite stringing. Any flex filament should do the job, but of course some specific filament brands perform better than others. Check out the full blog post for specific recommendations.
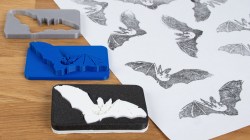
The remaining tricky element is that flexible filaments also tend to be poor at bridging, and if one is printing a stamp face-down on the build plate (to get that important, ultra-flat face) then the upper inside of the stamp may need some support for it to come out right. As [Prusa] suggests, this is a good place to use a manual, drop-in pre-printed support piece. Or if one has the ability to print in multiple materials, perhaps print the support structure in PLA since it is just about the only material that won’t completely weld itself to flex filaments. Of course, if one is designing the stamp entirely in CAD, then the best option would be to chamfer the stamp elements so supports aren’t necessary in the first place. Finally, don’t overlook the value of a physical design that makes handling easy and attractive.
Since 3D printing makes iteration so fast and easy, maybe it would be worth using this to revisit using rubber stamps to help create PCBs?
Better to print a negative of your stamp and use that to mold the rubber pad.
Using photopolymer stamp resin, which has a gum like consistency, on an mSLA printer is doable but doesnt give as good a result as doing a molded transfer. Depending on your printer resin you may need to give it a brushing of PVA to prevent cure inhibition.
Yep. I figured someone would have pointed this out.
I think it would be better to use SLA to print a negative, use some shore 50A or whatever silicone to make the actual head and then FDM/SLA print a nice body and handle for the stamp
Just print design side up and give it a quick sand with fine grit to level everything. That way you don’t have to care about supports.
Are flexible filaments sandable?
Everything is sandable if you try had enough.
Yes, with more care (and you may have to do it wet) as it can more easily gall the sandpaper – but all filaments do that if you are too aggressive.
If not, then lasercut it flat. :-)
I printed stamps to make logo’s into leather. Works extremely well. Just make sure to sand down the 3D printed lines and make sure it sticks out far enough. Put the leather in warm water for 10-15 minutes, take it out, press the stamp into the leather and wait for one minute and done.
Why would anyone try it without SLA.
In my experience, SLA is cool, but it does take a lot of extra work to use safely. In most cases, I get the desired effect for any given project with my FDM, and can dodge the added workload.
I wouldn’t bother with the overhangs and just print the thin “rubber” part that you want to want to actually print, then (while it’s still on the build plate) contact cement or double-sided tape onto a “backer plate” which might be part of the handle.
This. The overhangs are superfluous, probably remnants of standard rubber / handle / pad sizes and the subtractive manufacturing process.
I like these simple but well sciences projects that find the optimal combination, saves a huge amount of accumulated time for the rest of us!
I use pla then sand it flat and smooth as possible. Then I just hit it with a couple coats of flex seal from a can. Super easy to print, and the flex seal dries very quickly so you can do a couple coats in a couple minutes. Never seen anyone do this. But it works extremely well. Not great for very fine definition though.