We touched on the open source SLS4All DIY SLS 3D printer a year or two ago when the project was in the early stages. Finally, version one is complete, with a parts kit ready to ship and all design data ready for download if a DIY build or derivative is your style. As some already mentioned, this is not going to be cheap: with the full parts kit running at an eye-watering $7K before tax. But it’s possible to build or source almost all of it a bit at a time for those on a budget.
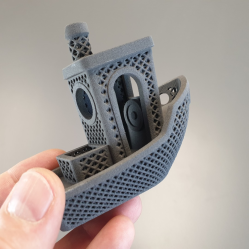
It’s important to note that to access the detailed information, you’ll need to create an account, which is a bit inconvenient for an open source design. However, all the essential components seem to be available, so it’s forgivable. In terms of electronics, there are two custom PCBs: the GATE1 (GAlvo and Temperature Control) and the ZERO1 (Zero-crossing dimming) controller. Other than that, all the electronics seem to be standard off-the-shelf components. Both of these PCBs are designed using EasyEDA.
Unfortunately we couldn’t find access to the PCB Gerbers, nor does there appear to be a link to their respective EasyEDA projects, just the reference schematics. This is a bit of a drawback, but it’s something that could easily be reproduced with enough motivation. Control is courtesy of a Radxa Rock Pi, as there were ‘problems’ with a Raspberry Pi. This is paired with a 7-inch touchscreen to complete the UI. This is running a highly modified version of the Klipper together with their own control software, which is still undergoing testing before release.
The laser head is built around a 10 W 450 nm laser module from China and a high-end galvanometer set. Two 200 W halogen tube heaters heat the print bed, and 200 W silicone heating pads heat both the powder bed and the print bed.
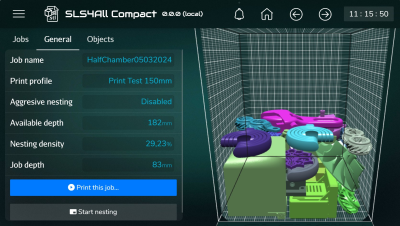
The upper and lower frames are basic boxes made from 2020 profile aluminium extrusions, with aluminium sheets for the panels. There are no big surprises here. As expected, numerous custom-made aluminium parts are involved, and this is where most of the cost lies. This might be a significant challenge for those who don’t have access to a CNC milling machine. The mechanics can be viewed in-browser via Fusion 360 Live or downloaded as a STEP model for later import.
We last checked in on this project back in 2022, and we’re glad to see it finally cross the finish line. Is this the first open source SLS printer? Of course not! But we’re always glad to see more options out there.
“aggresive nesting”
Though I can personally attest that SLS results are nothing short of awesome, I’ve heard that the most affordable, powdered consumables are dangerous to breathe, and that you need to wear a respirator when the printer door is open and also while cleaning printed parts.
If this rumor is true, SLS is not exactly a “kitchen-friendly” 3D printing technology, unless you also invest in a fume hood with HEPA filters.
Can someone who has worked with this technology (e.g. in a service bureau) set the record straight on potential hazards and safe usage guidelines? (My quick internet search did not yield clear and satisfying answers.) Thanks!
That’s true, but melty plastic fumes and resin fumes are also stuff you don’t want in your kitchen. Each has its own particular risks. But none of these are “safe” like an inkjet printer is safe.
Fumes (gases) can “easily” removed from a room, just ventilate it. (Yes, this is a simplification.)
Dust will attach to surfaces and lay down at all places around the room. It is difficult to remove from those surfaces, and every air movement might detach it from the surface and make it airborne again. It will attach to clothing during work, so a airlock (with all its bells and whistles) might be needed. All in all. much more difficult.
You might want to read Bericht F2410 from baua.de. It has a lot of details and pointers. Warning: German
https://www.baua.de/DE/Angebote/Publikationen/Berichte/F2410.html
So do fumes they stick to everything as a condensate
You’re basically working with fine powdered metal. Which to my limited knowledge means very small particle size, easily blown away and inhaled, with very sharp edges that allow them to easily embed themselves in tissues. Think asbestos and glass/carbon fiber dust.
You´re basically reacting before reading. Or you´d think a 10W blue laser can sinter metal ?
A 30W blue laser seems to be sufficient for stainless steel 316L, demonstrated by videos of the Metal Base 1.0 project.
PA12 nylon, not metal
This class of SLS (generally) uses polymers, not metal. Typically nylon particles in the 50 um size range. Often glass-filled. Sometimes aluminum-filled. They are basically smooth and inert spheres, no sharp edges.
True, don’t inhale. Wear a respirator for nuisance dust. The stuff falls out of the air pretty quickly, but is easily stirred up by sweeping: use a vacuum cleaner with a HEPA filter.
It’s a lot less nasty stuff than laser printer toner, or even powder coating ‘paint’.
I was going to note that laser toner printers are probably a similar hazard. Probably something worth repeating. Beat me to it!
aren’t these often really flamable if you get a good amount of them airborn?
Sure, if you can manage to suspend enough in air for long enough, and provide a suitable ignition source. Kind of like flour, or cornstarch, or hair, for that matter. Doesn’t seem to stop amateurs from cooking or cutting hair.
Also: Most powdered metals are flammable and burn bright and hot.
Also not relevant to this discussion of powdered plastics.
No recipe?
Powdered aluminum and rusted iron make for dandy welding.
Or other things.
Not illegal things, that would be ‘wrong’.
The powdered materials are a respiratory hazard (like any fine powder, though we happily ignore this for things like fine flours and sugars when using open-topped domestic mixers). They are far less of a hazard than resin printers, and without the contact sensitisation issues and the baths of flammable chemicals for rinsing.
I beleive both flour and steel will be probably easily broken down by human body.
Maybe, but flour is still a genuine hazard.
https://jamaicahospital.org/newsletter/what-is-bakers-lung/
I’ve got a formlabs fuse 1 in my living room. It’s not too bad if you wear a mask while working on it (I do a half face respirator cause it’s more comfy but n95 is fine) and I do my best to vacuum up all the dust that accumulates. I was worried at first about using a non anti static vacuum but have had no problems. Can’t comment on the long term health risks tho
Please report back to us in 20 years should you discover any long term health risks.
Of course
Half face mask is much better. N95 doesn’t help you with dust. It’s basically a splash guard against droplets, not much more than that. It’s great for operations as it prevents blood drops from entering your mouth. I tried N95 in the workshop when using the belt grinder but it was completely useless. The metal particles in the air still made my breath smell like rust, which is a very bad sign. I wear a half face nowadays, or my DIY forced air mask, depending how much I need to grind.
Got any details on that forced air mask? That sounds very interesting.
Almost anything is dangerous is powder form when inhaled though – especially if you do it very often.
One question that springs to mind is if this could be adapted for metal powder sintering. If a larger laser would do the job for example. Followed by curing in an oven.
Since those machines go for 120K according to google
it would take a much more powerful fiber laser 200W+ to DMLS/DMLM
No oven “curing” required.
An oven would likely be an understatement for a sintering furnace required for processes like binderjetting where powder is shape locked with an inkjetted fluid then consolidated into a smaller part in a controlled vacuum furnace. Different process entirely.
I’m happy to see more innovation in this space. Both this and the Micron are pretty exciting – in both cases I think there’s still a lot of work to do before they’re reliable and consistent, but this is a good step towards that.
I want to encourage the owners of this project to make this truly open hardware. The article calls out some shortcomings in this respect (having to make an account, not all design files available). OSHWA defines open hardware as requiring the designs to be available, as well as sufficient documentation to build it yourself – and for good reason!
I wonder if it would be possible to sinter metal powder with this by upgrading the power of the laser.
The 10 watts here isn’t far off what’s needed for metal SLS, and the wavelength even might be OK. The (much) bigger issue will be inert-atmosphere handling of the metal powder.
How so? Helium is inert and you can buy a tank of it online, in most supermarkets or party supplies stores because it’s used for filling party baloons. It would only be problematic in Norway where posession of helium is banned because it was commonly used for suicide. Any gaps could be detected with soap spray bottle and fixed with gaffa tape.
Sane people use argon. For any of the purposes mentioned.
“party” helium is cut with air for expressly that reason (and to make it cheaper).
WTF is “gaffa” tape? You mean gaffer tape? The gas-permeable, strong, but rippable cloth tape? Did I mention it’s gas-permeable? Geez, use packing tape if you want a gas-tight seal, and it’s a tenth the cost.
The problem is that the metal powder can’t be exposed to atmospheric oxygen at any point in its handling. You need to source it in sealed containers, transfer it to your printer’s material handling system without exposing it to air, do all the printing in the absence of air, and then remove your finished part. If you want to recover your un-sintered powder, you need to recover that somehow without exposing it to air.
It’s all very do-able, with many extant commercial systems to prove it, but it requires careful attention to material handling, workflow, and the associated support, including the vacuum annealing oven for post-processing.
All this is not a trivial upgrade from this cheap SLS printer.
Why so upset about Gaffa? You and I still understood what he was talking about. That is basically all that matters in English. There is no language council that decides what is right and wrong like with the French language.
Can you use nitrogen instead? Nitrogen is easy to make. They actually have a coffee machine that does it now.
Nitrogen was used for the early sls i saw working in ’02 or so. It used some kind of polymer coated steel powder, so didnt really sinter the steel. Don’t know about suitability at higher power levels…