[Julius Curt] needed to mark acrylic panels with a bit more clarity than the usual way of rastering the surface, so they attempted to 3D print directly to an acrylic sheet, which worked perfectly. The obvious way to do this was to bond the acrylic sheet to the bed with glue temporarily, but another way was tried, and it’s much less messy and precarious.
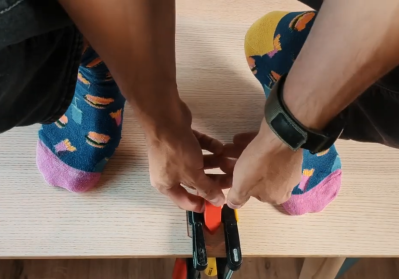
The first step was to create a 3D model which combined a constraining ‘fence’ to contain the acrylic panel with the required artwork floating above. It was easy enough to run the print long enough to build the fence, then pause the print mid-way to add the pristine panel and restart after a quick re-prime and wipe.
There were a few simple takeaways from the video below. First, to ensure sufficient tolerance between the fence and the panel, consider the layer width (plus associated tolerance when printed) and the laser kerf of your machines to ensure a not-too-sloppy fit. Secondly, that hot nozzle won’t do the acrylic surface any favours during travel moves, so enabling Z-hopping is essential!
Another use for this simple technique is to fully incorporate an acrylic sheet within a print by pausing at an appropriate height again, dropping the panel in, and continuing the print. A degree of overlap will lock the panel tight, with the plastic bonding very firmly to the acrylic, as [Julius] demonstrates in the video.
It’s always a delight to see how techniques can combine to create the desired effects. Here’s how to use a color laser printer and toner transfer paper to apply designs to a 3D printing front panel. Whilst we’re thinking about the multitude of uses for hacking with acrylic, what about not doing that and using corrugated plastic instead?
This is a great video, and a good reminder that even though 3d printers have come a long way towards being consumer products that “just work” instead of projects unto themselves, they’re still flexible and “hackable” (for some people’s definition of “hack”). Thanks for posting this!
I once did this with a polystyrene base. Worked great, but the bond I got wasn’t strong enough and the letters started falling off after a year outdoors.
was thinking of something similar to print an etch mask on fr4. print fence plop in fr4, print the layer, take it out flip it over and do the other side. but with rates from pcb mills, its almost pointless.
Not only that, the feature size and clearance you’d get from a 3D printer would probably make it useless for SMD parts, so you’d have to drill holes and be restricted to old TH parts.
Now if someone could figure out a dealer l feasible way to make plated holes, home production of PCBs might actually be interesting again, but I’ve never seen that.
When you only have a hammer…
…then you better start hitting things with it.
This sounds like the way one embeds magnets or nuts or electronics into a print.
3D printing PC on PC plate is better, just set the bed level properly