When it comes to transmissions, a geared continuously-variable transmission (CVT) is a bit of a holy grail. CVTs allow smooth on-the-fly adjustment of gear ratios to maintain a target speed or power requirement, but sacrifice transmission efficiency in the process. Geared transmissions are more efficient, but shift gear ratios only in discrete steps. A geared CVT would hit all the bases, but most CVTs are belt drives. What would a geared one even look like? No need to wonder, you can see one for yourself. Don’t miss the two videos embedded below the page break.
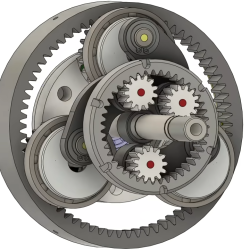
The design is called the RatioZero and it’s reminiscent of a planetary gearbox, but with some changes. Here’s how the most visible part works: the outer ring is the input and the inner ring is the output. The three small gears inside the inner ring work a bit like relay runners in that each one takes a turn transferring power before “handing off” to the next. The end result is a smooth, stepless adjustment of gear ratios with the best of both worlds. Toothed gears maximize transmission efficiency while the continuously-variable gear ratio allows maximizing engine efficiency.
There are plenty of animations of how the system works but we think the clearest demonstration comes from [driving 4 answers] with a video of a prototype, which is embedded below. It’s a great video, and the demo begins at 8:54 if you want to skip straight to that part.
One may think of motors and gearboxes are a solved problem since they have been around for so long, but the opportunities to improve are ongoing and numerous. Even EV motors have a lot of room for improvement, chief among them being breaking up with rare earth elements while maintaining performance and efficiency.
TLDR: Sadly, it’s just another complicated ratchet mechanism.
with a wobbly output – and still needs a friction component in the one way bearings (or a ratchet/pawl in which case it is not continuously variable)
you don’t need friction in a one way ratchet, you need a spring load. not even remotely the same thing.
you also clearly didn’t watch far enough into the video to see the speed-equalizing elliptical gears.
and no, a ratchet and pawl has absolutely no effect on the contentiousness of the gear ratio. that is entirely determined by the leverage of the drive arms.
even on a spherical-cow theoretical level, the ratchet and pawl means discontinuity of drive motion, not gear ratio. for this a classic solution exists: a flywheel.
Yes – I watched far enough to see the elliptical equalizer. It still had a wobbly output.
If a [not ratchet/pawl] one way bearing does not rely on friction what does it rely on? That spring/oval-needle or what ever else causes the one-way-ness doesn’t have teeth.
If the one way device IS a ratchet and pawl, then it is not continuously variable is it? If the motion is not far enough to engage one tooth then the ratio is 0. If it moves far enough to engage one tooth the ration is 1/r. Two teeth 2/r. n teeth then it is n/r
Or do I not understand how a ratchet and pawl works? Is there a fancy new kind that can go less that one tooth and catch?
@Cunning
A rachet and pawl doesn’t operate on friction. it operates on the ratchet physically being unable to pass through the pawl. Even in a frictionless world, solid objects can’t pass through each other.
The rachet and pawl isn’t providing the gear ratio. That’s the job of the variable lever arm(s). You’re trying to argue that a house can’t be warm because it’s driveway is cold. Looking in completely the wrong place.
Go study the video more until you better understand how it works.
Please learn the english language.
I never said a ratchet relies on friction. I said a NOT-RATCHET-PAWL one way mechanism relies on friction.
See the Honda RN01 post below by [GameboyRMH]. Item 6 in the diagram “Rollers lock in one direction and spin freely in the opposite”
That is the kind of one way mechanism that relies on friction.
A ratchet and pawl does not rely on friction. But in spite of what you think, it can not provide continuously variable output.
The lever arms might provide “variable ratio” but it is oscillating. It has to have a mechanism to turn that oscillation to one way rotation. That mechanism is a either a one-way-bearing or a ratchet and pawl.
If the design did NOT need a device to turn the back and forth oscillation of the lever arm into one way motion IT WOULD NOT BE THERE.
If you accept that it has to be there to turn back and forth motion to one way motion – it should not be too hard for you to understand the whole
1/r, 2/r…..n/r
thing.
If you can’t understand that please give up.
Piston engines have a wobbly torque output too
Yes, but the speed can still be constant. A ratchet has a wobbly speed output, which causes a lot of strain in the parts of the rotating mass.
Flywheels
The wobbly output is minimized to the point that it’s not an issue by the oblong gears. Also the next gear that is used to transmit power becomes engaged and takes over power transmission before the current gear being used starts to ratchet/over-run.
The commentator called the holding mechanism a ratchet mechanism not a ratchet/pawl mechanism. It’s possible that it’s an over-running clutch mechanism like what has been used in the ‘breakaway’ setup (when the gear selector is in the D position as apposed to the L position) of the low gear on automatic transmissions for a very long time.(At least 60 years as that’s how long ago I first seen one).
Link to an over running clutch set up.
https://youtube.com/shorts/H4SiM5Dcblg?si=UWj7Tyb-Lit-fZ2K
Yes. The oval gears are a neat trick, but it’s still a ratchet at heart
you make it sound like the ratchet is the whole deal. it isn’t. it merely requires a ratchet, in the same way it required ball bearings and shafts and screws.
nobody’s ever done this before. requiring a ratchet as one small element is hardly a high price to pay.
Look up a ratcheting CVT and come back to the discussion.
This is literally the epitome of, “what if we made a ratcheting CVT, but spun it in a circle?”
Video implies the ratcheting mechanism is specifically for the bicycle application, allowing the rider to coast instead of having the tires force the rotation of the pedals. Same functionality as existing 8- or 9-speed cassettes.
Yes, but as everyone pointed out multiple times in the comments of the video, the ratchets are mandatory for this design. It being on a bicycle has nothing to do with it.
“Same functionality as existing 8- or 9-speed cassettes.”
They’re out to 13 now, although I’ve stopped at 9, partly for reasons of chain & cassette durability. In a typical 12-25 (or 26) road cassette, the only difference between 9- and 10-speed is the 16-tooth cog between the 15 and 17, and otherwise all the jumps are the same size. They have 12-13-14-15-17-19-21-23-25 (or 26), versus 12-13-14-15-16-17-19-21-23-25 (or 26) which for me, is close enough to being a continuously variable transmission, and the chain drive can be up to 98% efficient. The “clicker” however is in the freehub body that the cassette slides onto, or in older technology, the freewheel. Some brands of modern freehub bodies are extremely loud when coasting. “Electronic Eel” here in the comments mentioned the 14-speed Rohloff Speedhub which is apparently an excellent design and very reliable, and each gear is something nearly 14% higher than the last; but its weight, and perhaps to a lesser extent its cost, have kept it from becoming very popular. FWIW, I have over 100,000 miles’ road cycling experience.
“FWIW, I have over 100,000 miles’ road cycling experience.”
I salute you!
It’s the prostate that gets it
None of anyone’s business; however there was a doctor who made a lot of noise a few decades ago with his assertion that saddles would have such a bad effect that they should be made illegal; and later he was proven totally wrong, because fit cyclists’ circulation is so much better than that of the general public, even that of most other athletes.
Aww man, was there EVER a better place to reply “ask your mom”?
Realize Toyota Priuses use planetary gears and Sun gears in their ecvt. They’ve been using gears for ages metal gears. They don’t use drums and belts in those. So as if this thing is some unique invention Toyota’s already done it with electric and gas lean motor combination using actual gear, Sun gears and planetary gears. And they’ve been doing it for almost 30 years. So this is nothing new. This crazy little thing
Precisely. This is not the first. Glad someone mentioned the Prius.
Following different things over the years people pretend they invent something new that already exists, if not exactly in some form.
This is fundamentally different. The Prius uses a differential, with two power input sources, that the differential mixes. This has been known for at least 1500 years.
This thing is a single input, single output transmission. It doesn’t look like it maintains phase relationship, which is a problem, but it doesn’t rely on friction drive so it doesn’t have a problem with slipping. There are lots of other CVT designs, like cone-and-belt, Beier drives, the really lovely NuVinci variator, but none of them are positive mechanical displacement type transmissions (for lack of a better term.)
Toyota already did this in the Prius . VT using gears.
Unfortunately, this transmission, being CVT, does not provide continious output rotation. Output rotation speed and torque is pulsed few (equal to number of “satellites”) times per output rotation, and working principle does not allow creation of steady output.
Interesting thing, really, but unuseable for transportation.
“Interesting thing, really, but unuseable for transportation.”
That won’t stop it from being used by automobile manufacturers!
B^)
Piston engines also produce pulsed torque, and that hasn’t stopped them from being quite popular in the transportation domain.
Would a flywheel help here too?
The torque of piston engines is pulsed, but not so much the speed. In a ratcheting mechanism, the speed of the ratchets is pulsed regardless of the torque, which will create very large spikes in torque/strain. A flywheel would intensify that. A compliant coupling would alleviate it.
This design doesn’t reply on ratcheting for torque, and compensates for pulsing with elliptical gearing. I’m fact the ratchet is only implemented as a bypass for it’s use on bicycles despite several people trying to claim otherwise.
Standard U-joints also don’t provide continuous, smooth output rotation, which is why we have CV joints. However, my wife’s last car, a Nissan Rogue with a CVT (which was very irritating to drive), had the CVT go out at 60,000 miles, which I found out was normal for these, and they’re so complex nobody rebuilds them, so you have to buy a new one, and parts and labor together came to $6K at the time. After all that, the gas mileage was not as good as that of a couple of older, bigger, more-comfortable cars we had in the past.
That’s why driveline U-joints are used in pairs, with the second 90 degrees offset from the first: the intermediate shaft sees cyclic variation in speed BUT that is cancelled by the second U-joint, so the output shaft (provided it is parallel to the input shaft) does not get the pulsation.
The implication being: If you put the spline back in incorrectly you get double the pulsation, and after you figured it out you felt like an idiot but learned something. You shouldn’t need to ask how I know that.
Ummm…. Piston engines have pulsed torque too. The 3 gears provide smoother torque transfer than your typical 4 cylinder.
The torque of piston engines is pulsed, but not so much the speed. In a ratcheting mechanism, the speed of the ratchets is pulsed regardless of the torque, which will create very large spikes in torque/strain. A flywheel would intensify that. A compliant coupling would alleviate it.
My first thought was “surely some gearhead in the last few centuries designed something like this already.”
That said, even if it was designed something that worked on paper, the technical limits of the time may have made it impractical so it never saw the light of day.
the best anyone’s come up with was the thing with cones and a belt. seriously.
not really, ratcheting cvt’s seem to have been around for several years before this thing
This isn’t a ratcheting CVT though, try actually looking at the mechanism. I don’t expect this is an entirely novel design, but the ratcheting is a bypass for bicycle use and not central to it’s functionality. This is obvious when looking at it’s operation.
Nope. The small gears must ratchet for it to work. Says the OP in the video comments: “One-way ratcheting/ motion is an essential feature of this transmission and not bicycle specific”
Kinda disagree, the nuvinci cvt is by far the most elegant kind of cvt I’ve seen, everyone I know from mechanical engineering school agrees
Very surely, something similar was in popular (something) magazine about thirty years ago.
This is similar to the Honda RN01’s “gearbox” which was also a CVT that worked by converting rotation into reciprocating motion and back with ratcheting mechanisms:
https://ridemonkey.bikemag.com/threads/honda-rn01-was-creative.285235/
I’m almost 100% certain I’ve seen that specific bike/transmission/gears on HaD before.
https://hackaday.com/2023/03/02/a-look-inside-bicycle-gearboxes/
Nice link. It even has the not round gears to smooth out the torque ripple, although here the gear is square instead of oval, because it uses 4 cams. That makes the “main difference” the planetary gear, and in this newer design the planetary gear does not have much advantage, because only one planet gear is used at any time, and the load is not shared between the planet pinions.
It seems the first application the developers are aiming for is bicycles. This means there is pretty though competition regarding efficiency and weight. Traditional chain gears have pretty good efficiency. Even designs like the Rohloff Speedhub have a hard time competing there and were just able to conquer a niche market over the years.
The prototypes that he showed in the video looked to me like they still have to go quite a way until they get their efficiency to a reasonable level.
i’d be very surprised if this ever got popular as a transmission for pedal bicycles. (although it might find a niche with e-bikes.) but that’s likely not the intention; bicycles (and e-bikes) would be a good, quick way to get practical experience with making these transmissions work on actual (if low-power) vehicles and in real use. a few thousand kilometres of road testing with such will likely teach them valuable lessons for when they scale up towards cars or motorcycles.
I would have to see some real data (Efficiency, power to weight ratio, endurance) before I believe in this thing.
I’ve been reading a bit in:
https://www.ratiozero.com/241203_Crowdcube_Ratio%20Zero%20MY24_Q4.pdf
One of the prototypes (In 2018) could not handle enough torque for a bycicle. Understanable for a prototype of course. The problem here is that only one gear in the planetary gear system is active at any one time, and thus the load is not distributed over the gears such as in a normal planetary gear.
I like the idea of the oval gears to reduce the ripple in the transmission ratio, but also wonder why they chose for simple oval gears. Ideally the form of the gear would be the inverse (reciprocal?) of the torque ripple to further smooth it.
They also claim an efficiency of 95% but they do not state whether this is just for the gearbox, or if it includes the chain drive too.
And they have an “Exit Strategy”. They intend to sell their company for USD 80M over 5 years. Sigh. Instead of giving this “invention” some time to develop it further and mature their intention is to get as much money out of it as possible, and as quickly as possible. Even if this thing can be made to work good (enough), extracting too much money too quickly may well bankrupt the company.
Sounds like a grift to me.
On itself it’s not a grift. It is actually one of the “get rich quick” methods that actually work:
Make some invention.
Build a company around it.
Delegate enough tasks to other people so the company mostly runs itself.
Sell the company.
Take for example Dexter from Haddington Dynamics. It started with a robot arm from mostly 3D printed parts and some carbon fiber tubes, (Also shown on Hackaday) and 3 years later the company was sold for USD26M to the Ocado group. And similar things have been repeated many times in history.
That is a grift. It’s the definition of a successful one, and not coincidentally the basis for most venture investing. “Not a grift” would be developing a company without the expectation of selling it off as soon as possible.
This is a variation of an idea I had when I was young. The basic idea is that a piston on a crankshaft will move more or less depending on the length of the crank. In fact, when the crank is 0 length, the piston doesn’t move at all. However, a piston gives reciprocating linear output. In order to turn that back into rotary output, you can use a rack and pinion, with the rack attached to the piston, and the pinion having a freewheel so it only engages its output shaft in one direction. Now, since the rack only turns the pinion during half the stroke, you have to add one or two more of these mechanisms at different phases in order to keep turning the output shaft continuously.
This new mechanism “simply” arranges all the racks in a circle. Quite clever, actually.
The transmission isn’t truly continuously variable due to the freewheel. The adjustment needs to reach the next click on the freewheel ratchet before a change happens. Of course, having several freewheels creates more adjustment points.
I’d say it’s also not strictly “continuous” as with the gears “passing the baton”, each gear has to re-engage. The ratio is mathematically dependent on the number of teeth skipped while not holding the baton, which will be an integer. I also wonder if the re-engaging can be done without significant tooth wear – perhaps with shaped teeth which become another ratcheting mechanism.
I would agree that this may not be “continuously” variable if the planet gears have ratchets, but not because of the skipped teeth while reversing. Indeed, there is no reason for an integer number of teeth to be skipped. Instead, the ratchet mechanism has a quantization – the pawl can only skip over an integer number of teeth. Thus, the gear ratios relate to the number of teeth in the ratchets. However, with some good choices in number of teeth (mainly in the ring gear?) a vernier effect could be created, allowing a factor of 1/N smaller steps, where N is the number of planet gears.
If the planet gears’ freewheel mechanism uses sprag clutches, then the overall design is back to a friction drive at its heart, relying on a wedging action to transmit torque.
There’s a similar transmission patented by Paul Pirez of Epilogics early ’90s. They did well with their freewheel, sometimes called “mechanical diode”. CVT itself was never mass produced or adapted.
While this one isn’t new I saw a three-dimensional hypercycloidic drive that came out of some university that was something new. Someone should give us an update.
Would Toyota eCVT not count as a geared cvt they only have gears no belts.
This is nothing new. Hasn’t anyone on this post heard of Prius? Prius has had a fantastic geared CVT for many years.
Toyota since 2004, I think. And Ford use it now, hardly new.
But the Prius eCVT isn’t a one-input one-output CVT. It has three ‘ports’: A motor/generator/starter, the ICE, and the wheels&electric motor. By varying the two input speeds and direction it varies the output speed. It’s a fixed gear ratio. There is no variable ratio anywhere. Importantly, that means there is no torque increase at low “gear” or output speed.
RatioZero promises continuous variability all the way down to 0 rpm output. This implies infinite output torque. While various factors, like the flexibility of the arms and the slop in the sprag clutches will limit the torque somewhat, and prevent near-zero rpm operation, but the torque would still be insanely high if the output shaft can’t move.
In applications where the output shaft could be blocked, some kind of slip clutch must likely be added to prevent overload.
In a large diesel electric locomotive this variable transmission is accomplished using a large variable transformer and electronic switching. Electrically it’s far more complicated, but mechanically far simpler.
You should take a look at the gearboxes on GP motorbikes, they change gears in ms, there’s a moment when the 2 gears are on at the same time!!!
Might as well pile on with the toroidal cvt. Two concave surfaces with rollers connecting them
Existing version use a magic fluid that sounds similar to non Newtonian fluids with high viscosity
under shear.
Looks like an interesting 3d printing project to make a dry version.
Had not heard of a toroidal version. Is it similar to the Nuvinci?
pretty much is the same as the nuvinci but in a nissan.
my partner has a bike with a nuvinci and it is surreal to ride on flat ground. Probably also wild on hills, but it is a lightweight womens/step-through and I am a fat bloke so I can’t really stomp on it so I have to be happy with 14 speeds rather than infinite.
thank you to the naysay commenters here. the ratchet was the part i wasn’t understanding properly from the video.
Check out Agco’s CVT for tractors. It’s brilliant and, apparently, bulletproof. No clutches, constantly engaged. The crankshaft remains directly coupled to the transmission.
I’d love to play around with a 3d printed model of this. Looks very interesting.
I came up with an electrical analogy that might help some understand this. Imagine continuous rotation as DC, and oscillating motion as AC. This CVT is like a DC-DC converter that first converts the input DC to 3-phase AC, shifts the voltages of those phases up or down using 3 VARIACs ganged together, and then turns that back into DC using a 3-phase half-wave rectifier.