Despite the impressive variety of thermoplastics that can be printed on consumer-level desktop 3D printers, the most commonly used filament is polylactic acid (PLA). That’s because it’s not only the cheapest material available, but also the easiest to work with. PLA can be extruded at temperatures as low as 180 °C, and it’s possible to get good results even without a heated bed. The downside is that objects printed in PLA tend to be somewhat brittle and have a low heat tolerance. It’s a fine plastic for prototyping and light duty projects, but it won’t take long for many users to outgrow its capabilities.
The next step up is usually polyethylene terephthalate glycol (PETG). This material isn’t much more difficult to work with than PLA, but is more durable, can handle higher temperatures, and in general is better suited for mechanical parts. If you need greater durability or higher heat tolerance than PETG offers, you could move on to something like acrylonitrile butadiene styrene (ABS), polycarbonate (PC), or nylon. But this is where things start to get tricky. Not only are the extrusion temperatures of these materials greater than 250 °C, but an enclosed print chamber is generally recommended for best results. That puts them on the upper end of what the hobbyist community is generally capable of working with.
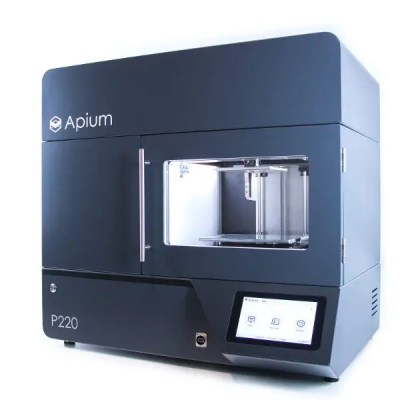
But high-end industrial 3D printers can use even stronger plastics such as polyetherimide (PEI) or members of the polyaryletherketone family (PAEK, PEEK, PEKK). Parts made from these materials are especially desirable for aerospace applications, as they can replace metal components while being substantially lighter.
These plastics must be extruded at temperatures approaching 400 °C, and a sealed build chamber kept at >100 °C for the duration of the print is an absolute necessity. The purchase price for a commercial printer with these capabilities is in the tens of thousands even on the low end, with some models priced well into the six figure range.
Of course there was a time, not quite so long ago, where the same could have been said of 3D printers in general. Machines that were once the sole domain of exceptionally well funded R&D labs now sit on the workbenches of hackers and makers all over the world. While it’s hard to say if we’ll see the same race to the bottom for high temperature 3D printers, the first steps towards democratizing the technology are already being made.
Engineering Challenges
Put simply, a machine that supports these so-called engineering plastics needs to be an amalgamation of a traditional 3D printer and an oven. But of course, therein lies the problem. The printer itself, especially of the type and quality that we’ve become accustomed to at the desktop level, wouldn’t survive in such an environment. For a consumer 3D printer to successfully produce parts in PEI and PEEK, it would need to be extensively modified; which is exactly what NASA did with a LulzBot TAZ 4 back in 2016.
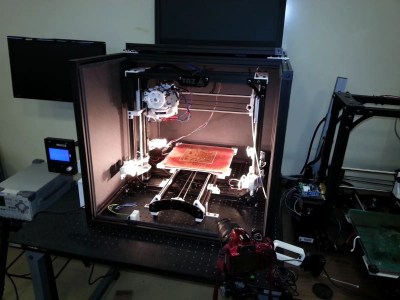
The first step was building an insulated enclosure that could fit around the TAZ 4, and installing an array of 35 watt infrared heating lamps inside of it. Naturally the machine’s exposed electronics would overheat in such an environment, so they had to be relocated to the outside of the box.
The stepper motors would overheat as well, but rather than trying to move them, the team at Langley Research Center opted to design cooling jackets to fit over each motor through which pressurized air could be circulated.
Like other desktop 3D printers, the TAZ 4 also utilized a number of printed parts in its construction. Printed in ABS , these parts would have quickly failed inside the heated chamber meant to support PEEK. The parts were reprinted in PC, but even this material wasn’t resilient enough for permanent use. So in classic RepRap tradition, the team printed the third and final set of parts on the modified printer itself in a form of PEI known commercially as Ultem.
Somewhat surprisingly, the team had little trouble upgrading the TAZ 4 with a hotend and nozzle that could extrude plastics at up to 400 °C. The popular E3D-v6 hotend costs less than $100 USD and was found to be capable of reaching these temperatures, though the team did need to replace its thermistor with a higher-rated model and make some adjustments to the printer’s Marlin firmware to allow it to reach temperatures that under normal circumstances would trigger a thermal shutdown.
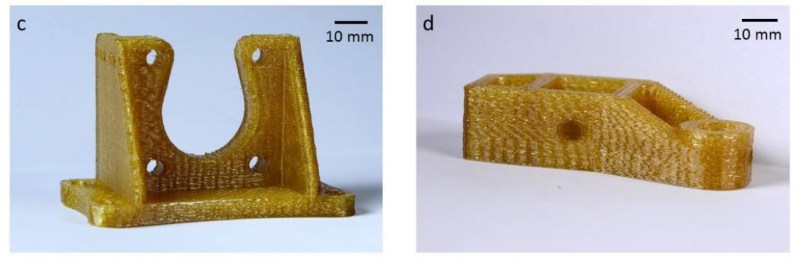
Ultimately, the NASA report concluded that the modifications to the LulzBot TAZ 4 were a complete success. They noted that attempting to print PEI with the IR heating lamps off lead to serious print issues such as warping and delamination, though this was to be expected. No final dollar figure is given for the cost of the modifications, but considering the base price of a TAZ 4 was approximately $2,200 USD at the time, the entire project was likely 1/10th the cost of comparable commercial offerings.
Starting from Scratch
NASA’s experiment showed that it was possible to modify an existing open source desktop 3D printer to print high temperature engineering plastics, and they even showed it could be done relatively economically. But nobody would say that bootstrapping this way was an ideal solution. There was too much duplicated effort involved in the conversion, as the engineers had to specifically undo design choices originally made by LulzBot. Even so, the experiment did create a valuable baseline for other projects that want to start from scratch.
Just last month, a team from the Michigan Technological University unveiled Cerberus, an open source high temperature 3D printer capable of producing parts in PEI and PEKK that can be built for just $1,000 USD. Rather than attempting to adapt an existing design, the team started from the ground up with high temperature printing in mind. All of the sensitive electronic components are mounted well away from the sealed build chamber, which uses a mains-powered 1 kW space heater core to rapidly bring it up to operating temperature.
Crucially, all of the stepper motors have also been moved outside of the build chamber. While this does make the kinematics somewhat more complex than what you’d see in a traditional desktop 3D printer, it means the Cerberus doesn’t need a dedicated motor cooling system like NASA’s modified TAZ did.
A simplified design combined with the use of off-the-shelf control electronics including the Arduino Mega 2560 and RAMPS 1.4 board, and the same E3D-v6 hotend used on the modified TAZ 4, puts the Cerberus well within the means of the motivated hobbyist. Especially since the team has provided clear and detailed assembly instructions for their printer, something notably missing from NASA’s report.
Expanding Possibilities
Between NASA’s TAZ 4 retrofit and all-new designs such as the Cerberus, it’s clear that the technical capability to print PEI and PEEK objects in the home workshop is there for anyone who wants it badly enough. It’s not quite as easy as buying a $200 3D printer on Amazon yet, but if the demand is there, more low-cost machines based on these core principles will certainly start hitting the market. It’s really not much different than the current wave of affordable laser cutters that have been taking over makerspaces these last few years.
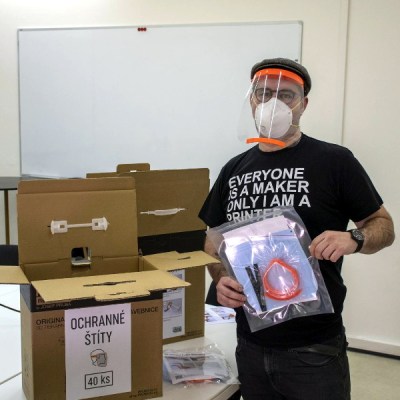
So, is there a demand for them? This time last year, the answer might have been different. But with the world still combating the COVID-19 pandemic, there’s a new demand for rapidly produced personal protective equipment (PPE) that nobody could have anticipated.
As explained in the documentation for Cerberus, the team at Michigan Technological University was inspired to look into developing an affordable high temperature 3D printer specifically because it could be used to create PPE that would survive heat sterilization. Rather than being disposable, the team believes items such as face masks printed in PEKK could be used over the long term.
Printed parts that can be repeatedly sterilized would obviously have other potential medical applications. A portable low-cost machine that can produce these components could potentially save lives in remote areas of the world were rapid access to traditional supplies and equipment may be unavailable.
Critics of 3D printing have often said that the core failing of the machines is that the parts they print are rarely robust enough to be used as anything more than a rough prototype. But when a $1,000 printer can produce parts in aerospace-grade materials, it seems like we’re closer to a manufacturing revolution than ever before.
Thank you for the first somewhat interesting 3DP article on HaD for a long time (not that most of it is common knowledge in the 3DP community, but there are probably a few newcomers in here).
Thank you for sneering at the other articles.
Reusable 3D printed parts in intriguing, but given the NHS apparently considers metal items like scissors to be single-use disposable*, I’m not holding my breath on this.
* as office first aider I took a colleague to A&E. the doctor took a fresh pair of sterile scissors to cut off the dressing I’d applied to my colleague. He then threw them in the bin. I know it was a bin, not a “stuff for sterilisation” container because he proceeded to throw the bloodied dressing in there. A couple of minutes later, He then took another fresh pair of scissors to cut open a fresh dressing, and they too (along with the packaging) went in the bin.
One doctor != NHS
That doesn’t sound right. Scissors would have to be disposed of in a sharps container along with used needles and scalpels, and bloody dressings would go into a biohazard bag if they are wet.
All went in a biohazard bag. Scissors were not sharp tipped, so maybe didn’t need to go in the sharps container?
But I agree, it’s not right.
One could speculate that the waste could be sorted later, with more time available than in an ER room. But yeah, probably they went to incinerator instead and were recovered as raw metal.
Had a similar thing happen when I had some stitches removed… A little sealed packet with an alcohol swab, a pair of tweezers, and a tiny pair of scissors. Swab swab, snip snip, and everything went into the trash. I asked if I could have the tweezers and scissors after they were used, but he shrugged and handed me an new unopened packet. I think on the scale of costs it’s probably cheaper to toss cheaply made items than it is to run them through a sterilization protocol. Less chance of liability problems as well.
these single use metal items are made of cheap carbon steel (not stainless steel) so they will corrode when exposed to blood and other body fluids. Heat, air and water (autoclave) will make the corrosion worse. Keep doing this makes the problem worse. The corrosion is a great place to harbour pathogens. Would you really want something that might be contaminated with something nasty to be used on your kids.
I’d expect them to not be single use and so be reusable for a long time. I’d also expect you not to be disingenuous but whatever…
You can expect all you like but this doesn’t change the reality of the situation.
I have personal experience of handling such metal items that were contaminated. You ignore my warning at your own personal risk. I just hope you don’t put an innocent third party at risk through your stupidity.
Wow…
Hospitals and clinics moved to disposable largely as a result of AIDS/HIV. There are documented cases where people became infected by instruments and devices that had been sterilized according to the practices BITD and were re-used. This lead to pretty much single-use everything. The manufacture of items from carbon-steel is an economic after-effect.
Probably started as a result of mad cow disease. Prions are devilishly tricky to kill(denature), and will EASILY survive the standard sterilization treatment.
wikipedia.org/wiki/Prion
Interesting, but for some applications, the electrical and chemical properties of the plastic are just as important as the mechanical properties. Ask my former students – I do not grade on a curve, but I do give credit for effort and existing work; so you get an A- for effort, a B- for content, but the assignment remains incomplete.
Are the electrical and chemical properties the entire list of properties that can be considered? What grade do you give yourself on that part, have you considered every arbitrary requirement that could be important?
I want to see Selective laser sintering(SLS) or Selective laser melting(SLM) come to the masses.
give the masses a cheap, powerful, hassle free laser – and you will. At the moment you can only have 2 of said traits. This is what currently limits SLS/SLM proliferation.
LED lasers – cheap, hassle free. But weak and combining the output of multiple diodes removes cheap and hassle free.
CO2 lasers – cheap and powerful. But finicky, fragile and not long lasting. Also the HV power supply is a bit of a death machine.
DPSS fiber – powerful and hassle free. However anything but cheap.
flashlamp-pumped SS – cheap-ish (if eBay is involved), powerful. Will not last long though. Again, HV power supply is absolutely deadly.
All other types of lasers tend to be even worse, mostly allowing only one of the 3 desired traits, some have none of them.
I have a few ideas on how I would make this work.
Simplified powder handling system, preheating the powder to somewhere below sintering and melting temp(not new).
Diode laser and polymer powder to start out with.
Metal may come later with improvements in laser tech.
Ehm… do you know that ordinary metal SLS absolutely must be and is preheated close to the sintering temperature and even then you need a powerful laser AND argone filling or a very good vacuum not to oxidize or even explode the powder?
Preheating does seem useful. I might expect resolution to suffer at some point, given enough preheating to approach fusion (melt) temperatures closely enough to drop laser power requirements by an order of magnitude. Heat from the melt zone will spread, and you want a sharply defined melt zone. Also seems like a hot enclosure would become more challenging to design and be shorter-lived.
A passively Q-switched diode pumped Nd:YAG or Nd:YLF “chip” laser should do it. Output will be intrinsically single mode, and with the Q-switching you can get enough energy in a short pulse to melt a tiny spot of powder even at 1-2W average power. At 1-2W average it could also be pumped with a single pump diode package. These lasers often diced from a layered wafer so can be very cheap.
While it would be cheap to manufacture and reliable, this is a VERY custom laser. You’d need a large production run to offset the development costs. It’d also print slowly due to the low average power. While layer thickness is likely to be limited by the pulse energy.
I think the problem is more the powder itself. It’s light and tiny grained. It’ll go everwhere. If you see how much PPE these guys wear I don’t think this is suitable at home.
Aside from the issues of cheap, high quality lasers that others have pointed out, people vastly underestimate powder handling problems. Loose powder can get *everywhere* if it’s not properly contained in an (expensive) enclosure. Fine SLS/SLM powders can get blown around if not careful, and its a way bigger hazard than anything filament/resin based.
Metal powders make the logistics even worse, especially if you’re printing anything reactive like aluminum powder. At best, powder-based processes will be like laser cutters, in that makerspaces with lots of dedicated space and some properly trained staff can primarily run the machines. Though, I’m still optimistic about metal paste/filament for personal hobby printing. It’s much cheaper and doesn’t have any loose particles to ruin your day.
Ahhh, “Kids these days”. Those that underestimate the complexities of powder-handling for SLS/SLM never had to change the toner cartridge of an old-school 1st/2nd generation laser printer.
It was a “practicality” test for noobs. I felt pretty good about about myself when I said “no problem” while wearing a white cotton long sleeve shirt “lemme just grab something”.
When I came back there were 5 engineers and a manager casually sipping coffee and watching to “see what would happen…”
I came back with nice length of hand paper roll. grabbed the carriage, yanked it out, had the paper towel covered in toner powder, wrapped it a bit further, shook it and dropped it back in. And repeated the sequence 3 more times for all the other toners. The paper towel had a beautiful mess on it.
The aplomb on everyone’s face showed they hadn’t a clue, was even more priceless.
About 2 weeks later, they did it to another new college grad… he was completely smeared and covered in all 4 primary powders. Face as well.
I can definitely understand why NASA would rather print in Ultem than machine those parts- I’ve machined Ultem myself.
It chips out pretty bad if you aren’t careful, its a fairly brittle plastic from what I remember. Chips out a bit like glass, a pita to machine. It has some really cool properties, so it makes sense they would be trying to print with it.
If you ever do try to machine it- leave every critical edge with some stock, and whittle down in multiple finish passes at progressively closer sizes. It really didn’t like standard helix endmills and sharp corners- use radiused endmills whenever possible, or it will chip out or pull out on you in small specs- and can shatter suddenly if you take too heavy a cut.
That does sound like extruding it’s a much better idea where possible.
The other nice thing about 3d printing is you can inspect the entire solid object as its made without having to x-ray every component to look for problems in the middle of a part.
True, though 3D printing has a different set of problems than moldings, e.g. layer adhesion.
Having had PLA parts turn soft and warp outside in the summer sun I just don’t get why it is so popular.
Every mention of this talks about the ease of printing it without a heated bed. I’m at a loss as to why that is so special too.
A heated bed is something like $10 on Ebay.
Obviously that’s not a great one but I can tell you from experience that it does fine with PET-G and can be used for ABS if you don’t mind having to use ABS-juice to prevent warping.
Even if your closed source printer doesn’t have the electronics and/or firmware to control a heated bed and you don’t want to replace all the electronics that still isn’t a show stopper.
All you need is an old computer power supply for electricity, an arduino and a relay and you can just set the temperature manually. For bonus points swap that relay out for one of the many little MOSFET switching modules available on Ebay or your favorite cheap parts shop and you can have PWM control.
With that kind of setup you could probably even clip the heated bed to your existing bed and not even make any permanent changes to the printer. You would loose a bit more Z-axis this way than if you just replaced the bed though.
Obviously the Arduino is overkill and you could throw a more basic micro-controller and a MOSFET on a piece of perfboard yourself but I’m keeping this familiar and friendly to even a beginning maker. And if you are that capable why not just replace all the electronics so your heated bed control is integrated?
Or, neverminding that it’s overkill, for a really simple build just get one of those many mass-produced cheap 8-bit printer controller boards where the “arduino” is integrated into the board and use it just for it’s bed control. Piece of cake!
“I was able to buy a 3d printer but I don’t have a heated bed…” makes no sense!
Today I learned that everything that is printed need to be outside in the hot sun. Who knew!
It doesn’t have to out in the hot sun. PLA prints will melt if left in a car parked in the sun. I’ve seen a few threads on reddit by people who left their printers in their car for a couple hours and came back to a machine with a bunch of warped printed parts that couldn’t print any more. Don’t use PLA for anything you care about and want to last or function for a reasonable amount of time. It’s mostly good for throw-away/give-away stuff.
Really? I have almost exclusively used PLA including for parts that are outside all year round. I have the capability to print in ABS/ASA etc as my printer is fully enclosed and has a heated bed but just haven’t found the need. My greenhouse guttering has been held up by PLA brackets and all the non-standard pipe fittings are PLA which have survived 3 years outside with no issues.
The only PLA parts I have had fail through mechanical stress or damage are ‘hands free’ door handles several of which are still going strong after daily use by hundreds of staff. I suspect a lot of the failures could have been prevented if I hadn’t been pretty lazy with the design and print settings.
Leaving a 3d printer in a car in the middle of summer may not be such a common scenario. Just saying :)
Not 3D printer. 3D prints!
“people who left their printers in their car for a couple hours and came back to a machine with a bunch of warped printed parts”
@Somun: Sorry. Obviously I can’t read properly *facepalm*.
Taking it to the hackerspace or a friend’s house.. have some stops to make on the way there and/or the way back.
And why aren’t more people printing accessories FOR their cars? I haven’t done much of that yet but I’m certainly interested in doing so.
I made a custom coin and wallet holder for my car: https://drmrehorst.blogspot.com/2019/09/a-coin-and-wallet-holder-for-prius.html
Printed in ABS, of course.
A couple years ago I printed clips to hold up a tarp over my fishing boat. Where I live it typically gets over 100F (~38C) about 3 or 4 days a year. Most days are significantly cooler but it only takes once to destroy someting.
I happened to go check on it one of those days, the tarp had fallen, I picked up the clip and could easily bend it like it was made of putty.
Not everything I do needs to go outside but I like to standardize on one material, tune for it and stock up on it. So PLA is out!
Try to make it white. That should make it stand a bit higher temperature as it’ll reflect more of the energy.
you can post process PLA with heat, which ironically makes it much more tolerant to being heated in the future. But its a bit of a faff.
That said I print almost exclusively in ABS and higher end engineering plastics, I’d love for the ease and relatively safety of PLA particularly at the early prototype stage, but changing the filaments that often and reprinting working parts in better material is too much of a pain to be bothered with.
That PLA can be printed under hugely poor conditions for 3dprinting and give excellent results though is a great reason to print with it, and many areas of the world won’t get hot enough to easily melt prints either.
Does it get so much more heat tolerant that you can trust it in the hot sun or in a hot car?
Also if you want to print parts that fit and work together you had better be very good at predicting exactly how much shrinkage will occur during that post processing and compensating for it in your design.
The biggest reason pla is chosen is it’s the cheapest material there is. Also it has some of the highest variety of colours. Also given 100 years it will decompose while most every other plastic won’t have even started.
Cheapest material there is. No, and not by a good margin.
Highest variety of colours, no. Most pigments can be used in most polymers.
Decomposition. It’ll only decompose in composting conditions. Otherwise, chuck it in your backyard, bury it in soft peat or leave it in the Nevada desert for a decade. You’ll find it right like you left it. Maybe a little warped of it gets hot.
Oh and by the way. You will not melt PLA under any condition in your car. Polymers can deform at temperatures well below their melting point.
@ Microcenter
PLA – $15 /kg
ABS – $15 /kg
PETG – $20/kg
Plenty of colors in all 3.
And PLA only degrades at temperatures higher than what are found in landfills.
I don’t see a reason here to chose PLA.
Made from renewable resources is probably one?
3D printing hobbyists are some of the stingiest people on the planet. They will do anything to avoid spending another $5 on their printers. Imagine them spending $250-300 for a kg of ultem! It’s not gonna happen…
On the other hand I have yet to see a machinist make me something reasonably simple without wanting to be paid. I’ve had *several* 3D printing hobbyists print me some of my weird designs/experiments for free, I only paid the shipping.
I don’t think you can put them all in one bucket. Some of them always seem to be looking for stuff to replace on their printers. Others will buy whole replacement assemblies rather than spend a few minutes cleaning something.
I’d spend $250.00 to $300.00 for improvements
But would you spend $250-300 for one spool of filament?
Looks like a really well thought out high temperature build. Don’t think you will able to set any printing speed records on it as those belts are long and the moving masses high, so bridging might be a little bit of an issue. But that is only one small part of printing and taking longer to print matters not at all really – all 3d printers take long enough if your machine is halfway decent you sod off and leave them too it, perhaps checking every now and then for abort worthy issues.
PET/PETG made into thin fibers is known as polyester, which includes brand names like terylene.
So you’re basically extruding pants.
Not a fan of the stationary head, moving bed approach. I think using a CoreXY head moving in XY and the bed moving in Z only would lead to a machine that gives much better space efficiency, and using a tool-changer would be a good alternative to the rotary multi-head used here. Of course, it will have a different set of problems that will need to be solved.
The reusable-medical application seems like a red herring to me, but I absolutely know that I’d like to be able to print mechanical bits that have more heat resistance, so this is a great direction for people to be working in.
I remember when we used to chuck PEEK in the lathe to make hot ends. That’s a very interesting plastic. The ability to print with it would be very cool.
For the DIY approach, has anyone ever tried simply building a FFF inside an old kitchen oven? Could possibly even hijack the original heating elements to pre-heat the space inside.
Kitchen overs tend to have a large exterior volume and limited interior volume, and working inside an already enclosed space is not so easy. It’s usually easier to build the printer, then enclose it and add heating elements and sensors later. Of course, most folks aren’t going for very high interior temperatures, so there are certainly high-temperature efforts that I’ve not heard about.
Also a lot of ovens have real poor temperature control. Over then under shooting oscillating around their setpoint. A way around that is to pre-heat well in advance but…
If you were going to do this, it’d make sense to buy a 220V PID controller (assuming electric oven) and splice it in place of the existing thermal control.
And (at the cost of really extending the warm-up time) a couple of cast iron exercise weights in the enclosure as thermal mass should help smooth out the temperature variations. Big thick sheets of aluminum would work much better but cost a lot more. You can get exercise weights at thrift stores.
A counter top microwave/grill combo might be a bit more compact. Perhaps the turntable could be repurposed with a stepper/servo to make a polar machine.
I think at this point it’s less to do with the hardware and design as it is Stratasys holds the patent for heated build chambers for 3d printers.
I have a feeling when their patent expires we’ll see a lot more machines on the hobby consumer market.
US6722872B1 for interested parties
Oh that expires in just 4 months! 2021 may be a good year for 3d printing…
My DIY printer has had a heated chamber for years.
If I remember correctly it’s the concept of placing the movement mechanisms outside the heat envelope. Apparently that’s not the obvious solution to not heating them up and is totally novel in the US patent office’s opinion. :(
Every ceramics kiln I’ve ever seen has the electronics outside of the heated chamber. How do some of these patents get granted???
I gather that due to limited resources, they tend to grant patents and let companies sort it out in court.
Keep in mind that a patent is a ‘license to sue’ — the cops don’t go looking for patent violations. The patent owner has to find and sue alleged violators.
Not all patents will stand up in court. If you can show prior art, then I think it breaks the patent.
Caveat: I’m not a lawyer, especially not a patent lawyer, and this does not constitute legal advice.
Anyone have good techniques to get get Polycarbonate fully transparent and clear.
Or with post processing?
https://www.lulzbot.com/learn/NASA-high-temperature-printing#:~:text=Researchers%20at%20NASA%20Langley%20modified,print%20with%20PEI%2Dbased%20filament. is a document from 2017…
I’d think a Delta-printer would work well in an oven. Just have to water-cool the heat-break, and bowden tube. (or cool a direct-drive stepper and filament supply tube) Be a lot harder to make it multi-extruder or IDEX though…
I like that idea. The layout looks conducive to a heated chamber. I couldn’t find any preexisting examples – I kinda thought somebody would’ve tried it for ABS.
ABS isn’t that difficult. My printer heats the chamber to 50C. Electronics are outside the chamber as are XY motors. Everything else in inside. I print a LOT of ABS with no warping and no delamination.
Are you thinking linear bearings inside or outside the oven? I do see high-temp linear bearings available. How would you handle thermal expansion?
Nice article, really enjoyed reading it and agree with some of the points. However printing PPE for long term use, out of engineer plastics doesn’t make sense. Peek where I live is 1000GBP for a spool Ultem is just a bit cheaper. At the cost of 3-4 spools you can make an injection moulding tool (out of aluminium, rapid tooling) and buy a bag of raw pallets.
I would like to see low priced machines with heated chambers but there are some thresholds because of physics. So having a heated chamber at 60c is easy. 120c is durable at low cost and the upper limit of ruberbelts and some motors. At 150c you need special linear rails and electronics. So a reasonably priced machine for everyone can go up to 120 which is not ideal for peek/Ultem printing.