Since 1951, NASA (known in those pre-space days as NACA) and the United States Air Force have used the “X” designation for experimental aircraft that push technological boundaries. The best known of these vehicles, such as the X-1 and X-15, were used to study flight at extreme altitude and speed. Several fighter jets got their start as X-planes over the decades, and a number of hypersonic scramjet vehicles have flown under the banner. As such, the X-planes are often thought of as the epitome of speed and maneuverability.
So the X-57 Maxwell, NASA’s first piloted X-plane in two decades, might seem like something of a departure from the blistering performance of its predecessors. It’s not going to fly very fast, it won’t be making any high-G turns, and it certainly won’t be clawing its way through the upper atmosphere. The crew’s flight gear won’t even be anything more exotic than a polo and a pair of shorts. As far as cutting-edge experimental aircraft go, the X-57 is about as laid back as it gets.
But like previous X-planes, the Maxwell will one day be looked back on as a technological milestone of its own. Just as the X-1 helped usher in the era of supersonic flight, the X-57 has been developed so engineers can better understand the unique challenges of piloted electric aircraft. Before they can operate in the public airspace, the performance characteristics and limitations of electric planes must be explored in real-world scenarios. The experiments performed with the X-57 will help guide certification programs and government rule making that needs to be in place before such aircraft can operate on a large scale.
The Case for Electric Flight
To be clear, the commercial jetliner is in no danger of being replaced by an all-electric aircraft anytime soon. It would take a considerable breakthrough in energy storage, perhaps based on a whole new battery chemistry, to make such a plane viable even for domestic flights. It will be exceedingly difficult for electric motors to compete against modern turbofan engines, which have themselves seen a number of improvements over the decades to maximize power and fuel efficiency.
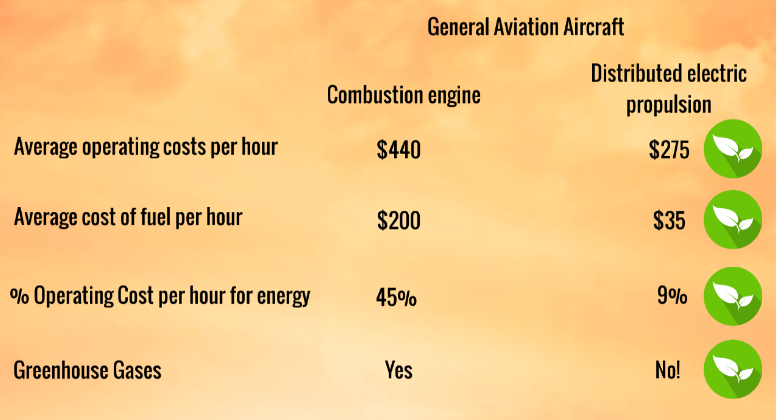
But that doesn’t mean there aren’t niches that electric aircraft could fill. Short flights with rapid turnaround times would be ideal for an electrically driven plane, especially if battery packs could be quickly swapped out upon landing.
If the packs can be charged via on-site renewable sources like wind or solar, it would even be possible to perform these flights with zero emissions. This would represent a considerable improvement over the relatively inefficient internal combustion engines which are generally used on the small aircraft that perform these short “hops” today.
Even if we ignore the potential environmental impact of using electric motors on aircraft, there are other compelling advantages. An electric plane will be quieter than its piston or turbine driven peers, and will be much less complex to maintain and operate safely. They would be particularly attractive to private owners, as they should be far cheaper to fly than traditionally powered aircraft.
Divide and Conquer
Unlike the more daring X-planes of the past, the X-57 actually got its start as a commercially available aircraft. Specifically a twin-engine Tecnam P2006T, which is notable for being one of the lightest weight planes in its class. Even when you factor in the cost of the modifications NASA has made, the sticker price of slightly less than $500,000 USD for a stock P2006T likely makes this one of the least expensive vehicles to ever carry an X designation.
As NASA sees electric aircraft as being well suited for so-called “General Aviation” flights, it makes sense they would want to base their experimental craft on an existing design that serves this market. Why go through the time and expense of developing a whole new aircraft when all you really want to test is the propulsion system?
To that end, NASA has replaced the original wing and engines of the Tecnam P2006T with what they are calling a “Distributed Electric Propulsion” system. Owing to the fact that the electric motors are less powerful than the original combustion engines they are replacing, it takes fourteen of them to propel the X-57 during takeoff and landing. But once the plane is in the air and at cruising altitude, the twelve motors in the center will shut down to save energy.
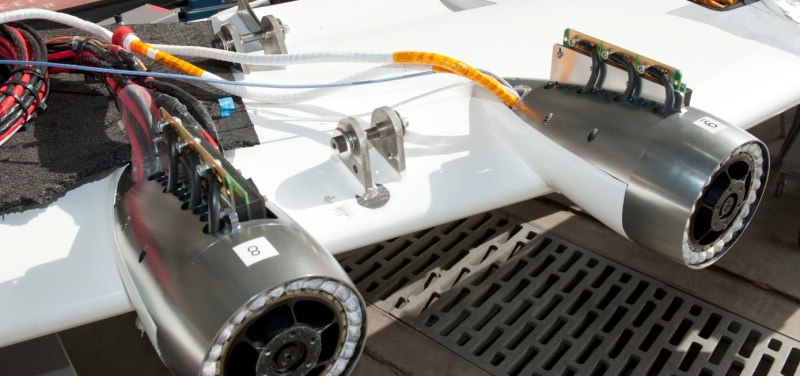
The center motors will use folding centrifugal propellers, so that once they are no longer rotating, they will lay flat against their nacelles to reduce drag. When additional power is needed, they will extend as the motors are spun back up. This arrangement is far less complex than the feathering mechanism traditionally used in multi-engine aircraft, and has the added benefit of being completely automatic. As long as the joints are regularly lubricated, physics can be relied on to take care of the rest.
When active, these small motors will dramatically increase the amount of airflow over the wing, which in turn increases lift. This boosted performance has allowed NASA to greatly slim down the plane’s wings, while the relatively low weight of the large electric motors allowed them to be placed at the wingtips. With all of these elements are combined, the X-57 is unlike anything that’s ever flown before.
Some Assembly Required
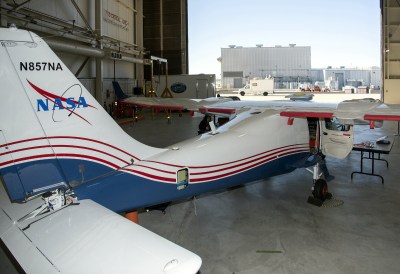
There’s still quite a bit of work to be done before the X-57 takes to the air under all fourteen electric motors. Presently, the project is at the “Mod II” stage, which is where the original Rotax 912S3 engines have been replaced with the same motors that will eventually be relocated to the tips of the new wing. The wing itself has recently completed its structural testing, and once it has been installed on the X-57 aircraft, the program will officially be in its third stage.
The final stage, “Mod IV”, will see the installation of the twelve smaller motors along the leading edge of the newly installed wing. At each stage it’s expected the efficiency of the aircraft will be increased, and ultimately NASA hopes to demonstrate a five-fold reduction in the energy necessary to operate this type of light aircraft. While the agency’s response to COVID-19 has slowed or halted several major projects, NASA says work on the X-57 Maxwell is continuing in California, and that flight tests with the plane in its final configuration are still expected before the end of the year.
i want an electric ultralight
Probable cheapest path is one of these https://en.wikipedia.org/wiki/Colomban_Cri-cri with two Honda Civic hybrid motors.
Already been done ! https://en.wikipedia.org/wiki/Electravia#MC15E_Cri-Cri
“Already been done” as though anything should only be done once. RW’s comment was an aid to Greg, not a novel new transport system.
You can build one yourself. See (for a not well designed example) for instance: https://www.youtube.com/watch?v=KidFSfdb8t8&list=PLAIipq7EZswtld3d8ttKQWQDFLS_e9tNu
High power brushless motors and motor controllers are now readily available for purchase, as are high capacity Lithium batteries.
Sorry, I won’t be the test pilot of this plane!
wondering if you meant this video instead:
https://www.youtube.com/watch?v=N6CS-YJ3_VU&list=PLAIipq7EZswtld3d8ttKQWQDFLS_e9tNu&index=7
https://www.youtube.com/watch?v=eNSN6qet1kE
or this one: https://www.youtube.com/watch?v=fMVHcmYJ7mc
All in good fun. You could do safer things…but why?
https://www.pipistrel-aircraft.com/aircraft/electric-flight/alpha-electro/ Done.
Neat idea, but electrics generally have a dismal range, Pathfinder/Centurian and Solar Impulse notwithstanding. Now, if a practical Aluminum-Air battery could be developed, that would be a game changer!
For any project, one got to start somewhere.
Though, isn’t a total of 14 props a bit many, why not start at a more traditional design?
Also, why not build a hybrid system?
Ie use a high efficiency generator on board together with the batteries. (Something of this sort could also be used as backup in case one were to run out of battery power or the like.) Also, a generator could fix the whole NOx issues of jet engines. (since we can have a catalytic converter, not to mention running cooler to start with.)
Covering the aircraft in solar panels could provide some range extension during day time flight. (since we likely fly above most clouds, then cloudy days shouldn’t be a major issue. Though, obviously we shouldn’t only have solar, batteries should be the main source of power, if not a generator.)
The only “tradition” about the number of propellers is that they must supply sufficient lift to fly the plane.
Your generator will increase the weight of the plane to the point where it’s not gonna fly.
Well of course we shouldn’t put in a standard chunky brick of a industrial generator.
That would obviously not be practical.
We would need to use something with a more light weight design. And in terms of the electrical conversion side of things. There we don’t need to aim for the standard 50/60 Hz output, airplanes already use 400 Hz since it greatly reduces the side of the generator. And we can always increase that frequency, not to mention rectify it since we don’t really need the AC output either. (we already use batteries, so the motors are likely brushless DC ones.)
Though, the idea with the generator isn’t really to be the primary source of power, but rather an additional and as a backup. Since redundancy is nice to have at times.
There are motor-generators that can quickly change. That is how you get regenerative breaking on EV cars. I believe there has already been at least 1 prototype hybrid airplan recently. As for this plane, using a flying plane to start with was an economic decision. Pusher props are much more efficient, as are ducted fans and there must be more powerful electric motos so they dont need 12-14. That is just inefficient weight use.
It does seem odd to have so many motors. OTOH they are NASA! They pretty much know what they’re doing, aeronautics-wise. If you know better than they do, you should probably be working for them.
Maybe the extra motors spread the acceleration forces along the wing better, leading to a lighter wing? And the article mentions, it increases airflow over the whole wing surface, making it smaller. I would imagine lightness is #1 consideration, since they’re bragging about fuel efficiency, and batteries still can’t compete with chemical fuel for energy content. This is intended to be a short-hop lightweight slow aircraft, far as I can see. As well as a testbed.
Maybe the production models will have fewer engines. They’re nice to have as backup though.
It’s a problem navies solve with steam catapults, it takes more power to take off than to cruise.
My bet is they just used excel to find out what config gives them best thrust to weight ratio with enough power for safe margins of operations. Remember those engines replace two Rotax 912 so engines that generate 100hp each, they don’t need power, they need weight savings for bigger batteries.
Rolls Royce have just announced that they are pulling out of Electric propulsion studies with Siemens, however as part of the project they did create a keg-sized 2.5MW generator. It was going to use a BAe-146 airliner as a testbed, which reminds me of the old joke.
Why as the BAe-146 got 4 engines Ans: Because there was not room to fit 6
https://www.theregister.co.uk/2020/04/27/airbus_rolls_hybrid_plane_grounded/
Did you not read the article before commenting? It explains why there are 14 props, and what happens with 12 of them during flight.
tl;dr
they generate electricity to run the other 2 props?
B^)
The wing area on the Tecnam P2006 (originally) is 14.75 m^2. You’ll probably lose about 3 to 4 m^2 of that from movable surfaces like flaps and ailerons, and wing leading edge that is too curved to place cells. With 10 m^2 of area for cells, that’s about 2kw, at best. Since you’ll likely not be flying at the equator the sun probably has a bit of an angle and you lose even more power. Solar cells might help, but not all that much. The downsides, they’re probably a pain in maintenance, add another 20 kg (absolute minimum) in weight for the cells, then another few Kgs for the cables and charge controller and the cells and their electronics are a fire risk.
Yes, it will likely be a gimmick the majority of the time.
It would likely be a fairly minor range extension to say the least. Likely more efficient to go for better aerodynamics and a more efficient power train to start with.
It’s something I’d fit if I was Mad Max and I came acros ths plane and some panels in a barn. But yeah since it needs airstrips to take off and land at anyway, might as well plug in while you’re there.
Now I’m wondering about fitting a nuclear reactor to a Jumbo! NASA planned that in the ’50s, with the idea that you just wouldn’t fly over anywhere populated.
They flew a plane with a reactor on board. The verdict: you can’t put enough shielding in a plane to have a sufficiently large generator be safe for the crew and still be able to fly. During the height of the cold war, a plane that could stay aloft indefinitely was definitely appealing, so they spent a fair amount of time and money investigating the problem.
Unfortunately, the nature of fission is such that technology is unlikely to change the verdict; you need a sufficient mass of fissionables, and you need a certain mass of shielding to deal with the byproducts of that fission, and those values don’t allow a nuclear reactor to power its own lift.
(It also probably wouldn’t be economical, as with the NS Savannah, but economical was never a concern for military avionics research in the Cold War.)
Wasn’t there a mini reactor powering the space laser project?
The Convair NB-36H is an example of a nuclear power air plane.
https://en.wikipedia.org/wiki/Convair_NB-36H
It made a total of 47 flight tests, some of them with an operational reactor in the back.
It also had sufficient shielding to not be a danger to its crew.
Though, there were “a risk of radioactive contamination in the event of an accident.”
It were a bomber by the way, so shooting the thing down might be something a defending force thinks twice about doing….
All the nuclear aircraft designs were flawed thinking and absolutely disgusting and really risky concepts. The paradigm of thinking that I’ve thought about before absolutely for now decades to power what I think would be totally USAF pimp… is a aircraft aircraft carrier that is like a drone with redundant propulsion systems and redundant power plant modules. Basically a huge electric motor driven system powered by an thermonuclear electric power plant.
Maybe like this design: https://hackaday.com/2019/08/28/kilopower-nasas-offworld-nuclear-reactor/
I still think external combustion is the best design so like worse case scenario we develop more improvements in external combustion and have crappy air performance vs like a hydrogen helium performance. Not sure what else would be phase change readily always available. Albeit, my vision has matured over the years and for aircraft… seems like just a lightweight ejectable with it’s own parachute and dampened system thermonuclear electric power plant.
Seems like a no brainer compared to the history of nuclear disgust and the need for the operations and systems to develop into more efficient, healthy and safe implements… no way ever consumed or even on our body. Like highly quarantined and secured… like no one is going to want to make crank with the batteries.
Just have to have an attitude like the “Father of the Nuclear Navy,” a.k.a. “The Kindly Old Gentleman,” or simply “KOG” to get the gears turning.
https://en.wikipedia.org/wiki/Hyman_G._Rickover
Nuclear vehicles have even been proposed including trains and are successfully used throughout the World by certain standard, regular and orderly skilled. Time to clean up the bad acts and their waste.
Solar cells would prove their worth for the casual flier that has his plane parked on the ramp all week. Slowly charge it up over a few days, then do few circuits around the pattern, practicing touch and go aproaches. Repeat. It won’t keep you current on cross country IFR flight, but many of those skills can be exercised from the comfort of your own flight sim.
I would imagine plugging it in for a week would cost a few dollars. and save on weight from having solar panels and voltage converters on board. Even fields that don’t have a tower will have electricity. especially if there is storage on sight.
FWIW pilots need to practice radio skills in the sim a LOT more than they need the flight experience. most people are pretty terrible at it, and bad things happen in the busy airspace over my house.
The article doesn’t make this as clear as I think it should: the entire point of this design is that the complete length of the airfoil has props blowing air over it. This gives it the performance of something with slats and slotted flaps, in half the wing area, and also may provide rapid adjustment of local airflow to manage localized stalling. AIrcraft carry all this hardware along to increase their stall/cruise ratio. This does the same thing in a completely different way, while also decreasing weight and drag. The batteries more than soak up the weight improvements, but it’s an x-plane. I was a little surprised to see how much less electric motors weigh than turbines for the same power, because I’m used to how much lighter turbines are than reciprocating piston engines for the same power.
Well, that is indeed a logical improvement. The article itself didn’t really mention that all that clearly.
The whole concept of the props folding back during flight to decrease air resistance seems like icing on the cake compared to removing the need for slats and flaps.
And yes, brushless DC motors are rather incredible how energy dense they can be.
My thoughts exactly. Modern wing design is littered with a hundred years worth of compromises.
A wing needs to be efficient at cruse speeds (narrow), At take off and landing, wing needs to have lift at low speeds (wide). A wing needs to be efficient, but also has to handle large variations in angle of attack. An aircraft needs a short takeoff and landing (slow speed, large wings). An aircraft needs to be relatively immune to the effects of gusts (a high wing loading, fast airspeed, small area wings) .
All of these compromises can be thrown out if we can design a wing for one airspeed and one angle of attack. That is what the X57 is attempting to do. With a whole wing distributed propulsion system, we can produce a constant airspeed and angle of attach as far as the wing is concerned, independent of that of the aircraft.
The benefits : an optimized wing, narrower, lighter, less drag, better lift, stall proof, high wing loading (less bumpy flight) and short take off and landing, as aircraft speed, and wing airspeed are decoupled.
Another benefit is the inherent redundancy, which is easier with electric motors, the tight control and massive reliability of electric motors make it safe to move them to the outer edges of the wings. The outer motors rotate in a direction that allows the prop wash to reduce the wing tip vortex. (no winglets needed)
The one drawback, mitigated to an extent by redundancy, is the propulsion system become an integral part of the wing. If all the motors stop, your chances of a safe landing comes close to 0.
If we accept functioning motors as part of the wing, then we might as well discard the rudder too , as the motors can provide the yaw function.
A final benefit of electrical, whether distributed or not, is the reduced coupling of instant power and weight. The power requirements of aircraft engine varies massively. At take off you need lots of power as you gain altitude (potential energy = mgh). At cruse you need a lot less power, less power, but with a reciprocating internal combustion engine, you are still carrying that heavy engine. In electrical systems the weight is in the batteries, so the additional power a motor can deliver, adds little to total weight.
However, you also don’t get lighter as you fly. Get a gear problem, and fly around until the gauge is on empty, but you’re still bringing all that weight down with you.
I’m envisioning ejecting the pack over a non-populated area…maybe with a parachute? Maybe…?
You could, but then you’re instantly left without power which makes landing a one-shot attempt.
Also, think about it for a second: first you need to find the non-populated area, dump your battery pack, then fly to the airfield without power… not to mention what happens when literally a ton of lithium batteries hits the ground. Don’t do it in bushfire season.
There are better options than batteries – fuel cells come to mind. Even lithium-air batteries are technically a dumb idea for an airplane because they pick up oxygen from the air when they discharge, which actually makes them heavier as you go.
just put some wind turbines on the plane to generate its own electricity whilst flying ;)
Wind powered aircraft are a thing… this is how they work.. https://en.wikipedia.org/wiki/Ridge_lift
The fuel costs are high. A 2-4 person aircraft burns 8 to 15 gallons of gas per hour at $6 per gallon. To be practical any aircraft must provide at least half an hour of excess range beyond computed fuel use to destination airport.
Agreed, particularly since the base airframe is pretty efficient, seems to do near 20mpg or about 7.5 gallons an hour, and it will do it on 92 octane pump gas not avgas, at ~ $4.50 a gallon (Probably cheaper in most of US)
That $200 number seems a bit high for even the neolithic ’40s design Lycomings and Continentals that have 7 or 8 to 1 compression ratios. Someone got an automotive LS-1 approved (With modifications) for an owner maintained aircraft, not a particularly sleek one, and said with that, that while the power doubled, the fuel consumption halved, and I think he claimed 6 gallons an hour, so 12 was as thirsty as the old eggbeater.
Anyway, gallons per hour is a bit of a stupid metric for an aircraft you want to get somewhere in, if you just want to hang around, get a hotair balloon. So prolly trying to sell these to police agencies for civil surveillance or something.
aren’t the old aicraft engines actually high compression? Why else would they need high octane gas?
btw modern turbo diesels should not be ignored in aicraft, quite a few of them, even new designs use them. Apart the better efficiency, they can also be made to run on kerosene.
AVGAS isn’t about “high octane.” It’s about lead.
https://www.faa.gov/about/initiatives/avgas/
The lead is the primary reason AVGAS is so expensive – transportation, it cannot be shipped by pipeline and must be trucked from refinery to airfield.
The reason the lead is in there is get the octane up over 100 to allow high compression engines
thats not the whole story. AVGAS is more expensive because it has a completely different distribution network and system. it must be filtered every time is moved of container, must be stored in containers out of the ground and containers have a different design, etc etc.
plus, while auto fuel changes for season and location. AVGAS is always the same everywhere and everytime. also tends to be produced in fewer refineries and in smaller quantities.
Aircraft with reciprocating piston engines use 100LL, which is 100 octane. The “LL” stands for “low lead” which compared to what came before, is true, but they still have a _lot_ of lead in them. They run 100 octane not because they’re high compression (the most common aircraft engine, the lycoming io-360, typically has 8.5:1 compression) but because they’re old, poorly optimized designs that need all the octane they can get to keep from detonation, because they have manual user control over rich/lean fuel ratio as their altitude variation during a flight is so great that mixture control is necessary (and since it’s manual you can totally screw it up and blow up your engine) so it’s safer to provide some extra octane to reduce the tendency to blow up engines, and because people have learned that running slightly lean gives better range for the amount of fuel burnt, which requires higher octane.
The high octane/lean burn/longer range relationship was found experimentally by Charles Lindbergh and was the reason the Doolittle raid on Japan in 1942 worked. The US made by far the best aviation gasoline in WWII specifically to give aircraft almost double the range that anyone else expected: everyone in the world had a jaw-drop moment when they saw the range of US bombers, because of high octane in low-compression engines.
actually, plenty lycosauri can run on unleaded fuel. only problem is that for certified airplanes you need a STC for both engine and airframe and many airframe manufacturers cant be arsed to provide STC’s for MOGAS.
in experimental aviation, where there no such requirements, automotive fuel is very common.
> aren’t the old aicraft engines actually high compression?
No, they actually have a fairly low compression ratio compared to automotive engines.
> Why else would they need high octane gas?
Because airplane engines vary their mixture ratio and can get into lean detonation fairly easy. High octane fuel also gives an extra margin of safety. Don’t want your engine to get into detonation during flight, it could be your last.
“So prolly trying to sell these to police agencies for civil surveillance or something.”
They’re not trying to sell these to anyone.
They’re trying to sell the public on the concept.
B^)
It’s a layered sell, “look at us, we’re proving concepts of possible profitable relevance to the US airspace industry, it’s tax money well spent” They did so much more of that when they were NACA, seems like they forgot for 50+ years.
The comments ignore the key feature of the design that is not readily addressed by existing IC engines.
The additional motors provide higher, stable, lift to produced when needed, e.g. TO & landing by maintaining high velocity attached airflow over the section when the aircraft slows. This permits a smaller high aspect planform for cruise with a significant resultant drag reduction.
Sounds like Taurus Electro G2 on steroids. https://www.youtube.com/watch?v=rqDvGy3dExQ
thanks engatled, i didn’t understand at all until i read your comment
You’re welcome ;-)
isn’t that what some military aircrafts do with bleed air from the engines? and afaik it is not allowed on commercial aircrafts because relies on the engines
Commercial aircraft do the same thing with slotted flaps: narrow openings that let a little of the high pressure air from under the wing through to energize the boundary layer and delay stall on the top surface of the flaps. Blown flaps using bleed air from the turbines (or in early versions, from piston-engine-driven blowers, as on the German BF109 in WWII) were really popular for a while when people wanted the absolute most speed so specified the smallest wings, but fell out of favor in the 1970’s because they’re complicated, heavy, hard to maintain, and it’s easier to just put bigger engines in and land at a higher angle of attack. (Gross oversimplification there, but generally accurate as far as I know.)
And in addition to weight and maintenance it makes losing and engine an even bigger problem than it already is
This is my main concern about this whole idea: the lift depends on maintaining a high airspeed, which depends on power. What happens when you have either a catastrophic failure of the electrical system or just run out of power when you run into unexpected bad weather and have to fly around looking for a place to land? Out of power means high landing speed and long landing roll.
Should have said “high airflow over the wing” rather than “high airspeed”.
See, I knew there’d be a reason!
Let’s hope they are better at designing planes than they are at designing web pages. That site is truly un-readable.
Right. Looks like an undergrad presentation, but with less substance.
It also bothers me how low-level their materials are. I clicked on the “X-57 Physics” video. Not a single number (otber than “twelve”) in the whole video. How can you call something “physics” without using numbers? Useless, and in my opinion, condescending. They seem to have a “you wouldn’t understand – it’s science” attitude.
If it takes 14 props to take off but only two to cruise why don’t they launch it off the runway like on an aircraft carrier?
Yes, we just need more civilian nuclear powered steam catapults.
I think glider winches prolly work better for gaining altitude though.
They’ve been implementing Electromagnetic Aircraft Launching Systems (EMALS) on the new carriers since the USS Gerald R. Ford was launched in 2017. ¡¡News Flash!! Trump doesn’t like the EMALS – he wants the Navy going back to blowing steam. (Insert political comments here)
No, please don’t.
Bungee cords stretched on a bumper hitch.
Seems like for launching rockets also there’s the benefit of requiring less surface area of useless production… only for luxury for the most part. Man, imagine… back in the day the runways were “eco-friendly” or maybe not quite “carbon neutral” or whatever the term they use.
FWIW, DARPA had a similar program. Article with more information.
A lot of the comments have missed the point, that an X-plane is EXPERIMENTAL, not a prototype. NASA don’t do prototypes, they do research to test and develop new principals. For a real prototype have a look at Harbour Air’s Electrice DHC-2, designed for short-hop taxi service around Vancouver: https://www.flightglobal.com/airlines/harbour-air-flies-first-all-electric-commercial-aircraft-a-dhc-2-beaver/135711.article
12 extra motors just for take off? Then what, they’re just extra weight and complexity? Electric motors can pack a much torquier punch in a smaller package than any combustion engine, so… why not just upgrade the two large motors if the problem is take off power?
I would understand if they were meant for failsafe reasons, but the excuse that the two electric motors aren’t powerful enough doesn’t hold water.
We’ve been making electrics R/C planes for a couple decades now with amazing performance characteristics. I can understand that doesn’t necessarily scale up, but I would expect the design to at least be somewhat similar.
Normal wings are designed for a large variety of situations, with 12 motors the wing performance can be maintained by using the motors to vary the air flow over the wing. This allows the wing to be optimized for cruising, which is mostly what the aircraft does.
The reason why electric R/C planes are so performant is because they have better thrust/weight ratios than your standard airplane. That’s why you can see people make ridiculous foam core models that fly. It doesn’t scale up.
Read the comments above about the 12 smaller motors being used to create more lift on takeoff. I’d guess NASA will find out pretty early if the idea works as it should. ¯\_(ツ)_/¯
I see articles like this and realize why the US hasn’t had a manned space flight in 9 years now, It seems that every US agency has to be duplicating every project being done be other agencies and private businesses. Maybe NASA should be concentrating on space flight and let the FAA take the lead on aircraft and loan expertise when its needed, same with climate science, let NOAA Lead the earth science stuff and just help when needed. Maybe if some of these agencies were trying to do fewer things then they would do their core missions better and maybe one of them (NASA or FAA) might of noticed just how dysfunctional Boeing has become of late in r&d.
You do know “NASA” is an acronym for National *Aeronautics* and Space Administration? They have done aviation research since before they were NASA. Check out their many research subjects on aircraft crash survivability, autopilots, the Rutan designed scissors wing AD-10, and so many more. The FAA? They regulate aviation, they don’t research it. Note which agency funded the US$10 million Green Flight Challenge (via cafefoundation.org).
I do realize what NASA stands for, but why should they still be doing it? As you said the FAA regulates aviation and when accidents happen they not NASA investigate and hey they do have there own fairly large research division, not only that but hey look at that the FAA also holds the office of commercial space transport, you would think NASA would be the better candidate for that but I guess they are to busy researching coral beds, building covid 19 ventilators, and electric planes to worry about actual space stuff. The 70’s through now have turned most US agencies into pork barrel money pits that have strayed so far from their core missions that they no longer function well. The house no longer just needs a cleaning, it needs to be rebuilt from the ground up…..
All good points. I’d like to mention that there is a lot of overlap between agencies (accident investigation by the NTSB as well, for example). And pork is endemic as you mention. But compared to the billions spent in Space, the amount NASA spends on Aeronautics is a drop in the bucket. Clearing the deadwood would save far more than having to reinvest in recreating everything from scratch.
I’m just glad for the tremendous innovation that happens in the rest of the country and world! Aviation has come a long way since I earned my pilot license 48 years ago!
They’re already build diesel-electric tiltwing prototype:
https://en.wikipedia.org/wiki/NASA_GL-10_Greased_Lightning
There are as well a lot commercial lightweight Diesel engine which can be used as generator.
https://en.wikipedia.org/wiki/Category:Aircraft_diesel_engines
And of course modern Stirling engine, microturbine and Wankel engine.
So it’s not impossible.
It just struck me that if they were ‘catapulted’ into the air, that would save a *LOT* of onboard energy.
It just struck me that if they were ‘catapulted’ into the air, that would save a *LOT* of onboard energy.