[Sam Barrett] is doing something that is sorely needed. He’s doing real materials research on FDM parts.
There’s nothing wrong with the rough experiments like hanging a 1 L bottle of water from the end of a rectangular test print to compare strengths. We also have our rules-of-thumb, like expecting the print to perform at 30% of injection molded strength. But these experiments are primitive and the guidelines are based on hearsay. Like early metallurgy or engineering; 3D printing is full of made-up stuff.
What [Sam] has done here is really amazing. He’s produced a model of a printed ABS part and experimentally verified it to behave close enough to the real thing. He’s also set a method for testing and proposed a new set of questions. If it couldn’t be better, he also included his full research notebook. Make sure to read the FDMProperties-report (PDF) in the files section of Hackaday.io.
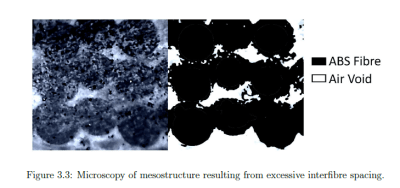
If research like this is being done elsewhere, it’s either internal to a large 3D printer manufacturer, or it’s behind a paywall so thorough only the Russians can help a regular peasant get through to them. Anyone with access to a materials testing lab can continue the work (looking at you every single engineering student who reads this site) and begin to help everyone achieve an understanding of 3D printed parts that could lead to some really cool stuff one day.
This sort of work is really valuable and is being done academically all over the world.
This project adds to that pool and can only be good.
This is impressive work! Congratulations!
the caption to the smaller image has its meaning reversed from the text in the actual image -“from excessive interfibre spacing” not excessive extrusion.
it is very nice that someone wants to spend the time and resources on researching FDM properties, that said this might be a lot harder than one might assume.
the material properties will in essence depend on the printer as well as the material, what gets heated where and when combined with how plastic cools would mean that there would be quite a lot of stress already in the part, combine that with the pseudo random composition of some plastic types and it starts to become difficult.
My first reaction was there is something wrong with this specimen, because I was missing the usual dog bone shape to reduce notch stress. But by reading the compressive report I learned about ASTM D3039 and other test styles (http://www.ae.iitkgp.ernet.in/ebooks/chapter5.html instead of https://books.google.de/books?id=fUc_JgzRyzIC&pg=PA40) *respect*
Nice work!
One challenge here is undoubtly that strength of the printed part depends a lot on the print parameters used. Like extrusion temperature. Like layer thickness. Like track density.
Does anybody know of a slicer program that will position layers offset from the previous layer to allow the fibers to be positioned in a close packed manner instead of directly on top of each other. It seems that this would provide more plastic to plastic contact at the cost of a rougher overall texture.
There is probably an answer in here.
http://hackaday.com/2016/07/27/3d-printering-non-planar-layer-fdm/
From what I’ve read this won’t actually increase the strength very much – feel free to conduct more research though! I’d point you to 3.2.6 of the report pdf at the project page if you’re curious.
I thought about doing that kind of test with custom G code. I think it might improve the XY strength.
You want strong you print in PLA. the PLA adhesion to each layer is a lot stronger than ABS. the Only reason to print in ABS is handling higher heat.
Also people feel more like it’s a “real world” party by the touch of ABS.
PLA is still a little strange to most people whereas ABS is a learned material.
PLA is better though – no warping, stronger at room temperature.
And PLA is apparently great for lost wax-style casting of metal parts without the horrible smell (and danger) of burning ABS.
PLA is also a lot more brittle and has less tensile strength, in short it is far from tougher than ABS, it is stiffer and it might adhere better at temperature x, the solution though is increasing ones temperature and z calibration for proper interlayer adhesion.
Material properties vs. ABS are all over the map. PLA is more rigid, but ABS is better for impact. Typical PLA parts can’t hold up to a morning sitting in my car so I don’t bother with PLA unless it isn’t going to leave my building. Even PETG can be a bit of a problem, especially black, nylon is only few degrees better with heat than PETG. ABS is probably the most affordable material that can take a decent amount of heat, i.e. I’ve even had a black ABS part sitting in the back seat and it’s shrugging off the heat just fine.
I didn’t know having an inter path distance of 0.04mm would make stronger parts. Now I will design walls to take an advantage of that!
I did my bachelor thesis on exactly this subject. We tested on multiple properties including water tightness.
There is a world of difference between the 3 major orientations of 3d printed parts