Car manufacturers will often tout a vehicle’s features to appeal to the market, and this often leads to advertisements featuring a cacophony of acronyms and buzzwords to dazzle and confuse the prospective buyer. This can be particularly obvious when looking at drivelines. The terms four-wheel drive, all-wheel drive, and full-time and part-time are bandied about, but what do they actually mean? Are they all the same, meaning all wheels are driven or is there more to it? Let’s dive into the technology and find out.
Part-Time 4WD
Part-time four-wheel drive is the simplest system, most commonly found on older off-road vehicles like Jeeps, Land Cruisers and Land Rovers up to the early 1990s, as well as pickup trucks and other heavy duty applications. In these vehicles, the engine sends its power to a transfer case, which sends an equal amount of torque to the front and rear differentials, and essentially ties their input shafts together. This is good for slippery off-road situations, as some torque is provided to both axles at all times. However, this system has the drawback that it can’t be driven in four-wheel drive mode at all times. With the front and rear differentials rotating together, any difference in rotational speed between the front and rear wheels — such as from turning a corner or uneven tyre wear — would cause a problem. The drive shaft going to one differential would want to turn further than the other, a problem known as wind-up.
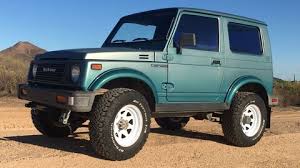
Wind-up causes transfer case components to snap or break. Thus, these systems should only be driven in four-wheel drive mode on loose surfaces, where tyres can slip a little to avoid wind-up in the drive train. Hence, they are called part-time four wheel drive systems, as the transfer case can be shifted to 2WD mode, sending power to just one axle for driving on sealed roads. This avoids the wind-up problem, but means that these systems only really add traction when engaged off-road on dirt, sand, or snow.
These systems also often incorporate a “low-range” gear in the transfer case, which gears down the drive ratio to the wheels, allowing much greater torque to be generated at the tyre and the vehicle to be driven more slowly. This is of major benefit in low-traction situations and when trying to slowly negotiate complex trails full of obstacles and ruts.
All-Wheel Drive, or Full-Time 4WD
Obviously, in some situations, it’s desired to drive all four wheels of the vehicle even on high-traction, sealed surfaces. Thus, a solution to get around the problem of driveline wind-up is to install a third differential in a vehicle, in between the front and rear axles, in place of the transfer case. This center differential can allow for rotational speed differences between the front and rear axles, thus making it possible to drive all four wheels even on paved roads.
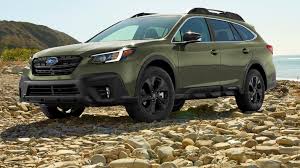
However, this comes with the drawback that the system can only deliver as much torque to one axle as is given to the other, due to the way differentials work. Thus, for example, if the front wheels are slipping, the rear axle will only receive as much torque as the front, and thus the vehicle will not be able to gain traction.
A variety of solutions are used to get around this problem. Off-road vehicles such as modern Land Cruisers and Range Rovers will have a switchable lock in the center differential, allowing equal torque to be sent to both ends when necessary. Alternatively, any one of a variety of limited-slip differentials can be installed in the center differential location, allowing a variable torque split depending on conditions. These systems are less capable offroad, but are less fuss for typical driving conditions. They are most commonly installed in cars intended for use on-road, but in occasional slippery conditions such as snow and ice. They’re also used in performance cars that drive all four wheels to put down power as effectively as possible for faster acceleration and better grip.
Front-Wheel Drive Based Systems
The other type of popular all-wheel drive system are the front-wheel drive based systems, most notably the Haldex type used in many smaller cars. These are installed most commonly in performance hatchbacks from brands like Volkswagen, Audi, and Mercedes. The systems work by having a typical front-wheel drive engine and transmission layout, with an extra drive shaft that goes to a special coupling which is then connected to the rear differential. Under normal conditions, the coupling, containing clutch packs, stays open, sending no torque to the rear wheels. However, under conditions where the front wheels start to slip and spin faster than the rears, the clutch pack is progressively engaged, sending up to 50% of torque to the rear wheels. The clutch pack is designed to operate at various levels of slip, allowing a variable amount of torque to be sent to the rear, usually anywhere from 100:0 front to back to a full 50:50 split. The Haldex system is often mocked and referred to as “faux-wheel drive”, as it only engages under such conditions. However, it is possible to engage the system manually using hacked controllers.
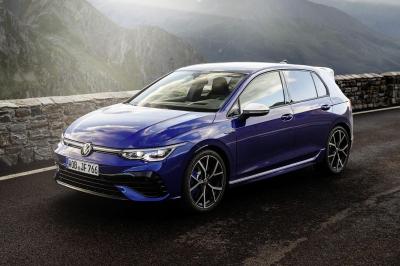
These systems are also used in rear-wheel drive based applications — such as the Bugatti Veyron and Lamborghini Aventador. The concept is the same, but as these vehicles are mid-engined, the coupling is instead installed on the front axle, with the rear axle getting the majority of the torque under most conditions.
Conclusion
Automotive marketing will always rely on buzzwords because it’s simply not practical to explain the mechanical specifics of a given vehicle’s driveline in a 30-second ad. However, armed with this knowledge, you should now be confident to shop for a vehicle that meets your needs based on what it’s got under the frame, not just on whatever fancy words are emblazoned on the badging. Be particularly wary of manufacturers that twist widely-accepted naming conventions to trick unknowing customers, and look at the components installed on the vehicle rather than the marketing terms to get a full understanding of how a given car will perform. Once you know what you’re looking for, you’ll be all the more ready to make the right decision!
Certain Jeep (and maybe Dodge) models had mechanical transfer cases that allowed you to select Rear-wheel drive, Part Time 4WD Low, Part Time 4WD High, and Full Time 4WD. The NP242, for example, could be switched from 2WD to AWD “at any legal speed” without slowing down.
I gotta tell ya, selectable AWD at 70mph is the bees knees.
Then being able to take that same vehicle and use traditional, locked together 4HI and 4LO is just magical.
sequoia also has 2wd -> fulltime AWD at highway speed
center diff only locks in 4low however (stock)
Yeah our old Jeep XJ’s would only let you change when stationary, and sometimes you had to drive a few yards back and forth to get out of Permanent 4WD. That sounds like a major improvement.
I hear simultaneously mechanically awesome and expensive as hell to fix 😂
It would be interesting to see how that works though.
I love this feature on my Jeep. Seems a little odd being able to shift like that at speed, but wow is it ever handy when going into weather causing bad road conditions without having to stop to shift.
Most 4wd toyotas are (or were) like this. Surf/fourrunners definitely were. I had a late 90s surf. That thing was unstoppable. Drive an edge/endura now. They’re diesel here, fast, quiet, techy. Totally souless though. Miss the surf every. Single. Day.
What is a surf?
From https://en.wikipedia.org/wiki/Toyota_4Runner
The Toyota 4Runner is a compact, later mid-size sport utility vehicle produced by the Japanese manufacturer Toyota and sold throughout the world from 1984 to present. In Japan, it is known as the Toyota Hilux Surf (Japanese: トヨタ・ハイラックスサーフ, Toyota Hairakkususāfu) which was withdrawn from the market in 2009.
My late 70’s Subaru GL had this, and it was magic. Cruising along in 2WD getting 35MPG, come around a corner, see the road completely covered in ice, push the ‘4wd’ button on the stick, and you could hear a little whine as the electric clutch engaged the rear wheels, and suddenly the car was very happy to go straight but very reluctant to turn.
I miss that. It was a great combination of economy and traction-on-demand.
In contrast, my jeeps seemed to get poor fuel economy and break driveshafts/front ujoints all the time. (Granted, they were much older cars with harder lives.)
I watched a guy try to tow one of these AWD/4WD Jeep Grand Cherokees in my alley on a two-wheel dolly trailer. He’d get like 20 feet then the AWD would kick in (viscous coupling was locking up, I think), then the rear tires would drag on the ground.
I tried to yell at him from my balcony “THAT THING HAS AWD AND 4WD” and he was just like “I ALREADY PUT THE TRANSFER CASE IN NEUTRAL F*** OFF!”. He then proceeded to drag it another couple hundred feet, leaving strips of rubber randomly, until he gave up and called his “Jeep friend.” The “Jeep friend” shows up and tells him exactly what I told him – I overheard because I went down to throw out the trash – and he comes back later with a full trailer… dumbass.
Some people are just too smart(or angry) to accept help from random strangers.
I am the furthest you can get from a gear head, so I can’t really blame the guy for not understanding what you meant. By “AWD AND 4WD” I’m guessing you meant it had a part-time 4WD mode, meaning it also technically could be switched into effectively a 2WD mode, which is what he should have done if he wanted to tow it on two wheels? Am I close?
If I’m not going too fast, I can flick in and out of 4WD on the fly in my 77 year-old WWII jeep.
And yet in the post-war Series IIA Landy my dad had, the data plate cautioned ‘Make a stop’ before shifting to 4WD.
Progress, eh :)
Certain 3rd Gen 4Runners are similar, and a rear electronic locker was a factory option. I have a 2000 Limited and the progression is RWD, 4WD high open center, 4WD high locked center, 4WD low locked center, 4WD low locked center and rear. The first two are shift on the fly, the latter two need a shift to neutral. I mean, the only other thing you could possibly want is a front locker, which people do, but the utility is questionable.
And trust me, on a 21 year old truck, there can be some cajoling to get the various solenoids to engage. Drive-reverse-drive-neutral-drive-weave a bit…
I was going to say, I had an 01 Ford Explorer that had a switch on the dash for 4×4 auto/high/low. In auto it was rear wheel drive until it decided extra traction was needed. Speed didn’t seem to be a factor as it definitely kicked in 4×4 high on wet highway roads doing 70mph. You could tell when it kicked in because the steering would stiffen up a bit and it would have a noticeable change in handling. I also remember it had a serious bug where if you left in 4×4 Low and shut off the vehicle, it would be stuck in that mode the next time you turned it on. The only way to fix it was to disconnect the battery to clear the 4×4 modules memory. I discovered that on the side of the road once. I really miss that SUV.
Being torque limited by the differential has its advantages. If all the wheels have equal torque (locked differential) and one starts to slip, the torque is distributed among the rest of the wheels in a sudden jerk and this can lead to a cascade effect where all the wheels lose traction and start to slip.
Often especially on ice, you’re driving perilously close to the traction limit anyways, so when one wheel starts to spin free the others aren’t far behind.
If you have a “locked differential”, then all the wheels (on that diff) will turn the same speed regardless of how many of the wheels are on the ground.
This: “the torque is distributed among the rest of the wheels in a sudden jerk” sound like you have a limited slip differential, and when the slip limiting kicks in you get your sudden jerk as power is directed away from the slipping wheel.
Yes, all the wheels turn at the same speed regardless, which means all the torque that is produced by the engine is distributed according to the amount of traction each wheel has.
Consider that the car needs to produce a certain force to push against any resistance, from air resistance or incline, etc. This force is produced by the sum torque of all the wheels, so the sum torque of the wheels is a constant when you’re moving along at a steady pace. If one wheel loses traction and starts to slip, the amount of traction it had – the onwards pushing force it was producing – is now shifted onto the other three wheels which must increase in torque to keep you going along at the same pace.
So, if you are driving along on ice with all differentials locked, and one wheel happens on a patch of ice that is more slippery, suddenly the torque it was carrying transfers to the other three wheels. Maybe one of them exceeds its grip because of the sudden increase in torque and also starts to slip – now the two remaining wheels carry twice the torque and again one of them exceeds its grip on the road, which leaves the one remaining wheel with ALL the torque produced by the engine since the others aren’t contributing, which is four times as much. Given that the car was driving along very close to the limits of its traction anyways, it is likely that the final wheel will also lose grip and the car is now in a four-wheel skid.
In contrast, an AWD car with all differentials open will naturally limit the torque at all wheels to the torque at the wheel with the worst grip. This isn’t useful if you’re offroading, but it’s useful on smooth surfaces where all the wheels have equally bad grip – such as on wet ice or loose gravel.
This part is not correct for a vehicle with fully locked diffs:
“which means all the torque that is produced by the engine is distributed according to the amount of traction each wheel has.”
Torque/Power distribution to the wheels will be constant and will not change (if you have locked differentials), all wheels will continue to receive the same torque/power regardless of the number of wheels in contact with the ground. With all differentials locked, the vehicle will fairly smoothly handle variable traction (grippy, slippy, a wheel completely off the ground, etc.) terrain without introducing additional jerking.
The system you describe, where torque is shifted from the slipping wheel to the other wheels, is one with some sort of the traction control, such as an LSD or viscus clutch device.
From your description I wonder if you’ve encountered a LSD type diff with a “locking” feature, where really it doesn’t get locked, but instead let’s you set the slip tolerance to 0%. These behave similarly to locked diffs, but still require some slippage to engage the LSD, so if a wheels lifts or looses traction you get that jerk from the power being re-directed to the other wheels.
>all wheels will continue to receive the same torque/power regardless of the number of wheels in contact with the ground
Incorrect. I don’t know why that’s such a hard concept to wrap your head around, but it’s basically Newton’s third. If you let one end of a shaft rotate freely, there cannot be torque in that shaft. No action without reaction. A wheel that’s lifted off the ground has no torque as it’s just spinning in the air. This is just the basic mechanics of the situation.
If all the wheels are geared to rotate at the same speed (all locked or no differentials), then the torque that appears at the engine must be equal to the sum of the torques at all wheels. Conversely, if there is X amount of torque produced by the engine, then the sum torque of all wheels that HAVE torque (are not slipping) must equal to X. Here X is the amount of torque at a certain speed that is required to push the car along.
Therefore, when all wheels are gripping the ground, the torque at each wheel is X/4. If one wheel suddenly loses grip, the torque at the remaining wheels jumps up to X/3, and then X/2 with the loss of another wheel, and finally X when only one wheel is trying to pull the car along.
The locked differential doesn’t allow the car to give up and stop pushing along, so the less wheels you have gripping the ground, the more torque each wheel must carry. It’s like having four chains to pull the car along. If one breaks, the load shifts to the other three.
>The system you describe, where torque is shifted from the slipping wheel to the other wheels, is one with some sort of the traction control
I’m describing a system with exactly no traction control.
In order to maintain constant torque and power at each wheel, you must have some intelligent system that reduces the engine output when one wheel drops out of the game. This is obvious, because changing the number of wheels that have torque/power would change the total torque/power of the system.
It seems to be a common misunderstanding that torque/power can exist without going anywhere.
What I think you are describing is the energy stored in the (deformed) tires as they push on the ground, and the torsion energy stored in the loaded axles. When one wheel loses traction, the energy stored in the tire (as the tire returns to it’s regular shape) and axle driving the tire will be released in some way.
I think likely based on that, you could create a hypothetical vehicle[1] which would release so much energy on loss of traction as to make the vehicle jerk and loose traction on the other wheels.
But in real world scenarios, unless your the full-power-clarkson-I-do-not-care-about-broken-axles type[2], there isn’t so much energy being released and the release is more gradual. This would also be coupled with the vehicle slowing down slight making absorption of the released energy fairly smooth.
[1] It can be a spherical 4×4 and in a vacuum if that helps.
[2] If the respond to traction loss is give-it-more-gas, you will likely see even more traction loss.
>the torsion energy stored in the loaded axles
In a dynamic situation, the torque is equal to the stored energy in the axles and wheels. However, that is still not the point.
The point is, you need X amount of torque from the engine to push the car along at a constant speed (=constant power). Therefore the sum of torques at the wheels must reach X. If all the wheels are geared to rotate at the same speed, then they must share the torque X equally. If one wheel is slipping, it cannot have any torque, therefore the remaining wheels must increase their share.
Of course here we’re assuming that the wheels and the engine are turning at the same speed, but that’s just an abstraction.
And torque is actually energy in all cases. It’s a measure of potential energy around a pivot (Nm = Joule). A spinning axle transmitting torque will twist to the amount of torque that it’s transmitting. When the load torque at the other end is released, this will of course release the stored energy, but this is not the important effect. The engine keeps adding more energy into the system, and since this energy is not consumed by the wheel that is slipping (zero torque = zero power), it must go to all the other wheels. Since the speed does not change – they all keep spinning at the same speed – then torque at the other wheels must increase.
This is correct ^^. A 50/50 torque split occurs with a plain open diff. A locked diff/transfer case sends equal rotational speed to each end/wheel, if one wheel has traction and the others are on a slippery surface, the one with traction will receive the bulk of the torque, if there were twisting force sensors in the axels, this one would have the greatest twisting force (torque is a measure of twisting force)
It is a very common error to refer to a locked diff/transfer case as a 50:50 torque split when it absolutely is not.
I have a AWD car with the engine mounted as a front wheeldrive car.
50/50 in normal condition, but if the front wheels start to slip it goes to to a 40/60 bias and then it starts to get realy fun :D
“the rear axle will only receive as much torque as the front”
“allowing equal torque to be sent to both ends when necessary”
I know I’m being somewhat pedantic here, but that’s literally the same. I’ve had this discussion with some AWD/4WD enthusiasts, and it basically boils down to: With an open center diff, the torque between front and rear will always be equal. Yes. Always. If the rear axle is completely lifted, the torque applied to it will be next to zero since the wheels provide zero resistance due to being in the air. Therefore the torque applied to the front axle will be next to zero aswell. Power taking the path of least resistance.
A locked diff on the other hand does not split the torque between the axles but instead provides each with the same amount of torque. The lifted axle will basically waste it all since it doesn’t have any grip, but the one contacting the ground will utilize it to move the vehicle.
Not quite. You can’t “waste torque”. Think of it this way: the torque in an axle is basically the amount of energy stored in a spring, which in this case is a twisting spring. When a wheel is free to spin, it carries no torque by definition, so the torque produced by the engine must be distributed between the remaining wheels which are not allowed to spin freely.
The sum of the torque at the wheels must equal the torque produced by the engine when you’re going along at a steady speed. If one wheel starts to slip, then the other wheels must carry more torque, in other words, they need more traction to keep you going along. This is why, with a locked diff, it’s possible that you suddenly lose all traction in all wheels when you’re driving over loose surfaces or ice.
A locked differential is like suspending a weight from a ceiling by four ropes; cut one rope and the remaining three must carry the weight. If they cannot (not enough traction) then the weight will drop.
Without limited slip the whole front or rear will will have no torque when one wheel slips. Not unusual that both front and rear slip and you go nowhere. Limited slip dfferentials are expensive and not widely available. The vehicle weight is not evenly distributed front and rear. My truck weighs about 5200 pounds with just the driver. But, 3400 pounds is on the front axle and only 1800 on the rear because of engine weight. It’s just about useless in the winter without a half ton of snow or sand in the bed. 4wd or awd is a lot less useful than you might think. My next all-season vehicle I’m thinking helicopter or dirigible but parking could be a problem. I suppose not knowing how to fly could also complicate things.
As someone with a somewhat sensible vehicle – Subaru Forester that is – I can only disagree on the lack of usefulness of AWD.
It keeps you from spinning out on ice, where all wheels have low grip. If you try to accelerate too hard and one wheel starts to spin, the torque lost from that slipping wheel is added to the remaining three and they too might suddenly spin out one by one. With an open diff, as soon as one wheel starts to slip, the others lose torque and you avoid the cascade failure.
By my understanding, Subaru center diffs by default have a viscous coupling in the center diff which, while not actively managed, won’t transmit a torque spike, but rather increase torque in some zero-intercept polynomial-ish relationship to differential speeds between the two outputs. So the “cascade failure” issue really wouldn’t apply to them. It also wouldn’t apply to any vehicle with a viscous-only AWD coupling (such as many early, crude AWD adaptations of FWD or RWD cars, such as a Chrysler Town&Country or Lamborghini Diablo VT) or a soft-lock center diff such as diff+viscous (such as Subaru) or clutch coupling like a Haldex.
Also, I’m really not sure the “cascade failure” of grip is really as big an issue as you make it out to be. I lived a good number of years in states with icy and snowy winters, and have driven vehicles with a variety of drive setups in a variety of low-grip situations. I was lucky enough to have a car with a selectable 4WD system with a locked center and open axle diffs in a sheet ice conditions (early spring freezing drizzle for about 4h, followed by nighttime into a cold snap at 1 locker on ice, but from driving some trucks with locking center and rear in other low-traction conditions, I’m pretty sure I’d rather have that rear locked in really slippery conditions than not.
I would’ve preferred to still have my first-gen forester at that point, but I’d always prefer a lockable center diff to an open one if I was still living in a place I regularly had to worry about road conditions.
It depends which Subaru trim you take into consideration.
They did have many different configurations. Hell, there were even differences between 4speed-auto boxes. 4EAT-ACT (Haldex rear, able to FWD) and 4EAT-VTD (45-55 split diff with Multi-Plate lockup clutch, not able to FWD).
Non-DCCD manuals did have the viscous centre, but the DCCD ones had an adjustable torque split and Multi-Plate lockup clutch.
I was going to say the same about subarus, they can change awd system with trim. I have a 2006 legacy limited, AWD, no traction control and no stability control. I was looking to retrofit some control and which AWD system was best. In the end i just settled for what I have, it is predicable and works.
I own a 2001 Forester with automatic transmission and an electronically controlled clutch in the center diff. I also have a 1997 Outback with a manual transmission and a viscous coupling in the center diff.
I can sometimes tell when the computer controlled system starts to lock the center diff and haven’t noticed anything similar with the viscous coupling, but its a very minor difference and the systems pretty much feel the same. I think Subaru put a lot of effort into minimizing the differences in driver experience between the systems.
I was (or maybe still am) considering a Subaru Forester. What do you mean by “somewhat sensible”?
Get the Forester, it’s a great car all around. I’ve been enjoying the heck out of my 2010 Forester for the last seven years, and can’t recommend it highly enough.
Also, I live in Northern New England, and used to live on a rather steep hill. The Forester is the first car I’ve ever driven that made it up that hill every time, without even slipping enough for me to notice. It just doesn’t seem to notice the weather! (to be clear it’s not invincible, nor is it perfect, but it is a very good car in my opinion – it’s also my fourth Subaru. They have definitely improved over the years.)
The one I have is an import. Forester STi made in 04/2000. It’s got the WRX drivetrain, suspension and brake kit in it, all stock. So turbo EJ20 with 240HP, a bit lowered and firmed up plus the bigger brakes. Hence the “somewhat”, since a regular turbocharged (~200HP) or even N/A (~160HP) Forester would have been the more sensible choice.
Helicopters are easy to park. Tie it to a lamppost and leave the engine running.
I drive a 2012 Subaru STi. It has three limited slip diffs, all different kinds. The car is magic in the winter – with winter tires on, it’s practically like driving in the summer. I pull away from a stop light up to the speed limit at what I feel is a “reasonable” acceleration (not flooring it) and look around me like, where the hell is everyone… only to see the’re still back at the intersection creeping through at 15 km/h.
My 2010 Forester isn’t as well equipped as your STI, but I have had many similar experiences.
2000 Forester STi here, same thing pretty much. Hauling down the Autobahn with a 10-20cm layer of snow on it at some nice and comfortable 60kph, annoying the hell out of people with expensive Audis and Mercedes’ which just can’t keep up for some reason.
Or driving on a twisty snowed in road like on rails while the BMW in front is fishtailing like it’s on a hook.
Given your trim level, your Forester may be a bit more sure-footed than mine (I have a base model US-spec Forester). Still, when driving with reasonable caution, snow is not a problem for mine (the traction control makes up for the open differentials quite well).
The AWD on my minivan seems to do the exact opposite of what is useful. On the slippy stuff it seems like I have to floor the gas pedal to get it to cut in. I haven’t had much chance to investigate if it’s working “as designed” or is worn out. I have been pondering re-engineering it with an electrically controllable unit off a subaru or volvo or something. … However, there is also a solution for electronically controlling wheel slip with the ABS system, like modern traction controls do, which might allow it’s performance to be tuned more to my liking.
That’s just the wrong approach. You’re supposed to take the engine revs way down instead of going all “POWER” like Clarkson.
Unless by “cut in” you mean getting the differential to lock.
Could be worn friction fluid.
The viscous “clutch” is also a service item.
It likely is, I intended to replace ALL the fluids in it when I got it, but so far only got round to oil and coolant.
We made the minivan mistake too. its awd system was made by audi and if the front wheels slipped than the rear should push right? Problem was that since the front wheels had already slipped when the rear pushed you also couldn’t steer. The rear clutch was also ‘non serviceable’ with no drain or fill plug it was only designed to be swapped out as a whole unit. It was the worst of both worlds, actually make driving worse and the v6 unibody awd minivan got worse combined fuel economy than a frame based v8 4×4 truck.
You left out electric AWD systems, which usually have one electric motor for each axle, or possibly 1 up front and two rear. No driveshaft between axles is needed. Some hybrids have a gasoline or hybrid engine driving the front wheels with an electric motor driving the rear, again with no physical connection between the two.
I came here to note this as well. I thought electric AWD would merit at least a paragraph at the end, since the same issues of torque/power split apply but they are almost entirely in software. Fun! AWD electric is actually *more efficient* than the alternatives, and the motors can be sized differently front/rear or even use completely different technologies allowing for more interesting variations. The dual-motor versions of the Model 3, for example, have an induction motor in the front and a permanent magnet synchronous reluctance motor in the back.
In twenty years, folks reading through the hackaday back issues are going to be shaking their heads at how folks could still be discussing ICE in a hacker journal in the year 2021.
“In twenty years, folks reading through the hackaday back issues are going to be shaking their heads at how folks could still be discussing ICE in a hacker journal in the year 2021.”
Goodness only knows what they’ll make of us discussing 1970’s (and earlier) processors, glass-blowing, blacksmithing…
…valves…. tesla coils…
You can have the motors connected in series or parallel, which distributes the power and torque differently depending on their speeds, but the effect depends on running them from the same motor controller – whether it’s a constant voltage/current supply for DC or a VFD for AC motors. The effect works better for DC motors since AC induction motors can’t have too much slip from the drive frequency before they just go wrong.
Article seems to be about the mechanical approaches.
Though I could be pedantic and complain about the lack of one combustion engine per axle too.
That would be a great HaD article, maybe covering
MTM TT Bimoto
Mini Cooper Twini
Mosler TwinStar Eldorado
etc..
Pikes peak Suzuki escudo, for those of us who grew up with a particular Playstation game series.
A heavily turbocharged v6 in each end AFAIK
I saw a proposed hybrid system, I think it was a small turbine air compressor and air powered wheel motors.
That’s used on some city buses around here, though I’m not sure if the air motors are separate or if they just flip some valves and switch the turbine from compressor mode to motor mode. Cool sounding when they pull up to a stop.
I know that was supposed to be humorous, but there was a Citroen 2CV variant ( https://en.wikipedia.org/wiki/Citro%C3%ABn_2CV#Sahara ) made by welding two front ends together in a pushme-pullyou arrangement.
Don’t John Deere MFWD tractors have a traditional rear axle drive with a hydraulic motor for the front wheels?
hub motors seem like the holy grail for 4wd enthusiasts. simply by monitoring current draw and rpm at each wheel, its possible to determine the traction state of the wheel and respond accordingly.
I really liked the coupling used in the 4WD of my old Nissan Xtrail. I think it was electromagnetic?
The intermittent AWD was pretty good, but I could disengage it completely for 2WD in the summer or lock it in 4WD to get away from the constant on/off when driving on crappy roads in winter.
If that thing didn’t lose heat in winter like it was a convertible, I would have bought another one.
Slightly counterintuitive answer here: 2wd with a lockable rear/front diff is actually safer and better for the vast majority of drivers. The reason for this is that when it comes to stopping, you don’t want your drive train to have more traction than your braking system ever. Many AWD cars give the false impression that since the car has adequate control on an icey road that braking will as normal outperform the drive train, in reality the braking will likely fail and cause the car to spin if the driver panics.
The lockable rear diff potentially will provide more power up a steep grade than even a part time 4wd system which would likely see the front wheel spin and the thus all traction fall on the single rear wheel.
Story time: I was driving (in 2wd) in icy conditions going 25-30 on a 40 speed limit road and being obnoxiously tailgated by a tesla (likely a dual or trimotor). Being in 2wd it was very obvious that the road was icy as the rear wanted to shimmy. As We approached a turn into a stop sign I feathered the brakes and felt the car begin to spin, gently pumping the brakes I kept the car under control. The tesla I saw begin to slid completely as the driver had obviously panicked. Fortunately no accident. Anyway the tesla kept about 400 yards between us from then on lol and and only once we reach a major well salted and lit road did the Tesla pass me (which is how I knew it was a tesla)
How do brakes care about your cars drivetrain?
Hint: The only two cases where the drivetrain will actually have an impact on brake performance is when the center diff is completely locked since it will screw with your brake balance and when any diff is locked since it’ll screw with your ABS.
In any other case, there’s zero difference.
Most vehicles with ABS don’t have an accelerometer or anything other than the wheel speed sensors to detect if the vehicle is moving. So once all four wheels stop turning the ABS assumes the vehicle is not moving.
But hit Seattle with a rare snowstorm and the city becomes Street Pinball with drivers who don’t know they need to *get their foot off the brake* to regain control. They were taught “stomp and steer” but in extreme slick conditions where ABS gives up, go back to the old method of a slow but firm pumping on the brake pedal.
Push and if the car is still moving but the ABS pulsing has quit, let off the brake then push again.
If you’re practiced enough it’s still possible with ABS to ‘feather’ the brakes, applying progressively more pressure, timed to reach full pressure right when the vehicle stops. In my old 1977 Mustang I used the manual brake pedal with a vacuum booster. Due to the different pivot point of the manual pedal it had more travel so I could be real smooth with the brake pressure. Anyone else who drove it complained and said my brakes needed bled because they were used to the typical very short pedal travel of power brakes.
Still didn’t help one winter in Grangeville, ID where when I’d stop, the car would slide *sideways* over to the curb and even with the trunk full of firewood, old Computer Shopper* catalogs, and cable chains on studded snow tires there were hills it couldn’t go up and I didn’t want to drive down.
*The tabloid sized ones at least 2″ thick Website? Who needs one?
I think this discussion goes to the next level when you are selecting a homologated road car to participate in racing. Some racing series that favour keeping the cars economically accessible will limit entrants to use the ‘drive train configuration’ that was stock on the car (a good example is the Targa Newfoundland). So taking a front engine, front wheel drive car and mid-mounting a V8 is out of the picture. But where it gets fun is looking at cars that have some sort of dual drive systems with primitive computer control, or electronic ABS. Here you can skirt the rules but implementing your own ‘virtual electronically locking diffs’ by taking over the ABS system to create a primitive traction control without having to change a lot of hardware. Maybe the car has an early electronically controlled centre diff. Some rules permit you to change the electronics controlling this device so long as the device stays the same. Lots of room for hacking potential and all in the name of going faster!
And to the point of some other comments, when electric hybrids come into the picture, the ability for custom control electronics to unlock that little bit extra performance goes sky high.
My best 4WD car was a 4.2l Mk 1 Range Rover with an L.S.D. transfer box.
All upgrades installed by a rich farmer…. nice while it lasted.
I still have the engine and transmission though!
LSD transfer box…
Sounds like a groovy ride or a bad trip.
B^)
And then there’s EVs…
I just got done having the transfer case on my 1967 Dodge Power Wagon rebuilt. It has a 2WD/4WD lever and a low/high speed lever, with a parking brake drum mounted to the back. It’s a divorced New Process NP200 transfer case. Basically the “Part-Time 4WD” section. If you want to see how the drivetrain’s connected on it, I made of a video on the process of taking it off the truck for the rebuild (don’t have a video up yet of putting it back on yet):
https://youtu.be/Cqjq2GVGbBg
There are instruction and warning plates on the dash as to how to properly operate it, in particular not running in 4WD mode at high speeds.
I believe there have been some AWD models that are/were a tranny/differential front-wheel drive and a hydraulic drive to the rear wheels, providing the necessary “slip” for the front/rear relationship, but also still providing torque to both axles to have traction.
Am I wrong here?
It was probably not hydraulic drive to the rear wheels, but a hydraulically operated haldex clutch that couples the rear axle to the transmission…which is pretty much most haldex systems out there. There are also some that are mainly RWD and haldex front.
You’re probably thinking of predecessor to Haldex systems, where it was fully reliant on the properties of the “friction fluid”.
Like those some of VW’s old “Synchro” equipped models had.
Seems like they changed name to 4motion the same time a computer were controlling it.
Fiat likes to use viscous couplings on some of their EU offerings…the Panda is one of them
some commercial trucks have a system like that, but the other way around – rear is the always driven side, front gets to help with hydromotors
Land rovers have been permanent 4wd with a lockable centre diff since 1983 and the introduction of the 90 / 110 later branded the defender, so a bit earlier than the 90’s by a decade or so. Prior to that, it was available but only on certain models of the series ranges.
Range Rovers have been this way since their introduction in 1970, and the military only 101FC forward control first introduced in the 1970’s the same.
Great point! All of the Discovery’s have had AWD, from the start, the Rangies have also been that way, and every single Defender was that way too. The Series were the only ones that were 4wd. The “4wd” lever only locks the LSD in the center, but it’s always active. It’s been this way since the early 80’s. You can get a kit to convert it to 4wd, but why would you do that? It does not help MPG.
There is a subtle difference between the diagrams shown and the AWD system on the Subaru pictured. The diagrams (other than Haldex one) show an off center front diff, this causes a little problem call Torque Steer, since the power paths to the front wheels are different lengths (from different length of axels from the off center diff) power will choose the path of least resistance (i.e. send more power to the front wheel closest to the diff) causing the vehicle to pull to one side.
Subaru have a the front diff in the center of the axle, mounted onto the front of the transmission. This keeps a symmetrical geometry between the wheels, giving very balanced power distribution to all wheels and helps eliminate any “funny business” when you apply power.
I’m a big fan of Subaru in general (my daily driver is a very modified Legacy GT) but the “Symmetrical AWD” marketing campaign never seemed legitimate to me.
I just can’t imagine that the difference in torque transfer due to unequal axle lengths is ever significant.
AWD isn’t quite able to replace 4WD yet. And it’s not like 4WD is hugely simpler, the modern ones have some complicated electronic and mechanical features to them. The more extreme the conditions the more user control is preferred, and that leans usually towards a 4WD system.
I have a fairly convenient 4WD setup on an old Chevy Colorado Z71 pickup truck. It’s not versatile enough to be a good rock crawler. But I can select between 2WD for driving when I have traction and lo/hi 4WD for off-road or extreme conditions (mountain snow). The rear diff locks up automatically when the amount of slip between the wheels becomes too great, avoiding that scenario of one wheel spinning with no traction while the other is stopped. It’s great for how I drive, but that level of automation is a compromise and because I can’t control the behavior on-the-fly it prevents me slowly driving over rocks with one wheel in the air. Because I’ll not hit that threshold driving slow and a wheel will spin fast and the lock will clunk into place jerking things while in a precarious position.
For a car or crossover SUV that doesn’t have much ground clearance, hands down AWD is the best option in any practical scenario I can think of. The newer ones with some electronic controls are even better, you can let them be automated then flip through some modes under more demanding conditions.
I bought a Colorado ZR2 a few years ago just so I got the e-lockers on the transfer case, front and rear differentials. Haven’t had to use them all at the same time, but it felt like good insurance (been stuck a few times off pavement and it’s not too fun when you’re not expecting it).
AWD isn’t supposed to replace 4WD. They have very different use cases, that’s the whole point.
And then there was the 2CV Sahara.
Why not have two engines?
https://www.hemmings.com/stories/2016/06/02/is-citroens-2cv-4×4-sahara-the-most-innovative-off-roader-ever-built
Newer EV designs (Rivian, I think) take that a step farther and just put a motor on each wheel. In the best of circumstances all the speed-matching and torque juggling is done in software. Of course you just know that someone’s going to extend that to six wheels or more…because why not?
https://www.youtube.com/watch?v=yzwM8KE2L3I
Yep, its the Rivian that has 4 independent motors. I’m curious about various control strategies an EV with 4 motors might use to emulate the differentials in a mechanical system.
The ‘dumb’ way is to look for speed differences between the pairs of wheel and compare that against an upper bound. Slightly smarter is to consider speed differences between the front and rear tires.
A little smarter than that would use steering angle as an input and use that to determine what the upper bound should be.
Then really smart would be to use motion sensors in the chassis to get a chassis vector, body roll values, etc and use all that to figure out available grip.
Maybe suspension data could also factor into such a system but at what point does the complexity become unmanageable?
This has been something I’ve been curious about since, if you’ll excuse the pun, EVs started gaining traction.
Some years ago I read about and in-wheel electric motor.. to be used in configurations of two or four. Would that still only be called 2wd and 4wd?
There is a difference between a “viscous fluid clutch” and a “clutch with non-Newtonian fluid”.
Years ago, a man was describing his Lada Niva to me.
As English wasn’t his primary language, I left with the impression that the driver could select either Front Wheel Drive, Rear Wheel Drive, or Four Wheel Drive, as well as High/Low ranges. But I misunderstood, I thought selecting which axle to drive would be a nice option.
people are always telling me how the AWD on my Subaru works, or how awesome it is. i always have to point out how the A only has one leg and a tail, and that means something totally different.
My 18 Ecosport SES is, 4WD. Amazing in snow and with torque vectoring, it’s a rally SUV in the twisty turns. Hugging the turns. I noticed that it’s front drive most of the time. Go for it, or off road, the system is activated. I have yet to see the limit of my SES! Friends of mine have a Honda crv, another has a journey. With the journey not sure how to keep going, and the Honda being a CVT, it was heating up pretty good. Just like my friend’s Hyundai Kona. So glad Ford decided not to use a CVT
Why is the Haldex system “often mocked”? If I understood its explanation correctly, it takes the choice out of the hands of the driver. But for your average driver who just sees a vehicle as a tool to get where they need to go, the Haldex seems like a pretty clever solution to the problem to me. But I’m no gear head, so I’m probably misunderstanding.
Because haldex is almost digital. You can switch it on or off without any limitations, but if you need some other torque ratio then it starts slipping like the clutch. When it slips it generates heat and it can burn down, therefore the operational time is limited in such scenarios. Therefore you can’t use it on off-road or constantly asymmetric conditions for example when you put chains only on 2 wheels.
The choice is taken out of driver hands by the controller software, it is a design decision, not property of the haldex.
My R32 skyline is an oddball. Without power, it is 100% rear wheel drive. The center differential uses an electronically engaged multiplate clutch to transfer up to 40% power to a front differential. Later generations (R33, R34) adjusted the torque bias to provide some torque under all conditions to the front wheels and retained electronic control to send more torque forward in response to a loss of traction. The control unit for the ATTESA AWD system in my 92 looks positively alien compared to “modern” car control computers. https://photos.google.com/share/AF1QipNwfU-kY3CD-0w6HjRZ0Ql3BVcTGdAjgYkOLg4oNgf1YdrYGNWPFZlNIL8Mh_aKIw?key=T1YwTzVUNEluNG1Fa0RNNmE2WlRGeTZDUmlZYVhR
There is a lot more to the various systems out there. Jalopnik had a pretty decent deep dive on the subject complete with SAE definitions for the various classifications of AWD/4WD systems.
https://jalopnik.com/how-all-wheel-drive-works-a-ridiculously-detailed-tech-1846233533
I had a 1998 Mercury Mountaineer with AWD. A planetary gear differential was at the input of the transfer case with a chain drive down/left to a viscous coupling driving the front axle. It had limited slip differentials in both axles. IIRC the setup has very slightly different gear ratios to front and rear so under normal conditions the viscous coupling’s input and output speed is just a hair different. That shortens its lockup time and keeps some torque to the front at all times.
With the V8 it could spin all 4 wheels on dry pavement if I really got on it, wouldn’t spin them for very long before it’d get traction and *go*. Snow didn’t bother it. Just go and keep going. I only got stuck with this system once, and that was in a Sport Trac with a full drivetrain transplant from a 1998 Mountaineer. I drove up on some snow that had been bulldozed into a pile and the wheels sunk in pretty deep.
Sold it for $1000 when it had 230000 miles on the odometer. Replaced it with a 2007 Expedition EL. That thing has a much more complicated setup with a rotary switch for 4 low, 4 high, 2WD, and Auto. Auto claims to be like the good old AWD but all it’s doing is auto switching between 2WD and 4HI, quite clunkily and audibly. It’s not too fun when it engages in a turn. It works but is nothing like the always there smoothness of the zero-electronics-that-could-fail 1990’s AWD.
i had a Wagonner 80 V8 4WD, is unstoppable, kicked off many new toyotas , and everything is easy to solve and cheap , not as luxury as new vehicles but is a beast to enjoy.
A cheap alternative to a limited-slip differential that’s used in modern cars is simply to apply the brake on individual wheels that lose traction, forcing at least some torque to be sent to the other axle. This requires some form of computer that can guess when a wheel has lost traction, and individually addressable brakes.
It’s even used on 2wd cars as traction control.
That’s basically just ESP (or anti-spin) at work.
Downside is that in a long session of slippery driving could overheat the brakes, but it is cheaper since it’s just augmenting the existing ABS system.
Almost everything Land Rover made for about 20 years was full-time AWD with centre lock you could engage at any speed – basically anything with the LT230 transfer case.
The SAE (Society of Automotive Engineers) has released a standard SAE J1952. This defines the meaning of the different types. They do not use 4WD, 4×4, … but only AWD. The available definitions are part-time AWD, full-time AWD and on-demand AWD.
You can find most information back on this site without having to pay for the standard: https://www.theglobeandmail.com/globe-drive/culture/commuting/taking-the-spin-out-of-all-wheel-drive/article4314186/
If all companies adapt or don’t adapt to the standard is of course another thing … .
” The clutch pack is designed to operate at various levels of slip, allowing a variable amount of torque to be sent to the rear, usually anywhere from 100:0 front to back to a full 50:50 split. ”
Sorry but this idea of a fixed split numbers should – in modern AWD systems with real-time controlled clutches – be removed out of our thinking. With decent controls methods, you can go from practically 0:100 (high front wheel slip) and 100:0 (rear on ice) in fractions of a second.
Reasoning in available torque capacity on the rear and the front is more meaningful than thinking in torque splits.
Not a hack, but an informative piece. Thank you Lewin.