Not all 3D scanning is alike, and the right workflow can depend on the object involved. [Ding Dong Drift] demonstrates this in his 3D scan of a project car. His goal is to design custom attachments, and designing parts gets a lot easier with an accurate 3D model of the surface you want to stick them on. But it’s not as simple as just scanning the whole vehicle. His advice? Don’t try to use or edit the 3D scan directly as a model. Use it as a reference instead.
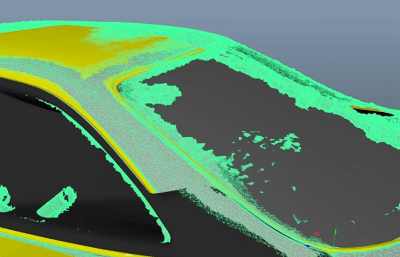
To do this, [Ding Dong Drift] scans the car’s back end and uses it as a reference for further CAD work. The 3D scan is essentially a big point cloud and the resulting model has a very high number of polygons. While it is dimensionally accurate, it’s also fragmented (the scanner only captures what it can see, after all) and not easy to work with in terms of part design.
In [Ding Dong Drift]’s case, he already has a 3D model of this particular car. He uses the 3D scan to fine-tune the model so that he can ensure it matches his actual car where it counts. That way, he’s confident that any parts he designs will fit perfectly.
3D scanning has a lot of value when parts have to fit other parts closely and there isn’t a flat surface or a right angle to be found. We saw how useful it was when photogrammetry was used to scan the interior of a van to help convert it to an off-grid camper. Things have gotten better since then, and handheld scanners that make dimensionally accurate scans are even more useful.
I wonder how effective combining image segmentation AI with photogrammetry would be. You could use the AI to separate the final scan into individual objects.