As we’ve said many times in the past, the creation of custom cases and enclosures is one of the best and most obvious applications for desktop 3D printing. When armed with even an entry-level printer, your projects will never again have to suffer through the indignity of getting hot glued into a nondescript plastic box. But if you’re printing with basic PLA, you need to be careful that nothing gets too hot inside.
Which was a problem when [Oleg Vint] started work on this 3D printed case for the popular TS100 soldering iron. But with the addition of a standard 608 bearing, the case provides a safe spot for the iron to cool off before it gets buttoned back up for storage. Of course, you can also use the flip-out perch to hold the iron while you’re working.
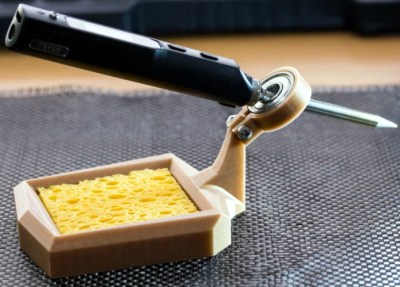
As [Oleg] explains on the Thingiverse page for the case, he actually blended a few existing projects together to arrive at the final design. Specifically, the idea of using the 608 bearing came from a printable TS100 stand originally designed in 2017 by [MightyNozzle]. Released under Creative Commons, [Oleg] was able to mash the bearing stand together with elements from several other printable TS100 cases to come up with his unique combined solution.
In a physical sense, this project is a great example of the sort of bespoke creations that are made possible by desktop 3D printing. But it’s also a testament to the incredible community that’s sprung up around this technology. While the logistics of it still could use some work, seeing hackers and makers swap and combine their designs like this is extremely inspiring.
[Thanks Arturo182]
Wonder how long it’ll go before it warps? PETG maybe?
If that’s a problem, give the bearing clamp a bit bigger ID and line it with a strip of silicone cut from a cheap baking sheet
Note that the bearing contacts the iron around the same spot where the iron contacts the plastic body of the handle. The stem of the soldering tip is not actually very hot – otherwise the soldering iron itself would melt.
Why a bearing? Seems like there’s an infinite number of better alternatives, especially since 608 bearings in single quantities tend to cost dollars at the local hardware store.
The same point could be accomplished with two large steel washers.
A bearing is kind of a good solution because the inside race and the outside race are only minimally connected at tiny points on the balls. I could imagine the conductivity between inside and outside is therefore not very high?
Steel has pretty bad thermal conductivity, and the iron is only touching it by two small points. The interface between the iron and the steel is already the limiting factor.
Plus, the bearing is packed full of grease, which will start dripping out if the bearing actually gets hot.
If only there were some easy way to hack the grease out of the bearing beforehand?
Why bother when you can just use a pair of washers?!
Or make a coil out of the old coat hanger, reuse door stop spring etc.
It doesn’t have to be a working bearing. It could be bearing that is no good anymore but is fine for this purpose.
True, but most likely you won’t have one at hand and have to buy it.
I’m willing to be that almost anyone has some old soup can or a jam jar lid in the trash they can use to cut a pair of thin steel washers faster than they’d drive to the hardware store.
If you are an advanced 3D printer user you always have a stock of 608 bearing, brass M3 thread inserts, M8 screws and washers, neodymium magnets etc.
Still you could save the 608 for the purpose you actually bought it for, or for anything that actually requires a bearing, so you don’t have to buy yet another one the next time you need it.
What people are saying here sounds to me like, “I have five one dollar bills, so I might as well blow my nose on one of them and toss it in the bin. Tissue paper? Why? I already have these dollars!”
Yah but then you wouldn’t be using PLA for something like this.
Nevermind the PLA comment. I saw someone recommended PETG so I assumed it had been printed in PLA. Then I clicked the link. Now I have to go look up what SBS is.
You don’t get outside much? Roller blades, skateboards…
You take ONE bearing out of your skate and you have to replace the lot, then it costs you $20 for the cheapest set. Could be, if you already have a bunch of old bearings laying around, but if you don’t then there’s no sense in doing this.
The “best” source that was mentioned in the articles was to re-purpose a cheap fidget spinner, but still this is going out of your way to use a part that isn’t actually suited for the purpose.
Yup. But to my experience most people will still drive to a hardware store instead of investing the time and (re)use the stuff they have lying around at home…
You guys are hell bent on going to the store.
This is an interesting topic in and of itself. Yes, I too have found that people will fixate to a known solution rather than a better solution that is more readily available.
It has lots of ironic consequences, like, did you know they sell drink can pull tabs separately in crafts stores now? Just bags full of pull tabs. What was a sort of macaroni-on-string boring sunday solution to making fun things and decorations out of waste is now “the way you’re supposed to do it”. So of course if you don’t have pull tabs, you’ll have to go out of your way to buy them.
Same thing with the 608 bearing. The first guy might have used it because they had one at hand, and the next person thinks, “Oh, that’s a necessary part.”, and then other people go to troubles rationalizing why this is so – as evidenced here – because it doesn’t make any apparent sense to use the bearing, therefore there MUST be some very good reason why it is specified.
That’s how you do cargo-cult engineering.
“True, but most likely you won’t have one at hand and have to buy it.”
I thought the idea was re-purposing something you already had laying around.
After all, if you are content with buying a part for it, you could just as easily buy a ready made case.
3D printing lets you design/adjust around a repurposed part like this in a trivial way.
I thought that the point is there are no ready-made cases exactly like this, so you have to make one.
Treat some long serving piece of hardware to a new bearing and use the old one. Saw, alternator in the car, furnace blower..
You have to start another project to complete the first, but then you have the chainsaw in pieces on the table and you STILL have to go out to buy a new bearing. That’s an example of yak shaving, and it’s still trying to force the original specification by inventing special circumstances that would MAKE it sensible.
I started thinking about the problem, and there was a Pringles can on the table in front of me, so I took the steel bottom of the can and cut it into a 1″ strip, folded it in half for rigidity, then bent a loop at one end. Much more compact than the 608 bearing.
608 bearing looks cooler than pringles can bottom and washers.
Only good reason.
I think the idea is the ball bearings have minimal contact patches and act as a heat break, preventing warping of the print over time. Washers would melt into the print quickly.
I just tried it. I took a strip of steel between my fingers and lit up my butane soldering iron. I heated the iron up to temperature, then turned it off and pressed the tip ½” away from where I was pinching the steel. It never got painful to hold, just barely warm – the soldering iron cooled down before the heat could transfer through the steel. The bearing isn’t holding the iron by the tip anyhow, so this is the worst case scenario.
To compare, I repeated the test with the gas on, and it took about 30 seconds until it started to hurt. In other words, if you keep the iron on and press it directly to the washer, it might start to melt the plastic after about a minute.
If you’re still worried, you can easily take the steel washer and cut out radial slots into it with a hacksaw, or you drill out a few holes around the disc to reduce the heat transfer area between the ID and OD. Works just the same.
At which point your time investment is considerably more than a 608 bearing.
Unless you need to go out and buy or order one in.
or I could just use a bearing, got a box full of those
And I can wipe my bottom on $1 bills. I also got a box of those.
I also have toilet paper, but hey, why use a good solution when you can use an expensive solution that doesn’t fit the purpose?
Magnets!
[quote]Your comment is awaiting moderation.
“Magnets!”[/quote]
So controversial!
Your comment was put into the mod queue by Akismet’s artificial intelligence. It knows best.
(Seriously, we’ve put in a few tickets, and been told that we may not peer inside the black box. It’s probably just cats anyway.)
I already had a 30pk of 608zz bearings that I already had on hand from Amazon for $9
It worked well, was $0.30 for me and I already had it in my spare parts box.
If you were so inclined it wouldn’t be hard to mix up the design for a pair of washers or a nut though
As compared to a cooling mini-tip, the bearing has some mass. As said, it has poor inner-race to outer race contact.
I see the can transistor heat radially-finned heat sinks as a thought. The hot tip touches just 2 tangenital spots, (whereas the inner radius would grip a transistor can with near perfect contact.) The fins would be uber exposed to air. Maybe hard to find these, in this era of micro-smd’s.
Interesting idea, if it doesn’t work well enough, replace the bearing with a ceramic type.
Minor improvement – remove the shields so as to improve the convective airflow between the races and reduce the heat transfer
The crappier fidget spinners have a dry unshielded bearing in, but I think the hole is a tad small to get most irons into.
I thought they all used dry unshielded bearings? It won’t spin properly if there’s any grease or friction from the shield.
I am playing with ideas for a minimal heat loss solder iron holder, and one thing I was going to try was glass beads around a wire ring.
I’ve been using a stand that holds it near the joint of the tip and the handle for at least a year. Printed in ABS or PLA, I forgot which. Hasn’t melted or warped at all, and I often put it in at 430 degrees. I like how it holds it securely so you don’t have to worry about it moving around and burning something else on your desk.
If you were worried, I guess you could print a stand (or cut from sheet) slightly oversized and use silicone tubing, slit, as a grommet, and that would keep the last few degrees off if you were concerned it would glaze and smear.
Make the hot part touch nothing, Problem solved-https://www.instructables.com/id/Magnetic-Soldering-Iron-Stand/
My first thought was that the bearing would heat up causing the grease to boil out getting all over the soldering iron.
But as @Dude pointed out the iron rests so far into the bearing it shouldn’t very hot in that spot.
So then why use a bearing at all? Several people pointed out that a bearing provides minimal thermal contact between the races but then why does that matter if it’s not hot there?
I think the answer might be “use what you have on hand” and that’s what he had on hand. Don’t we all do that?
Note that this is a second hand take on this subject. [Oleg Vint] replicated the idea because the other guy had told them so. That other guy [MightyNozzle] literally wrote, “You need these items.”, in their instructions. Then they went out to give links to 608ZZ metal or ceramic bearings on Banggood where they sell between $7…12 in single quantities. Their message wasn’t “I hacked this together from old parts”, but, “This is what you need to make your own”.
HaD in turn is presenting this as an established solution for this particular problem because two people have already done it, and both present it as the way it should be done. Now at least four more people have replicated the design, verbatim with the bearing, and nobody has questioned whether it makes any sense to put in a seven dollar part that has nothing to do with the function of the thing.
Of course you can have bearings the cheaper, or use broken parts – that’s not the point. It’s the unquestioning adherence to instructions and example that makes my head itch.
Wait, that’s a $7 bearing they are using? As a soldering iron stand? I assumed they were just some of those things you get a tube of from China for a couple dollars.
LOL. Does the original author have bearings on their eBay page?
Yes! Or at least recommending; that’s what makes this so stupid. The original instruction links to super-expensive single item bearings.
That’s another thing I’ve noticed. There’s many people on Thingieverse, Instructables, Youtube and other places, who present “hacks” that are essentially just long shopping lists to Asian webmarkets. The hack consists of taking a bunch of ready-made parts and hot-gluing them together, and that’s it. They appear to be made up just for the purpose of advertising the wares.
Besides, if you’re ordering a tube of cheap bearings from China, you still have to order the whole tube and that’s gonna be like $5-10 anyways just so you can have the one bearing.
I know some people like to hoard stuff, but that’s false economy. When you die, your relatives are going to find boxes and boxes full of bearing that you never used for anything.
Some of my DIY USB soldering gun holders:
http://www.zoobab.com/soldering-workshop-for-kids-and-adults
If I were going to make a case for a portable soldering iron I’d have included a place for the cleaning sponge, a little solder, and the power supply. I’d probably consider whether I could make the power supply modular for battery and mains power too. Maybe I have a tendency to go too far though, I don’t know.
Dont have a 3D printer so i just soldered some paperclips together…
http://glassier.biz/20220120_190141.jpg
http://glassier.biz/20220120_190154.jpg