Toolchanging in 3D printers is no longer something from the bleeding edge; it’s going mainstream. E3D has a high-quality kit for a toolchanger and motion system, our own Joshua Vasquez has shared details about the open-source toolchanging Jubilee design, and just recently Prusa3D formally announced the Prusa XL, which promises toolchanging with up to five different extruders.
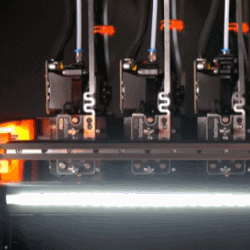
It’s safe to say toolchanging on 3D printers has stepped to the front, but what comes next? What kind of tools other than extruders make sense on a 3D printer?
First, let’s explain what makes separate extruders such fantastic tools. Being able to change extruders on-demand during a print enables things like true multi-material printing. Printing in more than one color or material will no longer be done by pushing different filaments through a single nozzle, which limits a print to materials that extrude under similar conditions and temperatures. Toolchanging means truly being able to print in multiple materials, even if they have different requirements, because each material has its own extruder. That’s a clear benefit, but what about tools other than extruders?
3D Printers Have Often Been Modded To Do More
Cutting tools and lasers are two common 3D printer retrofits that seem to be likely candidates for toolchanging, but they are not without their own issues. Lasers require eye protection and ventilation, and cutting tools create troublesome dust and fragments. Nevertheless, over the years we’ve seen quite a few 3D printers modified into light-duty laser cutters, or converted to CNC engravers. It doesn’t end there; we’ve seen an extruder that embeds copper wire into prints, and even printers turned into through-hole soldering machines.
As clever as these are, some are really just repurposing a 3D printer into something else, and the results have little or nothing to do with the business of extruding plastic to create objects. But others do seem aimed at genuinely enhancing the 3D printing process by adding new capabilities, and could make worthwhile candidates for tools in a toolchanging 3D printer. But which ones make practical sense?
The Best Tools Might Be Ones We Haven’t Seen Yet
The most useful tools are likely to be ones that help a 3D printer do its work better, or more efficiently. For example, E3D have made a pretty solid case that a cutting tool as a secondary processing step can add real value to 3D prints under the right conditions.
Another example of enhancing prints is ironing, which uses an extruder’s nozzle to smooth out the surface of prints. It looks fantastic when it works, but as that link explains, reliability and results can vary. Perhaps a specialized tool, designed specifically for ironing, could smooth prints more reliably and efficiently than an extruder nozzle? Such a tool might even be useful for embossing prints, as well.
A more ambitious task would be a pick-and-place tool that can drop hardware like nuts or magnets into a print while it’s in progress. 3D prints that contain captive hardware would no longer need a human operator involved; a boon for using 3D printers in a manufacturing role.
Of course, the possibilities aren’t limitless. A tool will be limited to a certain size and shape, and a 3D printer’s frame and construction will also play a part in what is feasible. For example, a cutting tool requires the machine to press the tool into the part being cut, but no such force is required to move an extruder when 3D printing. A machine’s capabilities may limit what is possible to do with a given tool. But the enthusiasm with which hackers have pursued things so far makes me suspect that there’s much more where all that came from.
Do Tools Besides Extruders Make Sense?
Maybe robust and open toolchanging won’t just be bringing multi-material printing to workbenches. Perhaps its real contribution will be the way it continues to enable the kind of enthusiastic experimentation hackers have displayed for modifying 3D printers, and lead to things we haven’t even seen yet. In the meantime, extruders seem to be enough to worry about.
What’s your experience with toolchanging? Are things like pens, lasers, and cutters on a 3D printer just gimmicks, or can they actually enhance and improve the job of creating useful plastic parts? We’re listening, so let us know what you think in the comments.
I would love to see extruder with a thick and thin nozzle. Fast print, but accurate surfaces.
But this might be challenging for the slicer
This was my first thought too.
Challenge for the slicer for sure, but some already do every-other, fat-infill layers. You’d also like to calculate when swapping up to the thicker nozzle makes sense, given that toolchanging itself takes a few seconds.
(I got tired of swapping nozzles, so I have a 0.6 mm printer and a 0.3 mm printer. At least that’s my excuse.)
Slic3r PE had those settings since atleast 2019, you can choose different extruders for support, infill and outer surfaces. And you setup nozzle diameter in extruder settings.
CEL-Robox in the UK made one of these. The single filament version had two nozzles 0.4 and 0.6 on a common heat block. The nozzles were offset so a small rotational angle would swing the nozzles into and out off position. The it was a Bowden system so there was a system of valves linked to the rotation to switch the opening of the plastic to each head. There was also a complete head manually changed over available with two separate Bowden set ups and had two nozzles on the head that could have two different filaments fed to its own nozzle. They still shared the heat block. The nozzles were offset so the heat block assembly could be rotated to bring the selected nozzle into position. The software was proprietry and after the valves failed and a whole new head (read expensive) was purchased, and they failed. I stripped it of electronics (pity it was using 32Bit ARM in 2016) I rebuilt it as a standard single nozzle, marlin-octoprint-cura set up to rescue. The original system had great ideas, but over-engineered. Reliability will be tool changing’s greatest challenge. Look up my Robox Rescue on Hackaday.
I’ve still got one, functioning as a single nozzle printer. The nozzle you’re not using still gets hot, and cooks it’s filament into solid carbon, if you use the other one for too many hours straight. Bad design.
Cura can do this. I know, because I build it many years ago when multi extruders where still very experimental.
No idea how to configure it exactly in the UI, but the backend most certainly can do this fine.
Pick and place. Really want my future Pusa XL to pick and place.
I really want my future to have a Prusa XL.
B^)
I’d like to see a rotary nozzle with a little IR LED tied into the trajectory planning section so that it’s pre-melting the surface of the previous layer right before the next layer of filament hits it.
Same. There’s 1 research paper that tries it and it increases layer adhesion significantly.
Nice Idea ! I was searching but I didn’t find that paper. It looks very interesting to improve layer adhesion during printing. Any clue in where to find that paper?
a perfect tool would be an inkjet head or uv print head to print color onto layers or other markings
which could allow you to spray some industrial inks or other coatings on.
Or a release-layer for supports.
Or UV resin and a UV LED.
Pick-and-place would probably be geometrically unfavourable (risk of crashes when picking)
But a simple part dispenser to drop one or two different parts on-demand seems very do-able.
Either dropping nuts into hex/square holes, or a heated head to place threaded inserts.
The question isn’t really what *might* be useful – almost any tool you can think of would be useful to someone – the question is, what tools would be useful to *anyone* doing 3D printing?
The original hype was that 3D printers would become a kind of push-button appliance like a Star Trek replicator, and for that, yeah, you’d need multiple materials and finishing steps and so on. But the reality is that they’re not that, they’re just another workshop tool, albeit a very versatile one. IMO, adding special-purpose tools is like adding a hammer attachment to a saw: just because two tools are useful doesn’t mean there’s any value in mashing them together. What makes a better 3D printer is if it does better 3D prints.
To that end, I can maybe see the point in multiple nozzle sizes. What could make a big difference would be a 5-axis printer (with appropriate slicer support); if you could print 90° overhangs, that would really open up the possibilities for designing printable parts.
Sorry, that was meant to be a general post rather than a reply to the above…
Yea, the lets add a swappable milling bit devices all looked to be nightmares. We had a nice one at the makerspace for a while. Too many places to get dust into.
Printers just don’t have the mass and rigidity for milling well. Better to add printing capability to a mill.
Liquid injection to fill in regions with resin / calking
This please… I think it might be much more efficient and might produce a stronger part to extrude a perimeter and then infill with some sort of adhesive compound like an epoxy or a resin. I would think it would be much faster as well. Also seems like you could produce a mold and then fill it with plaster, latex, or something. Think of what it would do for a lost wax casting process.
Random idea: If you can print a mold, then why not be able to fill it while you print it? In fact, you could go beyond the idea of traditional molds (where you make one mold to create multiple parts) and instead incorporate (perhaps multiple) molds into a larger printed assembly, filling them as you go.
Initially, I was trying to envision a part where you might need rubber-like seals added, but then I realized that this problem is perhaps already addressed by printable flexible filament. Still, there may be other materials that are more easily deposited as a liquid (or slow-hardening goo) instead of a fast-hardening goo.
Another use case might be creating complex-geometry ceramics. For instance, if you want to make a ceramic chain, you can print a chain mold and fill it with clay as you go. You can then fire it up, and ideally the clay will harden enough before the mold material fires away to give you the desired result.
You could also make parts that are pre-filled with a gooey material where there would be no way to put that material in there after the part is made. Not that I think this is a great idea; it’s just kind of like a sailboat in a bottle, except the bottle is solidly closed.
All those ideas are great for niche 3d-printers for (food safe) candy, like a chocolate egg with 3 different fillings and a dropped in hazelnut in the core.
I’d like to drop ball bearings in some voids to make parts heavy or magnetic or maraca-like. A tool to dispense steel bits would be fun.
Dispensing blocks to support overhangs could take the place of some support structure. Much faster to drop a stack of little cubes vs having to print them, and less wasteful.
Ooooh, a sand-filler.
There’s the printer with the printbed that automatically add supports via some elevation system. It’s similar, but a bit more rigid and variable than dropping blocks.
I like this a lot – what about lost pla casting though?
Imagine a (ceramic, clay, silicate, ?) paste extruder that could print a core at the same time – Instant access to complex cores.
We had an intern doing an project like this, with printing silicon molds and filling them with a 2nd specially designed nozzle for the silicon extrusion. It was pretty great. I found it a shame they never tried to productize this.
you could probibly do an automatic threaded insert installer.
resin injection, to reinforce load bearing parts head would mix and inject epoxy or uv curing resin to fill the voids in the infill.
cutting laser for adding precise details to roughed out areas, adding texture, selective annealing, cleaning up edges, etc.
I built a JUBILEE printer, with 3 tools, I like to have simultaneously 0.4/0.6/0.8mm nozzle to launch a design without changing nozzle. And the capability to have 3 different filaments in 1 time is so usefull. During a hackathon I could switch between thin detailed 0.4mm print to a raw big 0.8mm print instantly. I’m planning to have other kind of tools like ASMBL (light milling) to “finish” the prints and a plotter. Another interesting use is to have 1 tool printing PLA and another in PETG to use it as support filament, stick just a little between the 2 and suport remove is a pleasure :-). https://www.lesimprimantes3d.fr/forum/topic/43356-mon-imprimante-3d-jubilee-toolchanger-protocreation/?_fromLogin=1#replyForm
Ihave many ideas for crazy but possible heads. Airbrush, Dremel, laser, soldering, sowing, foam cutting, scanning, plotting, stichting, microscope…
The Jubilee system mentioned is exploring options around this concept – I saw a demo where they had an extruder, a digital microscope and a couple pipet tools and used the “printer” as a sort of DIY lab automation platform. There’s a lot to think about when you start considering the 3d printer more as a platform for programmable motion rather than just a digital manufacturing machine. Tool changing is an essential part of a lot of automation and manufacturing processes so I think it’s a natural evolution of the home digital fabrication tool.
I worked on a 90s wax 3D printer than had a fantastic planer attachment that not only smoothed out the surface of each layer but allowed for layers to be removed and reprinted- it definitely wasn’t a tool-changer kind of tool as it was the length of the build plate but it changed my idea of what a 3D printer could do.
Some straightforward ones I can think of: alternative material infills either as a removable support (like wax or sand) / for strength (resin, silicone, etc), pick and place for nuts+ parts/ in general, immaterial processes- heat/UV cure and subtractive processes. Maybe something that could manipulate the buildplate/fixture to somehow reorient the part or use it just as an automation platform to like take care of your fish.
Hopefully we also see some more alternatives to printer controls + slicing as we move towards more flexible functionality.
I’m thinking of going a different direction, using an articulated arm with a tool changer to mill a part in 7 axis, then swap to a 5 axis 3d print tool head to add parts in place on non-planar surfaces.
I’d love to see a 5 axis tool changer 3d printer!!