Ever needed a strong yet adhesive-free way to really stick PLA to glass? Neither have we, but nevertheless there’s a way to use aluminum foil and an IR fiber laser to get a solid bond with a little laser welding between the dissimilar materials.
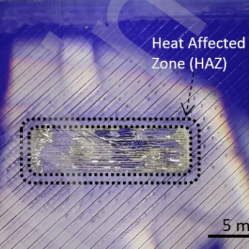
It turns out that aluminum can be joined to glass by using a pulsed laser process, and PLA can be joined to aluminum with a continuous wave laser process. Researchers put them together, and managed to reliably do both at once with a single industrial laser.
By putting a sacrificial sheet of thin aluminum foil between 3D printed PLA and glass, then sending the laser through the glass into the aluminum, researchers were able to bond it all together in an adhesive-free manner with precise control, and very little heat to dissipate. No surface treatment of any kind required. The bond is at least as strong as any adhesive-based solution, so there’s no compromising on strength.
When it comes to fabrication, having to apply and manage adhesives is one of the least-preferable options for sticking two things together, so there’s value in the idea of something like this.
Still, it’s certainly a niche application and we’ll likely stick to good old superglue, but we honestly didn’t know laser welding could bond aluminum to glass or to PLA, let along both at once like this.
So, this is like reactive multi-layer foil welding(*). But, you know, without the reactive or multi-layer parts. Energy supplied by laser instead of chemistry.
A lot simpler, provided at least one of your substrates is transparent to the wavelength of light you need.
They don’t actually say in the paper whether the bond is chemical or purely mechanical. It would be interesting to know what the actual mechanism is. “future work” they say.
(*) Indium Corp’s Nanofoil, https://en.wikipedia.org/wiki/Reactive_multi-layer_foil , also covered by Krasnow’s Applied Science youtube channel.
Has to be mechanical, although except for actual melting and fusing does happen in plastics and organics.
Wonder what the bond failure point is.
Has anyone tried this with a regular fiber laser? It looks like they use a MOPA fiber laser but the pulse time is the maximum that it supports (200ns). With a regular fiber laser (q-switched) at 20W using specs from Raycus the Pulse Width Range(ns) is 120-150 and Max.Single Pulse Energy(mJ):0.66, which is faster and has more energy than theirs (0.3mJ). It seems like it could work.
Glass cover over solar cells in the top of a sensor module?
Hmm, my common or garden UV laser diode engraver goes straight through glass and clear acrylic. I wonder…
Hairspray, all you need is hairspray; like the kind an old lady would use to sculpt a rock hard hair sculpture (e.g. aquanet). It makes it super easy to keep the adhesive layer very thin and even and it washes off very easily with water.
I’m not following. Hairspray on glass with PLA is a very light bond, not strong at all. That’s not what this article is talking about, unless you meant something else.