When thoughts turn to the modernization and decarbonization of our transportation infrastructure, one imagines it to be dominated by exotic materials. EV motors and wind turbine generators need magnets made with rare earth metals (which turn out to be not all that rare), batteries for cars and grid storage need lithium and cobalt, and of course an abundance of extremely pure silicon is needed to provide the computational power that makes everything work. Throw in healthy pinches of graphene, carbon fiber composites and ceramics, and minerals like molybdenum, and the recipe starts looking pretty exotic.
As necessary as they are, all these exotic materials are worthless without a foundation of more familiar materials, ones that humans have been extracting and exploiting for eons. Mine all the neodymium you want, but without materials like copper for motor and generator windings, your EV is going nowhere and wind turbines are just big lawn ornaments. But just as important is iron, specifically as the alloy steel, which not only forms the structural elements of nearly everything mechanical but also appears in the stators and rotors of motors and generators, as well as the cores of the giant transformers that the electrical grid is built from.
Not just any steel will do for electrical use, though; special formulations, collectively known as electrical steel, are needed to build these electromagnetic devices. Electrical steel is simple in concept but complex in detail, and has become absolutely vital to the functioning of modern society. So it pays to take a look at what electrical steel is and how it works, and why we’re going nowhere without it.
Iron vs. Steel
The idea for a feature about electrical steel came from a story bemoaning delays plaguing renewable energy projects in the United States, mainly due to supply chain issues with the transformers needed to upgrade and expand the electrical grid. Building wind and solar farms is one thing; connecting them to the existing grid is another, one that often requires building completely new substations and refurbishing existing ones to gather the output of geographically dispersed generators and boost it to an appropriate voltage for long-haul transmission. Substations need transformers, often lots of them, and transformers are large, complicated devices that more often than not are custom-built. Lead times on large power transformers now routinely exceed 150 weeks!
The root cause of the three-year wait for large power transformers comes down to raw material supply chain problems, particularly with electrical steel. The electrical steel market is global both on the supply and demand side, so disruptions in one part of the world can ripple through the entire market. The electrical steel market’s current disruptions can be blamed on a host of factors: pandemic-era shutdowns of mines and factories, international sanctions, tariffs and trade disputes, off-shoring of manufacturing, and probably about a dozen other things. What it all means, though, is too little of this specialized material to go around.
So what is electrical steel? In some ways, the name is a misnomer; while electrical steel alloys are formulated specifically to change their electrical characteristics, these changes result in different magnetic properties, which is the key to understanding what they are and why they’re important. Electrical steel, which is used in the cores of nearly every device that uses magnetism, is probably better called “magnetic steel.” The material does have a few other monikers that better reflect this, such as “relay steel” and “transformer steel,” but the name “silicon steel” is perhaps most chemically descriptive, for reasons that will soon become obvious.
All steels are simply alloys composed primarily of iron and carbon, and electrical steel is no different. Pure iron is quite soft and ductile; the addition of carbon in just the right amounts serves as a hardening agent that gives the alloy its increased tensile strength and other desirable properties. Being primarily composed of a metallic element, steel is a good conductor of electricity. That sounds like it would be a beneficial property, and indeed it can be, as in the case of automotive electrical systems, which often use the steel body and chassis as a low-impedance return path.
Hysteresis Control
However, in electromagnetic assemblies like motors, generators, and transformers, carbon steel’s conductivity ends up causing problems that need to be solved. This has to do with the ferromagnetic properties of the iron in the steel, such as magnetic permeability and magnetic coercivity. Magnetic permeability measures the degree to which an external magnetic field, such as from a coil of wire carrying an electric current, induces a magnetic field in a material. Permeability is what makes steel stick to a permanent magnet — the magnet induces a temporary magnetic field in the high-permeability steel, causing the two to stick together. Coercivity, on the other hand, measures the degree to which a ferromagnetic material can resist becoming demagnetized by an externally applied field.
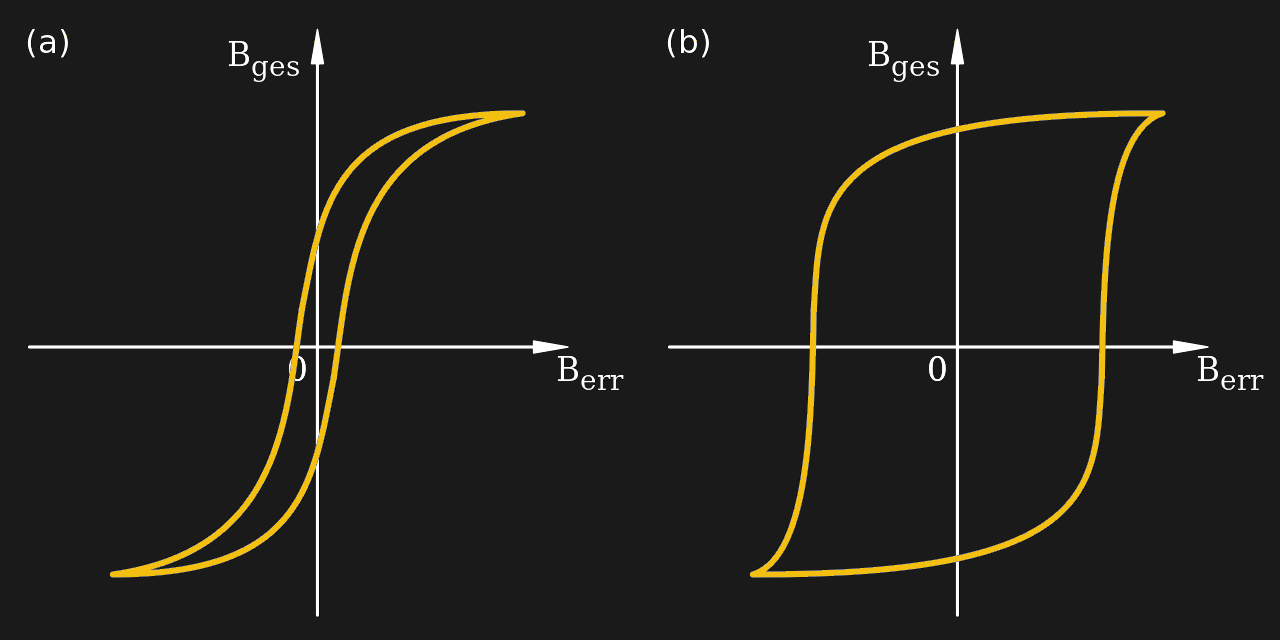
Electromagnetic components like transformers exhibit hysteresis, which just refers to how the history of a system can affect its current state. In an electromagnet, for instance, the core stays magnetic for a while after the current stops flowing in the coil. Likewise, in a transformer, the magnetic field created in the core by the alternating current passing through the coil doesn’t instantly collapse when the current reverses polarity. Rather, it lags somewhat, creating the characteristic shape seen on a hysteresis loop diagram, which maps the magnetic force applied by the coil against the magnetic field density in the iron core.
The details of why the magnetic hysteresis loop diagram looks the way it does aren’t really important to understanding electrical steel except to say that the narrower the loop, the more efficient the transformer (or motor or generator). This is because the induced magnetic field in the core spends less time opposing the magnetic field in the coils. But this leads to a paradox: pure iron has a very slender hysteresis loop, while alloying iron with carbon widens the loop. It seems like steel is therefore a poor choice for transformer cores than pure iron. What gives?
As with everything in engineering — and life in general — there are tradeoffs. While pure iron may be the best choice in terms of minimizing hysteresis losses, iron is a soft, ductile metal that would be difficult to form into mechanically stable transformer cores. The problem would be even worse in motors and generators, where rotors and stators need to stand up to the torque produced or applied. Steel is the material of choice for these applications, but the trick is to alloy it in a way that makes it mechanically strong while minimizing electrical losses.
Eddy Current Losses
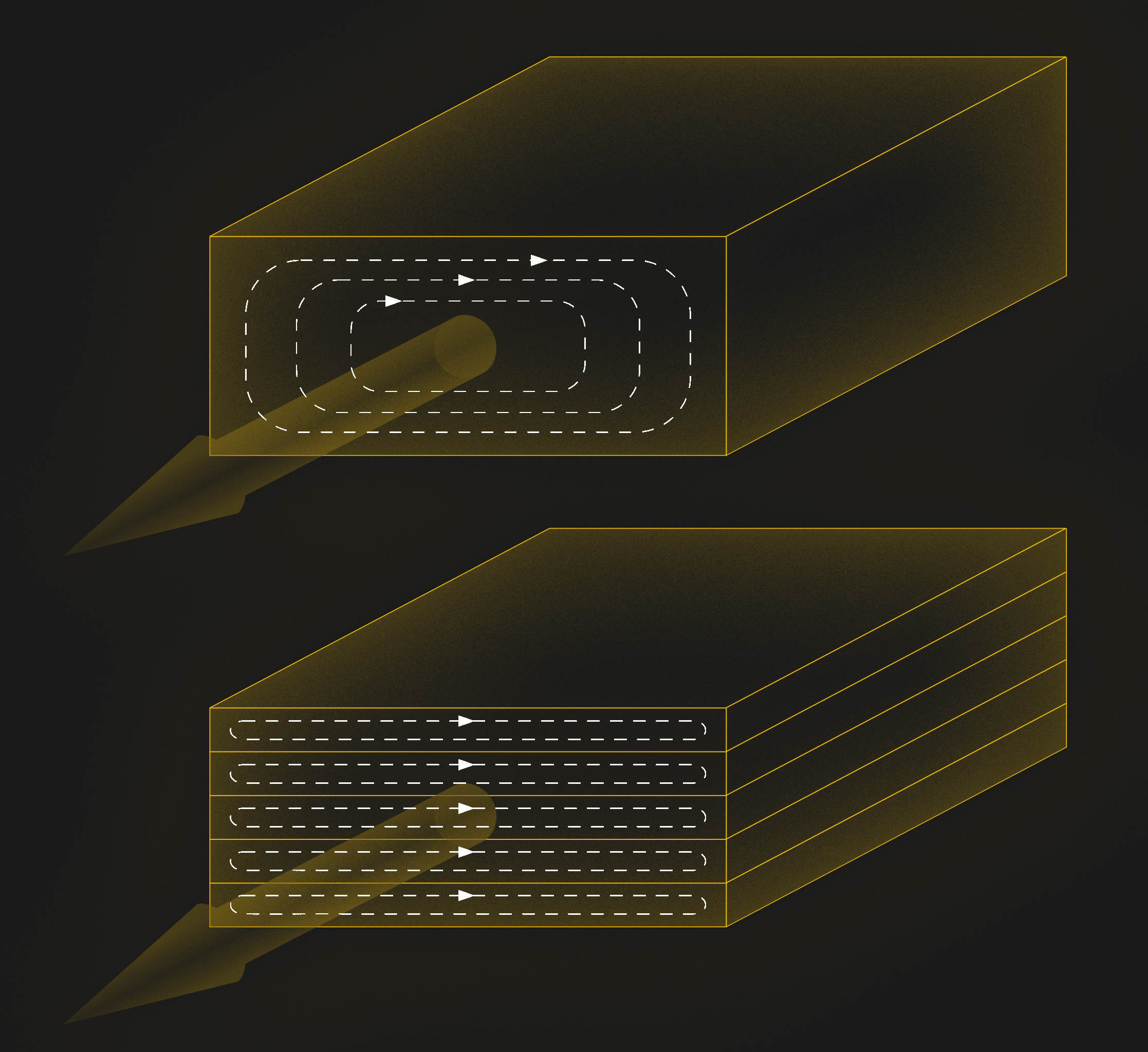
But wait — hysteresis losses aren’t the only losses electrical steel needs to deal with. There are also losses thanks to the familiar eddy currents, which are electrical currents induced in metals by magnetic lines of force passing through them. Eddy currents both physically oppose the torque of motors and generators, and dissipate electrical energy through heating. Since the magnitude of eddy currents is proportional to the area of the conductor — the iron core, in this case — it pays to reduce the size of the core. Or, as is more typically the case, to build cores from stacks of thin laminations, each electrically isolated from each other but which act as a monolithic component magnetically.
Also, eddy currents are inversely proportional to the resistivity of the core material. Put all these together and what you need is a material with the magnetic permeability and coercivity of pure iron, the structural properties of carbon steel, and electrical properties that land somewhere in between. That’s electrical steel.
The magic ingredient that gives electrical steel its desirable properties is silicon. Like all metals, iron is electrically conductive thanks to unpaired electrons in its outer orbital shells. Silicon, on the other hand, is a semiconductor with a higher resistivity (measured in ohm-meters, or Ω·m). When silicon is alloyed with iron and carbon at a concentration of between 3% and 6% by weight of finished metal, it increases the resistivity of the resulting steel. This occurs thanks to a combination of refining the grain structure (smaller grains mean higher resistivity) and forming a solid solution, where silicon dissolves into the iron-carbon matrix and reduces the number of free electrons available carry charge. The lower resistivity of silicon steel narrows the hysteresis loop and helps reduce the losses due to eddy currents compared to carbon steel, while maintaining a lot of the magnetic properties of pure iron and delivering the structural properties necessary for the application.
Going With The Grain
Because almost all electrical steel is used to make laminated cores, rotors, and stators, it’s usually manufactured as cold rolled coil stock less than 2 mm thick but sometimes as thin as 0.2 mm. Electrical steels are categorized by their grain structure and orientation. Non-oriented grain steels are cheaper to manufacture and have similar magnetic properties in all directions. This isotropism makes non-oriented grain steel more suitable for use in applications like motors and generators where the magnetic flux is constantly changing.
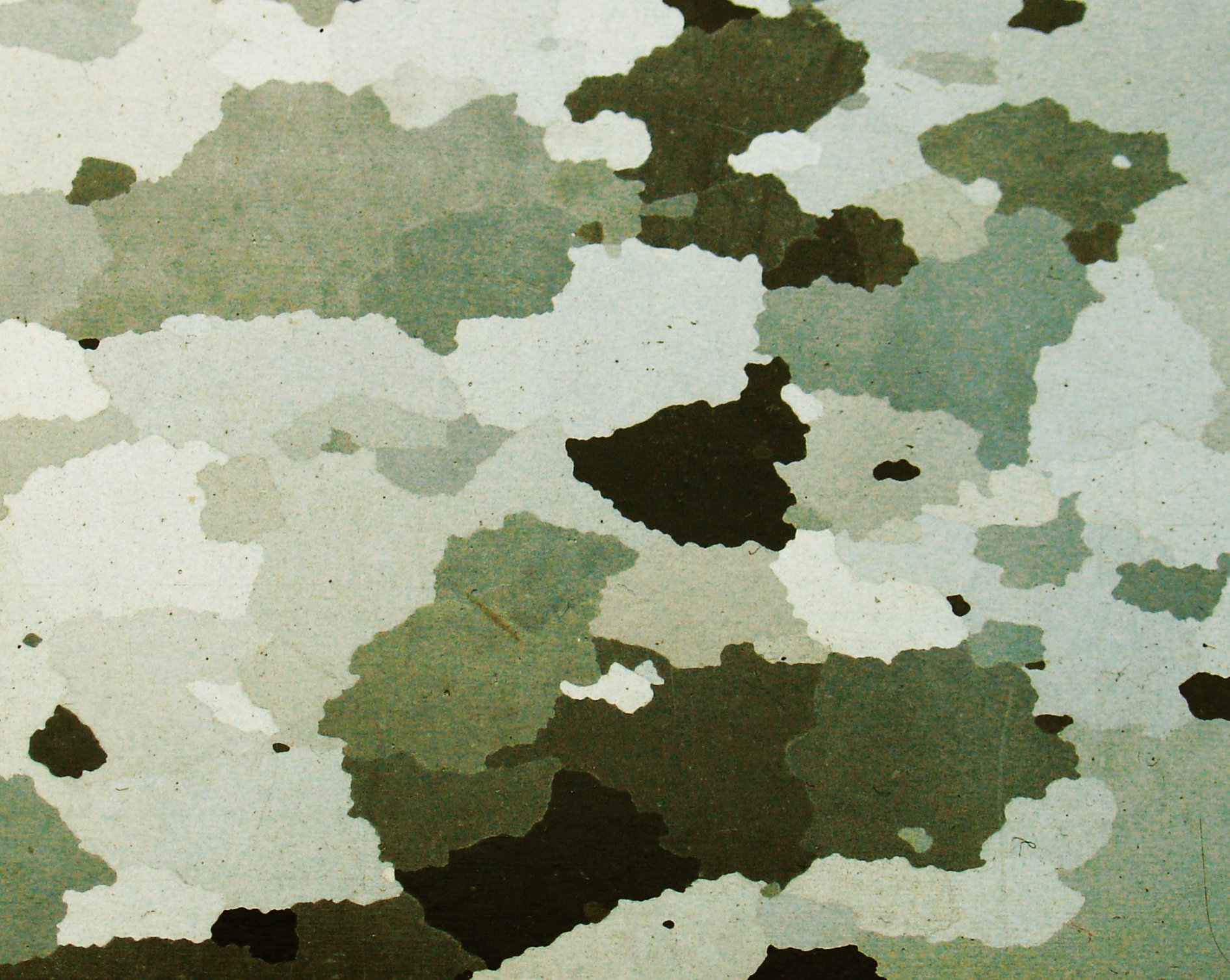
For applications where the magnetic flux doesn’t change much with time, like the large power transformers that are in such short supply these days, grain-oriented electrical steel is desirable. The magnetic lines of force in transformers mainly line up with the long axis of the laminations, so core material needs to have greater magnetic permeability in that direction. Grain-oriented steels suit this application better because the magnetic moments in the metal line up in the direction of rolling, giving strongly anisotropic magnetic properties. The first person to make grain-oriented silicon steel was a fellow named Norman Goss, who in 1934 invented a method that alternates cold-rolling and heat treatment of silicon steel to produce a steel with grains lined up in the direction of rolling. The process results in steel with a distinctive appearance known as “Goss texture.”
Since most electrical steel is destined to be laminated, coil stock is also often coated with various non-conductive materials at the factory. Coatings can be as simple as varnish or enamel coating, which are often used for coil stock destined for rotors and stators, to glass and even ceramic coatings.
Only about 1% of the 2 billion metric tons of steel produced in 2020 was electrical steel. It’s an impressive amount, to be sure, but we’re going to have to find a way to keep up with demand for non-oriented electrical steel for hybrid and EV traction motors, as well as the grain-oriented steel needed to build all the new grid components and charging stations they’ll need. Here’s hoping manufacturers find a way to keep the magic going.
Wow. Why is there no one-sentence-definition of steel in this thing? It is not that difficult.
Steel is forgeable (!) iron with less than 2% carbon (a dram more for stainless steel).
Wow, why is there no one-sentence-definition of carbon in this comment? It’s not that difficult.
Carbon is a molecule where most of the atoms are made from carbon.
Now where did you get that Idea? Carbon is an element. Not a molecule.
Because one-sentence definitions tend to be wrong, or at minimum require a bunch of carve-out exceptions in subordinate clauses or parentheticals. Hmmmmmmmmmm……
Can you define dram?
Yes. 0.11%.
A measurement of volume used to mesure whisky ⅛ of a fluid ounce.
Bear in mind though, a wee dram is usually more than it’s made out to be.
I would think that the average reader already knows what steel is…
humanity displaces and moves more than a trillion
tons of raw materials each year,and all of it is moved useing things made from steel
all of that steel is made useing fire,and gears and wheels,hydraulic and mechanical presses,every last bit of which would be comprehensible to people from 150 years ago
and to drive the point ,that not much has changed,
home,the people who OWN the presses are in many cases from the same familys who owned them 150 years ago
A CNC mill being comprehensible to people from 1850 is a stretch. There are an insane number of single use machines from 100 years ago that simply no longer exist.
Lots of rich families from 150 years ago no longer are. e.g. Vanderbilts. Descendants are reduced to giving politicians sloppy verbal BJs on CNN.
Ofcourse not all.
Those that aren’t are completely full of loonies. Not in a good way (e.g. the DuPonts, the Hiltons, the Gettys, the English Royals etc etc).
They wouldn’t know exactly how it worked, but it would be plenty comprehensible and they were already theorizing automatic machines and robots. And are you talking about Anderson Cooper? Lol yeah that is his job
You would be surprised to learn how few steelmaking has changed since the 1870’s. An up-to-date engineer of the time will certainly recognize the open hearth furnaces (which was the main process up to about 30-40 years ago) and might have read on the first tests with electric arc furnaces, which weren’t popularized until the 1890’s.
The Basic Oxygen furnace didn’t exist, as large scale oxygen production wasn’t viable at the time.
The process of making pig iron is essentially the same, albeit on a much larger scale.
All that, and no mention of Metglas? Super low loss amorphous metal used in distribution transformers, among other things.
Also, powdered metal transformers are fantastic for low loss/low eddy currents too.
Metglas has been in operation at its Conway, SC. location since 1989 and is based upon technology developed in the 1970s at Metglas, Inc. (then AlliedSignal) research facilities in Morristown, New Jersey. Amorphous Steel, also known as metallic glass alloys, differ from traditional metals in that they have a non-crystalline structure and possess unique physical and magnetic properties that combine strength and hardness with flexibility and toughness.
Gotta find out more – glass steel.
Nice write-up!
I had steeled myself for a boring treatise on hysteresis but by the end I was transformed.
I’d hoped for an insightful comment but all I got was a silly con.
Seriously, they need to step up the charged comments.
Why are we irresistibly drawn to forge hysterical comments?
Really appreciate these educational articles. Keep it up thanks!!
Article leaves out other “steels”. There is 49% iron, 49% cobalt, 2% vanadium steel. This has been known for over 50 years, but is little used due to expense of cobalt & the elaborate heat treatment & processing (it is “black art” I refer to this as “séance”). This alloy has narrow hysteresis loop, high resistivity, & one other important property not mentioned (high magnetic saturation to almost twice that of silicon steel). Also not mentioned is the villain: CARBON. It imparts high resistivity to the steel like silicon, but the steel AGES to have wide hysteresis loop. This leads to old transformers overheating, & relays sticking in the actuated position. Carbon steel has to be re-annealed every 10 years to retain its magnetic properties, making it not practical for use. Substituting silicon for the carbon eliminates this aging effect while retaining the desirable resistivity-raising effect.
New stuff yay mentions glassy steels (these contain boron). These have “invaded” high-frequency territory, where normally metal-oxides (ferrites) reign supreme. These promise the low losses of ferrite, but high magnetic saturation of metallic magnetic alloys.
There’s also been some interesting papers about artificial taenite in the last year or two, regarding production, materials testing, and tuning mechanical and magnetic properties. The last paper I read was regarding creating slightly cheaper permanent magnets with similar field strength and longevity to rare-earth magnets, where they concluded that the optimal formula for that was about half and half iron and nickel with <1% phosphorous (see patent US 11,462,358 B2).
A fine article about an important matter. However, this statement is wrong:
“…wind turbine generators need magnets made with rare earth metals…”
I could explain why it is wrong.
ChatGPT? We have silicon steel being higher resistance in one sentence and lower resistance in the next.
I’m pretty sure HaD has begun automatically feeding trending videos from the youtube algorithm into chatGPT to generate articles. It’s just a text-based mirror of a certain side of youtube now.
I’m a chemist by education and electrical engineer by trade yet I don’t often think about the chemistry of the components. This was completely fascinating, thanks for writing it.
Unmentioned in the article is the use of steel in major AC transmission lines. For these transmission lines the center of the conductor is steel which is usually wrapped with copper conductors for the outer quarter-inch or so. Due to it being AC current, most of the current flows through that outer quarter-inch. This construction allows the tower supports to be positioned much further apart.
They usually use aluminium instead of copper these days. Much cheaper, and higher conductivity to mass ratio.
Also, while the conductivity for equal cross section isn’t as good, you don’t have to limit yourself to the same diameter as you would for copper at your frequency of operation. The depth for aluminum is higher, after all.
IIRC, one of the cheapest coatings for electrical steel intended for laminations used to involve a simple heat-treating process. I say “simple,” but I’m betting it’s not, as the process has to both anneal the material, so there’s less stress in it causing eddy current losses, and leave a thin insulating layer on the surface.
It’s been years since I’ve done anything with that stuff, but that’s what I vaguely remember.
I worked for a steel company that did produced GOES. To make it, is like baking a cake an you don’t know what kind you baked till the very end. It could a high grade magnetic quality or scrap.