When you’re just learning to sketch, you use graphite. Why? It’s cheap, great at training you to recognize different shades, and most of all, it’s erasable. When you’re learning, you’re going to make mistakes, and un-making them is an important part of the game. Same goes for electronics, of course, so when you’re teaching someone to solder, don’t neglect teaching them to desolder.
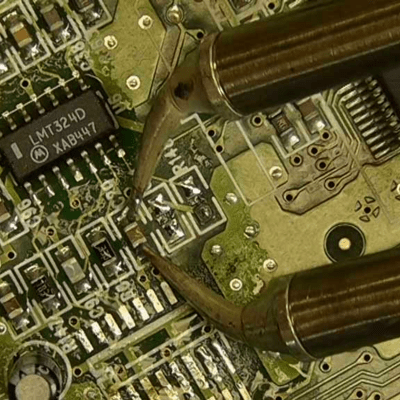
We could argue all day about the best ways of pressing the molten-metal undo button, but the truth is that it’s horses for courses. I’ve had really good luck with solder braid and maybe a little heat gun to pull up reluctant SOIC surface-mount chips, but nothing beats a solder sucker for clearing out a few through-holes. (I haven’t tried the questionable, but time-tested practice of blasting the joint with compressed air.)
For bulk part removal, all you really have to do is heat the board up, and there’s plenty of ways to do that, ranging from fancy to foolish. Low-temperature alloys help out in really tough cases. And for removing rows of pinheaders, it can help to add more solder along the row until it’s one molten blob, and then tap the PCB and watch the part — and hot liquid metal! — just drop out.
But the bigger point is that an important step in learning a new technique is learning to undo your mistakes. It makes it all a lot less intimidating when you know that you can just pull out the solder braid and call “do-over”. And don’t forget the flux.
Just going to leave this bit of genius here: https://hackaday.com/2017/04/03/have-you-ever-tried-desoldering-needles/
I have tried them with little success, I thought they were a brilliant idea but in practice I have had a hard time getting them to work and in one case, the needle that fit the pin was too large for the hole and blew out the plating
Yeah! I had that one on my list as well, but I still haven’t tried them.
To clean out the holes from the capacitors on my 2001 motherboard I just used old resistors. Cut the lead of the resistor off and hold it a pair of needle nose pliers while you heat it up and push it through the plugged hole. Then continue heating from the back side as you pull it through to clean out the hole. And repeat if needed.
A soldering station with tweezers is a good start. Some brands offer pretty large attachments, so you can easily heat all the pads of an SOIC and even dual row headers all at once and pull the parts away. Of course, a good IR soldering station comes in pretty handy too, as it tends to heat up more locally, compared to a hot air pencil. A little board preheating station can be nice too, if you have a multilayer board where the massive copper layers pull away and spread lots of heat from the area you want to rework.
Funny enough altough i use smd 0604 parts, I am using a rather big point on my solder iron with a angled flat side. It transfers heat way faster an more precise. To remove a resitor, I apply some flux and heat up both sides at the same time, having sharp tweasers at hand to grab the part of the solder point when molten. Works like a charm. And for through hole, desolder needles are awesome. Sometimes i first melt the pin and bend it straight with a small flat screw driver. Only electrolites on motherboards are a pain to remove due to the heat loss on the massive ground planes.
Old leaky Smd electrolites I always twist of cold while pushing them against the pcb so the pad stays on the pcb. Try it with an old pcb first to get get hang of it.
Ps. Why are my comments always flagged as moderated? Cookie setting?
Using a larger tip to heat up the whole component is a nice trick I use a lot myself.
And in regards to one’s comments getting flagged for moderation is fairly common for longer comments.
It though also seems to trigger on certain words and phrases, but I have yet to work out a pattern. My own comments tends to get flagged on a regular basis, especially the longer ones.
A moderation system that is biased against long comments is a real concern to me. Long clear detailed explanations should be encouraged! This is Hackaday, not twitter or reddit!
as far as I can tell, they have a Beavis&Butthead AI which stops at words like “holes”. “Hehe, he said ‘holes’! Look, he’s ‘using a rather big point!’ I’m gonna use my ‘big point’! hehe
In truth, partly this. It was a lot worse about a year ago when they clean-slated the weights in whatever trained algorithm they use. Tons of legitimate posts went to spam, where we had to fish them out. It’s still not up to pre-2020 levels of accuracy.
It would be a huge amount of effort to switch over, but community moderation can work well. Not like on Reddit, that’s too easily gamed. The system on Slashdot has worked pretty well for over 20 years. Some people who got sick of Slashdot forked it into Soylent News a few years ago, so using a similar moderation system doesn’t have to “turn hackaday into slashdot” which I think we can all agree we probably don’t want :-)
Is there somewhere we can talk about this instead of hijacking a thread about desoldering? I heard that once upon a time Hackaday had forums :-)
The main trick that I have learned for both soldering and desoldering is that you can never have too much liquid flux. Flux is one of those things that you can “get by” without until you start doing fine work or having to do very much rework, then it is indispensable. As a consequence, many newbies don’t learn its power or they think of “flux” as that cheap paste crap. I recommend get some of those syringes of liquid flux as soon as possible even if they are a bit more expensive.
Figured out that solder won’t bond to aluminum (because of the oxide layer?) so you can use those common aluminum tweezers.
You can solder to aluminum, at least I’ve seen tips for doing that. And yes, it’s the oxide that is the problem.
I have NEVER been able to solder to stainless steel, regardless of temperature, flux, solder (tin/lead/silver) or mechanical treatment (scratching).
One tip that I ALWAYS use is to take some new solder and first add to the existing bond. This not only adds flux but also helps to make the existing solder easier to heat up. Of course I like to have a mix of the dreaded “lead” solder. Call me old school and unsafe if you wish. But this method works without fail.
It’s the lead free I dread working with.
Also fluxes, you can get liquid flux in a pen form too, much easier to get delivered and to store than truly liquid stuff. Pick a rosin flux or a no-clean one, others are too agreesive and may damage the copper of the PCBs.
with small smd components I usually add a huge blob of solder which covers the whole part at once, which can then easily be shifted.
Leadfree solder is actually more harmful to you.
Because of the higher soldering temperature, flux is burning/evaporating faster and in bigger amounts. And breathing in the flux vapor is the most harmful thing happening when you handsolder at home, without proper air filtration. Of course, if you hold the leaded solder between your lips, or don’t wash your hands after handling the leaded solder, that might build up to some lead intake over time. Usually you don’t solder hot enough to evaporate the lead in the solder and breath that in tho.
Of course, the leaded solder has other issues when the electronics end up in landfills, third world country “recycling” operations or aren’t properly disposed in other ways…
Might want to read up the soldering/rework on SMT ceramic caps. Basically don’t try to use a soldering iron on larger size caps as thermal stress can crack/weaken internal layers. Use a hot air tool as it warms up *both* the board and cap together so you won’t have a point source of heat.
https://www.murata.com/en-us/support/faqs/capacitor/ceramiccapacitor/mnt/0001
The Chinese hot air + soldering tool I bought was cheaper than the usual $100 solder station. and it has been work fine for the past 4-5 years. No excuse for not buying that if you are doing any serious electronics.
I have one those 30$ jobs from the usual suspects and it’s fan based not pump
Its been in use for like 6 years now and only occasionally the little reed switch to sense its base gets stuck
Get hot air its so useful (hot melt glue, heat shrink and solder)
If you do get a desoldering station for through hole work regular maintenance is the key to success. If your tip gets pitted replace it. Replace the filters regularly. Lubricate the o rings. Clear out the nozzle with the proper tools and of course empty the solder collector.
Solder suckers DON’T WORK. Use the desoldering braid, it wicks away the solder when you heat it, much more effective.
Works fine for me the only reason I use sick is to clean up whatever didn’t get sucked
Solder suckers work well on through-hole components, particularly the suckers with an electric pump pulling air through a hot hollow tip.
Yup. I’ve had really good luck with a Hakko 808 desoldering gun, even with plated through holes. Just put the tip over/around the pin and melt the solder, pushing the tip flat against the board to get a decent seal. Then engage the pump to suck away the molten solder. The trick for plated through holes is to wiggle tip around in a circle so the pin is constantly moving around within the hole when you suck the solder away. This makes a significant difference and seems to help prevent bonding for the same reason as successfully gluing things together requires parts to be held still so the glue joint can set.
It wicks away “most” of the solder leaving a layer held by capillary action. A “good” solder sucker is much better. Cheap and small solder suckers are the ones that “don’t” work.
Gee, I’m quite distressed to learn that the one I used for 25 years on my job, all that time, didn’t work.
Now, if you mean those silly irons with the rubber bulb on top, I might agree with you. But my Pace, as long as I kept the tip clean and replaced the filters, worked wonderfully.
It’s all case-by-case. You can do a lot with a “silly” iron under the right circumstances, and with a properly maintained tip. They’re great on single-sided boards, and awful on multi-layer. A really big problem is the high melt temperature of lead-free solder. I have trouble with that even with my regular Hakko 888. Just adding fresh 63/37 solder helps a lot.
I think the spring-loaded Soldapult style toys are much sillier; they don’t even add heat to the joint.
This is funny. I’ve heard people adamantly insist that the spring-pump suckers don’t work. Which is somehow like insisting that a hammer doesn’t work. There’s a little technique — it doesn’t do the work for you — but you can make it work with practice.
For me, I’ll heat up the region, get it nice and flowy, then pull the iron tip out to the corner of whatever pad/joint so that it’s still hot but the iron isn’t in the way. Then put the schnozzle right up to the joint. Don’t be afraid, it’s made of a high-temp plastiic. Make as good a seal as possible and fire away.
To be fair, it can be fiddly. You can never seal it down just right, and if your soldering-iron-hand slips a little bit, you can cool the joint back down before you suck. But it’s so much easier for undoing through-hole parts that it’s worth the practice. (IMO, etc.)
I know Al Williams has one of those nice / expensive solder sucker irons and he thinks I’m a savage with the manual pump.
If you get one with a silicone tubing tip, it’ll seal perfectly. My Engineer brand sucker works great.
Funny. I’ve tried desoldering wick and never got it to remove any useful quantity. Since I use one of those springloaded suckers which is far from ideal, but works the once a year I need to desolder something.
I learned about ChipQuick about ten years ago and it’s really great. Basically it’s a low temperature alloy (indium based) that you melt into the solder joint, forming a eutectic that melts at about 100C. You can use a heat gun to melt the treated joints and pull out the part. You can easily remove multi-pin DIPs and SMD packages with this technique.
The only small downside is that it mucks a bit with the tinning on the soldering iron tip, but cleaning it and applying fresh solder brings it back right away.
If you try it and like it there are other cheaper versions of this alloy that work pretty much the same.
Cheers.
@Alan – Please tell us more about the “cheaper versions” – I looked at ChipQuick SMD1 and it costs about 16 US$ for a few grams of alloy.
Step one – never ever use sharp conical shaped soldering tips like in the article illustration. Soldering is all about heat transfer, the more surface area you can slap on the part the better. Flat or concave mini-wave tips are your friend.
Worked exclusively for years with conical and chisel tips – because that is all I (and my employer) had. Bought a “knife” tip one day to try it out, and have not looked back!
I now use it all the time where I would once have swapped between conical/chisel depending on the job.
I’ve tried de-soldering braid, ChipQuik and solder suckers (not very expensive ones mind) and thought that they are all hard work. Using all three seems to help me, but I often still warp or char the PCB with the hot air trying to get parts off.
Solder braid works great when you have the right stuff. When old braid gets tainted or oxidized, it doesn’t work very well. Chemtronics is my favorite with flux in it, everything else I tried doesn’t work well. I use different widths too depending on the size of the component.
Do you add flux to your solder braid? Makes it pull even better.
I have used Flux to enhance the dry stuff, but the fluxed chemtronics usually works without problems. Good idea to share…
Don’t know about compressed air but I always blow thru the holes to get the solder out when changing through-hole parts. Heat up the hole (adding solder to fill it) and then remove iron and blow…
Don’t have your bare feet under the board holder while doing this though…
This is off topic but I’m wondering what drawing software is used for the first image
It’s not software, it’s Joe Kim, our Art Director. He’s awesome.
Very much so – the retro graphics here are great!