The widespread availability of inexpensive 3D printers has brought about a revolution in what can be easily made at home. However these creations aren’t perfect, particularly when it comes to the adhesion between their layers. Aside from structural failures along the layer lines there is also the question of those joins being permeable, limiting the possibility for waterproof or gas proof prints. It’s something [German Engineer] has tackled in a new video, in which he’s looking at the design and preparation of small propane tanks.
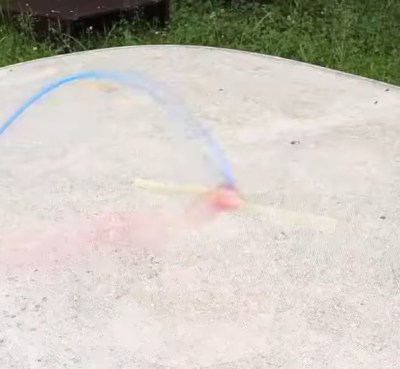
The attraction of propane as a fuel is that it liquefies easily on compression, so a propane cylinder or tank will be an equilibrium of liquid propane with pressurized gas above it, whose pressure depends on the ambient temperature. This means that any tank must be expected to have a working pressure somewhere between 150 and 200 PSI, with of course a design pressure far exceeding that for safety reasons.
Filling a 3D printed tank immediately results in the propane escaping, as he demonstrates by putting one of his prints under water. He solves this with a sealant, Diamant Dichtol, which is intended to polymerize in the gaps between layers and create a gas-tight tank. A range of three tanks of different thicknesses are treated this way, and while the 1 mm thick variety bursts, the thicker ones survive.
It’s clear that this technique successfully creates gas-tight prints, and we can see the attraction of a small and lightweight fuel tank. But we can’t help worrying slightly about the safety, for even when the material is a lightweight 3D print, high pressure equipment is not to be trifled with. Tanks do burst, and when that happens anyone unfortunate enough to be close by sustains nasty, even life-threatening injuries. Use the technique, but maybe don’t hit it with high pressures.
Continue reading “Gas-Tight FDM 3D Printing Is Within Your Grasp”