If you have an interest in audio there are plenty of opportunities for home construction of hi-fi equipment. You can make yourself an amplifier which will be as good as any available commercially, and plenty of the sources you might plug into it can also come into being on your bench.
There will always be some pieces of hi-fi equipment which while not impossible to make will be very difficult for you to replicate yourself. Either their complexity will render construction too difficult as might be the case with for example a CD player, or as with a moving-coil loudspeaker the quality you could reasonably achieve would struggle match that of the commercial equivalent. It never ceases to astound us what our community of hackers and makers can achieve, but the resources, economies of scale, and engineering expertise available to a large hi-fi manufacturer load the dice in their favour in those cases.
The subject of this article is a piece of extreme high-end esoteric hi-fi that you can replicate yourself, indeed you start on a level playing field with the manufacturers because the engineering challenges involved are the same for them as they are for you. Electrostatic loudspeakers work by the attraction and repulsion of a thin conductive film in an electric field rather than the magnetic attraction and repulsion you’ll find in a moving-coil loudspeaker, and the resulting very low mass driver should be free of undesirable resonances and capable of a significantly lower distortion and flatter frequency response than its magnetic sibling.
Speakers Driven By Static Electricity
If you’ve ever felt your hair lift as you take off a synthetic-fibre jumper, you will be familiar with the phenomenon of electrostatic force. Coulomb’s Law in action, the force resulting from a significant difference in the accumulated electrostatic charge between garment and wearer. Harnessing this force in a speaker would require a charge that varies at audio frequency creating the force on a sufficient surface area to create sound waves, by proximity with a conductive electrode maintained at a constant opposite charge.
The film is held at a very high constant static charge by the application of a multi-kilovolt DC supply, while the electrodes on either side of it are supplied with very high voltage audio frequency in an antiphase push-pull configuration. This push-pull feed on either side of the film ensures that the forces on it are the same when it moves to either side of its center position. If there was a single electrode on one side of the film it would introduce distortion because the half of the cycle when the film was furthest from the electrode would receive less force than the closest.
In the majority of electrostatic speaker designs, the high voltage audio is created using a step-up transformer from a conventional audio amplifier designed for moving-coil speakers. It is possible to create an audio amplifier with an output in the multi-kilovolts, but the designers of such amplifiers face challenges from the high voltage itself and from the availability of suitable devices capable of delivering low-distortion audio at those voltages.
The Drawbacks
Once you’ve reconciled yourself with your speaker’s propensity for sending sound backwards, you then have another problem to contend with. Electrostatic speakers are very directional, so while you can set them up for a perfect stereo image in one spot, a relatively small movement can take you out of it. Various attempts have been made to broaden their spread with differing degrees of success, some manufacturers produce curved panels while others attempt to supply the grid of electrodes from a series of delay lines to create the effect.
Finally in the litany of electrostatic speaker woes, these speakers are not so good when it comes to bass reproduction. Electrostatic speakers will therefore often come with a moving-coil bass unit as a companion to the electrostatic panels, and will usually incorporate a separate bass amplifier and active crossover. Because the radiative patterns of cone speakers and the electrostatics are different, the bass-to-treble balance will vary as you move around the room, further accentuating the sweet-spot issues.
Build Them
Of course, general information about electrostatic speakers is all very well, but this is a site for hardware hackers. You want to see real examples, and maybe have a go yourself. In which case we won’t disappoint you, with electrostatic speaker builds from [Mark Rehorst], [Jazzman], and [Ken Siebert].
The materials required for home electrostatic speaker construction are fairly straightforward, with maybe one exception: the plastic film that forms the moving part. [Mark Rehorst] has an exhaustive list, and makes this important point: “Buying stuff specifically for ESLs is like buying parts for Ferraris. The seller knows you expect to be robbed so they try not to disappoint you“. The world of high-end hi-fi works to different economic rules it seems, so sourcing the same components from suppliers in other industries is the way to go.
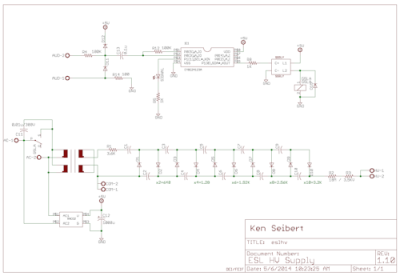
The transformer is an example with plenty of scope for stretching your budget. Audio transformers are expensive at the best of times. Happily there is a cheap alternative; most home builders use standard mains transformers connected in reverse. It has to be said though, as soon as you put a transformer in an audio circuit its performance is only as good as that of the transformer, so there may be some compromises in this component.
Any thin flexible plastic film can make a noise in an electrostatic speaker, but for best performance the thinner your film, the better. 5 micron thick Mylar seems to be the preferred choice.
Once you have your film, it needs a slightly conductive coating. It mustn’t be too conductive: charge must accumulate but not flow away too quickly. Some electrostatic speakers will take a few minutes to reach their maximum volume for this reason, as the charge moves very slowly to fill the panel. Older designs used graphite powder rubbed onto the surface of the film, while more recently they use spray-on coatings intended for static protection in the electronics business.
The fixed electrodes can be made from a variety of materials. [Mark] uses perforated aluminium, while [Jazzman] and [Ken] use a grid of wires, and in one case welding rods. A well known commercial design uses a very large perforated printed circuit board with the electrodes etched in a carefully designed pattern to try to broaden the angle of the finished speaker.
The high voltage bias supply is usually generated with a voltage multiplier chain from an AC transformer, though more recent designs may use solid state inverters. Normally about 4 to 6 KV DC is required for this task.
If you have got this far in an electrostatic speaker build, you should have something fairly special: there is very little engineering that the commercial manufacturers can do to make it much better. Listening to an electrostatic speaker can be something of a startling experience, but beware of superlatives. The hi-fi industry has a special kind of mumbo-jumbo with a whole vocabulary of pseudoscience to make its adherents feel good about eye-watering price tags, and electrostatic speakers are something they have placed on a special pedestal all of their own. You probably won’t be disappointed with your speaker build, but you’ll know it has the flaws detailed above and you’ll put up with them for the bragging rights.
I owned a pair of these types back in the Seventies, they worked well enough, but eventually failed due to internal shorting which seemed to be a common fate with these.
Yes true enough, a really sad fate occurring usually by way of violent discharge from one stator electrode to the other, passing right through the diaphragm en route, burning a hole in said diaphragm, as a result of excessive input signal voltage applied (which was not that hard to do to many units back in the seventies),. Today’s units address that issue by utilizing either an over-voltage input limiter circuit (a few do this now) or adequately-insulated stator electrodes (many now do this approach). Played at low levels though, they were really sonic bliss; at least to my ears, anyway.
How focused can you get these beams? Is this the tech responsible for those highly directional speakers? Is this the same stuff found in ultrasonic ranging boards (Ping)?
my martin logan electrostatics have a curved driver that does a good job of dispersing the sound. they sound great all over my listening room, but the sweet spot, where the sound seems to come to life is about two people wide. I used to have a pair of magnepans that have a flat driver and they were a one person ride.
I have a pir of magnepan 1.6’s and I agree. The sweet spot is VERY narrow. Move your head just 10cm and they sound very different. The sound in that sweet spot can be quite nice though.
Maggie 1.6s here too. I understand the sweet spot issue, but they sound pretty darn good anywhere. I sometimes run them parallel (not toed in) when I’m not feeling persnickety, and they’re a lot less sensitive to placement.
I don’t really se it as an issue. Just find the spot and stay there while you listen. Besides, more directed sound should give less reflections from side walls… I will try to match them to a homemade ripole subwoofer someday as I find the bass a bit thin.
I’ve seen a similar device installed at a convenience store (installing a point of sale system at the time) and it was an ultra narrow beam directly down so only the customer waiting on line would hear the ads playing. It was a creepy sensation essentially you hearing something someone 2 feet away couldn’t.
Those work by ultrasound interference. They essentially modulate the audio on two ultrasound beams that cross in some volume of space, and while travelling freely they won’t interact.Where they hit an object the mutual interference pulls the sound down to audible frequencies, basically making any surface into a loudspeaker.
You’re basically hearing the beat frequency between two inaudible audio signals as they vibrate a surface, because the surface – such as your own earlobes or a shirt collar – vibrates to both sounds and moves as they cancel or amplify each other.
To hear the beat frequency you need some none-linearity, like a demodulation diode or detector. Otherwise it would just be amplitude modulated ultrasound. I think at least part of the non-linearity in this case is in the human ear itself, probably the ultrasound level is quite high.
Doesn’t the second beam do that? Eg you have one beam of, say 40KHz, and one at 40,100Hz, and where they overlap there’s a 100Hz beat frequency, produced in the air. That’s the theory, far as I know. So no non-linear element needed, like you would if there was only one, modulated, beam.
Correct, you need a nonlinearity. The boundary between air and any object in the way provides that, not your ear.
The Harry Potter traveling exhibit has a Voldemort display, when you stand in just the right spot, you are standing under one of these ultrasonic sound beamers. You don’t hear it as coming from the ultrasonic transducers, nor do you hear it directly in your ears. You hear it from any object placed in the beam.
So I heard Voldemort’s whisperings as if they were coming from my hat. I could step back and place my hand in the beam, and hear the voice coming from my hand. With my hat off, my head and shoulders were now the source of the sound. At that point, it sounds like someone talking into your ear from no definable direction.
I stood there for over an hour, watching people’s reactions as they’d hear the whispering.
“Is this the same stuff found in ultrasonic ranging boards (Ping)?”
These days, cheap ultrasonic ranging boards usually use piezos. However, old cameras of this type used an electrostatic ranger (the gold disc):
http://en.polaroid-passion.com/images/appareils-polaroid/660-autofocus.jpg
Are you sure? I always thought this is a piezoelectric transducer.
I looked it up and was fascinated. They really are electrostatic on that model!
Reverse lookup the image, some company bought the old patents.
Thanks for the answer. I remember my grandfather having a couple of old cameras in various states of disrepair… I had access to some high voltage at 8 years old and didn’t know it. Awesome
I think that this article is a bit deceiving about the directionality of ESLs. It is well known that the mentioned “delay line” method works as expected and these ESLs can easily have a better polar response (horizontal only) than any conical speaker. I have built them myself.
Unfortunately most people only get to listen to Martin Logan’s which sound nice but are not comparable in sound reproduction to many of the DIY designs out there. Once you hear them you will never want anything else GUARANTEED.
I had never heard of Martin Logan until I read this article. My knowledge of electrostatic speakers comes from owning Quad ELS-57s in the late 70’s. The best speakers I ever listened to till I heard some of the newer models appearing in the 80’s. You needed a big enough room so that they could to be sited to prevent reflections of walls behind and to the sides. The also needed to spaced about 10 feet. For a couple of years I had the space to do this and had a “sweet spot” about 3 people wide. They were driven by a custom pre-amp and a Quad 405, with a fixed shelf equalizer designed by a friend, which managed to overcome most of the lack of bass. The sound could only be described as transparent.
Thank you for a most interesting article Jenny. You spurred me to do some Googling and I found that Quad still manufacture in Germany, but some of the prices are approaching the eye-watering level. A refurbished pair of ELS 57s are 1.5K Euros. Unfortunately I don’t have the space or the finances to indulge myself like I could then. In any case I doubt that my hearing would be able to appreciate them.
Just noticed I have written ELS instead of ESL! Definitely a “senior moment”.
In the other direction, “73” about 1970 had an article about making a speaker with newspaper and aluminum foil. Not hifi, but it conveys the concept of electrostatic speakers. It was presented as a gimmick, a speaker that wouldn’t be noticed.
Wireless World once had an article about constructing electrostatic headphones. The close coupling to the ear probably means better bass, but I’m not sure I’d want to that high voltage close to my head.
Given that I’ve seen instructions on making an electret microphone, I don’t recall seeing articles about making electret headphones, similar in concept except you give the plate a permanent charge, so no high voltage needed during operation.
Michael
The author calls the delay-line an “attempt” at improving polar response. I can assure you that it just flat out works. I have built them myself. Electrically segmented ESLs can easily have a superior polar response to just about anything else. Mine are flat to 60 Degrees off-axis.
Unfortunately Martin Logan doesn’t build this type of ESL (they are all single segment) resulting in a totally different listening experience. Listen to some segmented ESLs and you will never want to listen to anything else.
What? No discussion of sulfur hexafloride?
Hahahahahaha…I was wondering if someone would bring this up
No infinite baffle to fill with it on these :)
I think that he is referencing Dayton Wright ESLs which use SF6. No need for infinite baffle when you are willing to make something excessively complex!!
I’m afraid to ask how an ESL could use SF6 :)
A quick peak at google says Dayton-Wright XG-8 were 1 meter square (and something deep) boxes, some number of ESLs inside, then sealed and filled with SF6. The patent https://www.google.com/patents/US3778562 makes it seem like you would get better sound by having multiple ESL sheets exerting pressure on the dense SF6 and then the SF6 presses against the 1 meter square diaphragm on the two surfaces of the sealed box.
Interesting idea, really bizarre design but it was the 70’s.
The voltage breakdown of SF6 is much higher than air.
So you can jack up the voltages and therefor output without arcing over.
In the 70’s the Cockroft-Walton voltage multiplier for our small university’s accelerator was filled with it for just this reason.
Don’t breath it in (opposite effect to helium) as it’s hard to get out of your lungs. It’s heavy.
And it’s a terrible greenhouse gas.
I’ve been wanting to do a few pairs of electrostatic headphones for a while (and I would think they would side step the directionality and bass response issues to some degree), having PCBs produced for the plates and spacers. A lot of this stuff will be useful to me. Getting the film has held me up in the past, that and the HV bias supply and my desire to make a fully solid state, transformerless amp design, but maybe I should start more simply. Or even buy the driving electronics on ebay and just see if my earphone design is even any good before I go to all that extra work.
I would assume that they are very “beamy” and thus be a great distance noise maker. The higher up you go the poorer the dispersion is. However they are inefficient at converting power to sound. Titanate discs are quite efficient by comparison. I put one under a guitar string bridge and connected it to a speaker sans amp, it was not of a crystal radio volume. Some guitars have a headphone jack for practice and it’s not amplified.
The failing of these in the home may be caused by the fact they are also electrostatic air cleaners and what goes up will come down along the insulation barriers and start leaking off the HV bias.
If you’re old enough, there were flat passive plastic mesh and film electrostatic tweeters in cheap consumer hifi and stereos. They were mono-polar and carried their own bias which seemed to peter out with little ageing. Not to be confused with the one note Motorola piezo horns of the seventy’s and later.
There’s also ribbon and plasma speakers that may be developed at home with the right wizardry, alas not by myself
You all left an intresting reading and summery of experiences.. I got my first REAL stereo in Highschool when I got a Magnovox Console Stereo. It was a basic stereo but got me interested in speakers. That console had a 10 inch subwoofer, 10 inch woofer, 6 inch midbass and 3 by 5 inch horn tweeter. The compression horn is by far the best tweeter, voice horn speaker ever made. Altech and Klipsch make the best, ( in my opinion) . When the amplifier went bad I took out all the speakers and decided to research speaker enclosures. I built a Subwoffer enclosurer and a 3 way speaker book using the passave crossovers I had to rebuild myself with lots of research. To run my speakers I got into audio components. I got a Marantz Preamp and McIntosch MC2100 amplifier. Thrones turntable and Pioneer Cassette deck. The system worked GREAT. I had to finance it all through my Step Dad, Worked all summer to pay it all off, but it sounded Fantastic. For a high school freshman to have built my enclosures only guessing at the Theile Small peramiters of the speaker specks. I did a great job. I still own that Mcintosh MC2100 and matched it with a McIntosch C26 Preamp.
ELS speakers always fascinated me. Now it’s time to replace my cone, voicecoil style speakers and explore something different. Only drawback Is the ELS speakers require a lot of current and my McIntosch amp has the audioformer output transformer doesn’t put out the high current to make electrostatic speakers dance, produce any loud volume.
I will continue to read as much as I can find.
Actually ESLs work best with an amplifier that can deliver higher voltage. Also, it needs to be capable of handling a mostly capacitive load. It’s the latter restriction that causes the most problems.
Actually ESLs work best with an amplifier that can deliver higher voltage. Also, it needs to be capable of handling a mostly capacitive load. It’s the latter restriction that causes the most problems
About 30 years ago there was a series of articles about building an ESL in the magazine “Elektor”. They advised to use a coating of methylcellulose as slightly conductive coating, which is just wall-paper glue. They recommended a very thin, liquid mixture, thinner than if used for its original purpose.
Another easy and cheap diaphragm coating is liquid dish washing detergent applied with a cotton ball. The conductive ingredient, which practically all dish soaps contain, is sodium laurel sulfate. It gives near ideal resistance and high output but it attracts dust so it’s only suitable if the speaker will be covered with a grill cloth / dust cover.
I use and recommend Licron Crystal ESD but it’s not cheap (over $50 with shipping). Anyone who comes up with a clear, cheap, easy to apply permanent coating and posts how to make it would be doing a great service to the DIY community. BTW, I too can attest that electrical segmentation works astonishingly well.
So like the moving coil speaker is the opposite to the dynamic microphone, an electrostatic speaker is the opposite to the condenser microphone?
Pretty much, yeah. Or maybe the electret mic is a bit closer.
No, condenser microphones need external high voltage, so they are more like electrostatic. I forget about condenser microphones, so I’m not sure if they are exactly the same.
But electrets can be microphones or headphones, they seem like electrostatic except in making them, they re given permanent charge.
Michael
I was thinking of an electret as a charged element moving around between 2 plates. A bit like this. Except in this case sound provides the movement, and the electret provides the charge, other way round.
Must say that i’ve never heard a clearer sound than listening to a pair of those old QUAD firescreens driven by a QUAD pre-amp/power-amp combo. It took some getting used to as every record did sound quite different. I’m hoping I’ll stumble across one or even a pair at a thriftshop one day
I wonder if there’s a magical combination of a heat-shrink plastic that has the conductive properties suitable for a membrane. That would solve the tension problem. I can see web search results for mylar heat-shrink tubing – maybe sheet or roll can be found?
Plenty of DIYers use regular mylar and tension it with heat rather than mechanically. It is pretty common practice.
It is also used quite a bit to rejuvenate old diaphragms which have fatigued a bit and need more tension.
I guess the solution to the phasing issue would be to have the speaker at ninty degrees and port both sides.
I’m not sure how that helps. One side is pushing while the other is pulling, so aiming them in the same direction will just cancel out.
A box with a port is meant to take the sound off the back of a speaker, delay it by 180 degrees, and put it back out the front. It is imperfect because it only works over a fairly narrow range of frequencies, which is why you normally only see this done for bass frequencies.
Lot’s of paragraphs in this article are copy pasted from the kenseib website. I don’t see any clear indication of what was written by the HaD writer and what’s written by kenseib, this is very bad journalism.
Please use author quoting properly, it’s not hard to use single, double or triple quotes or even slanted text to indicate a quoted paragraph. Attribution to the original writers is required.
Thank you
It does not surprise me that this article is almost entirely plagiarized.
Electromagnetic speakers have diaphragms that move back and forth, just exactly like electrostatics. Electrostatics tend to be different in that they generally have much larger radiating surfaces and and much poorer efficiency in terms of turning power into audio. In my audio career I have owned a large set of folded horn speakers that had to near the most efficient speakers ever manufactured, and a pair of electrostatics, that have to be among the least efficient speakers ever created. When you consider a speaker that is just 3db less efficient than another requires double the power to reach the same SPL, and you consider that electrostatic speakers are in the order of 20db less efficient than the most efficient speakers manufactured, you can see why they generally don’t want to loose the back wave. And porting a box leads to all kinds of nasty resonances. Also, because of the very way the electrostatic motor works, the diaphragm is driven over it’s entire surface, while in a conventional speaker the diaphragm is driven in it’s center and depends on the stiffness of the cone and the surround for damping and physical support. There is no reason one could not make a conventional sized electrostatic driver, but it would be ridiculously inefficient. There was a time when electrostatic tweeters were popular, over conventional low frequency drivers. And even my electrostats had a companion subwoofer, and that has a conventional driver in it.
BTW, electrostatic headphones often have acoustically sealed backs. Efficiency is not such a big deal with the transducer is an inch away from your ear and you are not looking for room filling sound.
what about the monsoon multimedia system mm700, mm1000, et al, with esl sats, supposedly?
I should say before I comment that much of the info in this article came from my website (Jazzman’s DIY Electrostatic Loudspeaker Page) and to the extent that it inspires others to take the DIY plunge, I’m OK with that. I would just add the following.
Aside from low bass output, all of the shortcomings historically attributed to ESL’s have been overcome, and the bass output issue too is overcome in modern hybrid designs.
A properly segmented insulated wire-stator ESL is very reliable, relatively easy to drive (predominantly resistive load) and projects polar response that’s even better than most conventional speakers. And they can play to painful volume without arcing.
Additionally, inexpensive toroidal power transformers (about $20 a piece) are quite suitable for hybrid designs (only)– the recommended ones with single 230V windings on the primary compare so well to the ultra-expensive specialized ESL transformers from Plitron and Aplimo that I dare say most people would not hear any difference.
With all the info available on the web, the greatest impediments to building your own hybrid ESL is the practical necessity of active bi-amping it and [most of all] the woodwork. The bi-amping part is really easy but not cheap.
wow,,,, i had a barn find on some aeon i’s,played with them for a few months and was getting really poor if any sound from the panels, so i followed the washing in the shower guide and used a heat gun on low setting super carefully now they both scream…… ESL’s for life…… ;)
I built a pair. They’re fabulous. I run music from my Mac (HD files), send them through a MiniDSP 2×4 processor, and feed the analog output into a couple of IcePower amps. The bass runs off some humongous woofers and a Hafler amp.