There are two types of Hackaday readers: those that have a huge stock of parts they’ve collected over the years (in other words, an enormous pile of junk) and those that will have one a couple of decades from now. It’s easy to end up with a lot of stuff, especially items that you’re likely to use in more than one design; the price breakpoints at quantities of 10 or 100 of something can be pretty tempting, and having a personal stock definitely speeds the hacking process now that local parts shops have gone the way of the dinosaur. This isn’t a perfect solution, though, because some components do have shelf-lives, and will degrade in some way or another over time.
If your stash includes older electronic components, you may find that they haven’t aged well, but sometimes this can be fixed. Let’s have a look at shelf life of common parts, how it can be extended, and what you can do if they need a bit of rejuvenation.
New Sample Books of Old Components
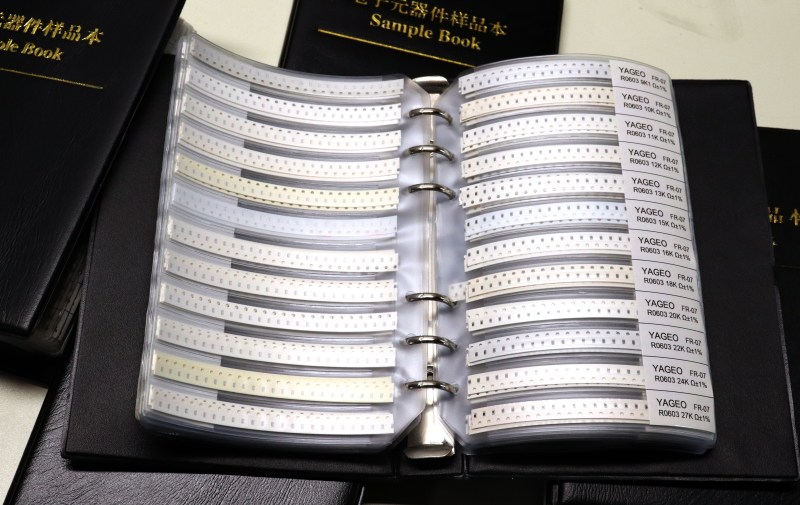
More than 20 years ago, I bought a couple hundred of each of the common E24-series values of 1/4 W through-hole resistors – 169 different values in all. In the intervening two decades, I’ve rarely needed to purchase resistors for quick prototypes or even small-batches of boards; I just re-stock whenever a bin goes empty. More recently, I started to purchase similar assortments of surface-mount components, including resistors, capacitors, and a smaller selection of inductors. The fact that I need to stock multiple sizes is offset by the lower per-unit cost of the SMD parts, so the up-front investment is roughly the same, as is the convenience of having parts on hand.
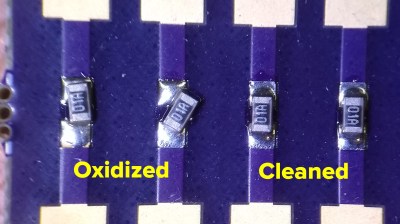
While I’ve never had a problem soldering the through-hole resistors, the SMD parts from the sample books have proven problematic right from the start. I found that some of the components don’t reflow correctly: they float on top of the molten solder, shifting around and not adhering to the PCB, finally held on by nothing but flux in some cases. This is commonly known as a “head-in-pillow” defect. After a little experimentation, I’ve concluded that some of these component sample books are probably populated with cut tape from very old component reels which are no longer suited for automated pick-and-place assembly. I imagine there’s a little cottage industry — somewhere — of cutting up expired reels, stuffing them into books, and hawking them on eBay.
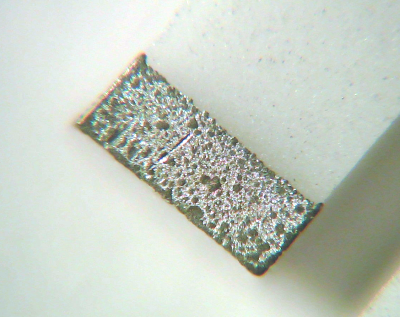
After being frustrated at having to hold down the components with tweezers during reflow to get them to stick, I turned to the Hack Chat over on Hackaday.io for help. There, [salec] suggested that I try cleaning the components by rubbing them on an ordinary sheet of paper before placing them on the PCB. To my surprise, this worked like a charm; the cleaned components soldered perfectly. I subsequently took a look at some of the components under a microscope, and found that the terminals showed a layer of oxidation — easily removed with the paper trick — that prevented solder from properly wetting them. If you try this yourself, make sure you wash your hands thoroughly afterwards, since these older parts may use tin-lead solder, and the cleaning process produces very fine particles which could easily be absorbed if ingested. There’s a short video at the end of this article that shows the process of cleaning these components and the effect it has on their performance during reflow soldering.
Solderability is a Thing
It turns out that solderability is a measurable attribute. By dipping a component terminal into molten solder and examining the resulting solder film, you can evaluate its soldering performance. A form of this dip-and-look method is codified in Mil-Std-883 Method 2003.7 (PDF), which also includes an accelerated aging test that exposes the part to water vapor at around 90 ℃. The pass/fail criterion is 95% solder coverage when examined under magnification.
Back in the good old days when solder was made with lead, solderability needed to be periodically tested because lead-tin alloys are subject to oxidation than can impact solderability. This effect is much less pronounced in lead-free solders. In fact, a paper by Air Products (PDF) shows that tin-lead solder grows an oxide layer about ten times as thick as tin-copper or tin-silver solder. This is what leads me to believe that the problematic SMD components I’ve encountered are old, tin-lead coated parts.
An application note from Mini Circuits (PDF) explains the age restrictions on current-production parts for some picky customers. The U.S. military has eliminated date code restrictions on parts, and NASA now only requires parts to be reviewed after 5 years to see if they need to be tested. Before the advent of lead-free solders, military applications required solderability retesting of components three years after the marked date code. More evidence for long shelf-lives comes from a Texas Instruments study (PDF), which found no impact on ICs stored for more than 15 years in a humidity-controlled environment.
So, if you are buying RoHS-compliant parts today, they’ll probably be fine for a long time. If, on the other hand, you’re buying parts of unknown provenance from online auction sites, or have already amassed a collection of lead-solder coated parts, you may need to address solderability issues at some point. For old through-hole components, I’ll often re-tin the leads with the iron and a little fresh solder just before soldering them in place when dead-bug prototyping, as this helps make a good joint. This same trick could theoretically be used with surface-mount components, but practically, it would be much more difficult; the paper trick is much easier.
PCB Aging
Common FR4 printed circuit boards also age. Although the substrate can absorb moisture, requiring a pre-bake before soldering in some circumstances, the primary concern for the hobbyist is again reduced solderability over time. As with component leads and pads, the surface treatment determines how aging will affect the usability of PCBs. Common finishes seen for hobbyist prototype boards include leaded and lead-free HASL (hot air surface leveling) and ENIG (electroless nickel/immersion gold).
The literature lists tin-lead HASL as having an “excellent” shelf life exceeding 12 months, while lead-free HASL and ENIG are both listed as 12 months. You’d think that the gold coating would stay solderable indefinitely, but the gold coating is actually somewhat porous and allows oxygen to contact the nickel layer, which easily oxidizes. It’s also a little surprising that tin-lead HASL supposedly has a longer shelf life than lead-free HASL based on the shelf life of components with similar finishes, but your mileage will vary depending on storage conditions.
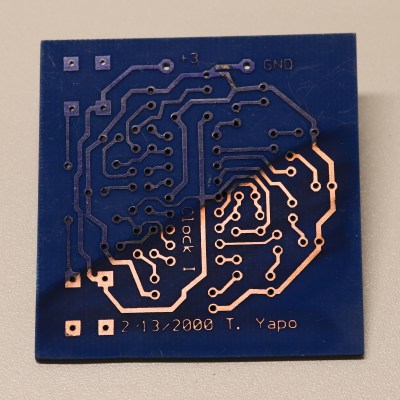
The recommended method for long-term PCB storage is vacuum sealing. If you have a kitchen vacuum sealer, you could certainly give this a shot if you have boards you want to preserve for a while. Throw in a desiccant packet if you have one. And if someday you find yourself with old PCBs that just won’t solder, you could try using a little extra flux, or even a quick dip in an etching solution — rinse thoroughly afterward — to restore solderability.
Interestingly enough, if you’re etching your own PCBs, you may not have to worry about aging at all. I recently found a PCB I had etched using the toner transfer method in February 2000, then threw in a box and forgot about. Today, a quick wipe with an acetone-soaked paper towel revealed perfectly clean and ready-to solder copper under the nearly two-decade-old toner. Once you remove the toner, however, the clock starts ticking. If you wait too long, you may have to re-clean the copper – a Scotch-Brite pad is my preferred tool – before soldering. This PCB was one of two that I made for a PIC16F84-powered LED clock project; the other board got populated and is probably around here somewhere.
What about the Solder?
Solid solder, either in bar or wire form, that contains no flux, is essentially forever. Even though the outside may become oxidized, with the appropriate application of flux during soldering – you need to apply a flux if your solder doesn’t bring its own – the joint will turn out fine. Even flux-cored wire solder seems to have a practically unlimited life, although manufacturers will tell you that it does eventually go bad, due to the slightly corrosive action of the flux. I have used some very old flux-cored wire solders, and have never heard of anyone – at least at the hobbyist level – having a serious issue with old wire solder. On the other hand, if you are assembling commercial products, you might want to heed the solder manufacturer’s advice, although you may be less likely to encounter old stock in that kind of environment.
Solder paste is a different story. It definitely goes bad, and I have seen it. Depending on the manufacturer and product, there will be an expiration date on the package, and usually instructions for refrigerated storage. Solder paste contains very fine balls of metal mixed with a liquid flux. Over time, the flux can dissolve the protective oxide layer on the outside of the solder balls, causing them to fuse together. This effectively increases the viscosity of the paste, making it more difficult to work with – especially if you use a syringe and hypodermic needle for assembling prototypes. This process also reduces the effectiveness of the flux, so that during reflow, it is less able to dissolve oxide layers when it’s really needed.
In a hobbyist environment, you can push things a little. I have stored a syringe of paste, claiming a shelf life of one year refrigerated, for around three years at room temperature out of sheer laziness. While it still “worked,” a fresh syringe of the same stuff was amazingly easier to use near the end. I won’t be doing that again – I ended up with a lot of unnecessary rework. There are some solder pastes on the market that don’t need to be refrigerated: Loctite GC10, for instance, can be officially stored for one year at room temperature. I’m sure it could be pushed much longer than that in a hobbyist context. The only downside is that it appears to only be available in relatively large containers.
Wrapping Up
So those are a few issues you may encounter when using old parts. If you know of any others, you can share in the comments below. We’d all like to know about them.
I’m not even going to get into the aging issues with electrolytic capacitors. Between the electrolyte drying out and the oxide layer possibly needing reforming, they’re absolutely terrible, but I had to mention it here just in case anyone didn’t already know this, especially since we recently ran an Ask Hackaday article about capacitor issues.
Meanwhile, you can check out the video showing how to clean SMD parts and the results. it’s only 2:20 long, but if you want to skip right to the good part showing the reflow, you can go directly to 1:36.
Thanks!
I was unaware of SMD components developing a thin, but stubborn layer of corrosion before being placed.
In general, most suppliers state a 3 year shelf life for sealed SMD part spools, as even inside a plastic bag diffused moisture begins to cause problems.
There is also a phenomena where some 0.1% precision parts can settle into their stable values in that time.
Usually, people figure out mixing extra solvent-diluted flux into a SAC305 solder paste will solve most issues like tomb-stoning. However, once you mix in extra flux, one usually only has a few weeks to use the remaining paste even if refrigerated. Note a silver solder is very good at sticking to the dozens of different coatings manufacturers use.
Sample books are often stored exposed to the atmosphere without a desiccant.
YMMV
;)
I just wanted to say that I am not opposed to fair use, and I’m a loyal Hackaday reader, and I know Disney is a multi-billionaire corporation that won’t be hurt by this, BUT AS AN ARTIST your use of Beggar Jafar from Aladdin in the header picture, without attribution or permission, does not sit right with me.
That’s not Jafar, it’s Julian Assange. :-)
IT IS FALSE AND DEFAMATORY to suggest that Julian Assange has now, or ever, taken an obsessive interest in Arabian relics locked within secret caves.
My first thought when I saw this article and I am not an artist.
I wondered why he looked familiar…
I’m pretty sure I worked with that guy in the 70s.
You’re much too uptight, friend. I don’t think Jafar had an affinity for China-surplus component reels, as the unnamed fellow above does. Welcome to remix culture – where your dank memes will adapt to service us.
+1
A culture free to appropriate is richer
A culture that drives creators into poverty runs out of sources to “appropriate” from.
Clearly Not Jafars alter ego beggar. This poor bastard sold his gold tooth to buy more electronics. The lack of dark circles around the eyes indicate that depicted caricature has gotten required sleep and didnt spend all night troubleshooting some psychotic device which was cooked up in in a similar frenzy several nights before. So its not Jafar and clearly unbelievable. Lack of hooked nose and inclusion component reel with parts flying off also differentiate.
That seems like a fair objection.
REallly? on hackday you get these kind of comment?
at least on torrentfreak you know they are trolls but here?
Also it’s been modified (pretty he wasn’t holding a roll of smd in the movie…)
A really informative and useful article, I’m really happy to see you writing for Hackaday now!
I never thought that solder could go bad. I’m still using up the solder that my dad left me. I think he got from a job that he worked at in the mid-1970s. It still works fine. I only do through hole soldering though.
It’s a good point. I think the resin can dry out, but I also think it takes a long time. As a kid, I had to buy solder in small quantities, but then I found some good deals on rolls. One did fail, but it seemed at the time to be mislabelled, or maybe was the wrong mix (I can’t remember which). I did have a “large” roll, nice and thin diameter, and that lasted about 30 years, until it ran out. A new roll started about 5 years back, that one may survive me, except it’s too thick.
Michael
>> “In the intervening two decades”
This is why I love Hackaday… An entirely new implementation of the ‘Decade Counter’…
+1
You’re much too uptight, friend. I don’t think Jafar had an affinity for China-surplus component reels, as the unnamed fellow above does. Welcome to remix culture – where your dank memes will adapt to service us.
That would possibly explain my dislike of my batch of old vero board that is almost impossible to solder to …..
Have you tried cleaning it in any way?
Still slowly working through 2000 5mm red LEDs from the ’80’s that reached the end of their shelf life in 1991, according to the bag…
A 10x10x20 led cube?
Crap is the stuff you throw away, while stuff is the crap you keep… I call it inventory.
Thanks! I now have a new term to use with the Mrs. for the excess crap… er INVENTORY in the garage.
Regarding solder wire: I used for many years my father’s spool with no problem – – actually it could solder perfectly a board that still had photoresist on! On the other hand I’m having a lot of troubles with new spools, even not cheap ones…
Just cureous:
For hobby it might be usefull to buy separate solder balls and flux, for long term storage, and mix a bit just before application.
Has anybody tried this?
Great article. Thank you!
My electronics instructor told us to use the eraser from a #2 pencil to remove oxidation from copper tracks. I haven’t had to use that trick for a while but I remember it working when I tried it last.
HOORAY!
My hat off to Ted… this is the only HaD article I’ve read where the author has not only watched the linked video, but also tells you how long it is and where to skip to to get to the good part!