3D printing is arguably over-used in the maker community. It’s just so easy to run off a quick prototype and then… well, it’s good enough, right? Choosing the right plastic can go a long way to making sure your “good enough” prototype really is good enough for long term use. If you’re producing anything with gearing, you might want to cast your eyes to a study by [Mert Safak Tunalioglu] and [Bekir Volkan Agca] titled: Wear and Service Life of 3-D Printed Polymeric Gears.
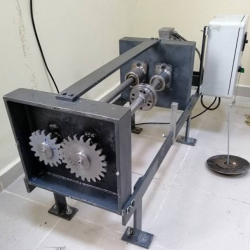
The authors printed simple test gears in ABS, PLA, and PETG, and built a test rig to run them at 900 rpm with a load of 1.5 Nm against a steel drive gear. The gears were pulled off and weighed every 10,000 rotations, and allowed to run to destruction, which occurred in the hundreds-of-thousands of rotations in each case. The verdict? Well, as you can tell from the image, it’s to use PETG.
The authors think that this is down to PETG’s ductility, so we would have liked to see a hard TPU added to the mix, to say nothing of the engineering filaments. On the other hand, this study was aimed at the most common plastics in the 3D printing world and also verified a theoretical model that can be applied to other polymers.
This tip was sent in by [Benjamin], who came across it as part of the research to build his first telescope, which we look forward to seeing. As he points out, it’s quite lucky for the rest of us that the U.S. government provides funding to make such basic research available, in a way his nation of France does not. All politics aside, we’re grateful both to receive your tips and for the generosity of the US taxpayer.
We’ve seen similar tests done by the community — like this one using worm gears — but it’s also neat to see how institutional science approaches the same problem. If you need oodles of cycles but not a lot of torque, maybe skip the spurs and print a magnetic gearbox. Alternatively you break out the grog and the sea shanties and print yourself a capstan.
One word for 3D printing good gears: nylon.
Especially with some filler like glass or carbon fiber
Doesn’t that filler cause excessive abrasion?
Yes, but anyway it’s common to make one gear (the easiest to replace) softer than the other so it concentrates wear. Kitchen mixers often have a metal worm gear cut in the motor shaft, driving a plastic sprocket.
Not that you can get a replacement gear from the manufacturer anyways, but it’s the thought that counts.
“nylon”. This. I wanted to see it against a nylon benchmark.
These days PC and ASA are also pretty common, could’ve been worth it including those as well. ABS has kind of lost a lot of its early days appeal and these days I rarely see anyone mention using it.
ABS is still the recommended material for your Voron or RatRig printer parts. Most users won’t see any difference between that and ASA (unless you’re printing outdoors in full sun or something), so why spend +30-50% more?
ABS not only isn’t dead, it’s the preferred polymer for a good chunk of the DIY community due to being cheaper and easily printable with enclosed 3d printers. It isn’t nowhere near as popular as the other filaments, I’ll grant you that.
Easily printable? Maybe I’m doing something wrong.
I tested ABS with a hotbed between 80 and 120C, nozzle between 24 and 260c. Core XY printer. PEI both washed and cleaned and with PVA. In an enclosure. Printing speeds to crawling mode. I spend more time testing than I did actual printing.
I can’t get it to stick properly. I was printing 24 feet for under chairs to even the load on a larger surface. Round feet, with a 24mm brim. If I did more than one at the time, it would fail. The brim would already warp and lift up when printing one. I set the Z offset lower than I feel comfortable with. Even then it took 1.5 hours to print each due to the crawling speed, or 6 minutes with PLA at top speed (with the 25kg printer shaking). Infill was set to 100%.
That’s why I didn’t even bother trying PC. ASA or PETG might have been better options.
If you print too slow, the first couple of layers will always warp when printing w a warpy plastic.
I don’t even try multiple object prints.
What’s working for me (with polycarbonate).
Moderate speed (50mm/sec) nozzle diameter thickness first layer.
100mm/sec later layers, half nozzle diameter.
I’m working on getting somewhat clear polycarb parts w clear filament.
Early efforts came out white, but tuning flow ratio is helping.
ELEGOO CC.
0.2 nozzle.
As he points out, it’s quite lucky for the rest of us that the U.S. government provides funding to make such basic research available
That was yesterday, and will become less and less true, until everything will be doged down.
Rent free!
Nice to see some real life tests on 3D printed gears.
It would be even nicer if the test apparatus itself was also 3D printed…
There is also very little info on how it works. How do you apply 1.4Nm at 900rpm?
The biggest clue is the weight on the right side of the photograph. It probably connects to a string wound around the flywheel in the middle.
Small calculation: 1.5[Nm] 900[rpm] / 60 [seconds per minute] * (2pi) [Rev -> rad/s] =141 Watts dissipated. This is becoming significant, and probably also the reason the motor speed is so low.
If I were to design such a tester, I would use thinner axles, that can be used as torsion bars, and then simply use two gear sets, one set at each end. By calibrating the torsion, you can set a constant moment. As a result, you do not have to dissipate any power (except for the friction of the gears and bearings themselves), and you can test two sets of gears at the same time. And you will have to test a batch to get reliable results anyway, so testing two at the same time halves the time for the test.
What will provide control of that torsion? Second motor? You will the dissipate that power in your motors. Clutch? You will dissipate that power in that clutch, like in the device used by researchers. It’s standard device used in gear testing. Search for “FZG closed circuit test device”.
the torsion bars themselves.
just imagine two long axles with identical gears on each end. now you mesh those gear two by two, but instead of just meshing them directly, you twist one of the gears a bit so the next tooth meshes instead of the one directly in front at rest.
Now instead of that, just imagine in one of the gears you can force turn the axle on the gear, while everything is meshed.
You’d have gears under constant torsion, but no work done, nor energy being dissipated except the friction of the gears themselves.
Ohh, that’s a great idea! Thanks!
Since you are testing for wear, or failure, it is assumed your “load” gears will wear as well. As wear increases, friction becomes less. Thus you have introduced a non-linear load and an unknown.
No. Torque in the torsion bars does not change with “friction”. (Or at least very little). It does change a bit with wear of the gears, because wear reduces the angular displacement of the torsion bar. But depending on the dimensions of the torsion bar this can be minimized to a small value.
Also, the tests are stopped intermittently to clean the gears and check for wear. And each time the torsion bars can be re-adjusted too. So wear is just a very minor issue. And this method is plenty good for DIY use.
There is more than one way to drown a litter of kittens.
What advantage does your method provide?
Besides extra complication?
Do they even teach KISS in engineering school anymore?
They hammered us with it.
I had a similar dynamometer application, dissipating about 100 watts. I used a brushed DC motor as the load, varying its load on the rotating shaft through PWM. In principle you can capture that load power and feed it back into the power supply driving the motor under test. I tried, but the buck-boost converter I used didn’t have the dynamic range needed, and 100 W was simple enough to dump into a brake resistor load. For testing the full dynamic range (stopped-full speed) you need to feed current sometimes, so I had to use a four-quadrant drive anyway, which starts to make the thing non-trivial but very useful.
You could measure torque through the load current (and speed through voltage, FWIW), but I found it was not very precise, and used a separate torque sensor to regulate the load current.
Not anymore lol. I guess we’ll all have to rely on YouTuber video experiments from now on.
“Not anymore”
What did I miss? Can you elaborate?
From Forbes: “The budget cuts at major research universities keep piling up, as more federal funding is frozen or eliminated, enrollment of international students is threatened, and inflationary pressures continue.”
Don’t know about America, but from experience in the UK I can assure you that universities could focus on their true purposes (teaching and research) for less than half their present budget if they’d simply sack all the bureaucrats, red-tape-generators, and pen-pushers, and if they’d stop with vanity projects like new buildings for more administrators to occupy and sculptural artworks commisioned at great cost all over campuses. In the UK, typically, 70% of a research grant gets swallowed automatically by central university administrations, 30% is all that is left to pay for researcher’s salaries (for the entire research group), equipment purchases, research consumables, travel, expenses, publications in journals which aren’t already signed up to discount schemes… Stop wasting 70% of the grants on administators and you’d find a much more productive university on a much lower budget, even more so when you remember that the administrators tend to act as an active burden and hinderance on progress, meaning that their salaries are not merely being wasted but are actively working against the researchers efforts.
True but partial.
US campus’s have turning into Clubmed like clusters of amusements for undergrads.
That’s a second huge waste center.
Part of the 70%.
All down to students going to college w no business there and no interest in anything but recreating scenes from ‘Animal House’ or ‘Half Baked’.
Easy student loans and stupid kids results in campus’s competing in ‘most fun’ categories, costs spiral.
Might be a doomer joke about how often lately it seems papers even with government funding will lead to hidden results and patents that prevent use by the general public even if funded in part by them.
There is no shortage of publicly funded research that ends up paywalled by parasitic companies like Elsevier. And no, serving up a PDF does not cost $30 or whatever it is they’re charging these days.
Republicans cut NASA’s overall funding by 24% and the science mission directorate by 47%; the National Science Foundation budget by 50%; the National Institutes of Health by 40%; and on and on through every science funding agency in the US. These will be absolutely disastrous for research in the US.
https://www.science.org/content/article/trump-s-proposed-budget-would-mean-disastrous-cuts-science
The paper cited is from a Turkey university, too
I wonder how POM gears would fare on this test. It is an exotic filament though, and kinda difficult to print due to the fact that it doesn’t stick to most of the printing surfaces.
Unless it’s some exotic multi-layer geometry or a thick gear, POM gears might be better made with a laser cutter.
Igus is a quite well known German company and manufacturer of bearings and they sell their own brand of 3D printer filament suited for sliding bearings. Igus is also doing some research into low cost robot arms and gearboxes for such arms.
https://www.igus.com/3d-printing-material/3d-printer-filament
I’d never seen a $360 kg spool of filament before.
Chutzpa!
$390, not $360…
Does the spool play w your balls as it turns?
They kept infill inside the teeth? Wouldn’t you have those 100% filled?
Pictures look like they were 100% infill to me.
my first thought is that these lifetimes around 1E5 cycles are not that impressive, not even usable. probably representative of their aparatus putting too much weight (torque) for the gears they had printed. for example, i used the lowest quality PLA to make a gear in my bowden extruder that lasted 10 years….but i back-of-the-enveloped that and i am getting like 1E4. so in my life, it’s another case where the moral of the story is something “infinitely reusable” actually is only used a very small number of times in reality.
but i still think this is kind of a ridiculous test. 1.5Nm is kind of a lot for a plastic gear. i don’t know off the top of my head all the teeth profiles – involute, etc – but the ones in the photo are clearly the weakest shape for teeth too. i’ve seen a lot of gears with more triangular / shallower teeth, which won’t stress the root of each tooth nearly as much.
and on top of that, 7E5 vs 5E5 cycles…those are the same numbers. the PETG gear may “last longer”, but if you are asking the question whether a plastic gear is durable with that kind of loading, i think the test pretty clearly shows that PETG is as unsuitable as PLA is. if your aiming to spin the gear all day long for months, they’re both unsuitable. and if you’re in fact only going to do a small number of rotations like my extruder, then either one is fine.
once again, just like the meditation on layer adhesion, i think this is unproductive. design your gears around your actual needs. you are going to be trading off torque vs thickness vs lifespan vs tooth profile for gains or losses of 10x or 100x. this 20% or 40% here and there of PLA vs PETG is less than the rounding error. when you’re engineering your designs, you need to know the properties of the material you’re using but you really only need to know within an order of magnitude. if you’re pushing the limits then you probably shouldn’t be using plastic! and if you do use plastic, you’ll have trouble at the margins even if you use PETG.
but by all means use petg — it apparently doesn’t turn into brittle garbage as it absorbs atmosphere :)
Hi, when you say ” you are going to be trading off torque vs thickness vs lifespan vs tooth profile for gains or losses of 10x or 100x” I find this very interesting. Do you have a resource that explains this relationship in greater depth ?
Otherwise, I think that the whole point of making the test extreme (exaggerated) is to say to the commoner that they don’t need to worry much about using up their printed gear. If they’re well designed, they should last long.
no i don’t have any sort of gear guide. my advice would be to try it and see how it goes. the more fearless you are, the faster you’ll learn :)
heh – that’s specifically why i’m always down on these meditations on material or layering hacks. as a noob playing with my printer, i iterate…i think about the things i know about, and then i print out a test object and then i start to think about the things i just learned about. i really think that’s the only way to go forward. even if there was a class where they taught everything i’ve already learned, i don’t think it’d mean much to me if i hadn’t already had all these projects (win or lose) under my belt.
i think people are reading these articles before they get started, and they’re thinking, “oh if i get the right exotic filament, and the right exotic printer, and the right exotic slicer, then my pieces will be strong enough.” it turns into a shopping list exercise, which is itself frustrated by the overabundance of advice.
but even if you get all of the best tools together, you are stuck with finding out what you can get away with, given your process. there’s no shortcut to avoid that experimentation.
anyways, if i don’t expect to be pushing the limits for a design, i typically start with a simple geometry (like for gear teeth, alternating innie- and outie- cylinders) and thin / small parts (like walls with a thickness of 1mm), and then i play with it to see if that’s “good enough.” if i expect to be pushing limits of precision i would read the wikipedia article on involute gears. if i expect to be pushing limits of strength, i will make parts thicker / bigger, and/or i will dream about how to add metal fasteners so that they handle all of the non-compression loads. but it’s always a kind of game to find out “what will i get away with?”
the people who do carefully model everything before fabrication, like professionals at boeing, all started out first by messing around and learning from failure in lower-stakes environments and with less precisely-characterized processes
I guess this is indeed the way to go. Btw, openscad has a very nice library (BOSL2) for gears that picks the best profile / allows for profile correction for the gears you’re designing.
i have the Not Invented Here disease :)
i am lucky to have seen a gear with cylindirical teeth and thought “oh gee, i could do that”, or i wouldn’t even have one self-designed gear under my belt. but after some other projects, i realized, i’m no longer intimidated by mathematically-defined curves in openscad…only took a decade! so if i wanted a better tooth, i would be happily copying math from the wikipedia article :)
Agreed, that is an unusably low number. For multiple reasons.
The study does not seem to indicate sample size or the number of runs of each material. Unless I am completely misreading the study.
Without multiple test runs there is no way to determine the reliability of the data. No way to estimate confidence in the cycle failure number.
Reliability is a statistics problem. Singular data points provide no use in reliability. You can’t draw lines or curves or correct for any unknowns with singular points. Without more runs with different loadings you have no idea just how much your accelerated wear conditions actually accelerated wear.
Additionally they do not list what infill settings they used, nor what pattern. Nothing on chamber temp variables, bed surface finish, or adhesion performance of the test samples. All are important to judge the data.
None of the plastics used are considered by any competent 3D printing authority to be engineering materials in the first place. Their hydrophilic properties alone make them unsuitable to task. Printing in nylon is no longer a huge ask for consumer 3D printers, nor is ABS/ASA.
And 10^5 cycles on a gear is a pointlessly low number. No reliability engineering team worth their salt would accept that going out the door on a rotating assembly.
“we would have liked to see a hard TPU added to the mix, to say nothing of the engineering filaments”
Agreed. I also wonder about the wear characteristics when running 3D printed plastic gears against other 3D printed plastic gears. That’s the condition that I, as a hobbyist, am likely to set up (when/if I start printing gears). A smoother, harder, more heat dissipative metal gear might be easier on the mating plastic gear than another plastic gear would be.
Note: As I’m just wandering into this 3D printing territory, I just may not have seen existing scientific research and/or YouTube level testing of plastic gears wearing on plastic gears. YouTube level would certainly suffice at this point. I’ll be checking around. If you know of something, I’d appreciate a gesture in the correct general direction.
Brilliant. Congratulations. You’ve successfully figured out what the Gear Industry has known ( documented, and proven ) for over 100 years. I.E.; that gear teeth ( even hardened steel ones ) bend, and that some synthetics are better than others for cogged wheels. Unfortunately, none of this testing took into account the amount of stress and fatigue introduced from the absence of a proper Involute Form, much less an accurate one. ( which has a fair amount to do with it, as well ) 3dp gears absolutely have their place. Accuracy, correctness, and longevity are not part of those equations when power/resistance are involved.
A plastic gear meshing with a steel gear might not be the best test, plastic against another plastic one of the same material would be more relevant to most situations where 3d printed gears are used. I don’t deny that sometimes you might mesh a printed gear with an existing metal one already attached to something, but far more often it is the case that you’re printing a gear because you’re also printing the rest of the gearbox it is used in. Plastic against plastic would wear down together, it might reach a stable(ish) point where further wear becomes slower even if significant backlash has been introduced by that point. Also, a further study involving gears spun at both higher speeds and lower loads and lower speeds and higher loads would be good, my suspicion would be that for high load low speed scenarios gears would last a pretty long time except where the load was at perhaps > 50 or 30% of the load which would cause immediate breakage.
P.S. this is a good study, but it is quite old, surprised hackaday hadn’t reported on it before
In mechanical design, you always want one hard part and one wear part.
‘Always’ is only a slight stretch.
The exceptions are, almost always, two hard parts.
Not two, by design, wear parts.
As others said:
Plastic on plastic is more relevant to a new design
Torque was a little high – 9-13 hours doesn’t seem like a lot. Maybe they upped it to keep test short. A repeat test at half the load would be interesting.
The difference isn’t significant – choose petg but don’t go buy a roll especially for gears, buy nylon.
Filled filaments might not work well against each other but against steel it could be a net benefit?
Paulvdh – I suppose a torsional spring would work as well? Probably easier to set though perhaps it would vary too much in use?
Call me pedantic, but some of the comments on testing come across as “Ur doing it wrong”. I don’t test gears, but I do test materials, and have a fair amount of knowledge about academic and industrial research (40 years, in fact). First off, a significant portion of research is done by relative newbies, graduate students guided by their professors, many of whom are developing predictive equations based on theory. The HaD article says that is the case for this study.
When you develop equations and test their validity, you don’t start with high end, high performance materials. You start with easily reproducible materials, in test rigs that have been used before, have a known relationship to (usually) simple mathematical description of physical motion, or (rarely) real world applications. the test rigs are generally previously validated by other people. In fact, development and validation of a new test rig is generally an entire PhD thesis, and represents 3-4 years of laboratory effort. Same for a new predictive equation.
Each research paper you see is likely to have taken the full time efforts of 2 or more people, including people whose names may never appear in the author list or in the acknowledgements. Because nobody wants to look like a failure, you also rarely see negative results, at least not without accompanying good results. The writing and graphs often dance around the data that had puzzling behavior. I spent 2 years off and on testing and writing before I finally learned from an older scientist that the blip I saw in my data had been observed 4 or 5 decades before. He gave me some references to look up, and I found that the answer had only recently been published by a physicist. The article I used had hidden the blip by not publishing their observed measurements for that part of the study. Instead they dropped in the graph of their applied loads and hand-waved their way through the explanations of what they measured. (Though annoying to me, ignoring initial transients is valid when your interest is long term behavior.)
What I dream of seeing is people thinking before they comment on the work someone has published. We drop in for a quick look for our gee-whiz new technology dopamine hit, but it should always sit in the back of our minds that what we see has generally been the work and sweat of years by people who don’t have a guarantee that all that effort may not even lead to a job, let alone the one they went to school to get. It’s great to present an idea of other ways to test, or other materials to use, just remember that the people doing the work had a finite amount of time, money, materials, and energy to get that one result you can see.
As the PhD physical chemist told the story about working 6 months to get his testing set up working for his thesis “It boiled down to one line ‘Care was taken to eliminate bubbles'”.
nothing wrong in pointing out that research is unproductive or unhelpful, or could be better. nothing wrong in pursuing a career, either.
seems like you’re saying that we shouldn’t criticize results or methodology just because someone is pursuing a career. shrug let them pursue, and let us judge what’s helpful or interesting to us.
There’s nothing wrong with you being the judge of what you like, so long as the rest of us aren’t subjected to your stupid comments.
And for Zeus’s sake at least learn capitalisation first.
More like:
Unqualified criticism is unhelpful.
That said.
GP is a ‘Physical Chemist’…(My late dad was trained as a ‘Polymer Physicist’, but found he was demoted to ‘Polymer Chemist’ when he got to the USA…Taught a lot of P-Chem.)
This paper strikes me as coming more from a mechanical engineering prospective.
From that prospective, they should have tested more materials.
Spend a Nickle and hire a post-doc, get an enclosed printer w an all metal hotend.
Experiment setup was no-doubt the majority of the time spent.
Also: Repeat tests for statistical significance.
For context, 7×10^5 sounds like a lot of cycles, but at a sedate 4 rotations per second (240rpm), that’s two days.
Also this is continuous rotation, whereas the stop/start/reverse and changing loadings, and jolts often which occur in real-world scenarios would i’d expect wear faster?
Ok for occasional use, but no more.
No, it’s not. The verdict is that PETG last about 40% longer. PLA does 500k cycles and PETG 700k cycles.
What you actually should USE is whatever fulfils your needs. If you expect your model do only ever need 100k cycles during it’s lifespan, PLA or ABS will give you 5x that.
All the gears performed the same (I only look at the magnitudes).
I said petg when I clicked the article. Im amazed at how easy it is to print with how durable it is, Ive left a few petg parts in my car, in florida, for 2 years now with no warping somehow. Used to print mostly ABS but fighting the warp takes skill and the out gassing is the worst.
Same here. I use PETG for parts in my car engine bay along with bits inside the cabin.
Was any lubricant used? If not I wonder if a bit of oil or grease would have helped at all.
It most likely would have but it wasn’t what they were testing. Once you find the best material then you test lubricants for their effect on it. Will this grease dissolve this plastic, etc?
“generosity of the US taxpayer.”
Yeah that probably won’t be happening anymore. Because all that matters is tax cuts.
“You can write a check or money order, payable to the United States Treasury, and in the memo section notate that it’s a gift to the United States. Mail your check or money order to the address below.”
https://www.fiscal.treasury.gov/public/gifts-to-government.html
Not much of a society if participation in the collective duties is voluntary. Things spin out of control when the only winning move is to not play.
I’m fairly certain that I’ll still be paying taxes this year.
Having said that, what would be a good source to find out about which tax supported research programs are being cut. Is that detail available yet?
Also not much of a democratic society when 51% get on the government tit.
That’s a failure mode of democracy, where the only winning move it not to play.
See also: The UK.
Time to move, employed brits.
You are a resource to be bled dry.
For those of us who prefer real numbers,
The longest lasting gear made it to 700,000 revolutions. That’s not very much considering the load was quite literally only 1ft-lb.
Had a feeling PETG would win. It is pretty wear resistant from my experience(it’s a bitch to sand lemme tell ya). Perfect for making guitar picks too.
This is remarkably similar to my undergrad thesis I did almost 10 years ago, comparing the durability of PLA, ABS, Taulman 910, and a variant of ABS-CF. although I tested at higher loads, 4000rpm and 10*10^6 cycles
It would be neat to see how much smaller a similar strength machined plastic would be.