A wall-mounted, electric car charging station doesn’t sound like it’d require the most exciting or complicated enclosure. This was pretty much the assumption [Mastro Gippo] and his team started out with when they decided to turn what came back from a product designer into a real enclosure for the ‘Prism’ charging hardware they had developed. As it turned out, the enclosure proved to be the most challenging part of the project.
The first thought was to make a cheap, simple prototype enclosure for integration testing. This led them through trying out FDM 3D printed enclosures, wooden enclosures, folded (glued) plastic enclosures, aluminium extruded enclosures, Zamac alloy enclosures, and finally the plastic injection molded enclosure they had been avoiding due to the high costs.
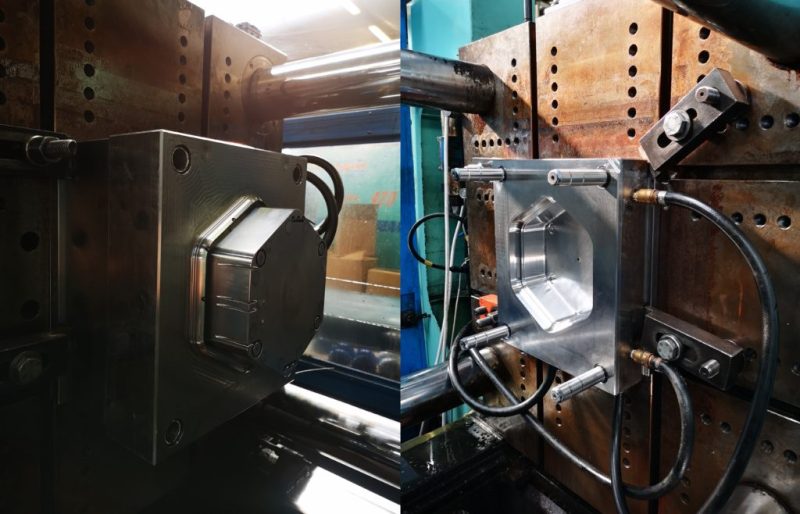
Even if it meant taking out a loan to cover the setup costs, the results really do speak for themselves with a well-integrated design and two really happy looking partners-in-business. It does make us wonder how projects lacking this kind of financial leeway can get professional-grade enclosures without breaking the proverbial bank.
FDM 3D printing is always getting better and with a lot of post-processing you can have one enclosure that looks great, but that doesn’t scale. Outsourcing it to a professional 3D printing company like Shapeways is better, but it’s still not injection-molding quality and if the product is successful you’ll eventually invert the cost/benefit you were shooting for in the first place. Where is the middle ground on great-looking enclosures? Please let us know your experiences and thoughts in the comments.
Kind of idiotic to take out a loan for injection molding with no investors or customers.
Just stuff your crap in an (existing, tested, environmentally/electrically certified) ABS box for the first product..
Yeah, I think they fell in love with the industrial designer’s sketches and wagged the dog from there. I have been involved with projects like that on several occasions.
I’d like to see the wooden prototype. Now that would be different.
I the wooden prototype got impounded by the fire marshall during an inspection of the facility.
Thanks for your opinion! We have both investors and customers, just not enough to pay for a mold. Sorry for not explaining the financial part of the company, it was not in the scope of the article.
How is funding from a loan that different from funding from investors or advance orders from customers? Self-funding can help the founders keep maximum control.
One area in the (low-end of) middle ground is a hand-bendable laser-cut case with screen-print:
https://photos.app.goo.gl/g2mxvoHt6xMArhrY8
Ships flat, and then can be bent to shape by the assembler:
https://photos.app.goo.gl/GGXLpiFQzsGPUWLu7
That’s a good one. Not perfect for every application. But I like it as I like origami.
Those are gorgeous, nice work!
Wow, it’s really beautiful! It’s definitely not watertight and robust enough for out project though :)
with enough silicone, it will be :P
…or duct tape. …or F4 tape. …or epoxy. THERE ARE SO MANY OPTIONS, NOW!
Left-Handed Customers call this product design a non-starter.
As a right handed person its a non-starter for me too. I’m not going to stop playing on my phone just to plug something in…
From their pictures, it seems they kinda lost the hole where the cable/hose would hang. Seems it will work more like a tire pump (?), where you hang the hose in the meter whichever orientation your hands prefer. Or come with a little thingie to be affixed in the wall at the most convenient position ?
It certainly could be designed to be reversible or ambidextrous, but if it was, I think they would have called that out as a point of distinction.
I’d say it’s worth a revision now, or risk lost sales and returns later.
We ditched the cable holder on the latest version, now you can rest the cable on top of the box or have a separate straight out holder
What hasn’t failed to amaze me is that molds aren’t just negative shapes of the part. They’re in themselves small machines with moving parts, their design accounting for shrinkage and the filling dynamics.
I guess unless someone comes up with modular moulds that can be pieced together like Portal test chambers, the chasm will remain as the physical reailty of the precision moulding tool.
We call them ‘sliders’ in the industry. Anytime you have an overhang or undercut (read snap feature) you just drove your mold cost up a factor of 3-10x. It is a very much a black art – even with simulation.
The enclosure for stuff connected to AC mains, or any hazardous voltage level, is oft the only thing between you and jail-time or civil torts.
Most molders (including UL-recognized molders) cut corners. Do not trust molders. Continuous verification and qualification are important, and probably required if your products has NRTL/SCC/NOM certification. If you sell only to the European community – your risk is minimal because ‘CE’ market surveillance is a joke. But if your product is subject to the the typical quarterly FUS audits done in North American states, plastic enclosures are a problem.
Some simple stuff that should be done:
1. tracibility docs for each batch of pellets.
2. melt-flow index testing before and after molding for each batch.
3. flammability tests for each batch.
4. mold dim verification at 60% through 100% of rated cycles.
5. do not allow china molders to ‘dispose’ of worn molds – require return.
My experience with American-based molders is not the same. You get what you pay for I guess. Your laundry list is nice on paper, but not even practical beyond military-grade hardware. You certainly will be in for a shock on costs with that list. Your tracibility is much more easily obscured than you think. 2 is especially onerous. And honestly, if the parts meet dimensional spec, how they got there is immaterial, to you the buyer.
What a lot of injection molders deal with is ‘smart’ customers who know their business better than they do….As an older engineer, I tend to feel less of the need to guide someone on how to run their operation and just care about the results all of which can be guaranteed with good design and material sourcing.
Yea, am a bit of a newbie on the subject of plastic enclosures and other various regulatory requirements. Thirty six years design and manufacturing. Over 100 products successfully submitted to UL, CSA, TUVR, etc per over 25 industrial and appliance and consumer product safety standards for various certifications. Over 50 products that passed CISPR 11, 12, 22, 24, 24, 25, 32, 47CFR15, and/or MilsStd461 after single submittal.
Three of the most expensive and well-known molders located in North America have been the most apt to fail the ISO1133 tests (simply because they could not be bothered to properly condition and pre-heat the injector and mold), and to fail UL FUS audits (mostly because they could not demonstrate material tracibility and were caught using high re-grind percentages).
You seldom get what you pay for, pumpkin. Life sucks, then you die.
Thanks for the info! Feedback like that is part of the reason I’m going open with these articles. Please send me an email with your contact info, so we can get in touch when we decide to export to the USA!
Seems like these two have enough experience to do a series of point/counterpoint articles on the subject.
Whilst I’m a long way from ever getting injection moulded parts done, I’m sure there’s plenty of readers who could benefit from hearing both sides of the story. Can an editor get articles written on this kinda thing?
Also, the cheap simple options for enclosures are also interesting for those of us doing short-run or one-off pieces. More enclosure articles please!!
“mostly because they could not demonstrate material tracibility”
That may be because they did not know what tracibility is. You should have asked for traceability.
Love the keyword “scale” here. Search for videos on how a proper injection mold works and at what speeds. Mind you that even these have a limited shelf life. During my aprenticeship we generally talked 100’000 shots with re-furbishing of the mold. After that, it’s scrap metal. Still this outperforms a 3D printer, whatever the technology.
Another keyword would be “material”. The mold will be built for a specific material in mind as it has to compensate for material shrinkage during cooling. These materials currently outperfom 3D printing materials by far concerning temperature, chemical and structural stability.
(says the tool maker by trade)
You also ‘pack’ a molded part with material at 10,000 psi. No void problems on injection molded parts, unlike FDM. We have some consumer product molds at my workplace that have done a million plus parts. The key is paying upfront to use tool steel and have it properly hardened. Aluminum molds are the minor leagues.
A lot of useful info can be gleaned from plastics industry trade magazines like Plastics News and Plastic Processing Equipment. In addition to advertisements and articles about the latest stuff, they often have ‘case studies’ about problems in molding and how they were solved. One involved an expensive mold that needed frequent extensive and very tedious cleaning, often in as little as several thousand shots. Scratching parts of the mold happened often, requiring more downtime for polishing or replacement.
The company called in a specialist who looked things over and made one recommendation, a slight reduction in injection pressure. Part quality increased, rejects dropped to near zero. There were no problems with flash. The company just let it run, forgetting about cleaning because the good parts just kept coming. When someone thought “Hey, when was the last time we cleaned that mold?” it had gone almost a million shots.
When they’d initially set it up and were having filling problems, their first reaction was to increase the pressure, which was correct, but instead of doing some incremental testing with small increases until it filled all the way they just jumped it up a ways, got a good shot and called it good enough.
Another one in Plastics News was a company that made galvanized steel “chicken boards” for the poultry and egg industry. Despite being galvanized, corrosive chicken waste would eventually eat through them. Then one of the company owners had a bright idea. “What if we made a plastic chicken board that’s impervious to ammonia and water?”. So they did. Sales were super! Until they weren’t. Checking their records they found they’d sold their plastic chicken boards to pretty much every producer in North America. Oops. Invented an indestructible product to sell into a limited market. Some people would throw up their hands and go out of business. Not this company. They’d bought their machinery and molds instead of farming out the production. Their response to running themselves out of a market was “What *other* plastic things can we make, no matter what they are?”. But if you do need plastic chicken boards, they can still make those.
Often, a good middle ground between a fabricated or 3D printed enclosure and custom tooling is to start with an off the shelf injection molded or die-cast enclosure, and add milling machine work and silk-screening. The results will look quite professional, although sometimes you won’t get exactly the exterior dimensions you want or may have to settle for a taller case than the project really needs.
That would have been fairly easy to fabricate out of sheet metal just using non-pro equip ie a $40 bending brake from HarborF etc.
No way in hell will you make a bent sheet metal box with an IP rating of more then 33, at least not without expensive welding.
I didn’t know what you meant by by IP rating, so I gargled this…
http://www.enclosurecompany.com/ip-ratings-explained.php
tl;dr IP ratings are about Ingress Protection. “They are used to define levels of sealing effectiveness of electrical enclosures against intrusion from foreign bodies (tools, dirt etc) and moisture.”
I would have thought vacuum form. I’ve seen guys do it in an oven with garden variety fittings. I know HaD had featured some homebrew rigs. Acrylic just has that modern shiney look that is pretty easy to achieve. PVC with vinyl wrap is another option for clean results without too much investment. But I do see the milled out stock extrusions and powder coated sheet metal routes used often. Submit drawings, decide quantity, pay for what you need, look the shit, if it doesn’t sell you’re out a few hundred. In my opinion, the first round of customers usually are not as swayed by aesthetics.
As an ex mold technician, I’m horrified by the pictures of what’s between the platens… Hydraulic fluid all over the place!? A clamp on the corner!? It well may be a small mold but you wouldn’t think so if it fell… I still love the way Engle machines clamp though. Very elegant. Complicated, but elegant.
thats a lot of time and investment for a custom box to throw some DIN rail mountable internal boxes into when the project isn’t finished.
So not at the stage of emissions testing.
Haven’t yet finalised the components or capabilities.
Lets design a box…
It’s your money (or the banks)
Signs we are heading for a recession – stupid spending
Yeah, that’s what I found the most confusing – “Now that we have our expensive beautiful box, let’s see if things fit in it!”
I enjoy reading the comments, I was aware (through previous HaD articles and comments) of the high price of making an injection mold, but some of these comments make it apparent _why_ the mold making process is so expensive.
A number of years ago I knew a “toolmaker”, but I had no idea of what went into his work!
As a counter-point to some of this discussion. Some years ago I was looking in to the possibility of having injection mould tooling made for parts that would be required in quantities of around 20 per year.
This would not normally be cost effective, we were looking at £20,000 for tooling costs. But the material to be used was Polyimide, and the materials savings compared to machining from solid were significant. Try finding a quote for 75mm x 100mm PI rod, it is £thousands.
I left the company so don’t know if the idea was followed up, they might have decided to stick with the machined glass ceramic vacuum insulator. (where the material was hundreds, and the machining was thousands)
interesting combination of requirements. If it was indeed a vacuum application, I can imagine having a ceramic part without outgassing issues is less of a headache than a formed plastic piece.
Are there injection moldable polyimide materials available?
Yes. Quick Google result: “AURUM® TPI is a thermoplastic polyimide resin that is melt-processable lending itself to fabrication methods such as injection molding and extrusion.
Offering continuous use temperatures to 240°C (465°F), AURUM® parts exhibit low outgassing, superior radiation resistance, excellent wear performance and resistance to chemicals. Components made from AURUM® resin are excellent replacements for metals, ceramics, and other plastics.”
I would probably never have thought of the possibility were it not for the fact that my girlfriend at the time worked as an engieer at an injection moulding company and we were discussing the problem over breakfast.
There are low volume low cost molding techniques, and there are high volume, high quality and extremely expensive molding processes. Pick the right tool for your needs.
The easyest and cheapest for design-prototypes, if you don’t want to go 3D printing, would probably be making a silicon or urethane mold and do some castings. There are a variety of resins available for these processes you can even do “ABS-like” castings in these molds. They only last for around 20 shots, but thats usually plenty for a first design prototyping test.
Yes, I was worried that nobody else suggested this. Vacuum carrying with polyurethanes is the classic ‘halfway house’ step to uneven moulding. It’s good for 10s to low 1000s of parts. That said, for small parts (Ice cream tub or smaller) it’s often not much cheaper than far East injection moulding bit it will be much cheaper than Western injection moulding. OTOH is usually faster and less risky than working in the far East if you don’t already have a supplier you trust.
Uneven moulding?? That was meant to say injection moulding!