If you’re not a woodworker, you might not have heard of the “45-degree rule.” It goes like this: a clamp exerts a force that radiates out across a triangular region of the wood that forms a right angle — 45 degrees on each side of the clamp’s point of contact. So, to ensure that force is applied as evenly as possible across the entire glue joint, clamps should be spaced so that these force triangles overlap. It’s a handy rule, especially for the woodworker looking to justify the purchase of more clamps; you can never have too many clamps. But is it valid?
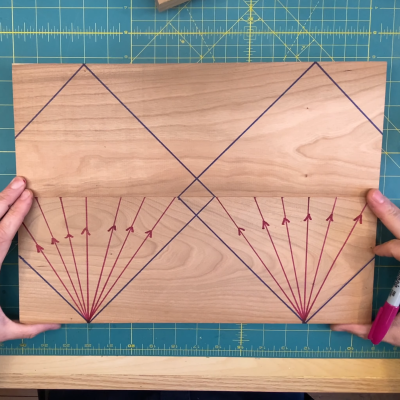
The short answer that [ari kardasis] comes up with in the video below is… sort of. With the help of a wonderfully complex array of strain gauges and a Raspberry Pi, he found that the story isn’t so simple. Each strain gauge lives in a 3D printed bracket that spaces the sensors evenly along the wood under test, with a lot of work going into making the test setup as stiff as possible with steel reinforcement. There were some problems with a few strain gauges, but once he sorted that out, the test setup went into action.
[ari] tested clamping force transmission through pieces of wood of various widths, using both hardwoods and softwoods. In general, he found that the force pattern is much broader than the 45-degree rule suggests — he got over 60 degrees in some cases. Softwoods seemed to have a somewhat more acute pattern than hardwoods, but still greater than the rulebook says. At the end of the day, it seems like clamp spacing of two board widths will suffice for hardwoods, while 1.5 or so will do for softwoods. Either way, that means fewer clamps are needed.
A lot of woodworking is seat-of-the-pants stuff, so it’s nice to see a more rigorous analysis like this. It reminds us a lot of some of the experiments [Matthia Wandel] has done, like load testing various types of woods and glues.
Nice video. Thanks for sharing it. The 45degree rule is pretty common outside of woodworking, as well. When disturbing consolidated soil near a foundation to avoid loss of support, the undisturbed soil must be at maximum 45degree slope. Shear failures in isotropic materials follow 45degree lines to the force. And so on.
Generally close enough, but not exact, and, as shown here, generally safe.
These rules fail spectacularly in some cases, though. Anisotropic materials, inhomogeneous materials, unconsolidated or loose materials (soils, sand, etc), soft, ductile materials, and the like can have VERY different behaviours.
HaD did an article series some time ago about moving around bulk materials, like pouring powders and stuff out of big hoppers. It was really cool. Sounds like this article has a lot of broad applicability like in your field as well.
Yeah. I think calling it a “myth” is clickbait. It’s a rule of thumb, not a myth. And it’s a pretty good rule of thumb, as his test results point out. So again, not a myth.
But this video is great. It’s a super clear explanation of the setup and how it works, aimed I think perfectly at the level of understanding that his target audience — smart modern woodworkers — would have.
And the actual takeaway for me is to not clamp close to the ends of the board, but rather say 45 degrees off of it. Which makes total sense, but I had not thought about it until watching this vid.
Don’t hate the player, hate the YouTube algorithm that forces them to make funny faces and overblown claims to get seen.
> the YouTube algorithm that forces them
It’s a two-way street. The algorithm chases the tubers and the tubers chase the algorithm, and both are being fudged by outside influence with trends and other effects. It’s like when Dr. Skinner trained pigeons to become “religious” by giving them random feedback: whatever the pigeon was doing at that time was rewarded, so the pigeon developed the idea that you have to make a little dance every time before pressing the lever to get the food out of the machine. Since you get the food after performing the ritual, even though the ritual does not matter, the pigeon just kept on doing it.
I for one have started avoiding all videos that look like the typical “You wouldn’t believe this incredible gadget” that are just mashups of fakes or stolen videos. Studies have shown that people gradually start to ignore useless junk like that, even automatically avoiding looking at ads on webpages, so the algorithm eventually catches up and starts punishing them.
Also used as a quick rule of thumb for propagation of strain through structural steel, though the rule of thumb is +/-30deg there IIRC.
Bolted steel joints follow a similar distribution of load. It’s about 25 degrees in that case though.
It ain’t clamped till some glue comes oozing out all along the line. You can squeeze all the glue out with too much force and have a weaker bond.
These findings I’ve been with all along. I never thought that it’s an angle of a straight line but an exponential curve with a lot of the grain thrown in.
I don’t know why it would make a weaker bond as long as the glue isn’t entirely removed, which is pretty hard to accomplish.
Goldilocks says “Hi”. This has all been studied for ages, and you want your glue layer to be about 0.1mm.
That’s hard to apply, hence “clamp it until squeeze out”. And yes, under certain conditions it is possible to squeeze too much glue out (dowel, tenons etc).
The net finding in this seem to be that hardwoods are stiffer than softwoods.
While my heart leaps at solid mechanics and instrumentaiton – and it’s good to see that the force-sensing fixtures used in digital scales are available for use, the author seems to be confusing strain gauges with these force gauges (scales) which are strain gauges attached to an elastic fixture that deforms in a predictible way under stress. This study could be done with old-fashioned spring-based postal scales just as easily.
A faster/simpler way of doing the analysis analysis would be photoelastic analysis – putting a beam of transparent optically active plastic (lexan/polycarbonate etc.) between two polarizers and subjecting it to stress. The results are immediate and intuitive, and setting it all up would take an hour or so if that.
Here’s a pretty good overview: https://www.sciencedirect.com/topics/materials-science/photoelastic-stress-analysis
The 45 degree legend is likely a misunderstanding of material failure along the shear plane which is most easily demostrated under tension but can occur in compression (and breaking a drill bit – helicoidal failure – demostrates it in polar coordinates more or less).
More likely the 45 degree “legend” is a conservative estimate that is only violated in known circumstances, like the force not transitioning past a knot in the wood.
Your point is easily proven by taking it to the extremes — imagine clamping styrofoam sheets or steel beams. Clearly the pressure spreads out differently depending on the material.
But that’s also why he had to use wood here, and a few different kinds of wood. And why doing it in acrylic wouldn’t be informative.
As the guy notes, slight variations in board edge mostly trumps the results. If you have a high spot, the entire board pivots around that point and throws off all the rest of the sensors such that the forces can appear all the way at the other edge of the board.
The “conservative” angle is to account for this fact. You apply more clamping than necessary to deform the boards against each other. Some points may get a little bit too tight, but that closes up the span in between.
This is great work but only shows results where the grain is perpendicular to the clamping force. Of course this is how 90%+ of glue joints are made. I expect the pressure distribution angles might be considerably more narrow for butt joints.
The curse of the modern world – this is actually an interesting video but the bl**dy stupid clickbait thumbnail would put me off ever clicking on it in the wild.
Exactly. I don’t give a damn about the “this is the youtube game” excuse
This is a disfavor to your work and a race to the bottom!
There’s better way to make your video standing out.
if it is not pure passion, i don’t know what it is.
the amount of thought and work put in this video is insane in regards of its… dunno… barely usefulness :)
woodworking is a billion dollar hobby in the US annually. the end-clamp placement information bucks intuition and common practice.