Don’t get too excited, a 3D printed radiation shield won’t keep you from getting irradiated during WWIII. But until the Doomsday Clock starts clanging its midnight bell, you can use one to improve the accuracy of your homebrew weather monitoring station by keeping the sun from heating up your temperature sensor. But how much does it help, and what material should you load up in your extruder to make one? Those questions, and more, are the topic of a fascinating whitepaper included in the upcoming volume of HardwareX.
Design and Implementation of 3-D Printed Radiation Shields for Environmental Sensors not only tests how effective these low-cost shields are when compared to an uncovered sensor, but addresses specific concerns in regards to leaving 3D printed parts out in the elements. Readers who’ve squirted out a few rolls worth of the stuff will know that common polylactic acid (PLA) filament, while easy to work with and affordable, isn’t known for its resilience. In fact, one of the advertised properties of the renewable plastic is that it’s biodegradable (theoretically, at least), so leaving it outside for any length of time sounds like it’s bound to go poorly.
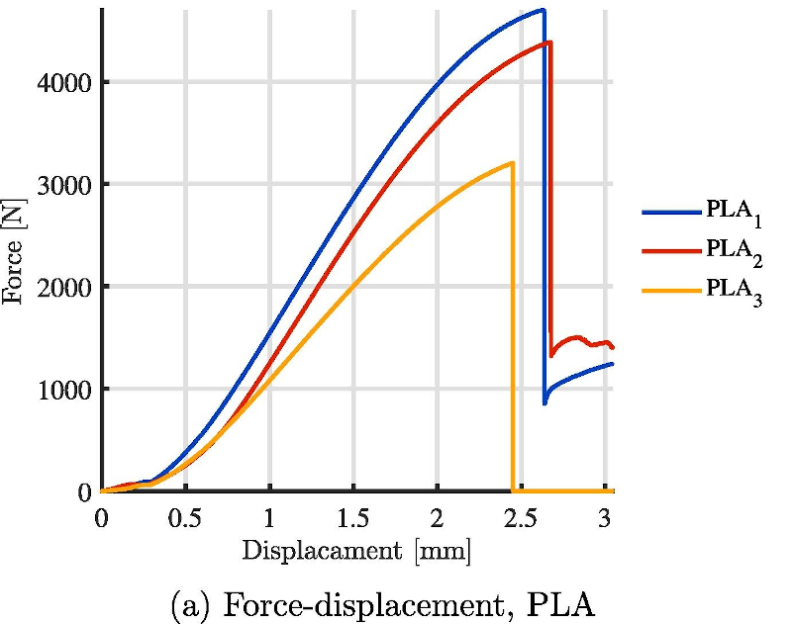
To make a long story short, it does. While the team demonstrated that the PLA printed radiation shield absolutely helped preserve the accuracy of the temperature and humidity sensors mounted inside of it, the structure itself began to deform rapidly from UV exposure. Further tests determined that the mechanical strength of the PLA showed a notable reduction in as little as 30 days, and a sharp decline after 90 days.
Luckily, there was more than one plastic horse in the race. In addition to the PLA printed shield, the team also tested a version printed in acrylonitrile styrene acrylate (ASA) which fared far better. There was no visible deformation of the shield, and after 90 days, the reduction in mechanical strength was negligible. It even performed a bit better when it came to shielding the temperature sensor, which the team believes may be due to the material’s optical transmission properties.
So there you have it: a 3D printed radiation shield will absolutely improve the accuracy of your weather sensors, but if you want it to last outside, PLA just isn’t going to cut it. On the other hand, you could also save yourself a whole lot of time by just using a stack of plant saucers. Whatever works.
Thanks to [tahnok] for the tip.
Can confirm, I designed and printed one of these that snaps together a year ago, it’s a year old in the Queensland weather and still going strong. In fact it’s doing better than the “stainless” steel screws that hold it up
This is what coatings are good for. Print using whatever plastic, and then coat for uv resistance.
PVC similarly degrades in sun, especially in UV-intense places like Arizona, where I live.
And yet… I have a homemade (electronic) anemometer and a weather vane, with PVC (plumbing fittings) housings that have been exposed to the elements for more than 20 years. No problem.
As Fred pointed out, that’s what paint is for.
I’ve used PLA in outdoor projects before but never ran into deterioration. Maybe I didn’t wait long enough or check thoroughly enough, but for me PLA doesn’t seem as biodegradable as it’s advertised to be.
it’s definitely not gonna compost the way a watermelon rind will, but it also changes quite a bit on exposure to the elements. it gets brittle and it can warp, too. depends on whether it gets direct sunlight, and on whether it sees any mechanical loading at the same time, and also of course on how thick it is and so on. like as near as i can tell, it readily sags at 140F if there’s any weight on it at all…not sure how this is represented by its material qualities datasheet.
i made a few bike lights with 1mm PLA walls, real thin flimsy stuff. on the plus side, they are still more or less holding together after some years despite weather and vibrations and so on. but even though i always park in a garage, the oldest one (2017) is brittle and cracking all over, only a matter of time until it dumps its contents.
i haven’t done experiments on it but i suspect it’s like most cheap plastics in the cold…around 32F most plastics turn fantastically brittle. of course, if you talk to people who wrench on cars in the winter, they’ll say the same thing for steel. it’s all a matter of expectations and tolerances.
basically, my impression is that if you’re expecting PLA to fall apart then it lasts well enough that you’re impressed by it. but if you’re expecting PLA to hold up to the elements then you’ll be astonished how quickly and completely it falls apart.
These helical radiation shields are new to me. The design looks like a good candidate for continuous 3D printing:
BARANI MeteoShield – RADIATION SHIELDS Helical solar radiation shields, the new standards of accuracy.
https://www.baranidesign.com/radiation-shields/
https://allmeteo.com/radiation-shield-comparisons
The web site has what looks like serious test data. This design is a commercial product. On the web page it says: “Free testing samples of MeteoShield Profesional are available for a 6 month loan. If you are satisfied after evaluation you can purchase it, otherwise just return the shield.”
Unfortunately one MeteoShield starts at 200 Euros. As far as I can tell, that does not include the sensor:
https://barani.squarespace.com/meteo-store/meteoshield-professional
They claim the design is patented/registered worldwide (“EUIPO 002979179-0001…0006”). At 200 Euros each, as a casual hobbyist I would not hesitate to print something similar to the MeteoShield for my own use/evaluation. I would not be surprised to see something similar by now on Aliexpress for five or ten bucks.
I printed a stevenson shield for my weather station 5 years ago, in white PLA:
https://www.thingiverse.com/thing:2009953
I already replaced the sensor once, but the shield is still there. Here, in south of France, temperature can go from -5°C to 40°C (few years ago we had a peak at 46.5°C) with a lot of sun.
Now failed PLA prints go to the fireplace, I think it’s the better way to recycle them. I regret that there is no way to recycle failed 3D prints, at least for the mainly used materials.
Glad to see at least one person use the term ‘Stevenson’ here. Felt a bit strange that there is no reference to Stevenson screens in the article body…
Fyi, Stevenson screens for those wondering:
https://en.wikipedia.org/wiki/Stevenson_screen
@irox said: “Glad to see at least one person use the term ‘Stevenson’ here. Felt a bit strange that there is no reference to Stevenson screens in the article body… Fyi, Stevenson screens for those wondering: https://en.wikipedia.org/wiki/Stevenson_screen”
Pedant mode ENABLED: What is being discussed here is commonly termed a “Radiation Shield”, or similar. In my opinion, a “Stevenson Screen” (not “Stevenson Shield”) is a very specific construct.
I’ve been toying with this for a while, and I came to similar conclusions, however I think this can be resolved by “simply” covering the PLA with a UV resistant material. My preference is a plastic UV window cover, where one side is sticky and the other reflects light/UV rays. Another option is to cover the shield with cut up pieces from an old raincoat.
Sounds about right. I’ve got one I printed that’s almost ready to install, but I’ll be installing it under a deck, not in direct sunlight. Not even sure if I’ll put a temp sensor in it, the main purpose is a pm2.5 sensor, and I figure that and the esp8266 will probably heat it up a bit in there.
I made a mason bee hive using black form labs resin. It’s been outside for three years old, looks fine today. Walls are about 1/4” thick, maybe that helped. Tried a resin based print?
“But how much does it help,”
Not sure honestly. I’ve got one on my store-bought setup and when the sun hits it the temp climbs 10+ºF over the actual outside temp
I don’t have a 3D-printer so i bought such a thing from Aliexpress (for quite a few $$), but i am not really impressed. When there is sun the temperature reported by the sensor inside is quite high, much higher than the official readings from the metorological service here. I should try removing the shield / putting another sensor next to it but without a shield and see how much difference it really makes.
@some guy said: “I should try removing the shield / putting another sensor next to it but without a shield and see how much difference it really makes.” This i sometimes called ‘differential sensing’. But how will you correct for the difference between the shielded sensor and the sensor that is not shielded? Which sensor is ‘correct’? Think about that. The term ‘shield’ is a hint.
I am afraid i don’t understand. The sensors (Si7051, probably unobtainium currently) have quite good accuracy, like +-0,15°, so this should not be a (big) issue.
I’ve run that test. In any decent amount of sunlight the temp sensor won’t read atmospheric temp without a shield. It’s off by a margin that’s tightly related to exposure time and wind flow. If you can take those things into account, in theory you should be able to calibrate away the solar radiation using the second sensor isn’t shaded for reference. I didn’t try, but this is basically what we do when we use a microprocessors internal temp sensor to estimate atmosphere. Only our source is the current not the sun.
I’m sorry but shouldn’t the two shields have been both in the same colour (white), for it to be a valid comparison?
Most of my radiation shields prototypes showed significant heat gain because 3D filament materials are highly transparent to the IR which gets re-radiated when sunlight hits the shield. The solution was to add air gaps & multiple foil layers to reflect that IR away from the temp. sensor:
https://thecavepearlproject.org/2024/08/10/using-a-bh1750-lux-sensor-to-measure-par/