Off-the-shelf stock parts are the blocks from which we build mechanical projects. And while plenty of parts have dedicated uses, I enjoy reusing them in ways that challenge what they were originally meant for while respecting the constraints of their construction. Building off of my piece from last time, I’d like to add to your mechanical hacking palette with four more ways we can re-use some familiar off-the-shelf parts.
O-Rings as Retention Features
Plenty of us are using rubber o-rings as airtight seals between static or moving parts. But their elastic and grippy properties give them a second life in other places involving removable components.
On my tool-changing machine, Jubilee, I quickly ran into the issue of securing idle tools onto their parking posts without the risk of letting them fall out. While one tool is being used, the remaining idle tools need to sit in a fixed location so that the machine’s carriage can pick them up later. To complicate the matter, the motion platform creates an appreciable amount of vibration, and idle tools that aren’t secured down are prone to slip out.
I’ve seen plenty of tool-changer builders opt for magnets in this case. They’re fairly compact, and you simply place one on the tool and another on its corresponding parking post. In my case, though, I opted for o-rings instead. Here, I use them to apply a bit of preload “squish” that secures the tool body to the metal pins of its parking post. The result is that tools slide into place with a small, satisfying amount of force and stay fixed even as the machine vibrates.
O-rings have the slight disadvantage in that their performance can be somewhat dependent on the accuracy of the 3D printer used to print the part that they will be installed into. In my first experiments, the fit was too tight. In others, too lose. If you find yourself in those cases, dear reader, know that two quick fixes include both (a) switching materials from neoprene to silicone, and (b) adding a tiny amount of grease to the parking post pins.
Overall, I’ve found this solution to be a reliable alternative to magnets, not to mention being widely available and still inexpensive.
DIY Thrust Bearing Retainer Rings
Thrust bearings often come in three pieces, that is: a set of steel balls locked inside a retainer ring and two washers to sandwich it. For the majority of my professional and unprofessional affairs, I’ll usually start by look through Torque Transmission’s catalog. But since I occasionally kept wishing I could customize my thrust bearing sizes, and since replacement balls are available on McMaster-Carr, I eventually tried rolling my own–to modest success!
To do so, I started by laser-cutting the center retainer ring out of Acetal (aka: Delrin), on of my favorite materials for prototyping. Both the low friction and clean laser cut edges make it a great choice for this application. After playing around with the hole diameter to seat the balls, I found a size where each ball would barely poke through the bottom of the ring without falling out. This trick is courtesy of the laser beam’s kerf, which puts a slight angle on the cut edge and makes each ball sit in a hole that resembles more of a cone if you zoomed in.
For the washers, I scoured Misumi’s catalog for thick steel shim rings. Combined, this approach gives me much more flexibility in acquiring thrust bearings in nearly arbitrary sizes.
There are a couple drawbacks with this approach. By far, the biggest issue is that a sad, tweezer-equipped human must load a bearing ball into each hole manually–a potentially arduous task for tiny balls that are all-too-eager to escape your fingernails and make a run for the nearest hallway, never to be seen again. The other issue is that the stainless steel shim rings I chose simply aren’t as hard as the Rockwell 60 hardened steel washers that the commercial parts use. The result is that the bearing balls will wear a small, circular channel into the shim ring. That said, that’s not a huge issue for applications that wont experience heavy loads.
Nowadays, I like to think of this entire approach as a bad idea–except when it’s not! Creating your own cages gives you the flexibility to define the inner and outer hole diameter. And for prototyping a one-off system, I may yet again reach for this trick.
COB LED Strips for Microscope Illumination
Taking pictures with the benchtop microscope first poses the challenge of illuminating your tiny subjects with enough light. Sometimes the microscope comes with its own light source. Other times, you can purchase a ring light attachment like this one from Aliexpress. Unfortunately, these light rings don’t always come in the sizes you need. And in cases where you’re working with oddly-sized lens bodies, sometimes you just need something custom.
In those cases, I’ve been tempted to fire up KiCAD and make a custom LED ring PCB. But while that certainly works, the voice in the back of my head keeps asking: isn’t there an easier way to do this? After letting the thought simmer in the back of my head, I found an answer: side-emitting COB LED strips.
For this sort of application, these LED lights are almost perfect. For one, they’re extremely flexible, capable of tucking into very small diameters. They can also be cut-to-length, giving you lots of flexibility on the size you might need. And with their adhesive backing, you can simply peel-and-stick the length to the cylindrical body you’re illuminating.
I ended up using this trick on Jubilee’s “camera inspection tool.” The result works perfectly for this sort of space-constrained setup.
It’s worth mentioning that the adhesive on the back of this LED strip isn’t super thrilled at being rolled into very small diameters. But in those cases, you can always reach for a zip tie for extra security. And, dear reader, if you’re convinced that a solid LED ring will still fit your needs better, I invite you to also consider “Angel Eye” LED headlights on Aliexpress.
Seamless Stainless Steel Tubes as Coarse Linear Guides
On occasion, my after-hours web-browsing habit of sifting through part catalogs uncovers some enlightening results. Recently, I discovered seamless stainless steel tubing. These are hollow stainless tubes available in a wide range in inner/outer diameter combinations. Seeing them instantly had me fantasizing about using them as coarse linear guides. And, combined with the right complimentary part, it turns out that they work surprisingly well for that purpose.
On their own, I discovered that the tolerances of the 8 millimeter tubes just aren’t good enough to simply attach an LM8UU linear bearing. Some tubes worked, but others were simply too large to fit the bearing. However, Drylin LM8UU Bushings offer a nice workaround for rods with a less well-defined outer diameter. These bushings are sold as sliding replacements to roller bearings. They’re made from an especially low-friction plastic and sold with slightly oversize inner diameters. To install them, one must tighten them down with just the right force such that bushing slides along the rod smoothly without binding or wiggling. This installation quirk makes them perfect for pairing with these tubes. You simply adjust the clamping forces until the setup slides smoothly.
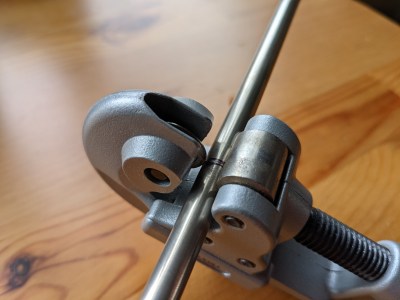
In contrast to hardened steel rods, these hollow tubes are extremely light–only 25 grams per 150 millimeters of tube length. These tubes are also easy to cut to length with mere hand tools. Here, a handheld tube cutter easily cuts these stock tubes down to size.
For my test application, I cooked up a syringe head for Jubilee. Here, a sliding piece attaches to the plunger of a typical 10 cc syringe, and a motor-driven leadscrew actuates it. Overall, the setup works really well for this type of low precision application. I will certainly keep this trick in one of my pockets, and I hope you do too.
Stock Part Slant Rhymes
That wraps up this B-Sides showcase for now. I hope this round of stock part “phonics” keeps you looking for new ways we can reuse everyday stock parts. And if you find something clever, do drop us a tip!
Great article. As always clever engineering solutions Josh!
I remember reading about some open sourced CNC router that used 1″ stainless steel tubing for the guide rails. I think it was the MPCNC (Mostly Printed CNC).
Those bushings look like a neat option.
MPCNC actually uses something even more common…electrical conduit. It’s way cheaper than stainless steel. But it worls pretty well.
I use 25mm aluminium tubing for my MPCNC.
I discovered stainless-steel drinking straws on closeout at WallyWorld and bought a bunch. I’ve used them as stock to make lots of stuff.
The way the Igus bearings are clamped on that syringe tool is super nice and 3D-printing friendly. I’ll add that to my toolbox for sure!
O-rings as tool changer retainers is something you see in entry level PCB mills and mini CNC machines from upstart companies. They’re usually eliminated by version 2.
They usually fail to grip the tool enough to extract it from the collet, or fail to release the tool when picked up, or the tool doesn’t quite fit in, which means the operator has to stand by at all times with a hand on the stop button at every tool change, before something snaps or bends out of shape.
I used a blue tooth button from a selfie stick with an old cell phone camera to make layer synchronized time lapse videos on my 3D printer. A few lines of custom gcode on layer change sends the X axis (and extruder) to the back of the machine, pushing the bluetooth button when it gets there. Photos snapped on the phone get uploaded to google photos as soon as they are snapped so they can be seen from any web browser. I run OpenCamera on the phone which allows me to lock exposure and focus and time stamp photos. After the photos are made, I use irfanview to bulk scale/crop images, then imageJ to turn the sequence into a movie. The cell phone camera takes high res images so I can see details in the prints that lower res cameras can’t capture. https://drmrehorst.blogspot.com/2020/04/fancy-no-hack-layer-synchronized-time.html
I also made a wire twister tool that uses a pair of Wago 221-412 lever nuts to hold the wires. Just strip the ends of the wires, snap them into the lever nuts, pull the trigger on the drill. You get fast, easy, and very clean twisted pairs in seconds. https://drmrehorst.blogspot.com/2022/02/ultimate-3d-printed-wire-twister.html
Old printers are an excellent source of hardened ground steel rods & some other surprisingly good quality mechanical parts – big old laser printers & photocopiers are best but even crappy inkjets yield some useful stuff.
Not sure if the ball bearings are magnetic – if they are, they might be easier to place using this magnet placer tool: https://hackaday.com/2023/01/14/diy-magnet-handling-tool-puts-an-end-to-placement-errors/
You could even modify the end plate to have a dimple for the ball bearings.