Early Friday morning a Boeing 777 performed an emergency landing in Moscow, according to Russian media. The Interfax news agency cites an anonymous source who claims the landing was caused by an engine failure on a flight from Hong Kong to Madrid. According to the Hong Kong civil aviation department this was a cargo flight. So far no injuries have been reported.
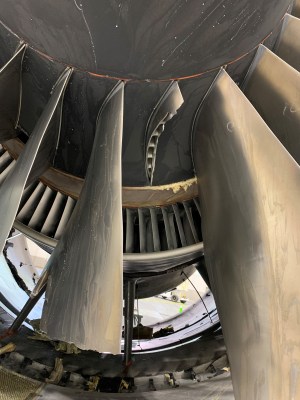
Engine failures happen, pilots train for them, and our airport infrastructure is setup to accommodate emergency landings like this. However, the timing of this reported failure is notable. This is the second engine failure on a 777 within a week, and the third to occur in a Boeing aircraft.
Shortly after takeoff on Saturday, February 20th, a United Airlines flight bound for Hawaii made an emergency landing after suffering a catastrophic failure of the right engine. The event was widely shared on social media, you likely saw the video from a passenger inside the Boeing 777-200 that shows the damaged engine on fire — if you haven’t you really should. There was also damage on the ground due to falling debris. This prompted Boeing to launch inspections of all 777-200s, and soon afterwards the NTSB published photos of the damaged engine. No injuries have been reported.
Two days later, on February 22nd, a Boeing 747-400 cargo plane operated by Longtail Aviation suffered an engine failure over the Netherlands, dropping parts that reportedly injured two people on the ground. This is a different model of aircraft but uses a Pratt & Whitney PW4000, in the same family as the Pratt & Whitney PW4070/4090 on the United 777-200.
Reports of this morning’s emergency landing in Moscow will need to be verified and investigated, and we have not seen confirmation on what type of engine the Rossiya Airlines B777-300ER used. For comparison the 777-300ERs of the United fleet and the 777-300ERs operated by Emirates both use General Electric engines rather than Pratt & Whitney models, so it is likely the Rossiya aircraft also had a GE engine.
The fact that the flights were all able to make safe landings is a testament to the redundant engineering of these aircraft. CNET did a deep dive into last Saturday’s engine failure and notes that it was an Extended-range Operations Performance Standards (ETOPS) aircraft capable of flying long distances on a single engine — necessary if an aircraft needed to make it half-way to Hawaii on one engine for an emergency landing. They also report on two other Pratt & Whitney PW-4000 engine failures in 2018 and 2000 2020, although as mentioned before, today’s incident likely didn’t involve an engine from this maker.
[Main image source: B777-300 by Maarten Visser CC-BY-SA 2.0]
Does this have anything to do with hollow blades?
Not directly, no. The blades are hollow to save weight, but it doesn’t in and of itself compromise the blade integrity. Turbofan blades have been hollow for many years, it’s not new tech. However, if the process in creating those blades was compromised, then they might have weaknesses that weren’t planned for.
It’s a little bit weight but mostly that they’re forcing LOTS of air through the blades, and through tiny holes in the surface of the blades to form an insulating layer, so that they can exist in an environment that’s hot enough to soften solid/noncooled turbine blades.
These are fan blades, not turbine blades. It saves a lot of weight; the hollow blades weigh around 30 pounds and produce enormous tension and bending forces from rotating and gyroscopic effects as the plane changes pitch and yaw.
Looks bad for Boeing, but in general I’m inclined to think this isn’t their fault, rather P&W or GE, they’re self contained units so not sure where this could possibly involve Boeing aside from how they’re interfaced with the rest of the plane.
One question to ask is whether these planes were mothballed during the earlier Coronavirus outbreaks. Could this be a symptom of that stagnancy time they had to endure?
It really shouldn’t look bad for Boeing in this case – they make the airframe that the engines are mounted to, but not the actual engines – nor does Boeing do any of the MRO on the engines. These are (at least in two cases) Pratt & Whitney engines – it should look bad for them. A Boeing 777 can have GE, P&W, or a few other engine types mounted to it, and (in the case of 737’s) they can be several models of engine.
If a wing comes off of the plane, that looks bad for Boeing and the airline – this should look bad for Pratt & Whitney.
I was wondering if these types of engine (or engines generally) were failing at about the same rate across the different aircraft manufacturers, or if it is occurring more frequently on one type of plane?. It might not be statistically significant anyway if there are only a small number of cases?
You know that and I know that but in the headlines, who’s plane fell out of the sky?
I got a super bight LED floodlight many years ago from B&D. The battery died very prematurely. B&D told me that they did not make the device and I had to call some other company, and they turfed me off to yet anther company. In the end I would up calling B&D and telling them that their name is on it in big letters. Last thing I will ever buy with that kind of support. I guess the moral of the story is, even if you only use the part but put your name on the finished product, you are going to get the blame. Choose your parts carefully. Even with something like TV’s. The caps go bad in the power supply. You don’t hear much about some company making the caps, you hear about the samsun tv’s failing.
The airlines contract separately with engine manufacturers for their maintenance. In this case it seems it’s GE instead of PW.
many times they don’t even own the engines, just lease them ;-)
I don’t know how anyone would ever want to run a business. There are so incredibly many levels of deals and logistics and contracts and subcontractors that it’s just insane.
Exactly my thought as well. So many people bashing Boeing for this when it’s the fault of the engine manufacturers (and/or the maintenance crews tasked with doing blade inspections)
Indeed, though understandable in many ways, as the last pile of Boeing scandals, that really were all Boeing’s fault haven’t died down and faded in the memory yet, and where full of poor practices by the company. So being on a Boeing again makes it easy to put the blame on them, as it was them last time…
Also could still be partly or entirely Boeing fault, seems like its too early to tell from what we know – I would be rather shocked if that was the case, but it is still possible to be the Boeing electronics driving the engine to self-destruct.
seems the cargo plane would have been more heavily used, considering the impact the pandemic has has on shipping infrastructure. they would want every plane they have in the air running cargo.
Ultimately, it is still their fault for specing what is expected of the blade and selecting the blade vendor.
e.g. If you bought a laptop from Dell with a faulty battery pack and cause a fire, Dell is directly responsible to compensate you not the battery vendor.
That’s not now it works with aircraft. Boeing or Airbus sell airframes. The airline then buys or leases engines directly from ge, p&w, rolls Royce, etc. Nobody pays Boeing for engines. This isn’t their mess this time
The initially failed blade had fatigue failure indications on both previous inspections. However, there is paint on the blades and the indications were thought to be from debonding of the paint, even though the indication was in the same spot both times and the paint had been stripped and the blade repainted between inspections. That failure in inspection is why they were grounded, due to the reality that the inspection system had been compromised.
The blame cast for Boeing is limited to the engine housing. While the blade was contained from high-velocity exit the subsequent damage is raising questions about other measures that might be taken. The main problem, it seems to me, is how to make access panels that are easy for people to use to inspect the engine that are sturdy enough to also contain that energetic and focused force. Imagine designing the front door of a house stopping a 100mph SUV.
The core issue with these engine failures is inspections that are too infrequent. These blades accumulate cracks, ablation, pitting, and chipping. There are acceptable thresholds for these types of wear/damage, and when exceeded the engine is taken out of service and repaired or rebuilt. Because the inspections ground the aircraft for a time, and require trained technicians, it’s my opinion that the airlines are cost cutting in this area perhaps justifying by saying the planes fly less frequently and/or are less loaded. These particular metal blades are acoustically vibrated and looked at with IR as the cracks will cause hot spots. There are also visual inspections for the other wear and tear. Attention airlines – please inspect your engines and airframes!
Engine maintenance is handled directly by engine manufacturers separately from the airframe.
Actually, airlines can decide to do full teardown/rebuilds on engines themselves (I believe that British Airways does it this way) or an MRO (Maintain, Repair, Overhaul) company can be contracted. Everyone has to follow the manufacturers guidelines, but there are a lot of caveats to how closely those rules are followed and some airlines chose to exceed manufacturer’s specs (replace parts more frequently or before they fall completely out of spec) while others simply meet spec – it is a financial choice for each airline.
But other things do figure into maintenance – not just how many hours or takeoff/landing cycles has the engine gone through, but how has it been treated while in operation – some pilots land harder that others (take a multi-ton high-rpm spinning rod and start smacking it around on its bearings) and even though a bird strike might not kill an engine outright, it can cause damage to a first or second stage blade that a pilot might not be able to see…
I think that is mischaraterizing the trouble.
Commercial transport aircraft (part 121, etc) have scheduled A checks where engine inspection is done. The time between inspections may be longer than normal because the individual aircraft are flown less, since the time between checks are in airframe hours. https://en.m.wikipedia.org/wiki/Aircraft_maintenance_checks
It could be with less flying corrosion is taking is toll on the engines sooner.
It is likely with aircraft coming back on line out of storage there will be a few more failures that appear until the fleet is being exercised regularly.
Wait until the investigation is done before blaming the bean counters.
You have no clue how frequent the inspections are do you?
ETOPS: Engines Turn Or Passengers Swim
Entrees To Our Pacific Sharks
Extremely thorough observation pre-flight
I did not think that through.
PSA: flight DOES NOT start with S.
pre-swim, then.
So is United, Boeing or GE buying that guy a brand new truck? (youtube vid)
Whoops P&W, was the Denver one in vid mentioned, GE was the Moscow one, the 4000 series P&W appear to still be grounded from soon after Feb 20th until remedial measures identified.
According to avherald, that’s the fourth Boeing with an engine failure this month.
…which still remains irrelevant. Boeing doesn’t make the engines. P&W and GE make the engines.
If a tornado can bury a wheat straw into a tree what can a little starling beak do to one those blades at full speed in just the right spot?
A noise like starlings make but very loud, probably. Canadian geese that’s another situation, Sully knows. Those geese are #1 cause of serious bird strikes. Turkey Vultures count less but they are in big numbers here suddenly.
Drone strikes?
As of the Airfleets record https://www.airfleets.net/ficheapp/plane-b777-32709.htm, there were GE90-115B engines installed https://www.geaviation.com/press-release/ge90-engine-family/ge90-115b-ges-best-ever-new-jet-engine-entry-airline-service
Btw, it was originally Emirates plane and changet in 2018 to Rossyia