Heating is one of the greatest uses of energy in human society today. Where we once burned logs to stave off the brutal winter chill, now we lean on gas and electricity to warm our homes and keep us safe and toasty. In some colder climates, like the UK, heating can make up 60-80% of total domestic energy demands.
However, there are alternative ways to provide heating. Using wind energy to directly provide heat could be key in this area, using a variety of interesting methods that could have some unique niche applications.
Conversion
If one headline has become repetitive and boring over the last two years, it’s rising gas and electricity prices. That has left millions around the world paying more than ever to heat their homes. Sustainable sources of energy at the home scale can offset this to a degree, for those that rely on electric heating methods—whether through resisistive means or via heat pumps. Of course, in the coldest of winters, common home solar panels are sadly at their lowest output, providing weak savings at best.
These issues have shed new light on alternative methods of heating homes in a clean, renewable fashion. In particular, wind energy can be used for heating if properly employed. The most obvious solution is indirect, whereby a wind generator provides electricity to run conventional electric heating. However, more interesting are the direct methods, which can be cheaper and more energy efficient in some cases.
Slam On The Brakes!
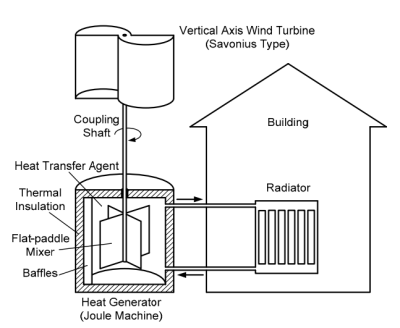
The most intuitive type of wind-to-heat generation is via a fluid-brake system, also known as a Joule Machine. This involves a windmill turning a paddle inside a container of fluid, most typically water. The energy captured from the wind stream is essentially dissipated into the fluid by the resistance it poses to the windmill, heating it up. The heated fluid can then be pumped to radiators to deliver heating where it is needed. It’s a simple enough concept, though takes careful engineering to make it work in practice. The key is in properly sizing the windmill and fluid brake to match each other, and to choose the right parameters to heat the fluid to a useful degree. The benefit of this method is that the system converts directly from mechanical energy to heat, bypassing the electrical stage which adds significant expense and complexity. It also saves an extra energy conversion stage which can be beneficial for efficiency.
A fluid-brake windmill is a remarkably simple device, mechanically-speaking. It could have been used for heating in early Industrial times had someone thought up the idea back then. However, they first gained prominence as certain enterprising individuals in Denmark experimented with the technology in the 1970s. The country was wracked by the global oil crisis, as it depended on a reliable supply for heating. When oil prices skyrocketed, alternatives quickly became attractive.
It bears noting that this concept is mostly applicable for those in rural areas with space to spare. They’re also places where the wind is likely to be more available. Plus, unlike built-up areas, it’s easier to build a bigger turbine that is more capable. Small or low wind turbines typically perform poorly, particularly in crowded urban areas. However, for a rural property with ample space and limited connection to grid utilities, a wind-to-heat device could work well.
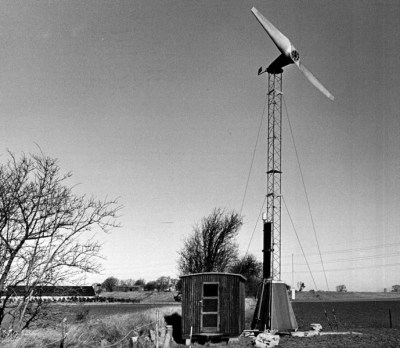
The early Danish design known as the Calorius Type 37 is a good example of a typical wind-to-heat setup. With a 5 m rotor and a 9 m height, it was capable of producing 3.5 kW of heat during a 11 m/s breeze. A pair of these unit would be capable of heating a medium-sized house.
In comparison, the more advanced LO-FA design from the 1980s demonstrated just how potent a wind-to-heat system could be. With a mighty 12-meter rotor on a 20 meter tower, it was capable of generating an estimated 90 kW of heat with wind blowing at 14 m/s. It notably used higher-resistance hydraulic oil for the fluid brake, rather than water in most other designs. The heat was then transferred to water for distribution. With so much heating capacity, the LO-FA could conceivably heat several homes, suggesting large wind-to-heat units could be ideal for off-grid communes or family farms.
Of course, the wind doesn’t blow all the time, so heat storage is often necessary if relying on such systems. The simplest way to do this is to combine a wind-to-heat system with a large tank of water to act as a heat storage reservoir. Dutch systems often relied on storage tanks with 10,000 to 20,000 liters of water on hand. This would provide enough storage to get through cold times with minimal wind with storage taking up roughly the same amount of space as a small swimming pool.
Mechanical Heat Pumps
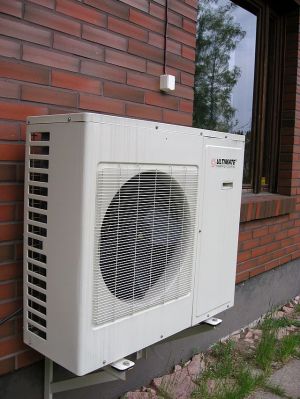
Alternatively, heat pumps can be of great benefit in this area, too. A fluid brake system may convert somewhere up to 90% of the wind energy captured into heat in the fluid. A heat pump, on the other hand, can be 300% efficient or more. This is because rather than converting the wind energy directly into heat, the wind energy is instead moving heat from one place to another instead.
There’s nothing particularly fancy involved in building such a system. One can merely take an existing electrical heat pump, and remove the motor, replacing the mechanical drive with the output of a wind turbine. Some gearing may be required to match the two, but fundamentally, that’s all that is required. This is generally more efficient than using a wind turbine to generate electricity that then turns an electric motor to run the heat pump indirectly.
Wind-to-heat systems relying on heat pumps are even more niche than their fluid-brake cousins. However, early research suggests that they could be a remarkably cheap and efficient way of generating heat directly from wind energy. Practical concerns may limit them to use in off-grid communities or other niche applications, but nonetheless, the thermodynamics check out.
Where We Stand
Today, far removed from the oil crisis of the 1970s, direct wind-to-heat generation remains more of a research curiosity than a popular method of warming homes. However, if you’re a university researcher, or working on new concepts for your city’s district heating system, or a rural hacker out on a farm, it may bear examining. For areas with abundant wind availability and high heating demand, wind-to-heat systems could prove useful for keeping everyone toasty and warm in a zero-emissions fashion.
>Of course, the wind doesn’t blow all the time
And even more rarely does it blow at 11-14 m/s. The yearly mean wind speed in central and northern Europe revolves around 3 – 3.5 m/s. The power output of a turbine is proportional to wind speed cubed (v^3) so that’s a pitiful amount of power on average.
Many parts of the Great Plains of the USA have average wind speeds up around there. Lots of rural areas, lots of houses that are heated by propane delivered to a tank at the house by truck. There techniques might be very useful there.
The mean wind speed I quoted was from 10 meters high (relevant to small turbines). Looking at the global wind atlas (https://globalwindatlas.info/en) the mean wind speeds along the great plains are generally around 4-6 m/s with some tiny spots in the mountains where the average tops 9 m/s.
This doesn’t seem very efficient to me! This device is only useful when you need heat AND when the wind is blowing hard enough. So, around here this means when the wind is blowing hard enough for about three months out of the year. In other words, when counting hardware utilization, a measure of efficiency, the system is already down to 25% utilized and this utilization will be driven lower as the wind does not blow strong enough most of the time.
At least a generator / storage battery has the potential to store energy 24X7.
I think this is also used as a heat storage system. Any sort of heat or electricity storage is volatile though of course and will lose heat/electricity over time, but heat storage doesn’t degrade in storage efficiency as quickly as chemical electrical storage does, so in some cases this might be a better long term alternative.
Either way I think the point is to think about things differently, using what we have to hand is a hackers bread and butter, but maybe there’s another option that doesn’t use conventional methods that’s even simpler.
I think the point is not just to rely on one technology but several
And reap the benefits
What are you going to do in summer with all that extra “free” heat energy?
Swimming pool / hot tub
Adiabatic cooling or just use heat pump both ways for both heat and cooling.
Electricity generation with thermoelectric/stirling generator.
Heat/electricity storage by price of water with minimal loss?
Properly designed thermovalve may actually alloy it.
https://www.nature.com/articles/s41598-019-55616-7
https://phys.org/news/2019-12-coolest-lego-universe.html
I mean properly designed building/vehicle may not need heating or cooling just moving heat inside building and sometime from outside.
It seems like a good match to me. When the wind blows is also when any small cracks will leak the most – and thus – will be the time to replace lost heat. Kind of weird that the wind blows when you need it – because – the wind causes you to need it.
@Dude
Yes, at ground level this may be true. Although when you elevate yourself from the ground by every 2.5-3 meters the wind typically has much higher velocity. The smaller the turbine the higher you want it mounted, of course within reason. The power delivery cables must be longer which in turn increases resistance and forces the use of thicker conductors.
No amount of elevation offsets the fact that at least around here, the machine would be useless 9 months out of the year. And a machine that can be used only three months of the year can only be utilized 25% of the time.
I think you would be surprised at how well a small windmill can work in a wide range of windspeeds – not saying it would be anywhere near peak through a year, but actually useless with a good turbine in a half way decent location is very very unlikely (as in don’t put it between massive buildings/tree entirely sheltered from the wind).
You are correct, BUT it could be long term help if the 3 months are the coldesty
… and since a hydraulic brake dissipates energy proportional to the square of speed, you cannot match such a device to a wind turbine for all speeds, you have to choose a single operating point, or you have to adjust the operating point of the brake to the actual speed/load (e.g. you need some sort of regulator).
Interesting ideas, but as the article points out, using a heat pump is probably the best route.
But that has issues as well, as the comments points out.
So most efficient and cheapest is probably to add an electric stage in between, then you can use a commodity heat pump.
And of course, sell any excess. And possibly use the power for other things as well?
I live in the Appalachian mountains, 45mph is not uncommon and in fall 75 mph days happen. The colder months are the windiest.
I wonder how many people discover water freezes at 32F/0C when the wind stops blowing? Yes you can use other fluids but they can be messy/toxic.
Electrical generation is a better option as it can be used in many applications.
Only if you use pure water. If you want a huge reservoir of cheap liquid, then be careful with corrosion and consider a salty brine – something salty enough to make growth unlikely and to freeze at a low enough temperature not to worry about it. If you can spend more on the liquid, there’s all sorts of options.
Calcium chloride in water comes to mind, good to lower temperatures than sodium chloride.
Yep, or possibly magnesium chloride if the properties work out better for a particular use case. When you’re using intermittent energy to heat brine, maybe it will help if you find a way to use the heat released by dilution aka enthalpy of solution. The figure I looked up is much greater per mass with Mg than Ca, but both are used and available as road salt / de-icer.
Put some alcohol in the water, nothing like some vodka to keep you warm on a cold winter’s night, even if you don’t drink it.
You need to be careful with the heat here, as Brits start to melt at 70F(around 20C)… look up the Great Thamesmead Puddle, if you can get by the massive cover-up, you’ll see. There’s an artificial lake there, now.
When I searched for this, one of the results returned was this very page. I assume this what you meant? https://www.theguardian.com/uk-news/2022/nov/30/cockney-riviera-botched-regeneration-brutalist-utopia-thamesmead
The Mechanical heat pump idea is interesting.. But you are compressing a Gas.. Storing it, and using it as required to transfer the heat..
In Basic Terms, it’s a Compressed Gas Storage System.. They have been tried before, Generally in the Pond Aeration Category.. Take an Air Compressor, put it on a Tower, and have the Bubbles piped into a Pond to keep your Fish from Dying.
However simple they are, generally not very ‘Efficient’. ( a nebulous term that can be discussed at length ), but simple to produce.. Therefore sometimes more ‘Effective’.
In the long haul, I’m thinking this is a good mental exercise, but it will boil back down to Wind-Electricty-Storage-Use, with you use being what ever you want.
They really need to get that cold Fusion Thing working again.. It would help a lot!..
Cap
You don’t have to store compressed gas to make the heat pump idea work.
We have heat pump water heaters right now.
You just need to make a hybrid wind-electric heat pump that heats a big, well insulated tank of water. Then you pump the water to radiators as needed.
You want a hybrid system with a clutch so it can use electricity to take up any slack in the system when you need more heat than current wind speeds can provide.
Remember that we never have to completely convert a system to “save”. Even if the goal is to eliminate something entirely, it is still worth considering a system that ‘only’ saves 60%, as long as you account for the burden on the new source.
Interesting, that might be another use for the differential CVT used in Toyota hybrids [1]. Connect the windmill to the ICE input (planet carrier), the compressor to the MG2 output (ring gear) and an electric motor to the MG1 input (sun gear).
That way you can drive the compressor at the required speed from a combination of wind and electric power.
(to be fair this probably does not work if there is no wind, as the MG1 would turn the windmill, but this can be solved with an additional brake in the windmill. You need a brake either way to stop the windmill during storms)
[1] originally only the Prius, but now all Toyota hybrids and several other hybrids from other car manufacturers use the same technic.
For those who don’t deal with m/s regularly:
I would not call 11 m/s a “breeze”. That’s 40 km/h or ~25 mi/h. 14 m/s is 50 km/h or 31 mi/h.
According to the Global Wind Atlas (https://globalwindatlas.info/en) there’s not a ton of land area with winds averaging 10+ m/s. Even the windy south end of the region I live in, covered in a bunch of wind power generation, averages in the 7-8 m/s range.
I like the idea of these things but it seems they’re destined to not working a lot of the time for a lot of people – but I suppose that’s why they’re described as “niche applications” in the article’s intro!
That average is quite sensitive to height above the ground, but for practical purposes you are right. No-one is going to be building a 100m+ tower to run a direct heat generation system.
I’ve probably got the space for this (though my neighbours might have the odd question and I’ve no idea how I’d get planning permission for it). But it’s just completely impractical. According to the met office, we have a mean wind speed of around 8kt or 4.1m/s. Heating our house in a cold spell in winter takes about 8kW of heat 24×7. So, supposing we could run a heat pump at 300% efficiency we’d need 2.6kW of input power. At 4m/s wind speed and 30% rotor efficiency, I’d need a 9m blade to put about 2.8kW of power into the heat exchanger.
A turbine with 9m blades is a pretty serious bit of gear to be putting in your backyard. It’s not a trivial thing to assemble. I’m thinking that the payback time for the £2.5k I spend on heating each year currently is not going to be short.
Depends on what you build it out of, where and how your energy is sourced, and if a greater degree of self reliance is worth the upfront cost. Though if you desperately need that last one you have probably already spent a small fortune on fuel storage, generators etc…
The small end of wind turbines don’t actually need to be expensive, probably within that payback inside a year or two with your current heating bill… Though if you wish it to be super high quality last forever with low maintenance that will cost more than the cheapest possible options. At the scale a single home needs the blades can quite easily be wooden or engineered timber products, the tower is equally possible to do quite cheaply and still with overkill strength – off the shelf mass produced pipes and a bit of concrete to anchor it to the ground.
The real issue for most of us reading HAD is that we live in relatively built up areas that won’t get great low level windspeeds or neighbour/regulatory approval, not that the technology can’t be used to great effect at the smaller and cheaper single household scale. Will also say I am less sold that direct to heat makes practical sense – you want to be off grid or greener you want a spread of energy inputs to greatly improve the odds that you will get enough energy out of the others when the wind isn’t strong enough, and you want to consume that energy in a multitude of forms. Which means despite the extra conversion step going straight for electric makes sense. Electric is reasonably easy and efficient to generate and store, we have high effeciency conversion of electric to just about everything you could want and doing it that way means your in house infrastructure only has to be electric – you are not putting in the wind-heat direct heating, and the electric resistance/heatpump and the combustible fuel burner to be sure you can stay warm when there is no wind…
> The small end of wind turbines don’t actually need to be expensive.
Is a turbine with 9m blades – likely a 19-20m rotor diameter – really on the “small end of wind turbines” though? You seem to be ignoring the energy assessment here – yes, I could build a turbine with 3m wooden blades but, at my 4.1m/s average wind speed, that’s going to give me a power output of about 0.5kW or about a sixth of what I need. On a quick look on Google, the biggest wind turbines I can actually buy have 4.5m blades (they’re rated at 10kW but that’s at 9m/s wind speed). They cost about £5k.
Doubling the blade length to the 9m I need for my average wind speed quadruples the wind area, quadruples the available power at higher wind speeds and quadruples the thrust on the tower top, making the tower significantly more expensive to build, let alone the difficulty of building blades that long.
Who says you have to have one single turbine? In the places where this kind of idea has merit, E.G. the northern very windy plains in the USA, it’s probably cheaper to have a large number of smaller turbines, whatever’s the size that can be built with lesser materials at a cheaper cost.
9 meter is in today’s world is really really tiny – probably able to just buy used blades that length and even longer than that right out of the junk pile as the commercial operations find it much much easier to make an existing turbine bigger than get permission to build another.
And 9 meter is well inside the radius folks built wooden bladed windmill for centuries with as well, those seem to be frequently 20 meter diameter, sometimes more.
Though spaceminions is right as well, the value for money and practical usefulness of more small ones can be the right choice – there is no one exactly perfect solution that is always performing better than the other across all windspeed and material costs. There are too many variables for there to be only one valid answer.
As someone who has been through this exercise, I built my windmill on the coast of Maine in the mid 1970’s. It used a three blade sailwing, 20′ diameter, driving a 25 KW 400 hz aircraft generator. Load was a few 500 watt photoflood lamps in the basement to convert that power into heat. For a wonder, it actually worked fairly well. I learned a lot from the exercise, mostly things NOT to do. Using a diffuse energy source like wind, converting it to concentrated high value electricity and then to dissipate as low grade heat means efficiency is really poor.
I see the first example is using a Savonius rotor to drive anything is a bad start. Efficiency of these simple drag machines is bad. A standard three blade rotor with good aerodynamic characteristics is a much better energy extraction device. Probably way less than 10% as compared to standard three blade machines that approach Betz limit of 59.3%.
But, that aside, locating a wind machine near or on a house is never a good idea. These heating systems, with mechanical or plumbing connections to the load ignores the noise and safety factors. On a house, it’s like living in a banjo box. I’ve seen it done and very soon given up as a bad job. I’ve also seen several examples of home built and commercial machines that self-destructed when mechanical failure or severe storm winds greatly overcame any safety shutdown features, if even included.
As for my background to justify my opinions, building that first machine, even with it’s limited success gained me access to the entire wind and solar culture for the next 15 years. I joined a company in New Hampshire where we manufactured wind monitoring equipment, controls for wind and solar, octahedron towers and other alternative power sources. We made controls for many companies, attended conferences put on by the United Nations, our government and some of the big companies who wanted to cash in on this growth opportunity. Joining a large wind farm in the Altamont Pass in California was really a thrill. All those machines with a white box in front of each one with my controls keeping everything running made for some proud moments. All those machines are gone now, being replaced with much larger and more efficient windmills. But that’s OK with me, just the price of progress.
This is a very good boots on the ground assessment thank you for this.
The average temperature over the course of a full year is fairly comfortable in most inhabited regions. Some day somebody will develop a modestly sized thermal battery (not a basement full of rocks).
No, I don’t think that a thermal reservoir you could fit in your house—that isn’t catastrophically dangerous and/or or enormous—and is capable of heating a home for an entire season is going to happen soon. Anything meeting those requirements is either going to be very very big or it is going to essentially be a bomb.
Well, technically…. Depends on what counts as a reservoir, how much power you need to counteract losses through your insulation, and how large is too large. :)
An example of good liquid containers would be pallet-sized 330 gallon IBC totes; they are box shaped and designed to be stacked up even when full. I think something like 500 gallons of road salt could release 1kW for 90 days. That’s from the enthalpy change of solution I see on a chart for MgCl2; if you don’t dilute it to infinity you only approach the limit, so you’ll instead want to find a balance point between using space for water for dilution and using more salt in the first place. Probably err on the side of more salt. The mass would be enough that the ground would probably shift – I’d probably make a separate slab; it’d be more spread out than a car, but heavier, so I don’t think a garage is ideal.
Recharging the system would mean removing the water, presumably by evaporating it. That’s a fair amount of water, but not catastrophic and not incredibly dangerous. You can store energy much more densely if you don’t mind more dangerous substances.
An example of good liquid containers would be pallet-sized 330 gallon IBC totes”
330 gallons! That’s a lot of root beer!
https://www.ibcrootbeer.com/
B^)
XD
I said “some day” … I didn’t say anything about soon. And if you don’t think that a lithium ion battery isn’t technically a bomb you should revisit the math. My point is simply that someday in the future (probably distant future) storing heat (or cold) directly instead of converting it back and forth to/from other kinds of energy will make enough sense that it will happen. Maybe it will be done on a much larger scale than a single house, but I’m pretty certain it will happen eventually.
Heh, some people are already working on it. From my calculator, 112 ton container of rocks the size of a biggest road fuel tanker (40,000L, 40m^3), heated to 500C contains 12,282kWh of heat. My (medium size, good isolation) home uses about 3kW during winter for heating, this tanker would be enough for 170 days (500C -> 30C).
Done
https://youtu.be/Azaf9tKJNoA
There are houses that have been built with a large thermal reservoir. It is filled with just water and heated from thermal solar panels during the summer. Beautifully simple from an engineering perspective (pipes, pump, valves). The house needs to be adapted to this. See https://www.sonnenhaus-institut.de/
Unfortunately, financially unattractive as a lot of space is required
Folks have built houses from scratch that don’t fill a basement full of rocks to provide the thermal mass. The tricky part to making it so seamless is that you really do need to build the whole building around being very thermally efficient and ideally passive in the absorbing and emitting. It is not enough to just put a few rolls of insulation down and hope that box of rock is enough.
But its been done to varying degrees of passive with all sorts of methods, one that stood out to me was a central load bearing wall that is both the core of the structure, a heap of thermal mass, and positioned that you don’t need a big pump, radiators etc to push fluid through – it is the centre of the building, every room is able to share that same mass entirely passively. If I recall correctly it did take something over a year for the comfortable room temperature yearly equilibrium to be reached, as it is still a lot of thermal mass that needs to get warmed all the way through.
Right, you need a lot of thermal mass to really average you out to climate averages, rather than be subject to the variance of odd weather patterns. My current residence for instance, has a lot of brick, and it averages about 2 weeks I think (To match a new ambient, not necessarily the comfort zone). However, you feel the variance over 3 or 4 days. This is particularly a problem when it gets too much solar gain in hot spells in spring or autumn, due to lack of deciduous leaf shade. Or the converse in the middle of summer, with a cool week, got too much shade for it to make it up from direct irradiance vs air temp.Then if you miss turning on the heat or cooling systems for a longer cold period or hot period, you don’t notice for 3 days, then you’re really uncomfortable for several days until they catch up again. It would be more ideal in an area where you got the extremes for only days instead of weeks. However this is working with what I have and very far from ideal, but it approximates the mass of some rock box designs I’ve seen for retrofit.
Is that a viable option? When building a house, just dig out another layer below the foundation and pour rocks im there? Probably run some medium through and use it as a thermal sink?
Just put some pipes under the foundation and blow warm outside-air through them in the summer. That warms your floor a little, and you can use the air leaving the pipes to cool the house in the summer, and as pre-warmed source for a heat pump in winter.
In fact you don’t need to put the pipes below the house, just put them in the ground whenever you have to dig a hole anyways.
It’s not *quite* as simple as producing heat with a brake, but it doesn’t take a lot more to make a low efficiency pump instead. It’s not a new idea to pump water with a windmill, although higher pressures aren’t as easy. Once you have a pump producing significant output, you can expend the pumping power to generate heat by deliberately producing hydraulic throttling losses. This has the advantage that it makes the load variable, so that you can match the incoming wind power. It’s easiest to produce heat from throttling with higher pressure, but as the fluid brake demonstrates, the energy has to go into the water’s heat if there’s nowhere else for it to go.
The thing is, conventional hydraulic systems with high pressure oil are also much easier to set up for larger power levels than electric. So while hydraulics is usually less efficient than electric can be, and more complex than pumping around water at low pressure, you could still turn a heat pump compressor with it if you like. And, possibly with the help of a hydraulic accumulator, you could do other tasks that might be useful in a rural area, like splitting logs or using tools that would otherwise use a large electric motor. (Typical single phase farm motors require massively oversized inverters to start up, if you aren’t using the grid or a spinning generator with inertia.)
This link mentions deliberate hydraulic heating. https://www.scirp.org/html/2161.html
The link abstract is dated 2010.
I remember talk about that back in the late 1970s.
Sure. Just thought it was a nice brief example. It might be harder to find firsthand examples of theirs, and their predominant tech is probably not this, but the Amish may have examples of good hydraulic alternatives to various things too.
It seems like we could put decaying radioactive material to work for heating…
Well all the countries they are talking about heating with pinwheels hooked up to stirred pots of liquid happen to be the ones that just eradicated nuclear for no good reason and now nobody can afford to heat their homes through the winter. Sure seems like they’re getting the squeeze, as in money is being squeezed out of them en masse.
Thomas Edison predicted that Radium would be used for that.
So we need renewable (wind, solar, etc.) energy generation systems to replace the bad bad fossil fuel and nuclear generators that work fine most of the time because there are lots of people using lots of energy. But the problem with most of them is that since they are either inefficient, or as said above, the wind doesn’t blow/sun doesn’t shine all the time, so we need large storage batteries/tanks/etc. to store the energy during the lean hours.
So the where most of the energy demand is, we have no room to build such devices, and where there is room for them, there is not a very high demand. I’m I getting this right?
I reckon in denser areas, district geothermal heating makes a lot more sense than direct heat via wind, but this seems like it could be good in more rural areas, as noted in the post.
Energon Cubes 4 the win!
Mechanical drive of a heat pump compressor is -theoretically- possible but the devil is in the details. Compressors and motors are hermetically sealed together with sealed pass-throughs for the wiring. Designing adequate sealing to not lose refrigerants through a rotating seal would be a trick.
A system with a cheap, fairly non-toxic refrigerant like propane could be fairly leak-tolerant, but there’s the thinking that pumping flammable stuff all around your house and through machinery may not be a great idea.
You could use a synchronous magnetic coupling or something, although just making a really good shaft seal might be better than some ideas. As a random idea, a hydraulic motor-pump pair might work? (Then only two extra fluid lines actually need to pass through the case – that doesn’t solve it but it moves the hard part of the seal from the case to the hydraulic motor.)
What about a wind pump pushing around a ferrofluid? Could you harness a magnetic hydraulic fluid to excite coils around the hoses?
They’re permeable but don’t produce a strong static field. You could use a magnetic field to adjust the braking force in a fluid brake, but generating power better than anything else seems unlikely. If you look at conductive fluids there’s magnetohydrodynamic generators, but… an alternator seems easier.
Or use eddy currents as combo braking/heating/l AND energy generation??
Time for me to head back to the experiment shed..
car ac compressors have a shaft (not hermetic), probably still ammonia compressors out there that ore not hermetic, though might need modifications for, say, propane etc.
The hot gas from an outside compressor (in shed?) can run inside a heat exchange to heat a safer transfer fluid which is pumped into the house causes some extra losses of course even with insulation etc.
Good point; I overlooked them due to how often car systems leak, but that’s probably more about the automotive stresses than the shaft.
Leakage of the sealing surfaces is a matter of time and use – every time it runs with a pressure difference across the seals, it leaks – but the car AC is simply not used very much so it doesn’t need frequent fill-up.
Get rid of data centers and distribute everything by placing compute cabinets in everyone’s house, move the load as needed seasonally, etc Companies subsidizes electricity and connectivity, maybe even rents the space. Use the heat for comfort and water heating. Companies save on cooling and all that heat isn’t wasted. Would require better connectivity maybe, but we should be doing that anyway. Obviously cities and suburbs are probably better candidates than rural.
I’d volunteer but we only have 100A service, and also it’s summer.
Would it be more profitable for them to store the data they have about you in your own home?
B^)
Okokok, I know this one… :D
Will you allow technicians into your house at 3am to perform emergency maintenance?
I oversee over 1000 servers just for one company in one data center, and we have multiple data centers just in the city I live in.
In any given day, we are performing maintenance on tens of machines or more per data center, how will that go if the tech is performing house calls?
Not to mention that 10G and 100G DAC SFP+ connections used from switxhes/routers to servers have a maximum length of less than 10 meters, and you are stuck with a full rack pulling 10’s of kW of power 24/7 in your closet.
Or you are looking at unworkable laaaaaaaggggg.
Then take a look at the spine/leaf/node fabric topology. Every switch and router connecting to every other switch and router, the number of connections is exponential. Imagine running that bundle of fibers across the city.
But then there’s the security aspect.
Our SSL/TLS servers are locked in 24‐hour monitored racks with CCTV, intrusion detection, and combination locks, and that’s even after the 3+ layers of security that the data center offers by default….
So, can a bunch of strangers spend up to a week decomissioning an obsolete rack of equipment and installing new gear in your house?
Oh, we have to swap the rack out for a deeper one to accomodate the larger routers…
Sorry about the damaged walls and scratched floor, and don’t mind the jet engine sound of the router fans running 24/7 and from the industrial hvac just outside.
We’ll be back at some random inconvenient time, probably when you aren’t home or at 3am to perform emergency maintenance.
Oh, and we can’t do anything about the latency, that’s just physics.
;D
If I read “A heat pump, on the other hand, can be 300% efficient or more” anywhere else than on Hackaday, I would run away. But because I tend to trust the sources here I need to ask how this is possible and why we’re not in over-unity-wacko territory. Basically, why can’t the heat pump run off its own energy once it’s started if its actually 300% efficient?
It consumes x Watt to move from side A to side B more than x Watt worth of heat – not really wacky at all. It must consume that energy to move the heat but because the outside has so much heat you can easily capture and move that is the work you are doing, letting you seemingly get more for less over actually generating heat with that input energy.
So say we’re talking 300% efficiency. I use 1 unit of energy (from mains power) to move 3 units (as heat). From what I understand, can’t I use part of the heat energy I’ve moved to just sustain the reaction and stop using electricity? Again, I’m not trying to spark an over-unity troll. I just want to understand how it works…
To convert heat into work, you have to have a colder place the heat can move to (see: sterling and steam engines). You cannot, therefore, expend work to create a temperature difference, then use said difference to get more energy than you originally had. At best, you could undo all the work of heating (thus, defeating the whole purpose) and still end up with less energy than you started with.
The “Carnot limit” is defined using that logic – if there were a more-than-perfect engine or a more-than-perfect refrigerator, then you’d be over-unity by combining them. However the limit isn’t 1 to 1 – instead, the greater the difference in temperature, the better an engine works and the worse a heat pump works. With infinite temperature difference, an ideal engine outputs everything coming in as work without any waste heat. With zero temperature difference, an ideal heat pump transfers heat without any input work. Neither one can actually be built, but the latter is very close in performance to just an excellent conductor of heat – large heat flow for a negligible temperature difference. The former is often best replaced with something that gets the energy that was going to become heat, (likely fuel) before it does so, because then the Carnot limit doesn’t go into play. If you have an ideal engine hooked up to an ideal heat pump in a closed system, the work the engine makes is the same as the work the heat pump consumes, and the heat the engine wastes is the same as the heat the heat pump removes.
Or to simplify, in some conditions the hot and cold temperatures are such that an ideal heat pump can produce three times as much heat as its input power, but an ideal engine consumes three times as much input heat as its output power.
I think this is the answer I was looking for. I get the whole moving more heat energy than consumed electric energy but I was confused because I was thinking of ideal conditions where the thermal energy and the electrical energy being convertible, they are equivalent. But it’s the “using it” part that is inefficient right?
If I understand what you mean, then yes. Basically once something becomes thermal energy, there’s no engine that can turn all of it into electricity or any other useful form – there will always be some heat that passes through.
Thank you! 🙏
Side note – incandescence and sunlight and such are examples of heat turning 100% into light, but that light isn’t free from limits when you want to turn it into another form so it still counts.
There are mini-split heat pumps with greater than 1000% heating efficiency.
That is, they move 10x or more heat energy than they require in electrical energy.
The magic rating is “HSFP” – Heating seasonal performance factor.
https://en.wikipedia.org/wiki/Heating_seasonal_performance_factor
https://learnmetrics.com/highest-efficiency-heat-pumps-highest-seer-hspf/
The ones we can buy in the UK are approx 4.3:1 (i.e. 430% efficient).
I am waiting for them to become >= 600% before it becomes economic to replace the gas boiler.
So – where do I buy your 1000% ones from?
In your SEER link, 13.0 HSPF is equivalent to 430% or COP of 4.3. Nothing approaches 1000% which would be ~30 HSPF.
Most Japanese/Korean mid-end to high-end COP 10 at normal range with cold climate an one COP 2.5 at -15C available mostly in Asian market but you can get 230-250VAC version as well as DC one(directly solar powered and SAHP), you anyway looking more of yearly overall performance.
https://www.energystar.gov/productfinder/product/certified-mini-split-heat-pumps/results?formId=3322-78-43-9918-904361013&scrollTo=2598&search_text=&outdoor_unit_brand_name_isopen=0&hspf2_btu_wh_filter=13%2B&is_most_efficient_filter=0&zip_code_filter=&product_types=Select+a+Product+Category&sort_by=seer2_btu_wh&sort_direction=desc&page_number=0&lastpage=0
As you can see most heat pump I reference don’t even have certification of ES because they are “never” will be sold outside of domestic market or Asia.
At least officially.;)
Anything with “seasonal” in the rating doesn’t really count for conversion to COP in my opinion. It’s artificially inflated by assuming the performance is better due to seasonal variations, but I tend to find that the true instantaneous COP (or the EER, without the “S”) is more realistic, and when in spring/fall an aircon/heat pump just runs less but not at as much better of a COP as is implied. The EER rating converts to about 6.3 COP which sounds more realistic as a top end IMO.
Heat pumps aren’t heating or cooling directly, they’re just moving heat around.
Even on a cold day, there’s enough heat outside that if you compress it all together, you can leave some of it in your house. :) Which also heuristically explains why they get less efficient at heating when it’s cold out…
energy cannot be created nor destroyed
An heatpump engine like any fridge engine is completely sealed inside an oil bath, to prevent the refrigerant from escaping. It’s not easy to power an heatpump mechanically for this reason, when dealing with very efficient but expensive and high greenhouse effect gases.
A permanent magnet coupling would be the best way in such case, but it increases the complexity even more.
Automotive A/C compressors are powered by belt & pulley, and operate across a variable range of speeds.