A game show just for hackers like you is coming to the Hackaday Remoticon for the first time this year. Everyone is invited to take part in Hacker Trivia on Friday November 19th at 5 pm Pacific time.
Think of this as a very specialized type of bar trivia. You’re welcome to grab some friends and form a team, or play as a solo act. The biggest difference here is that all of the questions have been drawn up by the wonderful people who write the articles you read every day on Hackaday. To say there is a geeky flair to this is a gross understatement.
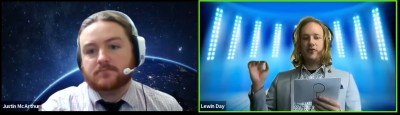
Your host for Hacker Trivia is Lewin Day. A staff writer for Hackaday, Lewin has for years dreamed of wearing powder-blue velvet suits, holding note cards full of esoteric questions, while speaking into an oddly-shaped microphone.
We managed to convince him to update the look to that of a modern game show host, and he didn’t disappoint with plans to broadcast from a secret location in Adelaide, Australia along with his producer, Justin McArthur. We’ve made it through a practice run, and I assure you, the game is delightful!
You can tune in live to Hacker Trivia to play along, but we want to make sure that you don’t forget. Sign up for a free ticket to Hackaday Remoticon and we’ll send you a reminder, along with information on how to take part in the online Bring-a-Hack social hour that follows the game show. Beyond these social events, Remoticon also has three keynote speakers, sixteen talk presenters, the Hackaday Prize ceremony, and a Saturday evening party. There’s even a conference ticket purchase option that includes a T-shirt.