One thing some of us here in the United States have always been jealous of is the WAGO connectors that seem so common in electrical wiring everywhere else in the world. We often wonder why the electrical trades here haven’t adopted them more widely — after all, they’re faster to use than traditional wire nuts, and time is money on the job site.
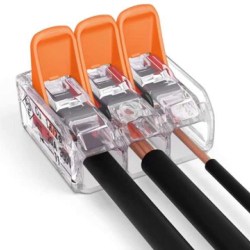
This print-in-place electrical connector is inspired by the WAGO connectors, specifically their Lever Nut series. We’ll be clear right up front that [Tomáš “Harvie” Mudruňka’s] connector is more of an homage to the commercially available units, and should not be used for critical applications. Plus, as a 3D-printed part, it would be hard to compete with something optimized to be manufactured in the millions. But the idea is pretty slick. The print-in-place part has a vaguely heart-shaped cage with a lever arm trapped inside it.
After printing and freeing the lever arm, a small piece of 1.3-mm (16 AWG) solid copper wire is inserted into a groove. The wire acts as a busbar against which the lever arm squeezes conductors. The lever cams into a groove on the opposite wall of the cage, making a strong physical and electrical connection. The video below shows the connectors being built and tested.
We love the combination of print-in-place, compliant mechanisms, and composite construction on display here. It reminds us a bit of these printable SMD tape tamers, or this print-in-place engine benchmark.
THIS is why I love 3D printers. There isn’t a lot of great stuff out there, but things like this are fantastic. Thank you for sharing!
Meh and whats with temperature above 60°C?
ABS/ABS+ is ok to 90°C. For me if something in my hobby electronics go over 80°C it’s good reason for replace connector/cable/radiator/etc. to bigger one.
You have to choose the material (or 3d printer technology) to match your use case. Design does not explicitly prohibit temperature resistant materials, while your FDM printer might. Also this is by no means meant for use in high power applications. Despite the 30V 9A clickbait title :-)
You should add an DISCLAIMER right above your description on thingiverse, just in case. People are people, they do stupid stuff. I even added one to a 3D printed utility knife handle because again: people…
Don’t get sued over burnt down houses :)
3D printers are prototyping devices and everyone using them holds the power to do damage in their own hands.
Finally some Czech guy. Was about time
Then you’ll use a different material?
I don’t know. What IS with temperatures past 60C?
Are you attempting to say that you don’t think this could handle hotter temperatures?
PLA is NOT the only plastic that can be 3d printed. Most printers can handle ABS or PETG. Some can even handle Nylon.
If you feel limited in what you can print by 60C then maybe it’s time for you to explore some better filament types!
And what’s the deal with airplane food?
It is extruded from the same machines that print these connectors.
B^)
Also tastes the same.
I beg to differ. There is A LOT of good stuff out there!
Every single room in my house has at at least two or three useful 3D-printed things that are in active use. People who think there isn’t a lot of good stuff you can do with *3D printers are just not paying attention.
Right, I have to add I use it for technical prints 99,9% of the time. Plus I try to always take notes regarding tolerances and so on to absolutely minimize my failed prints (a good printer helps with that, too). Our modern lifestyle produces enough plastic trash already, I try not to add to that with my hobbies!
So few?
Mike asked me once on the podcast about useful things that I’ve printed. I was recording at the time using a self-printed microphone spider shock mount, attached to the end of an adjustable arm mount made of aluminum tube and printed parts, and listening to him on headphones where the wire is routed through a printed clamp that holds it in place.
I started counting things within sight in my office. Stopped at 20.
The thing is, you start taking them for granted and it just blends into your life.
It’s huge, with a live wire sticking out the side. Nice concept, but some work needed.
OMG this is jus asking for trouble…. I wouldn’t even post that not to spread terrible ideas…
This is hugely dependent on the use case… This design is primarily aimed for prototyping. Great example would be to use this connector as replacement for breadboard wiring setup. Here on Hackaday i saw several projects featuring permanent installations of breadboarded circuits. I am sure that in many cases this can be better option as this 3d printed connector does not allow wires to go loose causing shorts under vibration or similar small to medium physical stress.
There is a reason why i didn’t designed this to take thick wires which might be used in AC mains wiring. This only takes wires usualy used in low-power and signaling scenarios. (eg.: the wires from CAT5 ethernet and SYKFY cybles). I hope such limitation will prevent people from wiring their mains using this :-)
Also if you think it is a good idea to use 3D printed connector for mains AC, you will eventualy burn your house down one way or another. No matter if i’ve shared the design or not.
Anyway. Thanks for your safety concerns and i hope you will help us to further improve this open design to increase the safety just a little bit. i beleive that through several iterations we will eventualy get to the “fully” safe 3d printed connector. at least in the long run. even when it might mean improvements in 3d printing technology itself.
” We often wonder why the electrical trades here haven’t adopted them more widely — after all, they’re faster to use than traditional wire nuts, and time is money on the job site ”
This what the beginning article states. The reason why we don’t use them is because the electrical trade is a craft and us US electrician still work with what has been proven to work decade after decade. I have seen many times these new Wago and Wago type pressure connectors fail. Quicker is not always best.
They come from Germany, and Germany is known for stricter requirements in security and safety than the US. I doubt your experiences are representative.
I don’t give a damn where they use them as long as they don’t use them in my house. Those connectors do not hold as well as a properly used wire nut.
Yes. These are not to be used in US residential, or commercial wiring. The rest of the world can do whatever. These connectors are not as secure as a properly twisted wire nut.
“These connectors are not as secure as a properly twisted wire nut.”
That is simply not true, wire nuts are complete garbage which is why they were banned from use decades ago in Europe.
That is a false statement to the national electrical code of recognizes them for the same uses twisted wire nuts I have seen wire nuts fail as many times as wagos fail most times it is due to operator error
“US electrician still work with what has been proven to work decade after decade”
All the North American homes full of aluminum wiring that insurers refuse to cover beg to differ.
I’m pretty sure aluminum wiring was used in the 60s its use was originally prompted by high copper prices.
Main issue I surmise is the dissimilar metal reactions when people replace items without shelling out for AL compatibility or using the special grey goo
There are aluminum conductors coming in from the utility for most afterall…
Don’t forget all the things they used instead of copper pipes
the polybutylene(80s) (went out of business with 1000s of claims unpaid)
or the cpvc(90s) that is now flooding homes (with diluted warranty :P)
or the pex that has that 20 year warranty (for now)
I wonder how much money has been ‘saved’ here its typically the labor that really costs
so maybe the piping saved some time (and money on labor)
Really? I’ve seen many wire nuts fail over the years for a multitude of reasons, yet never had a spring terminal fail in 30+ years.
Lever type spring busbar connectors are tool free and allow for easy individual conductor identification, along with a reduction of excessive cable length and a neat final installation.
There are also many cases where a wire nut just will not work. Wago lever terminals are specifically designed to work in a wide range of cases, allowing the safe connection of solid or stranded core conductors of different composition from 7/0.2mm^2 through to 6mm^2.
The argument of “that’s the way we’ve always done it” just doesn’t wash.
Quicker is often much better when combined with safer and better designed, which described the wago connector perfectly.
That’s funny our company has been using them for over 20 years and as long as you make sure they’re fully seated we have never had a problem with one they are listed by the national electrical code maybe you are not using them correctly
Speaking as an industrial electrician in Canada, I can assure you that WAGO connectors are just as reliable if not more so than twist-on connectors. They are only marginally faster to use initially, but they are easy to visually check if they are installed properly , as well as pull test. When you get to more than 3 wires, they are much easier to install, and less likely to have one poorly joined wire, so definitely better then. They are also less likely to damage the wires, specially if you ever take apart and put together again. They are much safer to work on live – the 221 model specially: you have holes for test leads to do live circuit troubleshooting without taking apart wires and can also safely remove the load wires without ever exposing the line wire. You can easily and safely splice new wires in, or remove unwanted wires.
Right now the only reason they’re not used in home construction is the higher initial cost. The best ones cost about 3x that of twist-on connectors. And of course home builders don’t care of their future benefits. Nor do they care of the repetitive strain injuries putting many twist on connectors can cause to their workers (which leads to some workers using power tools which leads to overtorqued connections.
Once the patents run out on these connectors, and their price drops, Twist-on connectors will go the way of soldered and taped connections or crimped on connections, and good riddance. The only advantage I’ve ever encountered of twist-on connectors is their ability to deal with a wide variety of wire sizes, for example connecting a #8 to a #14 wire, which really doesn’t happen very often.
On the one hand, I like the ingenuity here. On the other hand, I’m concerned that over time the plastic may creep, leading to a loss of contact force. It may be able to handle 9A of current when new, but I’d be concerned with how it holds up over years of thermal cycling. Anyway it is a really neat solution, I never considered printing connectors. This also paves the way to printing switches. For things like the output of an audio amplifier, a lab power supply, etc these seem like a nice solution (IE where you can visually monitor the connection). It just makes me nervous that someone will try to use these for mains a mains application, and will end up causing a house fire years down the line. Obviously in the linked video it is stated that these are for 30V, and nowhere is 30V used as a mains voltage. But some enterprising individual may just bulk up the print, a little more dielectric strength will get us to 120V, right? Anyway a little knowledge can be dangerous.
Just to make it clear. I did not done any testing, the specs are something between clickbait and rule of thumb.
30V is maximum voltage that you can have legaly exposed to touch in my country. 9A is rating for copper wire with 1mm diameter which can be fitted inside this connector.
As mentioned before… PLA plastic with glass transition temperature around 65C is not really good material to be used in high power applications. But for stuff like signal wires connecting sensors to microcontroller this should be relatively OK.
This is true. The Wago connectors and other similar ones use a metal spring to make the connection and the plastic is there only for housing. One should never use plastic for tightening the connection because it will eventually get loose from temperature, especially if the connection heats up (which makes a positive feedback loop). This type is suitable only for some low voltage, low current prototyping but nothing more!
Ever heard about “Deans T” connector? These are popular connectors rated for 60A. While they use metal spring, they still completely rely on plastic to provide enough pressure to hold the spring and everything together. They are made from fire-retardant PolyAmide (=Nylon). This material is also available in form of 3d printer filament.
Unless you have bad connections and high resistance at the join – which it doesn’t look like this will it shouldn’t get hot there easily. So thermal issues will likely be minimal – if you are getting hot enough in the enclosure to cause softening even of the low temperature PLA the electrics are probably about to let out the blue smoke…
Creep is a valid concern, don’t think it will be much of a problem though – as always material choice matters. But with seemingly very small deflection in closed position the clamping forces are lacking in leverage against any particular point. I’m not sure I’d trust them to keep working securely after many cycles, but its easy enough to tug test and be sure its gripping, and replace if needed..
The creep issue over time would be really worth testing, in 3d prints in general, I wouldn’t be surprised to find its actually better than solid of the same material at resisting creep with some geometries and materials, and terrible comparatively in others. What I can say is I’ve hung pretty heavy speakers off my wall a fair way on 3d printed mounts, printed mostly in PLA (the stuff that came with my printer – I prefer ABS in general) and none of them are showing any signs of deforming at the narrow weaker point that is bearing much of the load, the oldest bracket being I’d say 10 years old now (some reprints as I rearranged the room and needed different geometry and/or to also mount Vive Lighthouses).. But that one case doesn’t mean much, and I can say with certainty they don’t get warmer than 30 (as if the temperature in here is over 20 I’m halfway to dead, which leads, much as I hate using it, to the aircon going on), so your millage may vary.
Is WAGO under any kind of patents? That may explain a lack of presence.
Most likely, the WAGO connectors are not recognised by US electrical codes (because no one has gone through the process to get them approved).
They meet UL 486C for spliced connections. I recall them being okay re: NEC but hopefully someone with specific expertise can confirm that.
Here’s the link to the UL cert: https://www.wago.com/us/wire-splicing-connectors/compact-splicing-connector/p/221-413
Hmmm. That’s interesting. Because they really are easier to use than wirenuts. Maybe it’s just “industry inertia”? (no US marketing, tradies don’t know about them, higher perceived cost than wirenuts)
I suspect it’s all about price. Wago lever nuts aren’t nearly as cheap as twist-on wire nuts. Americans do one thing “better” than anyone else in the world- they seek out and buy the cheapeast crap they can find to do any job.
For use in AC wiring, we need to compare how they perform in terms of connection life, vibration, resistance to pull, etc before considering the WAGO type equivalent to wire nuts. Plus, the WAGO type have greater volume, which would require revisions to the box-fill rules.
I’m seeing some interest in the WAGO connectors from boaters.
@KenN
There are UL Listed connectors from this series, which means UL has already looked at all that stuff and said they’re good. Listed to 486C and 467 (for grounding use) for USA and Canada.
I’ve also used the push-in spring cage connectors, available at big box stores and in multiple poles (think about tying together 5+ wires in a nut). A lot of people think instinctively they wouldn’t be as reliable because you don’t clamp down so hard with a screw or twist it up with pliers. But in reality the spring contacts are reliable and vibration resistant.
Slight cynicism warning, Consider yourself warned this comment is marginally impugning the honour of any Electrician, and the construction trade as a whole…
Ok warning over here we go – Hard to use, equals more time consuming, which justifies the ridiculous prices electricians can charge…
If its simple, quick, and effective, its got no place in the smaller job site – where the cost of call out, labour etc vastly outstrips the slightly quicker install and the cheapest functional part can be passed on with markup to the client, harder to do that if the part costs £5 already… And on the big install jobs with so many connections to make saving even as little as 5p a connector will add up to fortunes, while not saving you enough time to pay for less work days…
@Foldi-One
I imagine a trade like electricians where most knowledge is passed down from master to apprentice would have a natural resistance to change.
I see prices in the $0.10 to $0.50 range per unit. At that cost, I don’t think materials cost would even be considered in pricing a small job. I’m not sure what you’re trying to say about the cost and speed and all. You’re saying the time it saves by using an expensive part is unimportant because the time spent in overhead, travel, etc. is so much larger that the electrician won’t care? And then you’re saying the higher part cost eats into the electrician’s margin because it’s hard for him to justify the price to the customer so he takes a lower margin on parts?
I’m not an electrician, but I’ve got a couple of alternative perspectives:
1. The customer is the one who doesn’t care if it takes you 1 min or 90 s to make the connection. He only cares whether it is done on time (which is relative of course) and how much it costs. Seems to me if it saves the electrician time or effort he will probably prefer it. Besides, it’s not like the customer is standing over his shoulder and will say “oh those little connectors take 2/3 the time! I think I should pay 2/3 the price!”
2. If the electrician’s margin hangs in the balance on a handful of 50c parts, I think he’s just doing it wrong. I’m not going to tell someone how to price electrician work, but in the end if the work is sound and the customer is ok with the price, then I think how ever he got there seems fine.
Maybe wire nuts are just such a minor thing that no one questions them.
@Grey Pilgrim
You are certainly not unreasonable in your perspective. (In truth its very much more in line with my overall views)
But I have seen such ‘professional’ folk try to pass of the £0.02 part as a the fancier easier to use/safer £0.20 one etc – there’s a reason we have stuck with the same builder, plumber, boiler maintenance guy etc for a long time now – they are not dicks padding the bill, but genuine and nice people I’d happily invite into my home, and actually do the job properly (plus faster than I could do it, and also being legal for them to do it).
I think for the price difference here nobody much is going to really care though – its probably not noticeable in the cost department using them or not, though as wirenuts are cheaper, why would you look at the pricier option without good reason. And the only real win I can see to using wago type is in the more modular ready build systems with lots of pre-run electrics – you can test each section, unplug, move to site, build and reassemble easily (and probably more reliably too), if you are only expecting to have put it together once, taking a little longer to really get it right on the cheapest possible connection shouldn’t matter.
Local supply places carry them, and at&t uses them for new telco wiring in homes, and they are all about making connections solid!
I have used them when installing low voltage co n.v trols in my place especially when space is tight or more than 3 wires also make very neat and tidy wiring job as they are not just a connection they also help keep wires in order.
That’s because they are garbage nobody should ever use in practice and will likely lead to issues in the long term. Their use can lead to connecting together different wire colors and all sorts of bodges that are blatant code violations.
Printed out of PLA I’d expect them to last all of a month at best probalby less. Especially since as PLA absorbs moisture it becomes brittle. You would have to print them from ABS/ASA, Nylon or PET.
WAGO connectors like this cause failure points to be placed in all sorts of weird locations you would never look for otherwise.
I’d look for failures at connection points, which includes junction boxes – the place where wirenuts and Wago lever nuts would be found. Where else would one look for failures?
There’s nothing to stop someone from twisting different colored wires together when using wire nuts.
I totally agree on PLA- PLA should never be used for anything that needs to last and/or gets exposed to moderate temperatures. It’s best for Starwars toys, tugboats, and similar throw away crap.
Wago nuts are the most reliable solution in use for 230V installations. They won a very conservative market through their reliability and ease-of-use.
These are used all over Europe for decades and are very reliable. I would even be tempted to consider them safer than screw terminals. They will not come loose over time and the wire cannot slip to side during tightening.
Unless you use aluminum wiring in your country, that would be really bad combo :-D
Never seen one in use for residential mains in the U.K.
Can’t tell if you had a bad experience, or had no experience with the Wagos.
I’ve worked for two (U.S.) different industrial machinery OEMs that have used them up to 480V in situations with vibration and thermal cycling with good results. I admit it took me a while to get comfortable with them, but now I like them much better than wire nuts. (I’ve seen them at 480V, but generally never more than 5-10 amps)
They (at least the ones we used) are listed for UL508A industrial panels.
Would I prefer a ‘real’ terminal block? Of course I would.
Should they be used in all sorts of weird locations? No. Splicing still needs to be done properly.
Should you splice different wire colors together? Would you do that with wire nuts? Rarely, but then you need to mark the conductors with colored tape. (I’ve only seen that in residential wiring)
Should you violate codes? No!
As wire nut replacements (i.e. small j-boxes like pigtailed motor connection boxes) they’re great. Also, I’ve seen them with up to 5 levers, so that’s much easier than trying to twist 5 wires into a nut and expecting them to stay. As a bonus, because the conductors don’t need to be twisted, I find it more flexible, compact and easier to undo if necessary.
I agree with your sentiments on the PLA version, but give the wago version a try some day.
Also imagine you want to add new wire to existing wire nut. With wago it is piece of cake. Especialy when you leave spare positions where it might be needed.
That is a false statement they are and have been recognized by the national electrical code for many many cycles of the code
They are available on Amazon in America and seem to have have an Official US arm (assuming they aren’t an American company). I constantly see people talking about them lately in the DIY space. 🤷♂️
http://www.wago.com
Ofc it’s not an US-company. It’s from Germany. Why do people from the US always think everything comes from there?
You can buy Chinese knockoffs for a fraction of the price that Wago charges. Search Aliexpress for “lever nuts”. Of course, they haven’t been tested and don’t come with all the safety certifications that Wagos do.
You don’t want to be a cheapskate when it comes to mains electrical installations (which only an electrician should do). Yes, the 221 is expensive but you only need a handful for the odd cases where you have soft multi-stranded wires. The majority of the wires here (switzerland, scandinavia, germany ..) are single stranded and the Wago connector for them is the cheap 773 series. Wirenuts are good bang for buck, a much better option than knockoff Wago’s.
The knockoffs aren’t as good as the real thing, but they do come in a bunch of useful configurations that the Wagos do not,!
Check this article. Original in in German, so google translate has to do the job: https://translate.google.com/translate?hl=&sl=de&tl=en&u=https%3A%2F%2Fwww.elektronikpraxis.vogel.de%2Fklemmfedern-von-minden-in-die-ganze-welt-a-545119%2F
We can buy unbranded ones the UK from walk in diy stores, and some similar connector variations that wago do not supply such as 2 and 3 pole inline splices, or one to many inline splices
Those would likely be the Chinese imports. [Great Scott] tested seven different ones against WAGO 221’s. Typical of China, two were quite good and cheaper, while five were both inferior and more expensive.
This is a clever design and is very cool, and I don’t wanna take anything away from the effort that this ingenious individual put into it. But I have to caution, the Wago connectors are designed such that if all of the plastic is removed, (IE melted away) the connection is still tight mechanically and low resistance electrically.. This design is the opposite of that, so it is straight up dangerous to use it in high current applications. It doesn’t matter if that high current application is at 3 V, or 300 V, hi current and a few ohms + plastic = fire.
Since this design is 3-D print it, it may make sense to emboss in the design itself “not for high current applications”
Or, since it’s such a small item, just emboss a big “NO” on it.
Hmm. All of mine now say “ON”.
I used to think that the brand name Leviton was pronounced
“Leave-it-on”.
B^)
Actually, I’m thinking it would be a great design feature to have the joint go open if the plastic melts or burns, as long as you add a brace of some stable material like ceramic to keep the wires from releasing. Too many times I’ve opened a cabinet to find a wire nutted 120 V or 240 V junction with all the plastic melted off the wire nut and the insulation burned off the wire. The nut wasn’t tightened enough or the copper was dirty and the resistance just heated it up enough to keep building up more carbon, adding to the resistance and increasing the heat, all without drawing enough amps to trip the breaker, until the wire finally burns through and drops to hit the cabinet and throw the breaker. Or, as in many cases, drops to hit an ill placed low voltage wire and cooks right through it’s insulation to blow out all the sensitive low voltage gear. The coil inside the wire nut just happily remains there, keeping the circuit going until the wire fails. Having a self fusing failover mode would be preferable.
This is a horrible idea since a slowly separating contact would arc over with even a few amps current. It would burn and melt everything around it. There is a reason circuit breakers have spring loaded contacts and arc guards…
Once I has a compressor with a cheap chinese ”fuse” which was a bimetallic strip and a spring loaded plastic that went between the contacts. Contacts were not spring loaded and separated slowly when heated by the current. After a few trips the plastic had melted a bit and did not isolate the contacts properly. the resulting arc welded the contacts together. Luckily it didn’t burn everything down with it…
I’d be concerned about oxidation. Maybe one could dip the copper wire into some Liquid Tin before inserting it into the clip.
The pressure on the wires is so high, i beleive it can *kinda* cut through the oxidation by deforming the wire a little. There are barely noticeable dents on the wire after using this clamp. But we will see after using this for some time.
In another similar design i’ve used thin coat of petroleum jelly to prevent copper oxidation. Gold plating would be optimal, but i guess this is not what you are looking for when 3d printing your own connectors :-)
I’ve been using WAGO for years in the US….but mostly for low voltage connections. I have always been a little hesitant to use them in high current /voltage applications because a springy metal clip in plastic seems like a problem to happen in the future….but they sure beat insulation-displacement t-taps for long term reliability. They also do not fall off like wire-nuts when someone revisits a j-box in the future…and they make up to 6 -wire splices…you can’t really jam that many wires in a wire-nut. They do make gel filled wago’s for better moisture reliability. I also am a big fan of transparent plastics to allow quick inspection of the connections.
But on my test bench, they are much quicker than wire nuts.
They should never get past the test bench that is for sure … they should never be used in an actual installation.
I consider them basically an slightly better equivalent to alligator clips…
That must be why they’re used in the millions every year by certified electricians in housebuilding, power current appliances and everything. And I speak of only Germany here. I guess there is no company here which is not using them. They’re what screw terminals were decades back: https://en.wikipedia.org/wiki/Screw_terminal and the word WAGO-Klemme is a eponyme now…
And btw: Check https://www.youtube.com/watch?v=bP0qHyVAymU and https://www.youtube.com/watch?v=eg6VPucscxI
Oh please! We should use them because they pass EU regulations? That worked out really well for the Notre Dame Cathedral didn’t it? You guys can’t even keep your priceless landmarks from going up in flames!
Dude here thinks US electrical standard are better than German :’)
Oh Rosie dear don’t you think it’s queer…
That these “hackers” don’t google to see if they’re available and meet standards in the U.S.?
https://www.wago.com/us/c/wire-splicing-connectors
Beep beep: your consideration is not what professionals think. Wago is there since the 1970s and guess what. They’re used in the millions each year (in Germany pretty much no other vendor plays a big role on the market) and aren’t even failing quickly when handling 3x their rated current (like 100A for the most used kind 222 and 221). They’re what screw terminals were before that.
Check youtube for over-current tests and re-evaluate your opinion. Because sometimes opinions are far from facts :)
Exactly! EU regulators love them! That’s all we need to know to stay away!
That’s a stupid comment.
You are talking about this strange twist on wire nuts, not? :-)
This Wage clamps are widespread here in Europe and do not present problems. Normal screw clamps present a higher danger for a connection loosening over time than the spring loaded clamp.
And have you ever had to terminate 5 12awg (20 amp, not sure the metric size) wires into a nut? It’s the jankiest goddamn feeling splice. I’d love to see wago stab splices replace the nuts, but they’re substantially more expensive in quantity 100+
I definitely agree that 5+ wires is a really difficult splice. I am an electrician and it is still something that I avoid if at all possible. If you do find yourself needing to make this kind of splice with a nut I recommend stripping the wires considerably longer than you intend the final splice to be. This allows you to get a nice tight spiral of the wires at the base of the splice and then cut off the excess to fit under the wire nut. Using a pair of decent lineman pliers to do the initial twisting also helps (cheap ones have too narrow a head to properly accomodate the wires). I was always taught that a wire nut is to protect and insulate a connection, not make it in the first place. Ignore the directions that tell you to just jam the wires into the nut parallel to one another and then twist the nut.
WAGO lever clamps work well in industrial applications where vibration can lead to oxidation buildup between wires, causing intermittent connections and increased resistance. I have seen installations fail over time with other connector types as voltage drops.
We use Wago elements in industrial context, literally a magnitude of dozens of thousands of connection points, many rated a 400V AC, and they are absolutely reliable. No screws, no nuts, everything is easily serviceable.
The polymer they use is absolutely amazing, it takes a LOT to break, it does not deform easily, it is perfectly insulating.
The only difficult thing is to find your way in the plethora of versatile items in the catalogue. But once you know it a bit, the anything is reachable on a DIN rail.
You’re clearly biased against the WAGO clips. Are you a Big Wirenut astroturfer?
I’m reading your comment as endorsing wire nuts over WAGO for high current/voltage applications. Is that because you trust a conical metal spring in plastic more than a lever-operated metal clamp? Seems like a weird trade-off to me.
I’ve never used one, but I think I would prefer them to wire nuts in just about any application they both were rated for.
Sounds like a good way to set your house on fire. No printable material has a flammability rating as far as I’m away.
Yeah, PLA will burn like a candle.
There are many UL94 listed filaments. So should you use them for printing clamps for wiring stuff in your home? HELL NO, that’s what certified connectors are for!
yep
Using 3d printed connections for wires is just asking for trouble tbh in my opinion
It Would take up to much space in a j box
People are arguing here like somebody is suggesting we all redo our home electrical wiring with these things. Why go straight to that?
I’m looking at them and thinking they could be great for things like speaker terminals, building solder-free kits for one’s kids to assemble, non-impedance matched receiving antennas, etc…
The headphone jack on my cellphone would also be a bad choice for carrying line voltage. Can I sue Samsung for that? Give me a break!
Excactly,
I built a cardboard robot on the weekend with one of my kids and something like this would have meant he could have done the wiring on his own.
Wago lever nuts are great for making power supply connections- poke the wire into the hole and flip the lever. Done.
I wired my 3D printer using wago lever nuts and used a bunch of the 5 terminal parts so I could add things like LEDs, fans, etc., without having to take everything apart.
These printed parts could be used in a lot of prototyping situations that aren’t expected to work for very long, or have crazy current running through them.
Yep. I think the article got linked by some electricians’ blog or some anti-WAGO lobbying firm. Definitely a lack of the normal open minds and critical thinking going on here.
If any of the panic mechants did take a moment to read the Thingiverse description the designer does offer warnings and limitations of the device
There’s no time for that!! Quick everyone! Protect your loved ones!! Turn off all the power in your houses!!
Neat for hobby use I suppose. That said,
Thanks to this article (and comments), I learned about the Wago Lever connectors and when checking also found in-Sure connectors. Never ever bothered to look as I’ve just always assumed standard wire nuts to splice house wiring in junction boxes or where-ever needed. Not that there is anything wrong with wire nuts… It is just now I know there are other solutions out there that may work better in some situations.
There is plenty wrong with wire nuts. For those who have seen everything done with screw terminal blocks a twist splice like a wire nuts looks and feels like a bad joke.
I’ve not had good experiences with spring loaded wire connections (working loose, intermittent contact, low power, requiring special opening tools), but those Wago connectors look like a good solution.
Will aim to give them a trial
The concern-trolls are out in force today.
ThInK oF tHe ChIlDrEn!
The “you can’t tell me what to do ” message received loud and clear.
Two “it’s not about you”. Some of you seem to forget a couple things. One like any publisher, the bigger the audience, the better (within reason). Two, articles and comments have a long shelf life. No telling who will be reading years down the line. Three there’s nothing wrong about thinking of others. I’d take people’s concern over the current apathy that’s societies soul.
That’s, um, four points?
Hi there. 2022 checking in. 👋
Bit late for the WAGO flamewar I suppose, but here’s my €0.02:
1: what better way is there other than lever connectors to connect a stranded wire to a solid core? If your answer involves screw connectors or solder, we are no longer friends.
2: Yes, genuine WAGO is expensive(ish). I’ve used the jab connectors in my house install, and now use the levers in professional environments where the cost is not mine. I’ve also bought a large quantity of 100% genuine chinesium variants. For all of these, I’ve rigged up a quick setup to run about 3x the max rated current through them (about 100A) for about 45min, and for all of them goes, the wire heats up long before the connector does. Even the clones had the PVC sluff off the wires before the connector started going soft. the PBT WAGO’s looked brand new after their ordeal. If they can do that, I can trust them with 10A 24V. So far I’ve yet to use them at 16A 230V, but I see no reason why not.
They do tend to bite your fingers when closing though.
“Won’t someone think of the fingers!” :-p
The WAGO connectors use metal springs to keep the wires connected. It will keep them secured even when the connector has heated up that the plastic becomes soft and starts to melt. This 3D printed connector seems to start failing like this cheap connector from China that used metal spring on plastic surrounding material type contacts
https://www.epanorama.net/blog/2018/01/24/cheap-quick-wire-connector-block/
Holy crap. What F&*#ing part of “prototyping” are you people not understanding? Most of you are waxing poetic about how dangerous these are (and/or its idea) with the tone of superior knowledge bleeding out of your comments. More like the fact you’re manifesting yourselves to the point of utter obnoxiousness.
Good job Harvie. Really. A hack of the truest sense of word.
It all comes down to how much bonding there is between the wires. This clip has a very minute bonding surface – the smaller wires touch the bus bar at a single perpendicular point (ie: 2 cylinders come together at a single point), the WAGO connector bonds at multiple points, along the surface where the clip meets the wire, and the Wire Nut is bonded at multiple points (along the three physical windings of the wire plus the bonding between the Wire Nut and the windings). The Wire Nut is still the most used here in the USA because it has the largest bonding area. This clip is a great idea for prototyping low voltage or audio connection, but beyond that I would not recommend it. I have the same concerns as others do here in that by posting this, people will take it too far and out of the bounds of designed aspects and hurt themselves or cause a fire.
as a US electrician with over 30 years of experience, I don’t know anything about the standards in Europe, but in the us, electrical products have to be UL listed for the purpose that they advertise.
The context of the opening paragraph, that these could replace a wago connector, is deceptive at best …and very dangerous at worst.
Also, for the record, you can buy Wago connectors here; I have a bunch in my van. ;-)
I also use wire nuts -but when I see wire nuts fail, it’s usually because a previous electrician did not twist the wires together first. I consider a wire nut to be a ‘cap’ or a ‘cover’ rather than an actual *connector*. If the wires aren’t connected directly by careful and skillful twisting, you’re not going to have a secure connection. I have seen porcelain wire nuts which I am sure are from the 1930s or earlier that are still secure with knob and tube wiring. Wagos aren’t that old, but I trust them as well.
While this is clever, it borders on being irrresponsible. While most of the comments here are focused on temperature of use related, you have neglected the real problem- FIRE. Plastics used in electrical devices have flame and smoke inhibitors for a reason. You can start a pretty good fire with small wires and low vontages. Please use the real connectors.
As a Commissioning Engineer I find the denouncement of the WAGO style spring contact clamps amazing…… If only because the ABS (the American Buro of Shipping) basically says in their recommendations that you should always use spring clamp contacts, unless you have a very very good explanation of why you can’t use them.
Of course the materials used should have the appropriate and applicable ABS and UL approvals, or the equivalent thereof.
Of course this is not limited to shipborne installations, I’ve done enough jobs where I filed (and got) for an exception to the NEMA rules, where I believed an IEC approach was better suited.
In other places I found the NEMA approach superior, and also got the go ahead to use it in place of IEC.
The only thing that all those jobs have in common, is that they are screwless and twist-wire-nuttless.
Don’t get me wrong, wire-nuts are fine when installed properly, but they are also 19th century tech, and as such outdated. Especially in industrial and utility applications where modifications are like to be made, the wire nut just does not have a place anymore.
The design needs to allow the wires to remain inside the connector when used so they are not exposed and in danger of shorting.
Oh God… Please don’t… You don’t have to 3D print every crap 🤦♂️ Wagos and other clamps are cheap as fck… AND SAFE!
My God. This is too fantastic for words. Design and functional use of it is just great. I hate that I didn’t come up with this myself. I know you could find things online and out there for cheap but to be able to make it yourself modify it configure it at a moment’s notice is just beyond words. I had the biggest grin on my face watching the video of this clamp. Absolutely fantastic. This is why we have 3D printers. Thank you thank you thank you. You rock. Amir