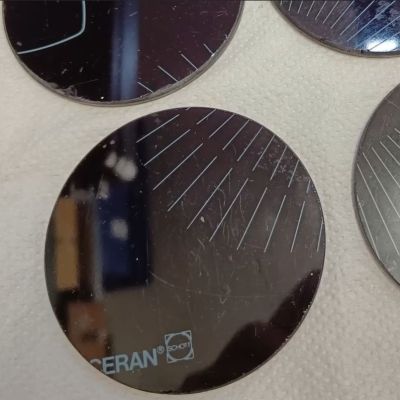
Ceran is a name brand for a type of glass ceramic that has a very low coefficient of thermal expansion (CTE). This is useful for stovetops, but it is also a highly desirable property for optical glass. The natural question: Can an old ceramic stovetop be upcycled into something visually striking? This is the topic of the most recent video in [Huygens Optics]’s series on glass ceramics.
Interestingly, by baking sections of the Ceran glass ceramic for 10 minutes at 961 °C, the CTE can be lowered by another five times, from 0.5 ppm / °C to a mere 0.1 ppm / °C. Following baking, you need a lot of grinding and polishing to remove any warping, existing textures, and printing. After polishing with 220 grit by hand for a few minutes, most of these issues were fixed, but for subsequent polishing, you want to use a machine to get the required nanometer-level precision, as well as to survive the six to eight hours of polishing.
Following this final polishing, the discs were ground into mirrors for a Newtonian telescope. This raised a small issue of the Ceran being only 4 mm thick, which requires doubling up two of the discs using a very thin layer of epoxy. After careful drilling, dodging cracked glass, and more polishing, this produced the world’s first ceramic stovetop upcycled into a telescope. We think it was the first, anyway. All that’s left is to coat the discs with a more reflective coating and install them into a telescope frame, but even in their raw state, they show the potential of this kind of material.
If you decide to try this, and you’ve already cut up your stove, you might as well attack some kitchen bowls, too.
Continue reading “Making Optical Glass From Ceran Stovetops”