[Zhihui Jun] is a name you’re going to want to remember because this Chinese maker has created quite probably one of the most complete open-source robot arms (video in Chinese with subtitles, embedded below) we’ve ever seen. This project has to be seen to be believed. Every aspect of the design from concept, mechanical CAD, electronics design and software covering embedded, 3D GUI, and so on, is the work of one maker, in just their spare time! Sound like we’re talking it up too much? Just watch the video and try to keep up!
After an initial review of toy robots versus more industrial units, it was quickly decided that servos weren’t going to cut it – too little torque and lacking in precision. BLDC motors offer great precision and torque when paired with a good controller, but they are tricky to make small enough, so an off-the-shelf compact harmonic drive was selected and paired with a stepper motor to get the required performance. This was multiplied by six and dropped into some slick CNC machined aluminum parts to complete the mechanics. A custom closed-loop stepper controller mounts directly to the rear of each motor. That’s really nice too.
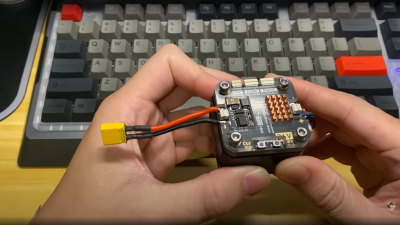
Control electronics are based around the STM32 using an ESP32 for Wi-Fi connectivity, but the pace of the video is so fast it’s hard to keep up with how much of the design operates. There is a brief mention that the controller runs the LiteOS kernel for Harmony OS, but no details we can find. The project GitHub has many of the gory details to pore over perhaps a bit light in places but the promise is made to expand that. For remote control, there’s a BLE-connected teaching device (called ‘Peak’) with a touch screen, again details pending. Oh, did we mention there’s a force-feedback (a PS5 Adaptive Trigger had to die for the cause) remote control unit that uses binocular cameras to track motion, with an AHRS setup giving orientation and that all this is powered by a Huawei Atlas edge AI processing system? This was greatly glossed over in the video like it was just some side-note not worth talking about. We hope details of that get made public soon!
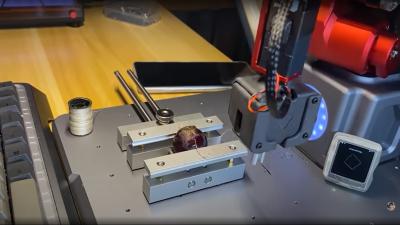
The dedicated GUI, written in what looks like Unity, allows robot programming and motion planning, but since those harmonic drives are back-drivable, the robot can be moved by hand and record movements for replaying later. Some work with AR has been started, but that looks like early in the process, the features just keep on coming!
Quite frankly there is so much happening that it’s hard to summarise here and do the project any sort of justice, so to that end we suggest popping over to YT and taking a look for yourselves.
We love robots ’round these parts, especially robot arms, here’s a big one by [Jeremy Fielding], and if you think stepper motors aren’t necessary, because servo motors can be made to work just fine, you may be right.
Thanks to [djtano] for the tip!
Can we wind back a little, where did he get that monitor at the bottom???? It’s awesome!
Right? It is probably custom made by him though. I think he released videos about DIY MIPI DSI lcd controllers in the past.
It’s called a “Ultra Wide LCD” or a “stretched Bar LCD” and it’s usually used for advertisements.
Waveshare makes them in 7.9, 8.8 and 11.9 inch sizes. You can get them at bezos barn for around 100 – 120€. They have an hdmi connector, so no adapter required
Now this is a project worthy of praise
I want to know where he found reasonably-priced harmonic reducers.
Right now we’re using some small units from Harmonic Drive (which is the same brand he shows in his video).
They’re fabulous, but they’re also $550 each, which is fine for our commercial application but kind of spendy for a hobbyist project.
Also, right now Harmonic is quoting us a FIFTY week lead time. Ah, the 2020’s
I think they were used. If you look at the shot where he’s got all the parts laid out around 6:20, you can see some wear on the casings.
Someone in the comments mentions he’s working for HUAWAI and earns around 400 or 500k€ / year. I mean, it’s the YT comment section… But I imagine he’s got the moneys for the stuff he wants to build ;)
Whatever the truth is: he seems to be a super smart person…
If you earn half a million/year, I don’t think that your employer will let you have time for hobbies lol
If you earn half a millon, your employer needs you more than you need your employer.
At the github there, he mentioned he got it for 600 yuan (second hard)
+1
hey dude can you please share the brand you used for harmonic driver or please share the link from where you brought from please I am really willing to learn by recreating it pls and thank you
Crowdfund this now! It is time for robotic arms to become as affordable and ubiquitous as 3d printers.
That fucker just stuffed a PhD or two into a single project!
Or that ‘fucker’ just showed that what you think is worthy of a PhD is merely a hobby project ?
I went over the top but you’re seriously delusional if you think this was 4 weeks of tinkering with limited knowledge in a single field.
Merely a hobby project. hahahaha
makes all the rest of us look like idiots. really cool project!
Too bad this project is quite hard to reproduce because of the loads of custom PCBs and machined parts, however this is incredible that he designed all of it : everything seems perfectly polished and user-friendly.
Custom PCB’s and machined parts are very much the easy part of this – the design & software effort are what’s truly insane.
I’m choosing to believe he’s built this on a lot of other people’s code & frameworks because otherwise he might just be some sort of superhuman.
“I’m choosing to believe he’s built this on a lot of other people’s code & frameworks because otherwise he might just be some sort of superhuman.”
He mentions his employer Huawei quite often, just like he does nationalist chinese statements etc.
Conspiracy theory:
This is at least in part a PR stunt, downplaying or ignoring the support from Huawei company ressources.
I mean, there is this stupid stereotype, that chinese can only copy known concepts and do as they are told, but are incapable of creative work. Which is something the chinese obviously do not like, but they like propaganda.
Look, here we have our super human tinkerer. Much better than yours.
The tone of the video is also quite arrogant.
But on the other hand – if he indeed did all of this by himself in his spare time – he very much earned the right to be arrogant.
Incredible work. What I always fail to see with robotic arm projects is any kind of followup – like what is this arm good for, what will it be used for? I have my robotic arm in my closet because it was fun to build but couldn’t think of any good use for it.
And yeah, he makes me feel kind of engineering deficient.
This!
I decided for me that buying a used industrial one is the better option. I found a Kuka 16kg Arm with not even 200h on its shoulder at a university where it gathered dust. 3000€, a day off work and a few hundred km to drive with a transporter is all that was necessery – oh, and waiting for the best opportunity, thats the most important part. It ran beautifully within the first two hours of minor bugfixing and some googleing.
Maybe I should write that journey up for an article :)
He claimed an accuracy of 0.01mm which i find hard to believe, but with that spec i can see lots of apps. The first being a pick and place for custom assembly of say 1 to 20 circuit boards. It may be slower than a traditional PnP but it would be flexible.
I think that’s the power of China here (I’m not criticizing). Just like 10 years ago when every american video contained a patriotic claim for America superiority… This guy’s main force is the environment he’s working in. He’s access to cheap electronic and mechanic material. Getting part CNC machined? No problem, it’s just on the bottom of the street. Anodization is almost free. PCB creation ? No issue. And so on.
If for each step of you project you don’t (really) have to struggle finding a manufacturer, and this manufacturer does not have any technical limitation, nor the price itself. Then you can go fast, and iterate a lot.
As he said, the hardest part was the software, and I really understand why.
Where I live, each single step would take 3 weeks to perform (at least), since choosing the manufacturer, importing his limitations, waiting for manufacturing, delivery and then do it again if you’ve made a mistake. You’ll loose interest in your project much faster than that.
I am very impressed by this whole thing. But the software is not really open source. Just a bunch of precompiled dll-files in the github repo.
Shame, since downloading a random dll file from China is on my list of Things I Won’t Do.
Does anyone know the software he is using in the video for 3d modeling? Just getting started and saw how detailed the software he used was.
he used fusion 360 if you are still interested