It’s one of the enduring images of a humanitarian aid mobilization: military transport planes lined up on runways, ready to receive pallets of every conceivable supply. The cardboard boxes on those shrink-wrapped pallets are filled with everything from baby formula to drinking water, and will join crates filled with the tools and materials needed to shelter, clothe, feed, and heal people in places where civilization has suddenly come into short supply thanks to a disaster, sometimes natural, but often man-made.
What if it didn’t need to be that way? What if, instead of flight after flight of supplies sent in to help rebuild, perhaps just one flight was needed, one stuffed with the tools of our trade: 3D-printers, Arduinos, electronic components, machine tools, and the experts to use them. It certainly wouldn’t make up for the short-term need for food and water, but importing the ability to manufacture the items needed locally would go a long way to repairing infrastructure in the disaster area.
Rethinking disaster response is the core mission of Field Ready, one of the groups we’ve partnered with for the 2020 Hackaday Prize. By way of introduction to this non-profit with a potentially world-changing mission, and to help those who are participating in the 2020 Hackaday Prize challenges, here’s a little bit about Field Ready — what they do, how they see digital manufacturing fitting into their mission, and where they’re going in the future.
Supply Threads
If the first half of 2020 has taught us anything, it’s that this world lives and dies by supply chains. The term “chain” is perhaps a bit oxymoronic, as it implies strength and stability. But as we’ve all learned, our supply chains are more like threads, easily broken and difficult to mend. The globally distributed supply chain that giveth inexpensive goods en masse can also taketh them away, especially in disaster zones.
It was with these bottlenecks in mind that Field Ready was conceived by Eric James, Dara Dotz, and Nick Haan in 2012. Their idea was to transform the logistics of disaster relief using the power of flexible manufacturing to essentially bring a “build anything” factory to the disaster. Since incorporating and receiving their non-profit status in 2014, they’ve tested their system with field responses to a wide range of humanitarian crises, starting with the 2015 earthquakes in Nepal.
After assessing the ravaged country’s needs, Field Ready helped start up a digital manufacturing lab in Kathmandu to manufacture whatever was needed by the host of aid agencies that flooded into the disaster area. The medical instruments and repair parts that the lab created could have been ordered, but with roads knocked out by the quakes and supply lines frayed, making them on-site was quicker and easier. In 2016, Field Ready made over 5,000 items. In addition, they trained over 600 people how to run the machines in the lab, leaving Nepal with the capacity to continue rebuilding, not to mention leaving them well-positioned to respond to the current COVID-19 crisis by building their own PPE.
The ongoing civil war in Syria provided another chance for Field Ready to innovate. Rescue and recovery operations from buildings collapsed by rockets and artillery are often helped by the use of lifting bags, sturdy flexible bladders that expand when inflated with high-pressure air. Lifting bags can lift the tremendous weight of concrete slabs and steel beams, but they were in short supply in the war-torn nation, so Field Ready created a means to manufacture the airbags from locally sourced materials. They’ve made over 100 bags and distributed them widely; the tools have helped save the lives of seven people so far, and what’s more, the design is freely available, so anyone can build a bag and save a life.
The Open Challenges
The Open Challenges of the 2020 Hackaday Prize invite anyone to enter with their ideas for addressing the topics outline by our four non-profit partners. The challenges are based on needs they’ve identified through their work in the field, and designs that address these needs have the potential to make a huge impact on their life-saving efforts and the disaster response efforts of other NGOs. Field Ready has a few highly focused devices in mind.
The first challenge is to produce a reliable, low-cost infusion fluid warmer. Under the best of conditions, medical treatment that involves infusion of fluids is anything but trivial. Intravenous therapy always requires sterile supplies and procedures, which can be difficult to obtain in disaster scenarios, and the venipuncture itself is invasive and prone to infection. But one of the lesser-known risks of infusion therapy is inducing hypothermia by not properly warming the infusion fluids.
To avoid the risk a patient faces when getting a large bolus of cold fluid, fluid warmers are routinely used. By warming the fluid in a controlled and reliable way to nearly body temperature, the risk of hypothermia and bursting of red blood cells, or hemolysis, can be averted. The trouble is, commercial fluid warmers are expensive and hard to come by in austere clinical conditions. The challenge seeks to rectify this with a design for a fluid warmer that can be assembled from readily available parts. Above all, the fluid warmer needs to be designed with safety in mind and with an eye to making it easy to construct by responders who likely will not have experience building medical devices.
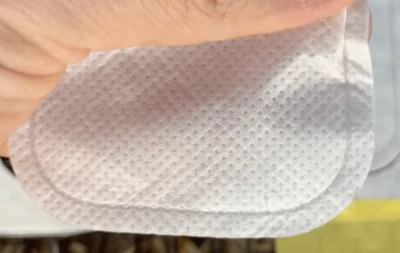
Another device in the Open Challenge is a heat sealer and plastic welder. Such a device has plenty of applications in the medical response space, from sealing sample bags to rapidly creating isolation gowns. We’ve seen hospitals the world over struggle with the latter over the last few months as stockpiles of PPE have dwindled. In a disaster situation, effective PPE could be vanishingly scarce. A heat sealer that could be used as a welder for synthetic textiles like Tyvek and spun polypropylene could allow responders to make isolation gowns, eye shields, and even face masks far faster than they can be printed or sewn.
The final device in Field Ready’s Open Challenge is for a versatile UV wand for curing adhesives. The range of UV-curable resins is vast, covering applications from semiconductor manufacturing to artificial fingernails. In disaster response, the ability to leverage these versatile adhesives is often thwarted by the expense of the UV curing stations needed to cross-link the uncured resin. Anyone accepting this challenge will need to design something that emits UV-A light at levels needed to cure resins, do it from easily sourced materials, and make it versatile enough to fit into many different manufacturing processes.
The Dream Team Challenge
When it comes to tracking products and assuring that customers are getting what they pay for, traditional manufacturers with centralized operations have extensive quality control and quality assurance programs in place. Many manufacturers keep track of products through lot numbers and serial numbers; testing of random samples of a product, designed to elicit any flaws in the manufacturing or assembly process before the product gets to a customer, is a common practice too.
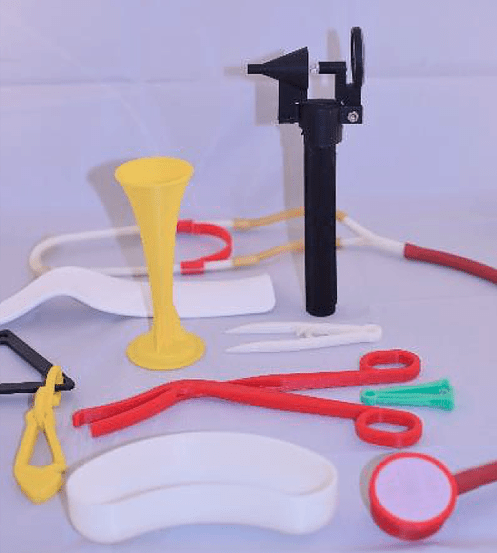
But for the decentralized manufacturing model that Field Ready applies to its disaster response efforts, traditional QA methods need not apply. Parts often go directly from the bed of a 3D-printer to an end-user, without the benefit of so much as a serial number or even a logo to let people know where the widget was made. This causes problems downstream, not least of which is getting credit for the good work they’re doing. Self-promotion aside, without a label an end-user who needs more of the widget has no idea whom to contact to get another, and someone who experiences a failure of the part has no recourse. The lack of tracing can lead to waste, as Field Ready gets no feedback on what’s working in the field and what needs fixing.
Applications closed today and the selection process is under way to choose three people who will work on Field Ready’s Dream Team over the next two months. They will each receive a monthly stipend of $3,000 to work with the organization on the Dream Team Challenge that aims to fix that lack of traceability. They’re tasked with assembling a quality control system that can be used to track every part made by Field Ready during its emergency response deployments. It will present a huge challenge, since items as small as 3D-printed umbilical clamps for obstetrical use to full-size structures like portable shelters and latrines have to be tracked. Diversity of materials presents another layer of difficulty, as Field Ready uses whatever they can to build the things they need. So any logos, serial numbers, QR codes, or labels need to work with wood, metal, glass, plastic, ceramic, or any other imaginable material, and must be robust enough to last under harsh conditions. Finally, the system needs to be remotely accessible, so that Field Ready can protect their users and continuously improve their offerings.
Let’s Do This!
Whether you made it onto the Dream Team, or prefer to work on one of the Open Challenge projects, Field Ready is positioned to put your efforts to good use. The world isn’t getting any safer, and there will always be a need for someone to step in to offer a helping hand. The less stuff they have to bring with them, the better, and with your help, Field Ready is making good on that vision.
Spend some time learning about the Field Ready challenges through this video Q&A session.
[Featured images: Red Team deployment in South Sudan field printing a water pump fitting; printing medical supplies in the US Virgin Islands with vehicle-powered 3D-printer. Courtesy Field Ready]
>What if, instead of flight after flight of supplies sent in to help rebuild, perhaps just one flight was needed, one stuffed with the tools of our trade: 3D-printers, Arduinos, electronic components, machine tools, and the experts to use them.
That’s still a form of helicopter humanitarianism, and doesn’t address the point that the local people are unable to maintain such technology and tools after you leave. There’s examples abound from the solar lanterns of rural India to the wells in Africa.
You can 3D print entire houses out of concrete while 300 unemployed locals watch your machines working; you may ask why did the locals not simply cast the houses using wooden forms? Because they didn’t have the money for cement, nor a truck to carry the grit and sand. They may lack entirely the infrastructure needed to do any of that, which you bring along, so your “local manufacturing” efforts using high technology is simply the same airdropping of supplies – only in such ways that only your experts can use them.
Without addressing the underlying economic, social and political, conditions – to which you as an outsider do not have authority, moral or otherwise – you are merely putting a band-aid on the problem while you’re actually there. This simply ensures that the issue will return, and that you or someone else will return with a fresh round of donations and Arduinos soon after – time and time again – making the whole thing a form of business, really, rather than humanitarian aid. Even if you don’t think of it as such.
The tragedy of the situation is that well-meaning people get so little done, and waste so much effort and money doing it. The small scale of these efforts, and the numerous competing providers that do not collaborate or even know of each other, ensures that none of them really make much difference – and that in turn ensures that the same donation drives can be had year after year, funding aid collection agencies in the western world and providing so many with the warm feelgood of paying “non”-profit groups for a clean conscience. If ever there’s a need to justify research or projects which are not really useful or cost-effective, say it’s for humanitarian purposes – but I digress.
The real hack would be to figure out what could be done differently, using local materials, local workforce, local expertise – things like rammed earth construction, soil improvements, irrigation canals, schools, local manufacturing of tools, small scale industrial capacity reconstituted and organized to meet the emergency needs – the people usually have it all, they just aren’t able to use it because of the social confusion and disarray of the crisis situation. The successful humanitarian would not go in with an Arduino and a 3D printer, but simply a notebook and a pencil, and a skill for organizing.
And this post too will be cleaned from these comments within 2-3 weeks, if not immediately. (As if there is no wayback machine)
That is why I support engineers without borders, they don’t do overly complex things, they typically do things using as much local resources as possible and teach the locals along the way.
I remember there was once a group that was looking for educational material to teach very basic electronics engineering in the poorer places of Africa, India, and the Middle East – simple stuff like how to wire a LED to a battery for a light. Reading the web forum, I saw one person come up with a solution for constructing a precise low value resistor by folding a piece of paper blackened on one side with pencil lead.
The paper was blackened with graphite, two strips of aluminium foil placed across leaving a narrow gap of visible graphite between them, then the paper was folded perpendicular to the strips to make a thicker bar, which was then sandwiched between rigid cardboard or wood and screws were driven through the ends to clamp the foil tight to the graphite. The screws were also used as connection terminals for the wires. The value of the resistor was then adjusted by whittling down the sides.
Their problem: no tin foil. Turns out it isn’t such a common item outside of western kitchens. Couldn’t even find silvered bubblegum wraps, because guess what – people don’t chew gum. I didn’t stick around long enough to find whether they found an ersatz solution to it.
Their other idea of making a simple galvanometer out of wire and small magnets taken out of headphones also fell short on the availability of scrap headphones. It begs the question, where would they have found the batteries and the LEDs if not by importing.
I’d like to add a few things also. I used to be a firefighter at a point and one of the things I can tell you before hand is that firefighters absolutely HATE new and complex equipment. There’s a surprising amount that can be done with just a rope and some cloth that becomes more difficult when we start adding complexity. Furthermore a rope and cloth are less susceptible to failure due to water damage or high temperatures than an arduino and they do not need regular maintainence (which is a huge PITA given the equipment we already need to maintain. I’m pretty sure we do not want yet another tool which I need to constantly charge the battery for).
Engineers and Entrepreneurs also have the habbit of thinking they can fix things without understanding the existing technologies out there. In fact this is exactly the reason why Elon Musk’s submarine was never used in the Thai cave. We already have stretchers which we can roll up into our pockets and carry without a problem. We also have the technology to provide oxygen to people underwater. Hence it made far more sense for rescuers to try and use proven techniques to bring the children out rather than put them in an untested capsule that would have been difficult to deliver to them in the first place as it was pretty big compared to the small sked stretcher that could fit in a divers pocket.
Oh dear! Did you not read the article? The whole point of this exercise is TO USE LOCAL PEOPLE AND SUPPLIES! And to leave the locals with both the skills and tools to carry on themselves. Did you just cut and past this waste of time and space you posted?
Did you not understand the criticism?
Airdropping yourself into a disaster zone with high-tech “digital manufacturing” equipment still relies on expertise and supplies that cannot be locally sourced, that you have to bring along. Otherwise they would have had it already at their local college hack-lab.
It’s complete make-belief that you’re relying on local means, because in very many cases the local people cannot readily assimilate the technologies you use and cannot continue to help themselves with it after you leave.
*taking notes*
Only use parts and supplies you can find at any Walmart…
Or whatever the local dollar store is called. That’s a good principle.
In many places, you’re literally down to what you can pick up from the local dump, because there is no Walmart (anymore, because the hurricane took it…), so you may not have access to even a simple multimeter if yours stops working, let alone a replacement stepper motor for your 3D printer, or filament, or any of the multitude of “vitamins” that cannot be made on the spot.
What I mean is, okay, you’ve trained 600 people to use 3D printers and laptops to make spare parts for machines like hospital equipment – but when the 3D printer runs out of filament, they have to order that from abroad. When the laptop screen breaks, they have to order that from abroad. When the Arduino board burns out, they have to order that from abroad…
It’s a system in decay because the surrounding society cannot support it.
Why is it necessary to track umbilical cord clamps?
Why is it necessary to track 3D printed otoscope, or stethoscope?
I can understand tracking a ~$100 otoscope or stethoscope against theft, but???