For the longest time now, I’ve wanted to build a real, proper radio telescope. To me, this means a large parabolic reflector, a feed horn made of brass sheet, coat hanger wire, and at least for the initial experiments, an RTL-SDR dongle. I’ve done the calculations, looked at old C-band antennas on Craigslist, and even designed a mount or two that would make pointing the dish possible. I’ve done enough planning to know the results wouldn’t be great. After months of work, the best I could ever hope for is a very low-resolution image of the galactic plane. If I get lucky, there might be a bright spot corresponding to Sagittarius A.
There are better ways to build a radio telescope in your back yard, but the thought of having a gigantic parabolic dish out back, peering into the heavens, has stuck with me. I’ve even designed a dish that can be taken apart easily and transported because building your own dish is far cooler than buying a West Virginia state flower from a guy on Craigslist.
Recently, I was asked to come up with a futuristic, space-ey prop for an upcoming video. My custom-built, easily transportable parabolic antenna immediately sprang to mind. The idea of a three-meter diameter parabolic dish was rejected for something a little more practical and a little less expensive, but I did go so far as to do a few more calculations, open up a CAD program, and start work on the actual design. As a test, I decided to 3D print a small model of this dish. In creating this model, I inadvertently created the perfect WiFi antenna for an ESP8266 module using nothing but 3D printed parts, a bit of epoxy, and duct tape.
Designing A Dish
The design of a parabolic WiFi antenna isn’t that much different from the design of an optical telescope. In fact, nothing is different save for the frequency of light we’re looking at. A rule of thumb for optics is that a perfect reflector needs to have a surface finish within 1/10th to 1/20th of the wavelength of light the reflector will be used at. For a visible light telescope at a wavelength of 400 nanometers, this means a parabolic mirror needs to have a surface finish that is perfect to within 40 nanometers. That’s the size of viruses, but it’s still something that can be made with cerium oxide, pitch, and a second block of glass.
WiFi, on the other hand, has a wavelength of 12.5 centimeters, and the surface of a parabolic WiFi antenna needs to be perfect within only a millimeter or two. This is easily attainable with a 3D printer.
To design this dish, I found some old freeware on the Internet that takes the relevant measurements of a dish — focal length and diameter — and spits out XY coordinates of a parabolic arc. These coordinates can then be imported into the CAD software of your choice, extruded into a 3D shape, and exported as a 3D printable object.
It’s Hexagonal, and Therefore Cool
This project was originally just a test to see how I could build a large, easily transportable parabolic reflector. This demands a few design considerations. First, the dish should be composed of segments, and these segments should fit in my car. I decided to build a hexagon-shaped dish, with each sixth of the hexagon composed of a left half and a right half. This makes the individual parts of the dish sufficiently small to fit in my car, and gives me the added bonus of only having to create two masters to pull a mold off of.
Making the dish a hexagon does have one slight drawback: I’m missing 17% of the dish. A hexagon inscribed in a circle has an area 83% as large as the circle itself. However, having straight lines on the outside of the dish simplifies any reinforcement or bracing I would need to build. In any event, this is only an experiment.
Another design consideration is how to attach the antenna to a mount. Ideally, you’d want to mount it near the center of gravity. In the case of something round, this is the center. That’s not a problem for a parabolic dish; we don’t need the center of the dish anyway because it will always be shadowed by the feed horn. Cut out the center bits of the dish, and we have a nice hexagon-shaped hole to serve as a mounting point.
A few quick cuts in Fusion 360, export to STL, and throw it in Cura. I ended up with this:
This is 1/12th of a dish, with another 1/12th of the dish copied and mirrored along the Y axis. No, it didn’t take two days to print a sixth of the dish; I bumped up the layer height and cut down the infill, but it still took about 10 hours to print these two parts. In total, that’s sixty hours of print time and two spools of filament for this experimental dish.
In addition to the 3D printed dish segments, there are a few more parts I need to turn this into a proper WiFi dish. I need some way to mount this thing to a camera tripod, and something to hold an ESP8266 at the focal point of the dish. Here is what I came up with:
The hexagonal piece simply slips into the center of the dish. On the back, there’s a 1/4-20 threaded insert for a camera tripod. On the front, there’s a hole designed for a 6mm dowel, or in my case, a plastic knitting needle cut down to size. I designed two mounts for ESP8266 modules. The first was a simple mount for the very popular and very inexpensive ESP-01 module. The second mount fit the Adafruit Feather Huzzah board, an ESP breakout board with a few neat features including a USB to serial adapter and a JST connector for a battery.
It’s Not Duct Tape, It’s Tape You Use On Ducts.
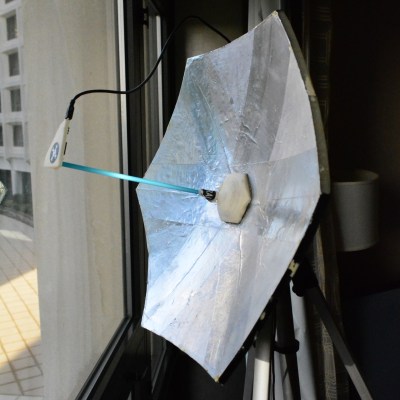
With the parts printed and everything assembled, this experimental dish still had a problem. It was relatively transparent to radio. While I could have used a metallic filament for this build, I really didn’t want to spend that much. Instead, I found a better solution: duct tape.
In the United States, the words “duct tape” has several meanings. The most common, by far, is a cloth-backed tape coated in plastic, a close cousin to gaff tape. This duct tape or ‘duck tape’ might look metallic, but it’s not. It’s also something you should never use on duct work. Don’t put this stuff on an HVAC system.
Instead of the cloth-backed “duct tape”, I’m using the stuff you should use on duct work. This “duct tape” is effectively thick aluminium foil with a pressure-sensitive adhesive on one side. It’s radio-reflective, strong, and thick enough so that it can be burnished smooth. I’m using duct tape to reflect radio waves, and in doing so created the best clickbait headline ever.
Testing the Dish Out
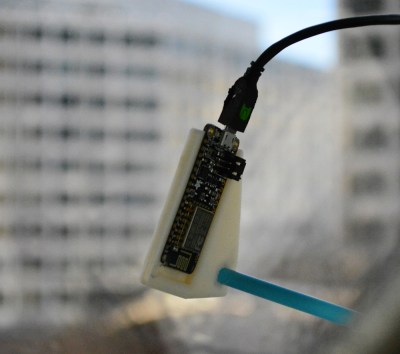
I live in a van down by the river in the middle of the woods, so testing the range of a WiFi connection or the gain of an antenna isn’t easy. Ideally, I would head out to the desert, go to the top of a mountain, and have a friend with a walkey talkey drive away with a WiFi router in tow. The second-best option would be a high-rise in a densely populated city. Luckily, I was in the Washington, DC Hilton a few weekends ago for Shmoocon. This is how I tested my dish.
After the Dishes and Donuts meetup at Shmoocon, I took my dish up a few floors and pointed it out over the vast expanse of townhouses and embassies. The experimental setup consisted of the Adafruit ESP Huzzah, programmed to report all visible SSIDs (with RSSI) over a serial connection. Without the dish, I was able to see about a dozen or so SSIDs. With the dish, I saw about 150 SSIDs at max count. The dish works, and it works pretty well.
The performance of this dish is very good for something that is cobbled together out of 3D printed parts and five-minute epoxy. It’s a 19-inch diameter dish, with an F/D ratio of 0.5. Theoretically, it should have a gain of 18.1 dBi if it were circular, and if the center of the dish was not in the shadow of the feed horn. My hexagonal dish is not circular, and the entire area of the dish is not illuminated, but I should still have a gain of about 16 to 17 dBi. Compare that to a commercial Cantenna at 12dBi, remembering decibels are on a logarithmic scale I did pretty well here!
An Experiment I Won’t Be Repeating
This was originally an experiment to determine if it was possible to build a parabolic reflector that could be disassembled and reassembled easily. Did it succeed? Yes. But there are a few caveats.
My original plan to metallize the dish consisted of 3M spray adhesive and aluminium foil. This was a complete failure. Even though the surface of the dish can be a millimeter or two from perfectly smooth, there were far too many wrinkles than I wanted to deal with. The best solution for a relatively wrinkle-free metallic surface is duct tape.
I still have to properly characterise this dish. I know the gain is good enough, and in theory, it should be well above the common, cheap, commercial cantennas or WiFi patch antennas. To quantify this difference is another matter entirely. I’m open to suggestions on how to do this, but keep in mind all the mountain peaks around my house have trees on top of them. Line of sight is a luxury.
As with all my projects, I’ve put all the details for this project up on Hackaday.io. This includes all the .STL files to print your own. I’d be very interested to see if someone else builds their own 3D printed parabolic dish, even more so if the design can be improved upon. If you manage to print one of these out, please send it into the Hackaday tip line.
Or just solder an wifi 2,4 GHz
Wifi scan before 9 wifis
After soldering 37 wifis
https://imgur.com/gallery/kU73v
I mean an antenna* see the pictures
That looks like a very sub-optimal way to do what you did. You have the original antenna still connected, with coax soldered to the end of it, then unshielded for an arbitrary length. Better would likely be to cut off the original antenna and solder the coax to the feed point, with as close a ground as possible for the shield. Or better yet, just get an ESP8266 module with a U.FL connector.
+1
There is the ESP07 for example, has the same footprint like the ESP12.
Could I get that PCB file and maybe the component values? I’ve been meaning to print one out for my wroom-02, but haven’t found the time to design it yet.
Where’s the duct tape?I mean an antenna* see the pictures
Report comment
On your subject of a real radio telescope; I and many, many others have old steel C-Band? Sat dishes in our back yards collecting dust and generally being eyesores. Most even have electric coaxial driven actuators. Some older people might even remember how they work :). I bet you could see some stars with a 3m dish!
particularly if you dropped it on your head.
“There are better ways to build a radio telescope in your back yard, but the thought of having a gigantic parabolic dish out back, peering into the heavens, has stuck with me.”
Be the talk of the town. Make it look like a giant inflatable eyeball facing the heavens.
Based on the photo, it looks like the tape could do with a bit of attention from a burnishing tool and some elbow grease. This might reduce the scatter and up the gain a bit.
This probably won’t make too much difference, the optical tollerance rule of lambda/40 really only applies where the physical size of the antenna is much larger than lambda. In this application size is commeasurable with the wave length so diffraction effects are going to be significant.
We called that metal tape “100 mph” tape.
We had a similar tape in the 80’s used for aircraft “battle damage”‘ repair. I can’t recall the details at this point. There was actually a course you could take if you were working aircraft maintenance (At Clark we has an old navy F-4 to practice on). Most fixes we learned would make MacGyver proud.
Apparently different from what the US military calls 100mph tape since that is cloth backed. There are a whole host of ASTMs and MIL-specs for it to meet. Metal backed tapes don’t generally meet the tensile strength or temperature range requirements, though they do offer heat resistance up to 200F/98C which is god for some applications.
When in the guard we ripped the soft top on a humv and had 90 miles to go when the rain started. Yep, its 100 mph tape for sure, well for us more like 70, but replaced a near square meter of missing top and no issues.
Why does it call it a “feed horn”? From the photos it seems he put an omnidirectional antenna in the focus of the parabolic reflector. There is no way he can get a 16 dB gain.
whatever, it’s clickbait. Who cares, right?
This. Probably the biggest fail of the project, and an easy one to address.
go on..
I think he is saying that a second reflector is needed in front of the feed. The second reflector can be as simple as a 4 inch curved metal sheet placed 1/4 wavelength in front of the ESP8266 module. Without the second reflector the ESP8266 is going to be in the path of constructive and destructive interference of the incoming and reflected wave. As a result the main lobe gain and side lobe suppression will suffer as much as 6dB performance.
Conductive paint? Graphite?
Or maybe chicken wire without the 3D printed mess? Remember, 2.4 Ghz wavelength is not so small afterall.
But anyone who owns a 3D printer is looking for ways to justify its purchase.
A surface accuracy needed for a reflector is about lambda/30, where lambda is frequency. For 2.4GHz Wifi, this is about 4mm. It would be difficult to get chicken wire to do this, but its easy for a 3d printed part.
EDIT: Where lambda is wavelength.
A wavelength/10 inaccuracy results in only a 1 dB degradation. We can stay within + – 12 mm, a nice 1 inch tolerance.
Lambda/10 is more like a 7dB drop, where lambda/30 is a 1dB from ideal. Big difference. But you’re right that it’s accuracy in RMS. At lambda/30, or even lambda/20 (only 2dB), that’s 11-16mm peak to peak error throughout. That’s still tough to do with chicken wire. If you still you can do it within an inch, you apparently haven’t tried to make anything with chicken wire.
Well, yeah. Fine, often. But there’s so much effort involved SOMEtimes, and with 3dB being 2x pwr, get accurate and you have almost 1-6ft dish instead of two, conjoined, as it were. 2 waya to go. Good, or big. Choices. Sometimes, no matter…
Neat!
You could also consider using copper tape instead of aluminum so it could be soldered at the seams
Out of curiosity, why didn’t you use an offset-feed design for the antenna reflector?
Because.
An ESP-01 isn’t going to shadow the dish at all. Even the Adafruit Huzzah thing doesn’t shadow the dish very much. A normal (as opposed to offset) dish makes design and assembly easier. Just because.
Makes sense, especially since there’s no feed horn on there that’s adding to the shadow.
clickbait rubbish title… awful antenna connection, awful pole in the center, ridiculous reflector (look at commercial antennas, do they give you any hints?)
Brit much?
Maybe their family was crushed by an ill-secured C-band TV dish.
Nothing hugely wrong with this. Nice work. It could be inproved with more complex math and an offset feed. The ESP antenna would be better as a horn with its beam pattern filling the dish area. Currently a lot of the directionality is lost because the small PCB antenna is omni-directional.
The design uses way more plastic than required. RF does not need a solid reflector, just one with small enough holes.
Easier to just go down to the local home appliance and cook store. Pick up the largest stainless steel cook bowl and make parabolic disk antenna. The beam width would be narrower and tight. Working with any kind of duct tape is messy.
or an umbrella
yeah I was just thinking this. A standard wok. or a cheap stainless mixing bowl. A plastic bowl with foil lining. A discarded home satellite dish…
The metal tape required is commonly called Flue tape and is available generally at woodstove supply stores. It’s essentially a very thick aluminum tape with a good adhesive on the back. Peel and stick stuff.
Also used for HVAC duct work
No need to use a tape that has both metal and cloth. The cloth will only make it rough and increase the scatter.
With an omni directional antenna on the module, it needs a second, small parabolic reflector to catch radio waves bouncing off the main dish but missing the antenna to focus them at the front side of the antenna. Transmitted waves from that side will then be bounced to the main dish.
No reason the dish couldn’t have been made round at the edge, with a big enough printer. To save filament use an Isogrid pattern on the back.
Here’s the McDonnell Douglas Isogrid design handbook. Go to the 42nd page and you’ll see the dimensions used for the grid walls and floors used in Skylab.
http://www.sheldrake.net/quarter_isogrid/NASA-CR-124075_Isogrid_Design.pdf
That isogrid stuff looks interesting maybe someone should do something on Hackaday about it!
MechEng student here, thanks for this! gonna study it
10/10 for the title
FWIW, I hacked together a spreadsheet that I used to create papercraft spheres, wherein the chart that was generated was half a gore. It wouldn’t be difficult to alter the formula used to create a parabola if anyone is interested. While it would consist of a (user-defined) number of flat panels, It has the advantage of being able to be (laser?) cut and scored out of flat material, which makes construction and transport a LOT faster and easier. Y’all are welcome to use (and improve) it as you see fit.
https://docs.google.com/uc?export=download&id=0BzsNTZn1VMXeQmFMSy1VbWI5MVU
https://docs.google.com/uc?export=download&id=0BzsNTZn1VMXedUlZcDhqb243dWs
Wouldnt it be easier to just buy a satellite dish? or i dont know get one for free in a scrap yard? This reminds me of 10 or 15 years ago, when i saw a brand new smal (hal fmeter) parabolic sattelite dish on a shop for ~15eur and i bought it just because i thought it would be cool to have that..
And 5 years after, i had problems to get wifi reception down floor, so i thought of buying an usb cable, and instead oh having wifi pen (wifhout external antenna, a black asus 54bg maybe 8 years ago) directly pluged on desktop usb port, i placed it in the focal point of the dish. And i could get a lot better reception.
Of course this wasnt a hell of a hack that i manage, but now i could always think of a french fries drip and hammer it to a parabolic shape, or any other small dot mesh/metal grid. But it is a lot easy and cheap just to buy a high gain antenna..
This is Hackaday, not “BuyOffTheShelfADay”.
I’m currently making ink for woodcut printing out of charcoal. Sure, I could have bought a tub of printing ink at the art store for $20 when I bought the other tools for this, but sometimes I just want to make things myself, just to see if I can, and to have the satisfaction of having proven I can. (And it’s coming along quite well!)
I have done something very similar with a project of mine, but I simply used one of the $50 parabolic grid antennas off amazon. The grid is a vertical polarizing filter, therefore the surface needed to be covered with foil since the integrated ESP8266 PCB antenna is not vertical polarized. I have not yet tried to get patterns off mine because indoors has way too much scattering. To characterize the directivity patterns you need an LOS environment that is free of multi-path obstructions. Separation of 40ft should be should be good enough, but keep in mind that the ground is also a source of multi-path so the DUT antenna and feed antenna should be elevated as high as possible. The feed antenna should also be co-polarized to the DUT antenna. You can try using the RSSI for your data collection, but the resolution can be rather poor and the update rate of the wifi beacons is slow. Expressive does provide certification test firmware that can be used to put the ESP8266 in continuous wave mode. Using CW mode would allow you to use a spectrum analyzer with your feed antenna for more accurate signal strength measurements. You should be able to achieve reasonable characterization of the main lobe from what I have described, but accurate side lobe measurement requires an anechoic chamber or serious multi-path correction techniques.
I wonder if chrome spray paint would do the trick, I assume that has a good metallic component to it right?
“… building your own dish is far cooler than buying a West Virginia state flower from a guy on Craigslist”
What did the rhododendron ever do to you?
Instead of duct tape you should use a mylar/space blanket. This is way less wrinkly than aluminum foil, but it has an higher reflectiveness
Old enough to remember how they worked? ;>)
Nowadays we see Dish Antennas deposited in most vacant lots, but I built a snowsled antenna for use at 2.6GHz to capture and decode HBO using a coffee can feedhorn. Did spend a night hand calcing and cutting the circuit board. Ahhh… the old days. Haha! The non circular edge gives it a neat rustic antique feel.
Since you’re focusing power, not an image, this concern with making the surface specular seems like more trouble than it’s worth.