3D prints aren’t typically known for their heat resistance. However, [Integza] noted that using the right techniques, it was possible to 3D print parts that could handle steam heat without failing. Thus, the natural progression from there was to build a piston-type steam engine.
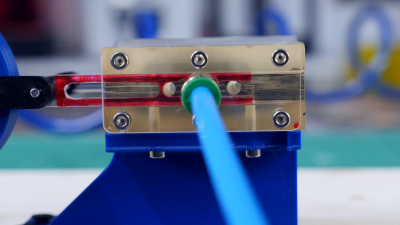
Resin prints are key here, as the melting point of such parts is much higher than that of those turned out by typical FDM printers. Try this same build using PLA for the hot parts, and you’ll quickly end up with a pile of molten goo.
To make such an engine work, valves are required to allow steam to flow into alternating sides of the piston to let it reciprocate continuously. A simple slide valve is used, allowing steam to flow to one side of the piston and the other alternately, as driven by an arm coming off the flywheel attached to the engine’s output shaft.
Tested on compressed air and steam, the engine ran continuously, chugging away enthusiastically. However, steam performance was compromised by the low pressure output of just 1.5 bar from [Integza]’s pressure cooker. Similarly, the cooker’s steam capacity was low, so the engine ran for just 15 seconds.
However, it suggests that with a better supply of steam, the printed steamer could indeed run for some time. If you’re not into the wetter engines out there, though, consider extruding a Stirling engine instead. Video after the break.
Continue reading “You Can 3D Print A Working Reciprocating Steam Engine”