Electric cars are all the rage lately, but let’s not forget about the old standby – internal combustion. The modern internal combustion engine is a marvel of engineering. Today’s engines and surrounding systems have better power, greater fuel economy, and lower emissions than anything that has come before. Centuries’ worth of engineering hours have gone into improving every aspect of the engine – with one notable exception. No automotive manufacturer has been able to eliminate the engine’s camshaft in a piston powered-production vehicle. The irony here is that camless engines are relatively easy to build. The average hacker could modify a small four-stroke engine for camless operation in their workshop. While it wouldn’t be a practical device, it would be a great test bed for experimentation and learning.
Suck, Squeeze, Bang, Blow
A multi-cylinder gasoline engine is a complex dance. Hundreds of parts must move in synchronicity. Valves open and close, injectors mist fuel, spark plugs fire, and pistons move up and down. All follow the four-stroke “Intake, Compression, Combustion, Exhaust” Otto cycle. The camshaft controls much of this by opening and closing the engine’s spring-loaded intake and exhaust valves. Lobes on the shaft press on tappets which then move the valve stems and the valves themselves. The camshaft itself is driven at half the speed of the crankshaft through timing gears, chains, or a belt. Some valve trains are relatively simple – such as overhead cam engines. Others, such as the cam-in-block design, are more complex, with pushrods, rockers, and other parts required to translate the movement of the cam lobe to movement at the valve.
Exactly when, and how fast a valve opens is determined by the profile of the cam lobe. Auto racing and performance enthusiasts often change camshafts to those with more aggressive profiles and different timing offsets depending on the engine’s requirements. Everything comes at a cost though. A camshaft machined for maximum power generally won’t idle well and will make the engine harder to start. Too aggressive a lobe profile can lead to valve float, where the valves never fully seat at high RPM.
Myriad Solutions
Engine manufacturers have spent years working around the limitations of the camshaft. The results are myriad proprietary solutions. Honda has VTEC, short for Variable Valve Timing and Lift Electronic Control. Toyota has VVT-i. BMW has VANOS, Ford has VCT. All these systems provide ways to adjust the valve action to some degree. VANOS works by allowing the camshaft to slightly rotate a few degrees relative to its normal timing, similar to moving a tooth or two on the timing chain. While these systems do work, they tend to be mechanically complex, and expensive to repair.
The simple solution would be to go with a camless engine. This would mean eliminating the camshaft, timing belt, and most of the associated hardware. Solenoids or hydraulic actuators open and close the valves in an infinitely variable number of ways. Valves can even be held open indefinitely, effectively shutting down a cylinder when max power isn’t necessary.
So why aren’t we all driving camless engines? There are a few reasons. The advantages of camless engines to camshaft engines are analogous to the advantages of electronic fuel injection (EFI) vs carburetors. At the core, a fuel injector is a solenoid controlled valve. The fuel pump provides constant pressure. The engine control unit (ECU) fires the injectors at just the right time to inject fuel into the cylinders.The computer also leaves the valves open long enough so that the right amount of fuel is injected for the current throttle position. Electronically this is very similar to what would be required for a camless engine. So what gives?
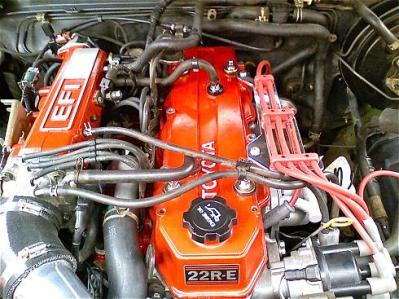
Hackers in their 30’s and beyond will remember that until the late 1970’s and early 1980’s, the carburetor was king. Companies had been experimenting with EFI since the 1950’s. The system didn’t become mainstream until the stiff pollution laws of the 70’s came into effect. Making a clean, fuel-efficient carbureted engine was possible, but there were so many mechanical and electronic actuators required that the EFI was a better alternative. So the laws of the 70’s effectively regulated carburetors out of existence. We’re looking at much the same thing with camless engines. What’s missing are the regulations to force the issue.
All the big manufacturers have experimented with the camless concept. The best effort to date has been from Freevalve, a subsidiary of Koenigsegg. They have a prototype engine running in a Saab. LaunchPoint Technologies have uploaded videos showing some impressive actuator designs LaunchPoint is working with voice coils, the same technology which moves the heads in your hard drive.
None of this means that you can’t have a camless engine now – companies like Wärtsilä and Man have engines commercially available. However, these are giant diesel engines used to drive large ships or generate power. Not exactly what you’d want to put in a your subcompact car! For the hacker set, the best way to get your hands on a camless engine today is to hack one yourself.
Ladies and gentlemen, start hack your engines!
Simple, single-cylinder camless engines are relatively easy to build. Start with a four stroke overhead valve engine from a snowblower, scooter, or the like. Make sure the engine is a non-interference model. This means that it is physically impossible for the valves to crash into the pistons. Add a power source and some solenoids. From there it’s just a matter of creating a control system. Examples are all over the internet. [Sukhjit Singh Banga] built this engine as part of a college project. The control system is a mechanical wheel with electric contacts, similar to a distributor cap and rotor system. [bbaldwin1987’s] Camless Engine Capstone project at West Virginia University uses a microcontroller to operate the solenoids. Note that this project uses two solenoids – one to open and one to close the valve. The engine doesn’t need to rely on a spring for closure. [Brian Miller] also built a camless engine for college, in this case Brigham Young University Idaho Camless Engine. [Brian’s] engine uses hall effect sensors on the original camshaft to fire the solenoids. This route is an excellent stepping stone before making the jump to full electronic control.
It wouldn’t take much work to expand these projects to a multi-cylinder engine. All we’re waiting for is the right hacker to take up the challenge!
In 1974 I worked at Cerwin-Vega, an L.A. loudspeaker manufacturer. The owner/founder, Gene Czerwinski, was backing a camless engine project using, IIRC, solenoids. I don’t know what they were using to control valve timing; the Intel 8008 was state of the art, and it doesn’t seem like it would have been fast enough.
What about pizeo-electric/hydraulic valves?
http://www.moog.com/products/servovalves-servo-proportional-valves/
Next up,
the Toyota Camfry Camry!
B^)
This is what I like about Hackaday … you never know what to expect. When I saw this variable valve timing article, it immediately took me back to a design I had worked on years ago. With gritted teeth, I read all the 170 posts (at the time) expecting to find what I never finished. But to my surprise, none of the hydraulic, pneumatic, solenoid, and of course the standard cammed systems, were like my design.
Now I’m all excited again but unfortunately I’m involved with another project … a multiple independent head 3D printer with 16 heads on a 1 x 1 meter print area with no belts, robotics, bearings, or precision rods.
So getting to the point, I would very much like to pursue the variable valve timing design again (it also features variable valve springs!), but I would need help.
Any entrepreneurs out there?
Sky Spencer
moreheads3dp@outlook.com
There is always a lot of talk/hype about servo- actuation.
The conventional combustion chamber on multi-cylinder engines has too small a squish volume, into which the valve opens, so a slow rising valve risks killing an engine (unacceptable).
Reliable actuator designs remain hideously expensive & large, which raises the bonnet line & price (unacceptable).
Unless you evolve thinking to accept fewer cylinders & longer stroke – such as used in sidevalve (rather than OHC/ OHV) type engine configurations then direct valve activation concept will remain a lab curiosity.
Personally I love a variant of Hyper-expansion engines; as the stroke is enormous, slow & the exhaust valve timings are not so critical ….& well suited to solenoid operation IMHO. One barrier to these was regulators obsession with reducing cubic inches. If the taxation refocusses on CO2, NOx & PM10s then this is something to watch.
That said the most likely direction is using small gas turbines to top up the battery pack while you drive & shop……
Have a look @ ducati desmo.it’s a motorbyke engine who uses a camless intake and output of mixture and gases using a rotary system. it’s out by some years now.
Camless enging is now being developed:
http://www.roadandtrack.com/new-cars/car-technology/news/a31657/koenigseggs-camless-engine-getting-close-to-production-in-china/
As I recall, Hot Rod Magazine did a spread on a solenoid actuated valve system many many years ago. (60s I think)
Two guys here in Los Angeles, engineers they claimed, but I never saw any production units.
Dr. Marius Paul owner of Engine Corp Of America designed a rotary valve system back in the 80s.
I saw one run on a dyno, and jesus, what power it had. Dr. Paul specialized in A.P.U. systems for the military..
Clever guy.. Google knows him..
The Opposed Piston Engine originated in 1918. I wonder why it has never been commercialized? Maybe it’s because it won’t fit in anything. Depending on the direction you turn it, it is too wide or too tall.
Camless, and not with us quite yet.
https://www.brighton.ac.uk/advanced-engineering/facilities/multicylinder-camless-engine.aspx
I expect demand for engines with wide speed / load requirements will drop in favour of series hybrid electric cars. No need to vroom up through the gears, if all you’re doing is driving a generator. Look at the London Taxis for an example. Up from 20 (uk) mpg on diesel to 50 mpg on petrol.
https://www.autoexpress.co.uk/car-news/98450/new-tx-electric-london-taxi-priced-at-55599
I was privileged to meet and see Dr. Pauls shop when he was still with us. (RIP) Very smart man, converted turbos to turbines, and made compact Auxiliary Power Units for the military. (APUs) The system I witnessed in his engine dyno was a Detroit diesel 2 stroke converted to a 4 stroke engine. The intake was a “Rotary Sleeve” type, driven from the crank. No valves, just a slot in a spinning bar. He tested the engine using a variable gas turbine as a adjustable turbo. Hard to describe the noise that thing made. Sadly, we all get old. He is missed.