Basketball has changed a lot over the years, and that goes for the sport as well as the ball itself. While James Naismith first prescribed tossing soccer balls into peach baskets to allow athletes to stay in shape over the winter, today, the sport looks quite different both rule-wise and equipment-wise.
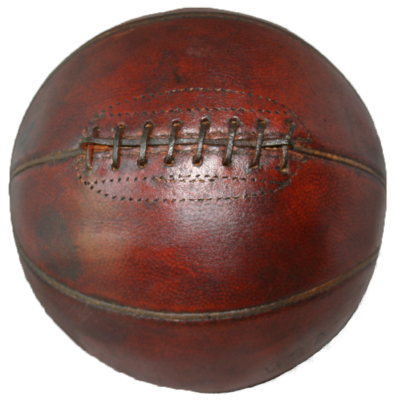
The basketball itself has gone through a few iterations. After the soccer ball came a purpose-built leather ball with stitches and a rubber bladder inside. The first molded version came in 1942, although most balls continued to be made of leather, especially for indoor-only use. Today, the NBA still uses leather-clad balls, but that could change. Wilson, the official supplier of NCAA postseason tournament balls, has developed a 3D-printed basketball that never needs to be inflated.
Much like a regular ball, the Wilson Airless Gen1 has eight lobes, bounces like you’d expect, and can be palmed, provided your hand is big enough. We would argue forcefully that it is far from airless, though we do get the point. According to TCT Magazine, the ball “nearly fits” the performance specs of a regular basketball, including weight, size, and rebound. This may not be good enough for the NBA today, but we doubt innovation over at Wilson has stopped abruptly, so who knows what the future holds?
Interested in trying one out? You may be better off trying to design and print one yourself. The limited-edition ball will be available on February 16th at Wilson.com for the low, low price of $2,500. It would probably pair well with the can’t-miss robotic hoop. Or, pair it with a giant 3D-printed hand for display purposes.
Main and thumbnail images via Wilson Sporting Goods
Why would you want to argue it was far from airless?
Because the ball consists of like 90%. Of course you can also call it airless because the air isn’t trapped inside the ball. So I think both interpretations are fully valid.
The point of air in a normal ball is to keep it inflated and hence it affects the bounce. The ball would not bounce or keep its shape without air. This ball doesn’t rely on air to keep its shape or to provide it’s ability to bounce, the ball would still function in a vacuum.
If it doesn’t trap air and doesn’t really rely on air for it’s main function then I would say it is airless, even if there happens to be air within its volume.
I think the correct term is ‘pressureless’. There is air, like in a regular ball. But unlike a regular ball, the air has room to enter and escape. Therefore inside the ball, there is the same pressure as outside the ball. Bar any temporary variations due to compression and decompression during use of the ball.
I don’t see too much room for interpretation here. :)
This will never see mass production because 3D prints by definition cannot be mass produced. A moulding machine can make far, far more balls per hour at far less cost.
3D printing is already used in mass production, and a moulding machine can’t produce the complex design that is this ball. Depending on the machine custom colors and designs could easily be produced as well. The cost of retooling is negligible since there is no tooling unlike moulding machines
Why do you think that 3D prints can’t by definition be mass produced?
First result on Google, from Oxford Languages for the definition of mass produced: “manufactured in large quantities by an automated mechanical process”. 3D printers produce objects through an automated mechanical process and you can use 3D printers to produce large quantities of items, so by definition it is possible to mass produce items with 3D printing.
3D printing for mass production isn’t really that different from other types of manufacturing, like machining and they are definitely used for mass production too although machining is avoided where possible due to costs just like 3D printing often is. Just because people avoid a method due to cost that doesn’t mean that the method can’t be used for mass production.
Also a moulding machine is limited in the complexity of items it can create. An item like the ball shown here could be a nightmare or impossible to injection mould. The holes in the surface of the ball could already potentially be a problem and any internal details would definitely make injection moulding it as one piece impossible. As it is just now, making the ball injection mouldable could require major changes and that would change the properties of the ball which is obviously undesirable.
Your argument here is basically saying that any kind of machining can’t be used for mass production either and that casting can produce objects faster and for cheaper. Whilst it may be true that they can make items faster and cheaper, it isn’t always possible to cast a part, you are very much limited in similar ways to how you are with injection moulding.
So wrong. Lots of products are already produced in volume via 3D printing, and the tooling for molding is expensive compared to that for 3D printing. I used to work in an industry that relied on molding for production … cycle times for fabricating molds are long and costs are high.
Prusa 3D prints nearly all of the plastic parts for their printers, which they’ve sold nearly half a million of by now.
There are multi-nozzle printers which can print 2 to 4 of the same print at the same time meaning that mass production can be a thing and there are surprisingly a lot of companies that use 3d printers for mass production.
I don’t see a lot of detail from the photo but i feel fairly confident PIM could be used to make the panels and they could be fused together at the joints with the ultrasonic thinger ma-tjinger. The honeycomb geometry might cause some voids, although i don’t recall the guidelines from material science.
It really comes down to your engineers and accountants figuring out how to scale it to meet a cost point.
Small quantities (like less than 100,000), customized or niche product i would bet fdm would be chosen since you could switch over equipment to run other jobs almost on the fly. It really doesn’t take long to re-tool a machine though if parts are on hand. The big cost is a dye that only makes one shape for pim.
“Basketball Jones, he’s got a basketball jones, oo baby oo oo oo!”
-Cheech and Chong
also, 1971 is calling and wants its speaker grills back. :)
I envision dirt, debris, grit, small stones, etc. rattling around inside.
It depends on where you play. If this is intended for professional or semi professional use then the courts will be kept as clean as possible and any balls that do get dirty or get things stuck in them can just be replaced.
That makes me think. The surface of a ‘normal’ ball has a certain friction. Would this ball have the same amount of friction? I guess the plastic needs to be coated with some rubbery substance.
Considering it is soft or elastic plastics that are used to print the ball it might not need any coating, just optimise the material used to have the correct grip in the first place.
Airless basketballs have been done before and a long long time ago actually. Turns out they suck! There are a LOT of materials with elastic properties but gasses are the only thing that have -perfectly- elastic collisions. That’s kinda what give them their predictable nice bounce.
Gases absolutely do not have perfectly elastic collisions. Look up the pv=NRT equation and then wonder what happens to the heat when you suddenly compress a gas. Absolutely not lossless.
I wonder do the holes act in a similar way to the dimples in a golf ball and extend the potential airtime for more longer distance shots.
I also wondered that. Then I wondered how having lots of air flowing through those holes in flight would affect it. I suspect a lot of extra drag. You’ve gone from a sphere with a drag coefficient of 0.5 to what’s basically a net, with a corrugated of drag probably much higher.
I’m any case, it might bounce like a normal basketball but it definitely won’t fly like one. I know nothing about basketball though, so no idea if that matters!
I’d imagine it would behave more like a whiffle ball
One whole year late to the game HD. This ball was actually _used_ in the NBA All Star dunking challenge in 2023. See this: https://www.youtube.com/watch?v=zRoHKpmcRS0 – it’s not very impressive.